Introduction
Proper power supply and crystal placement are critical for ensuring stable and reliable operation of microcontroller units (MCUs). Careful PCB layout and component placement can minimize noise, avoid signal integrity issues, and optimize performance. This article will cover best practices and guidelines for routing MCU power supply lines and placing crystals.
Power Supply Decoupling and Filtering
The Importance of Decoupling capacitors
Decoupling capacitors play a crucial role in maintaining a clean and stable power supply for MCUs. They act as local energy reservoirs, supplying current during sudden demands and filtering out high-frequency noise. Place decoupling capacitors as close as possible to the MCU’s power pins to minimize inductance and ensure effective noise suppression.
Selecting the Right Decoupling Capacitors
Choose decoupling capacitors with low equivalent series resistance (ESR) and appropriate capacitance values. Ceramic capacitors, such as X7R or X5R types, are preferred for their low ESR and high-frequency performance. Typical decoupling capacitor values for MCUs range from 0.01 µF to 10 µF.
Capacitor Type | Capacitance Range | ESR | Frequency Range |
---|---|---|---|
X7R | 100 pF – 10 µF | Low | High |
X5R | 100 pF – 10 µF | Low | High |
Y5V | 100 pF – 1 µF | Moderate | Medium |
Tantalum | 0.1 µF – 1000 µF | Moderate | Low to Medium |
Aluminum | 1 µF – 10000 µF | High | Low |
Decoupling Capacitor Placement
Place decoupling capacitors as close as possible to the MCU’s power pins. Ideally, the capacitors should be located on the same layer as the MCU to minimize loop area and inductance. If multiple decoupling capacitors are used, place them in order of decreasing capacitance value, with the smallest capacitor closest to the MCU.
Power Supply Filtering
In addition to decoupling capacitors, consider adding power supply filters to further reduce noise and ripple. Ferrite beads and LC filters can be used to attenuate high-frequency noise and improve power supply quality.
Power Plane and Ground Plane
The Benefits of Power and Ground Planes
Using dedicated power and ground planes in a PCB provides several advantages for MCU power supply routing:
- Lower impedance and inductance compared to narrow traces
- Better current distribution and reduced voltage drop
- Improved noise immunity and shielding
Splitting Power and Ground Planes
In some cases, it may be beneficial to split power and ground planes to isolate noise-sensitive circuits from noisy ones. For example, separating analog and digital power domains can help prevent digital noise from interfering with analog signals. When splitting planes, ensure proper connectivity between the planes using stitching capacitors or ferrite beads.
Via Placement and Stitching
When transitioning power and ground connections between layers, use vias to maintain a low-impedance path. Place vias close to the MCU’s power pins and decoupling capacitors to minimize loop area. Use multiple vias in parallel to reduce inductance and improve current handling capacity.
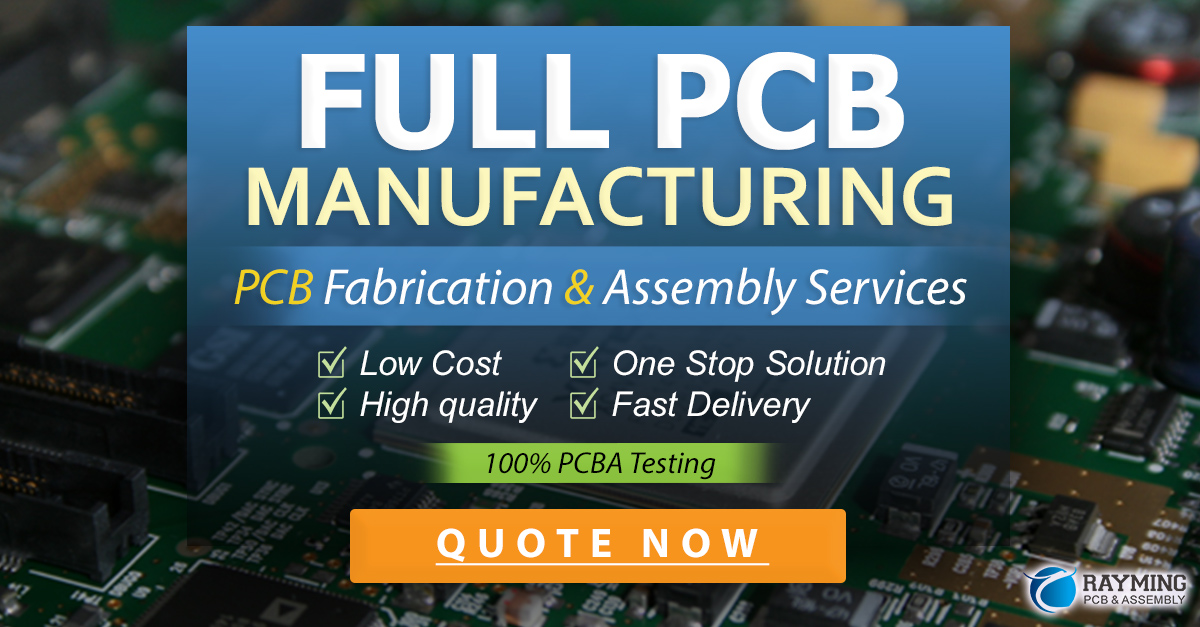
Crystal Oscillator Placement
Crystal Oscillator Basics
Crystal oscillators provide a stable clock reference for MCUs. They consist of a quartz crystal and load capacitors, which determine the oscillation frequency. Proper placement and routing of the crystal oscillator components are essential for maintaining signal integrity and reducing noise.
Crystal Placement Guidelines
Follow these guidelines when placing the crystal and its associated components:
- Place the crystal as close to the MCU as possible to minimize trace length and reduce the risk of noise pickup.
