Introduction to BGA Assembly
Ball Grid Array (BGA) assembly is a crucial process in the manufacturing of electronic devices. BGAs are a type of surface-mount packaging used for integrated circuits (ICs) that utilize a grid of solder balls to connect the IC to the printed circuit board (PCB). This advanced packaging technology offers numerous advantages over traditional through-hole mounting and other surface-mount techniques, including higher pin density, better electrical and thermal performance, and reduced package size.
Advantages of BGA Assembly
- Increased pin density
- Improved electrical performance
- Enhanced thermal management
- Reduced package size
- Better mechanical stability
BGA Package Types
There are several types of BGA packages available, each with its own unique characteristics and applications. Some of the most common BGA package types include:
Plastic BGA (PBGA)
PBGAs are the most widely used type of BGA package. They feature a plastic substrate and are known for their low cost and good thermal performance. PBGAs are commonly used in consumer electronics, such as smartphones, tablets, and laptops.
Ceramic BGA (CBGA)
CBGAs utilize a ceramic substrate, which offers better thermal and electrical performance compared to plastic substrates. They are often used in high-reliability applications, such as aerospace, defense, and telecommunications equipment.
Tape BGA (TBGA)
TBGAs use a flexible tape substrate, which allows for thinner packages and improved electrical performance. They are commonly used in applications that require high-density interconnects, such as mobile devices and wearable electronics.
Flip chip BGA (FCBGA)
FCBGAs are a type of BGA package where the IC is flipped and directly connected to the substrate using solder bumps. This configuration offers improved electrical performance and reduced package size compared to wire-bonded BGA packages.
BGA Assembly Process
The BGA assembly process involves several critical steps to ensure reliable and high-quality connections between the IC and the PCB. The main stages of BGA assembly include:
- Solder paste printing
- Component placement
- Reflow Soldering
- Inspection and testing
Solder Paste Printing
Solder paste printing is the first step in the BGA assembly process. A stencil is used to apply solder paste to the PCB pads where the BGA will be placed. The stencil ensures that the correct amount of solder paste is deposited on each pad, which is crucial for forming reliable solder joints.
Component Placement
Once the solder paste has been applied, the BGA component is placed onto the PCB using a pick-and-place machine. The machine uses vision systems to accurately align the BGA with the PCB pads and gently places the component onto the board.
Reflow Soldering
After the BGA has been placed, the PCB undergoes reflow soldering. The board is heated in a reflow oven, causing the solder paste to melt and form a connection between the BGA balls and the PCB pads. The reflow profile must be carefully controlled to ensure proper solder joint formation and to prevent damage to the components.
Inspection and Testing
Following reflow soldering, the assembled PCB undergoes inspection and testing to verify the quality of the solder joints and the overall functionality of the device. Various techniques, such as X-ray inspection, automated optical inspection (AOI), and electrical testing, are used to identify any defects or performance issues.
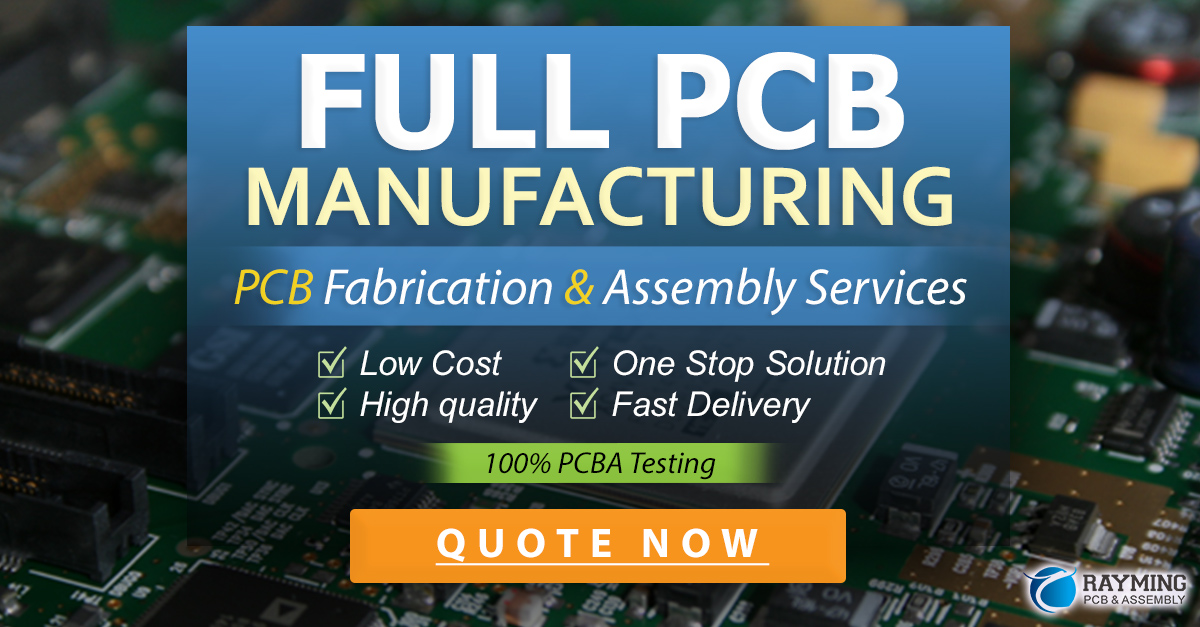
Challenges in BGA Assembly
While BGA assembly offers numerous benefits, it also presents several challenges that must be addressed to ensure reliable and high-quality results. Some of the main challenges in BGA assembly include:
- Thermal management
- Solder joint reliability
- Rework and repair
- Process control
Thermal Management
