What is a Wire Harness?
A wire harness is a collection of wires, cables, connectors, and terminals that are pre-assembled into a single unit to simplify the installation and interconnection of electrical components. The purpose of a wire harness is to efficiently and securely transmit electrical signals or power between different parts of a system, such as in a vehicle, aircraft, or medical device.
Wire harnesses offer several advantages over loose wires:
- Organization: Wire harnesses keep wires neatly bundled and routed, making the system more organized and easier to maintain.
- Protection: The outer covering of a wire harness, such as a sheath or conduit, protects the wires from environmental factors like heat, moisture, and abrasion.
- Efficiency: Pre-assembled wire harnesses reduce installation time and minimize the risk of wiring errors.
- Space-saving: By bundling wires together, wire harnesses take up less space than loose wires, which is particularly important in applications where space is limited.
Types of Wire Harnesses
There are several types of wire harnesses, each designed for specific applications and environments:
- Automotive Wire Harnesses
- Engine harnesses
- Chassis harnesses
- Body harnesses
-
Dashboard harnesses
-
Aerospace Wire Harnesses
- Avionics harnesses
- Cabin interior harnesses
- Engine control harnesses
-
Fuel system harnesses
-
Medical Equipment Wire Harnesses
- Patient monitoring harnesses
- Surgical equipment harnesses
-
Diagnostic imaging harnesses
-
Telecommunications Wire Harnesses
- Fiber optic cable assemblies
- Copper cable assemblies
-
Data center harnesses
-
Industrial Wire Harnesses
- Machine control harnesses
- Robotics harnesses
- Sensor and actuator harnesses
Custom Wire Harness Manufacturing Process
The process of manufacturing custom wire harnesses involves several steps:
- Design and Engineering
- Understand customer requirements and specifications
- Create detailed schematics and drawings
- Select appropriate wires, connectors, and components
-
Optimize harness layout for performance and manufacturability
-
Prototyping
- Build prototype harnesses for testing and validation
- Conduct functional and environmental testing
-
Incorporate customer feedback and make necessary revisions
-
Production
- Cut wires to specified lengths
- Strip wire insulation and terminate wires with connectors or terminals
- Assemble wires into bundles and secure with ties, tape, or conduit
- Label harnesses for identification and installation
-
Perform quality control inspections and electrical tests
-
Packaging and Shipping
- Package harnesses to protect them during transportation
- Label packages with customer information and shipping details
- Ship harnesses to customer site or integrate them into larger assemblies
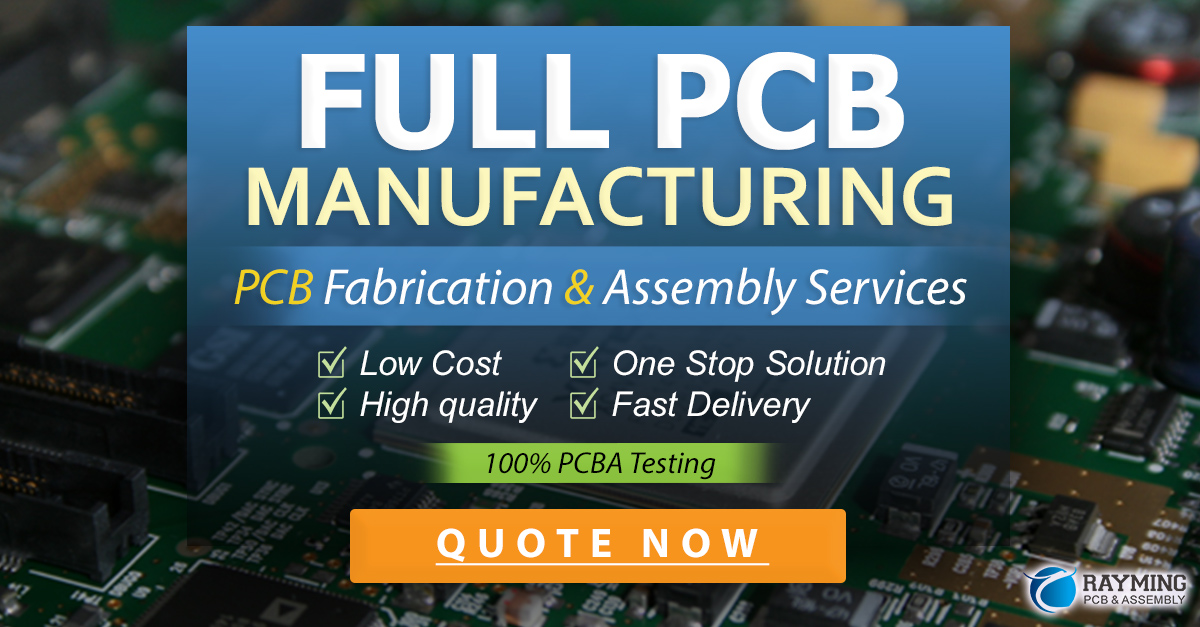
Choosing a Custom Wire Harness Manufacturer
When selecting a custom wire harness manufacturer, consider the following factors:
- Experience and Expertise
- Look for manufacturers with a proven track record in your industry
-
Ensure they have the technical expertise to handle your specific requirements
-
Quality Management
- Choose a manufacturer with a robust quality management system, such as ISO 9001
-
Inquire about their quality control processes and testing capabilities
-
Production Capacity
- Assess the manufacturer’s ability to meet your volume requirements and delivery schedules
-
Consider their flexibility to accommodate changes in demand
-
Cost and Value
- Obtain quotes from multiple manufacturers and compare pricing
