The Importance of Rapid PCB Prototyping
Rapid PCB prototyping is the process of quickly creating a physical prototype of a PCB design to test its functionality, identify any issues, and make necessary improvements before mass production. This process is essential for several reasons:
-
Faster time-to-market: By prototyping PCBs in-house, companies can significantly reduce the time it takes to bring a product to market. This is because they can quickly iterate on their designs and make necessary changes without relying on external suppliers or manufacturers.
-
Cost-effective: In-house PCB prototyping can also be more cost-effective than outsourcing the process. Companies can save money on shipping, handling, and markup costs associated with external prototyping services.
-
Improved quality control: When prototyping PCBs in-house, companies have greater control over the quality of their products. They can easily identify and address any issues that arise during the prototyping process, ensuring that the final product meets their standards.
The Benefits of In-House Rapid PCB Prototyping
Increased Flexibility and Agility
One of the primary benefits of in-house rapid PCB prototyping is the increased flexibility and agility it provides. When companies have the ability to prototype PCBs quickly and efficiently, they can respond to changing market demands and customer needs more effectively. This is particularly important in industries where technology is constantly evolving, such as consumer electronics, automotive, and aerospace.
With in-house prototyping capabilities, companies can experiment with new designs and features without the constraints of external suppliers or manufacturers. This allows them to be more innovative and creative in their product development efforts, leading to more unique and compelling products.
Improved Collaboration and Communication
Another benefit of in-house rapid PCB prototyping is improved collaboration and communication among team members. When the entire product development process is handled in-house, it’s easier for engineers, designers, and other stakeholders to work together and share ideas.
This increased collaboration can lead to more efficient problem-solving and better overall product design. Team members can quickly iterate on designs and provide feedback to one another, resulting in a more streamlined development process.
Enhanced Intellectual Property Protection
In-house rapid PCB prototyping can also help companies better protect their intellectual property. When outsourcing the prototyping process, companies risk exposing their proprietary designs and technologies to external parties. This can lead to intellectual property theft or unauthorized use of their designs.
By keeping the prototyping process in-house, companies can maintain greater control over their intellectual property and ensure that their designs remain confidential. This is particularly important for companies in highly competitive industries where intellectual property is a key differentiator.
Implementing In-House Rapid PCB Prototyping
While the benefits of in-house rapid PCB prototyping are clear, implementing this process can be challenging for some companies. Here are some key considerations for implementing in-house prototyping capabilities:
Investing in the Right Equipment
To effectively prototype PCBs in-house, companies need to invest in the right equipment. This includes PCB design software, 3D printers, CNC machines, and other specialized tools. The specific equipment needed will depend on the company’s product development needs and budget.
Here’s a table of common PCB prototyping equipment and their associated costs:
Equipment | Cost Range |
---|---|
PCB Design Software | $500 – $10,000+ |
3D Printer | $500 – $50,000+ |
CNC Machine | $5,000 – $100,000+ |
Reflow Oven | $500 – $10,000+ |
Pick and Place Machine | $5,000 – $100,000+ |
While the upfront costs of this equipment can be significant, the long-term benefits of in-house prototyping often outweigh the initial investment.
Building a Skilled Team
In addition to investing in the right equipment, companies need to build a skilled team to handle the prototyping process. This may involve hiring new employees with specialized skills in PCB design and fabrication or training existing employees to take on these roles.
Building a skilled team is essential for ensuring that the prototyping process runs smoothly and efficiently. Companies should look for employees with a strong background in electrical engineering, computer-aided design (CAD), and manufacturing.
Establishing a Streamlined Workflow
Finally, companies need to establish a streamlined workflow for their in-house prototyping process. This involves creating clear guidelines for PCB design, fabrication, and testing, as well as establishing communication channels between team members.
A streamlined workflow can help ensure that the prototyping process runs efficiently and that any issues are identified and addressed quickly. This can ultimately lead to faster time-to-market and higher-quality products.