- Keep the crystal and load capacitors on the same layer as the MCU to avoid vias and minimize loop area.
- Orient the crystal to minimize coupling with nearby traces and components.
- Avoid placing the crystal near high-speed digital signals or noisy components, such as switching power supplies.
Load Capacitor Selection and Placement
Load capacitors are necessary for setting the crystal’s oscillation frequency and providing a low-impedance path for the oscillator circuit. Choose load capacitors with high Q factors and stable temperature characteristics, such as C0G/NP0 ceramic capacitors. Place the load capacitors as close to the crystal as possible, with short and symmetrical traces to the MCU’s oscillator pins.
Crystal Frequency | Typical Load Capacitance |
---|---|
32.768 kHz | 12 pF – 22 pF |
1 MHz – 25 MHz | 10 pF – 33 pF |
25 MHz – 50 MHz | 10 pF – 22 pF |
50 MHz – 100 MHz | 10 pF – 15 pF |
Oscillator Circuit Routing
Route the traces connecting the crystal, load capacitors, and MCU as short and direct as possible. Avoid using vias, as they can introduce unwanted inductance and degrade signal quality. If vias are unavoidable, use multiple vias in parallel to reduce inductance. Keep the oscillator traces away from high-speed digital signals and power supply lines to minimize crosstalk and noise injection.
PCB Layout Considerations
Component Placement
When placing components on the PCB, consider the following:
- Group related components together to minimize trace lengths and reduce loop areas.
- Place noise-sensitive components, such as analog circuits and oscillators, away from noisy digital circuits and power supplies.
- Arrange components to minimize crosstalk and electromagnetic interference (EMI).
Trace Routing
Follow these guidelines when routing traces on the PCB:
- Keep traces as short and direct as possible to minimize inductance and reduce noise pickup.
- Use appropriate trace widths based on the expected current and voltage drop requirements.
- Avoid sharp angles and use gentle curves to minimize reflections and impedance discontinuities.
- Provide adequate spacing between traces to reduce crosstalk and coupling.
Layer Stackup
A well-designed layer stackup can significantly improve the performance of an MCU-based system. Consider the following when defining the layer stackup:
- Use dedicated power and ground planes to provide low-impedance paths and reduce noise.
- Arrange signal layers to minimize crosstalk and interference between adjacent layers.
- Use ground planes to shield sensitive signals from noise and EMI.
- Select appropriate dielectric materials and thicknesses to control impedance and minimize signal loss.
Testing and Verification
Power Supply Measurements
Verify the power supply quality by measuring voltage levels, ripple, and noise at various points in the system. Use an oscilloscope with a low-capacitance probe to measure high-frequency noise and transients. Ensure that the measured values are within the MCU’s specified limits and that no excessive noise or voltage spikes are present.
Crystal Oscillator Measurements
Check the crystal oscillator’s performance by measuring the clock signal’s frequency, amplitude, and jitter. Use a high-bandwidth oscilloscope with a low-capacitance probe to capture the clock waveform accurately. Verify that the frequency is within the specified tolerance and that the amplitude and jitter levels are acceptable for the MCU.
EMI and EMC Testing
Conduct electromagnetic interference (EMI) and electromagnetic compatibility (EMC) testing to ensure that the system meets regulatory requirements and does not interfere with other electronic devices. Follow established test procedures and use appropriate test equipment, such as spectrum analyzers and EMI receivers, to measure emissions and susceptibility levels.
Conclusion
Proper power supply line routing and crystal placement are essential for ensuring reliable and efficient operation of MCU-based systems. By following best practices and guidelines for component placement, trace routing, and layer stackup, designers can minimize noise, reduce signal integrity issues, and optimize system performance. Thorough testing and verification should be conducted to validate the design and ensure compliance with regulatory standards.
Frequently Asked Questions (FAQ)
1. What is the purpose of decoupling capacitors in an MCU power supply?
Decoupling capacitors serve two main purposes in an MCU power supply: they provide a local energy reservoir to supply current during sudden demands, and they filter out high-frequency noise from the power supply lines, ensuring a clean and stable voltage for the MCU.
2. How do I select the appropriate decoupling capacitor values for my MCU?
The selection of decoupling capacitor values depends on factors such as the MCU’s power requirements, the frequency range of the noise to be filtered, and the target impedance. Typical decoupling capacitor values for MCUs range from 0.01 µF to 10 µF. It’s common to use a combination of smaller and larger capacitors to provide effective decoupling across a wide frequency range.
3. Why is it important to place the crystal oscillator close to the MCU?
Placing the crystal oscillator close to the MCU minimizes the trace length between the components, which reduces the risk of noise pickup and signal integrity issues. Shorter traces also minimize the loop area, which helps to reduce the effect of electromagnetic interference (EMI) on the oscillator circuit.
4. What are the benefits of using power and ground planes in a PCB Design?
Power and ground planes offer several benefits in a PCB design, especially for MCU-based systems. They provide lower impedance and inductance compared to narrow traces, ensuring better current distribution and reduced voltage drop. Planes also improve noise immunity and shielding, helping to protect sensitive circuits from interference.
5. How can I verify the power supply quality and crystal oscillator performance in my MCU-based system?
To verify the power supply quality, use an oscilloscope to measure voltage levels, ripple, and noise at various points in the system. Ensure that the measured values are within the MCU’s specified limits. For the crystal oscillator, measure the clock signal’s frequency, amplitude, and jitter using a high-bandwidth oscilloscope. Verify that the frequency is within the specified tolerance and that the amplitude and jitter levels are acceptable for the MCU. Additionally, conduct EMI and EMC testing to ensure that the system meets regulatory requirements and does not interfere with other electronic devices.
Leave a Reply