-
Evaluate the value-added services they offer, such as design support and inventory management
-
Customer Service and Support
- Select a manufacturer that is responsive and communicative
- Ensure they provide timely technical support and problem resolution
Benefits of Working with a Custom Wire Harness Manufacturer
Partnering with a custom wire harness manufacturer offers several benefits:
- Improved Product Quality
- Benefit from the manufacturer’s expertise in wire harness design and manufacturing
-
Ensure consistent quality through their established processes and quality control measures
-
Cost Savings
- Reduce costs by leveraging the manufacturer’s economies of scale and purchasing power
-
Minimize waste and rework by using their optimized designs and production methods
-
Faster Time-to-Market
- Accelerate your product development cycle by outsourcing wire harness manufacturing
-
Focus on your core competencies while the manufacturer handles the wire harness production
-
Scalability and Flexibility
- Scale your production up or down as needed without investing in additional equipment or personnel
- Adapt quickly to changes in product design or market demand
Wire Harness Materials and Components
Custom wire harnesses are made from a variety of materials and components, each selected based on the specific application requirements:
Wires and Cables
Type | Description | Application |
---|---|---|
PVC | Polyvinyl chloride insulation, low cost, general-purpose | Automotive, appliances |
Teflon | PTFE insulation, high temperature, chemical resistance | Aerospace, medical |
Silicone | Flexible, high temperature, moisture resistance | Automotive, industrial |
Coaxial | Shielded cable for high-frequency signals | Telecommunications, medical imaging |
Fiber Optic | High-speed data transmission, immunity to electromagnetic interference | Telecommunications, aerospace |
Connectors and Terminals
Type | Description | Application |
---|---|---|
Crimp | Solderless connection, quick and reliable | Automotive, industrial |
Solder | Permanent connection, high strength | Aerospace, medical |
IDC | Insulation displacement connection, high-density | Telecommunications |
D-Sub | Rectangular, multi-pin, various sizes | Industrial, telecommunications |
Circular | Threaded or bayonet coupling, environmental sealing | Aerospace, military |
Harness Protection
Type | Description | Application |
---|---|---|
Conduit | Rigid or flexible tubing, mechanical protection | Automotive, industrial |
Braided Sleeving | Expandable, abrasion resistance | Aerospace, military |
Heat-Shrink Tubing | Seals and insulates connections, strain relief | Automotive, electronics |
EMI Shielding | Conductive materials, shields against electromagnetic interference | Aerospace, medical |
Quality Control and Testing
To ensure the reliability and performance of custom wire harnesses, manufacturers employ various quality control measures and testing methods:
- Visual Inspection
- Check for correct wire colors, lengths, and routing
- Verify proper connector and terminal crimping or soldering
-
Ensure labels and markings are correct and legible
-
Continuity Testing
- Verify electrical continuity between specified points
-
Identify open circuits, short circuits, or high-resistance connections
-
Insulation Resistance Testing
- Measure the resistance between conductors and the harness shielding or ground
-
Detect insulation damage or degradation
-
Dielectric Withstand Testing
- Apply high voltage between conductors and the harness shielding or ground