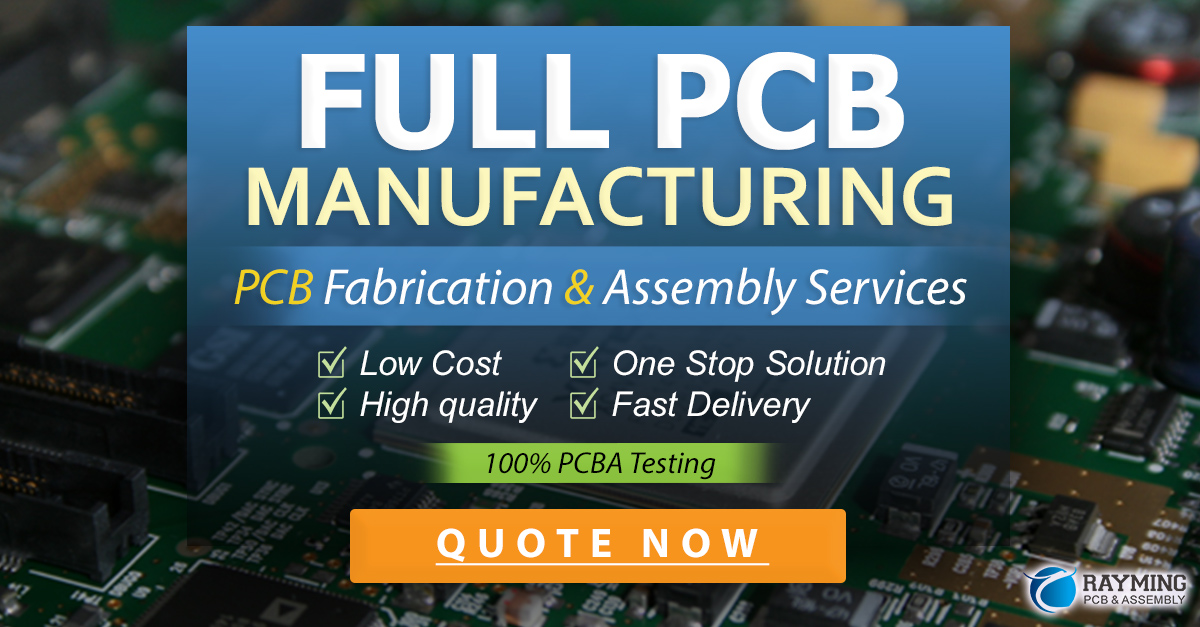
Real-World Examples of Successful In-House Rapid PCB Prototyping
Several companies have successfully implemented in-house rapid PCB prototyping and seen significant benefits as a result. Here are a few examples:
Tesla
Tesla, the electric vehicle and clean energy company, has invested heavily in in-house prototyping capabilities to support its product development efforts. The company has a state-of-the-art prototyping facility at its headquarters in Palo Alto, California, where engineers can quickly iterate on designs for new vehicles and components.
By prototyping PCBs and other components in-house, Tesla has been able to bring new products to market faster and more efficiently than many of its competitors. The company’s ability to quickly prototype and test new designs has been a key factor in its success in the rapidly evolving electric vehicle market.
Apple
Apple, the technology giant known for its innovative products, has also embraced in-house rapid PCB prototyping. The company has a dedicated prototyping facility at its headquarters in Cupertino, California, where engineers can quickly create and test new designs for iPhones, iPads, and other products.
Apple’s in-house prototyping capabilities have allowed the company to maintain a high level of secrecy around its product development efforts. By keeping the prototyping process in-house, Apple can ensure that its proprietary designs and technologies remain confidential until they are ready for release.
GE Aviation
GE Aviation, a leading manufacturer of jet engines and other aviation components, has also invested in in-house rapid PCB prototyping capabilities. The company’s Additive Technology Center in Cincinnati, Ohio, is equipped with state-of-the-art 3D printers and other equipment for quickly prototyping new designs.
By prototyping PCBs and other components in-house, GE Aviation has been able to reduce the time and cost associated with developing new jet engines. The company’s ability to quickly iterate on designs and test new concepts has helped it maintain its position as a leader in the aviation industry.
Frequently Asked Questions (FAQ)
- What is rapid PCB prototyping?
-
Rapid PCB prototyping is the process of quickly creating a physical prototype of a PCB design to test its functionality, identify any issues, and make necessary improvements before mass production.
-
Why is in-house rapid PCB prototyping important for product development?
-
In-house rapid PCB prototyping allows companies to bring products to market faster, reduce costs, and improve quality control. It also provides increased flexibility and agility, improved collaboration and communication among team members, and enhanced intellectual property protection.
-
What equipment is needed for in-house rapid PCB prototyping?
-
To effectively prototype PCBs in-house, companies need to invest in PCB design software, 3D printers, CNC machines, reflow ovens, pick and place machines, and other specialized tools. The specific equipment needed will depend on the company’s product development needs and budget.
-
How can companies build a skilled team for in-house rapid PCB prototyping?
-
Companies can build a skilled team for in-house rapid PCB prototyping by hiring new employees with specialized skills in PCB design and fabrication or training existing employees to take on these roles. They should look for employees with a strong background in electrical engineering, computer-aided design (CAD), and manufacturing.
-
What are some real-world examples of successful in-house rapid PCB prototyping?
- Companies like Tesla, Apple, and GE Aviation have successfully implemented in-house rapid PCB prototyping and seen significant benefits as a result. These companies have invested in state-of-the-art prototyping facilities and equipment to support their product development efforts and maintain their competitive edge in their respective industries.
Conclusion
In-house rapid PCB prototyping is a critical component of innovative product development in today’s fast-paced technological landscape. By bringing the prototyping process in-house, companies can reduce time-to-market, lower costs, improve quality control, and enhance collaboration and communication among team members.
While implementing in-house prototyping capabilities can be challenging, the long-term benefits often outweigh the initial investment. Companies that invest in the right equipment, build skilled teams, and establish streamlined workflows can gain a significant competitive advantage and deliver more innovative products to their customers.
As the examples of Tesla, Apple, and GE Aviation demonstrate, in-house rapid PCB prototyping can be a game-changer for companies looking to stay ahead of the curve in their industries. By embracing this approach to product development, companies can foster a culture of innovation and position themselves for long-term success in an increasingly competitive market.
Leave a Reply