BGAs generate a significant amount of heat during operation, which can lead to thermal stress and potential reliability issues. Effective thermal management strategies, such as using thermal interface materials and designing appropriate PCB layouts, are essential to ensure proper heat dissipation and prevent component damage.
Solder Joint Reliability
The reliability of BGA solder joints is critical to the overall performance and longevity of the electronic device. Factors such as solder paste quality, reflow profile, and PCB design can all impact solder joint reliability. Proper process control and regular monitoring are necessary to maintain consistent and reliable solder joints.
Rework and Repair
Reworking and repairing BGA assemblies can be challenging due to the high pin density and the difficulty in accessing the solder joints. Specialized equipment and techniques, such as hot air rework stations and reballing, are often required to successfully rework or repair BGA components.
Process Control
Maintaining tight process control is essential for achieving high-quality BGA assembly results. Factors such as stencil design, solder paste deposition, component placement accuracy, and reflow profile must all be carefully monitored and controlled to ensure consistent and reliable outcomes.
Equipment and Tools for BGA Assembly
To successfully implement BGA assembly, a range of specialized equipment and tools are required. Some of the essential equipment and tools for BGA assembly include:
- Stencil printer
- Pick-and-place machine
- Reflow oven
- Inspection systems
- Rework stations
Stencil Printer
A stencil printer is used to apply solder paste to the PCB pads. The printer utilizes a stencil with apertures that match the PCB pad layout, ensuring precise solder paste deposition. Automated stencil printers offer high accuracy and repeatability, which is crucial for achieving consistent solder joint quality.
Pick-and-Place Machine
A pick-and-place machine is used to place BGA components onto the PCB. These machines use vision systems to accurately align the BGAs with the PCB pads and place them with high precision. Modern pick-and-place machines offer high speed and flexibility, enabling efficient assembly of a wide range of BGA package types.
Reflow Oven
A reflow oven is used to melt the solder paste and form the solder joints between the BGA and the PCB. Reflow ovens can be convection-based or vapor phase, and they utilize carefully controlled temperature profiles to ensure proper solder joint formation without damaging the components.
Inspection Systems
Various inspection systems are used to verify the quality of BGA assemblies. These include automated optical inspection (AOI) systems for detecting surface-level defects, X-ray inspection systems for analyzing solder joint quality, and 3D solder paste inspection (SPI) systems for measuring solder paste volume and alignment.
Rework Stations
Rework stations are used to repair or replace defective BGA components. These stations typically include hot air nozzles, vacuum pickup tools, and specialized heaters for removing and replacing BGAs. Skilled operators are required to successfully perform BGA rework and ensure the integrity of the repaired assembly.
Best Practices for BGA Assembly
To achieve high-quality and reliable BGA assembly results, it is important to follow best practices throughout the assembly process. Some key best practices include:
- Design for manufacturability (DFM)
- Stencil design optimization
- Solder paste selection and control
- Reflow profile optimization
- Regular maintenance and calibration
Design for Manufacturability (DFM)
Designing PCBs with BGA assembly in mind is crucial for ensuring successful manufacturing. This involves considering factors such as pad size and spacing, Solder Mask design, and thermal management. Collaborating with experienced PCB designers and assembly providers can help optimize the design for manufacturability.
