Introduction to PCB Prototyping and Bill of Materials
PCB (Printed Circuit Board) prototyping is an essential step in the electronics design process. It allows designers to test and validate their designs before moving into mass production. Rapid PCB prototyping has become increasingly important as the demand for faster time-to-market and shorter product life cycles continues to grow. To ensure a smooth and efficient PCB prototyping process, it is crucial to optimize the Bill of Materials (BOM).
A BOM is a comprehensive list of all the components, materials, and quantities required to manufacture a product. In the context of PCB prototyping, the BOM includes all the electronic components, connectors, and hardware needed to assemble the PCB. Optimizing the BOM is critical for several reasons, which we will explore in detail throughout this article.
The Importance of BOM Optimization in PCB Prototyping
Reducing Lead Times
One of the primary reasons to optimize the BOM for rapid PCB prototyping is to reduce lead times. Lead time refers to the time between placing an order for components and receiving them. By carefully selecting components that are readily available and have short lead times, designers can significantly reduce the overall time required for PCB prototyping.
Strategies for Reducing Lead Times
- Choose components with high availability and short lead times
- Establish relationships with reliable suppliers
- Consider using alternative components with similar specifications
- Order components in advance, anticipating future prototyping needs
Minimizing Costs
Another important aspect of BOM optimization is minimizing costs. PCB prototyping can be expensive, especially when multiple iterations are required. By carefully selecting components and optimizing the BOM, designers can reduce the overall cost of prototyping without compromising on quality or functionality.
Strategies for Minimizing Costs
- Select cost-effective components that meet the design requirements
- Negotiate better prices with suppliers based on volume and long-term relationships
- Optimize the PCB layout to minimize the number of layers and reduce the board size
- Consider using cheaper alternative components that offer similar performance
Ensuring Component Compatibility
Ensuring component compatibility is crucial for the success of PCB prototyping. Incompatible components can lead to design failures, delays, and increased costs. By optimizing the BOM and carefully selecting components that are known to work well together, designers can minimize the risk of compatibility issues.
Strategies for Ensuring Component Compatibility
- Thoroughly research component specifications and datasheets
- Use components from the same family or manufacturer when possible
- Consult with experienced engineers or component suppliers for guidance
- Perform thorough testing and validation of the prototype to identify any compatibility issues
Facilitating Design Changes
During the PCB prototyping process, design changes are often necessary to improve functionality, performance, or manufacturability. An optimized BOM can facilitate these design changes by providing flexibility and room for modifications.
Strategies for Facilitating Design Changes
- Use modular designs that allow for easy component substitution
- Select components with multiple footprint options
- Keep the BOM organized and up-to-date to simplify the change management process
- Collaborate with the manufacturing team to ensure that design changes are feasible and cost-effective
Best Practices for BOM Optimization in PCB Prototyping
Standardize Component Selection
Standardizing component selection is a key best practice for BOM optimization in PCB prototyping. By establishing a library of preferred components that have been tested and validated, designers can streamline the component selection process and reduce the risk of compatibility issues.
Benefits of Standardizing Component Selection
- Reduced design time and effort
- Improved component availability and shorter lead times
- Lower costs due to volume discounts and reduced inventory
- Enhanced reliability and quality control
Use a Centralized BOM Management System
Using a centralized BOM management system is another best practice for optimizing BOMs in PCB prototyping. A centralized system allows for better collaboration, version control, and data integrity, reducing the risk of errors and inconsistencies.
Benefits of a Centralized BOM Management System
- Improved data accuracy and consistency
- Streamlined collaboration among team members
- Easier change management and version control
- Reduced risk of obsolete or duplicate components
Collaborate with Suppliers and Manufacturers
Collaborating with suppliers and manufacturers is essential for BOM optimization in PCB prototyping. By establishing strong relationships with key suppliers and manufacturers, designers can access valuable insights, expertise, and support throughout the prototyping process.
Benefits of Collaborating with Suppliers and Manufacturers
- Access to the latest component information and technologies
- Improved technical support and guidance
- Potential for customized solutions and faster turnaround times
- Reduced risk of supply chain disruptions
Continuously Review and Update the BOM
Continuously reviewing and updating the BOM is crucial for maintaining an optimized BOM in PCB prototyping. As new components become available and design requirements change, it is important to regularly assess the BOM and make necessary updates.