-
Verify the insulation can withstand the specified voltage without breakdown
-
Environmental Testing
- Expose harnesses to temperature extremes, humidity, vibration, or other environmental stresses
- Ensure harness performance and reliability under expected operating conditions
Wire Harness Design Considerations
When designing custom wire harnesses, consider the following factors to ensure optimal performance and reliability:
- Electrical Requirements
- Determine the required voltage, current, and power ratings for each circuit
-
Select wire gauges and insulation materials accordingly
-
Environmental Factors
- Assess the operating temperature range, humidity, and exposure to chemicals or fluids
-
Choose materials and components that can withstand the expected environmental conditions
-
Mechanical Stress
- Consider the expected levels of vibration, shock, and mechanical stress
-
Design the harness routing and strain relief to minimize stress on wires and connections
-
Electromagnetic Compatibility (EMC)
- Evaluate the potential for electromagnetic interference (EMI) or radio frequency interference (RFI)
-
Incorporate shielding, grounding, and filtering techniques as needed
-
Maintainability and Serviceability
- Design the harness for ease of installation, maintenance, and repair
- Use modular connectors and labeled wires to simplify troubleshooting and replacement
Frequently Asked Questions (FAQ)
- How long does it take to design and manufacture a custom wire harness?
-
The lead time for custom wire harnesses varies depending on the complexity of the design, the availability of materials, and the manufacturer’s workload. Typical lead times range from 4 to 12 weeks, but expedited services may be available for urgent projects.
-
What industries use custom wire harnesses?
-
Custom wire harnesses are used in a wide range of industries, including:
- Automotive
- Aerospace
- Medical equipment
- Telecommunications
- Industrial machinery
- Consumer electronics
- Military and defense
-
Can custom wire harnesses be designed for harsh environments?
-
Yes, custom wire harnesses can be designed to withstand harsh environmental conditions, such as extreme temperatures, humidity, chemicals, and vibration. The key is to select the appropriate materials, components, and protection methods for the specific application.
-
How much do custom wire harnesses cost?
- The cost of custom wire harnesses depends on several factors, including:
- Complexity of the design
- Materials and components used
- Production volume
- Labor costs
- Testing and certification requirements
-
Generally, higher volumes and simpler designs result in lower per-unit costs. It’s best to obtain quotes from multiple manufacturers to compare pricing and value.
-
What certifications should a custom wire harness manufacturer have?
- Look for manufacturers with relevant certifications, such as:
- ISO 9001 for quality management systems
- AS9100 for aerospace quality management systems
- IATF 16949 for automotive quality management systems
- UL or CSA certification for safety and performance standards
- IPC/WHMA-A-620 for cable and wire harness manufacturing standards
- These certifications demonstrate the manufacturer’s commitment to quality, reliability, and industry best practices.
By partnering with an experienced and reputable custom wire harness manufacturer, you can ensure your electrical system is designed and built to meet your specific requirements while optimizing performance, reliability, and cost-effectiveness.
Leave a Reply