Stencil Design Optimization
Proper stencil design is essential for achieving consistent solder paste deposition and preventing defects such as bridging or insufficient solder. Factors such as aperture size, shape, and spacing should be carefully considered and optimized based on the specific BGA package and PCB design.
Solder Paste Selection and Control
Selecting the appropriate solder paste for BGA assembly is critical for achieving reliable solder joints. The solder paste should have the correct particle size, flux chemistry, and rheological properties for the specific application. Proper storage and handling of solder paste, as well as regular quality control testing, are also important for maintaining consistent results.
Reflow Profile Optimization
Optimizing the reflow profile is essential for achieving proper solder joint formation and preventing defects such as voiding or component damage. The reflow profile should be tailored to the specific BGA package and PCB design, considering factors such as peak temperature, time above liquidus, and cooling rate. Regular monitoring and adjustment of the reflow profile are necessary to maintain process control.
Regular Maintenance and Calibration
Regular maintenance and calibration of BGA assembly equipment are critical for ensuring consistent and reliable results. This includes cleaning and inspecting stencils, pick-and-place nozzles, and reflow ovens, as well as calibrating inspection systems and rework stations. A proactive maintenance and calibration schedule can help prevent unplanned downtime and maintain high-quality assembly.
BGA Assembly Services
Many electronics manufacturers outsource BGA assembly to specialized service providers. These providers offer a range of services, from prototyping to high-volume production, and can support a wide range of BGA package types and PCB designs. When selecting a BGA assembly service provider, consider factors such as:
- Experience and expertise
- Equipment and capabilities
- Quality control and certifications
- Turnaround time and flexibility
- Cost and value
Experience and Expertise
Choose a BGA assembly service provider with a proven track record of successfully assembling similar products. The provider should have a deep understanding of BGA assembly best practices and be able to offer guidance and support throughout the design and manufacturing process.
Equipment and Capabilities
Ensure that the BGA assembly service provider has the necessary equipment and capabilities to support your specific requirements. This includes stencil printers, pick-and-place machines, reflow ovens, inspection systems, and rework stations that are suitable for your BGA package types and PCB designs.
Quality Control and Certifications
Select a BGA assembly service provider with robust quality control processes and relevant certifications, such as ISO 9001, AS9100, or IPC-A-610. The provider should have a strong focus on continuous improvement and be able to demonstrate consistent and reliable results.
Turnaround Time and Flexibility
Consider the BGA assembly service provider’s ability to meet your project timelines and accommodate changes in demand. Look for a provider with a track record of on-time delivery and the flexibility to support both prototyping and high-volume production.
Cost and Value
While cost is an important factor when selecting a BGA assembly service provider, it should not be the only consideration. Look for a provider that offers competitive pricing while also delivering high quality, reliability, and value-added services.
Frequently Asked Questions (FAQ)
- What is BGA assembly?
-
BGA assembly is the process of attaching a Ball Grid Array (BGA) component to a printed circuit board (PCB) using solder balls to create electrical and mechanical connections.
-
What are the advantages of BGA assembly?
-
BGA assembly offers several advantages, including higher pin density, improved electrical and thermal performance, reduced package size, and better mechanical stability compared to other surface-mount technologies.
-
What equipment is needed for BGA assembly?
-
BGA assembly requires specialized equipment, such as stencil printers, pick-and-place machines, reflow ovens, inspection systems, and rework stations.
-
What challenges are associated with BGA assembly?
-
Some of the main challenges in BGA assembly include thermal management, solder joint reliability, rework and repair, and maintaining tight process control.
-
How do I select a BGA assembly service provider?
- When selecting a BGA assembly service provider, consider factors such as experience and expertise, equipment and capabilities, quality control and certifications, turnaround time and flexibility, and cost and value.
Conclusion
BGA assembly is a critical process in the manufacturing of advanced electronic devices. By understanding the various BGA package types, assembly processes, challenges, and best practices, electronics manufacturers can ensure high-quality and reliable BGA assembly results. Selecting the right equipment, tools, and service providers is also essential for successful BGA assembly implementation. As electronic devices continue to evolve and become more complex, the importance of BGA assembly will only continue to grow, making it a crucial capability for manufacturers to master.
Leave a Reply