Benefits of Continuously Reviewing and Updating the BOM
- Ensures the use of the most suitable and up-to-date components
- Identifies opportunities for cost savings and performance improvements
- Helps prevent obsolescence and supply chain issues
- Facilitates continuous improvement of the PCB prototyping process
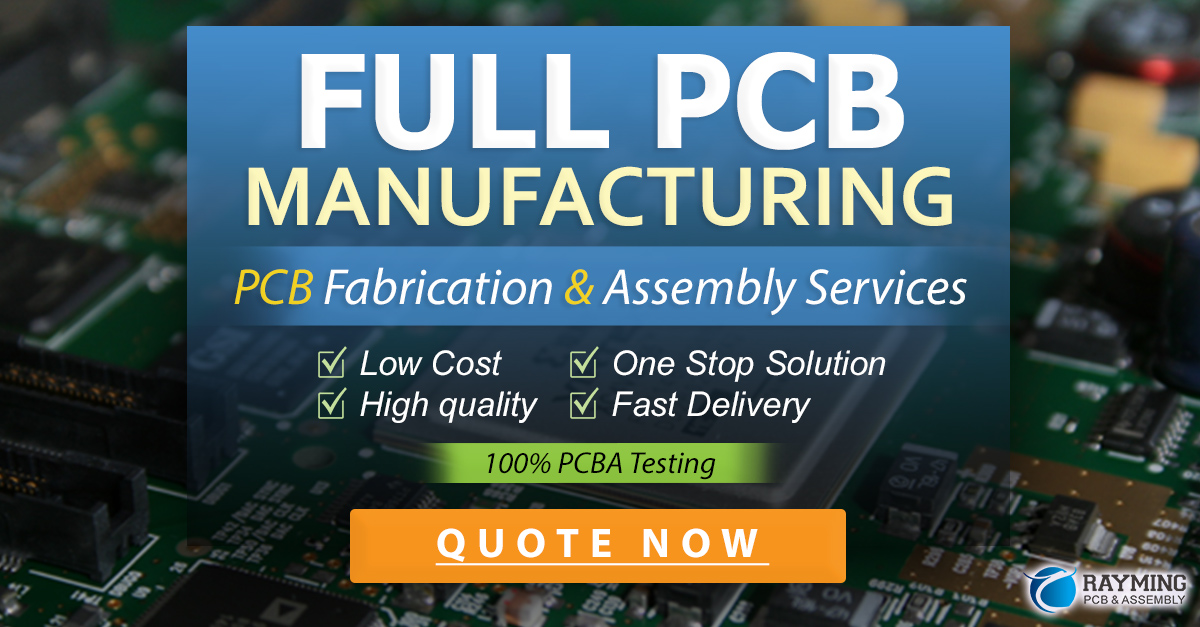
Table: Comparison of BOM Optimization Strategies
Strategy | Advantage | Disadvantage |
---|---|---|
Standardize Component Selection | – Reduced design time and effort – Improved component availability – Lower costs – Enhanced reliability |
– May limit design flexibility – Requires initial effort to establish a component library |
Use a Centralized BOM Management System | – Improved data accuracy and consistency – Streamlined collaboration – Easier change management – Reduced risk of errors |
– Requires investment in a BOM management tool – Needs training and adoption by team members |
Collaborate with Suppliers and Manufacturers | – Access to latest component information – Improved technical support – Potential for customized solutions – Reduced supply chain risks |
– May require time and effort to establish relationships – Potential for dependency on specific suppliers |
Continuously Review and Update the BOM | – Ensures use of most suitable components – Identifies cost-saving opportunities – Helps prevent obsolescence – Facilitates continuous improvement |
– Requires ongoing time and effort – May involve additional costs for updating components |
Frequently Asked Questions (FAQ)
-
Q: What is a Bill of Materials (BOM) in PCB prototyping?
A: A BOM is a comprehensive list of all the components, materials, and quantities required to manufacture a PCB Prototype. It includes electronic components, connectors, and hardware needed for assembly. -
Q: Why is BOM optimization important for rapid PCB prototyping?
A: BOM optimization is important for rapid PCB prototyping because it helps reduce lead times, minimize costs, ensure component compatibility, and facilitate design changes. An optimized BOM streamlines the prototyping process and enables faster time-to-market. -
Q: How can I reduce lead times through BOM optimization?
A: To reduce lead times, choose components with high availability and short lead times, establish relationships with reliable suppliers, consider using alternative components with similar specifications, and order components in advance, anticipating future prototyping needs. -
Q: What strategies can I use to minimize costs in PCB prototyping?
A: To minimize costs, select cost-effective components that meet the design requirements, negotiate better prices with suppliers based on volume and long-term relationships, optimize the PCB layout to minimize the number of layers and reduce the board size, and consider using cheaper alternative components that offer similar performance. -
Q: How can I ensure component compatibility in my PCB prototype?
A: To ensure component compatibility, thoroughly research component specifications and datasheets, use components from the same family or manufacturer when possible, consult with experienced engineers or component suppliers for guidance, and perform thorough testing and validation of the prototype to identify any compatibility issues.
Conclusion
Optimizing the Bill of Materials is a critical aspect of rapid PCB prototyping. By carefully selecting components, minimizing lead times and costs, ensuring compatibility, and facilitating design changes, designers can streamline the prototyping process and bring their products to market faster.
Implementing best practices such as standardizing component selection, using a centralized BOM management system, collaborating with suppliers and manufacturers, and continuously reviewing and updating the BOM can further enhance the benefits of BOM optimization.
By prioritizing BOM optimization in PCB prototyping, electronics designers can improve the efficiency, reliability, and cost-effectiveness of their prototyping efforts, ultimately leading to more successful and competitive products in the market.
Leave a Reply