What is a Wire Harness?
A wire harness, also known as a cable harness or wiring loom, is an assembly of electrical wires or cables that transmit signals or electrical power. It is designed to simplify the wiring system by bundling multiple wires together, providing a more organized and efficient means of connecting various components within a device or system.
Key Components of a Wire Harness
To understand the Wire Harness Manufacturing process better, let’s first explore the key components that make up a typical wire harness:
-
Wires: The primary component of a wire harness, wires are conductors made of copper or aluminum that carry electrical current.
-
Connectors: These are the endpoints of the wire harness that allow it to interface with other devices or components. Connectors come in various types, such as plugs, sockets, and terminals.
-
Terminals: Terminals are conductive elements that provide a connection point for wires. They are usually crimped or soldered onto the wire ends.
-
Insulation: Insulation is a non-conductive material that surrounds the wires to prevent electrical leakage and protect against environmental factors such as heat, moisture, and abrasion.
-
Shielding: In some cases, wire harnesses may include shielding to protect against electromagnetic interference (EMI) or radio frequency interference (RFI).
-
Grommets and Seals: These components are used to protect the wire harness at entry and exit points, preventing damage and ensuring a secure fit.
Wire Harness Manufacturing Process
The wire harness manufacturing process involves several stages, each critical to ensuring the quality and functionality of the final product. Let’s dive into the step-by-step process:
Step 1: Design and Engineering
The first step in wire harness manufacturing is the design and engineering phase. This involves creating detailed schematics and drawings that specify the layout, dimensions, and materials of the wire harness. The design takes into account factors such as the intended application, operating environment, and performance requirements.
Step 2: Material Selection
Based on the design specifications, the appropriate materials are selected for the wire harness. This includes choosing the right type and gauge of wires, connectors, terminals, and insulation materials. The selection process considers factors such as current carrying capacity, temperature rating, flexibility, and durability.
Step 3: Cutting and Stripping
Once the materials are selected, the wires are cut to the required lengths and stripped at the ends to expose the conductor. This process is typically automated using wire cutting and stripping machines to ensure precision and consistency.
Wire Gauge | Stripping Length (mm) |
---|---|
22 AWG | 5 |
20 AWG | 6 |
18 AWG | 7 |
16 AWG | 8 |
14 AWG | 9 |
Step 4: Crimping and Soldering
The exposed wire ends are then crimped or soldered to the terminals or connectors. Crimping involves using a special tool to compress the terminal around the wire, creating a secure mechanical and electrical connection. Soldering, on the other hand, involves using a heated soldering iron to melt a conductive alloy (solder) onto the wire and terminal, forming a permanent bond.
Step 5: Insulation and Shielding
After crimping or soldering, the connections are insulated to protect against electrical shorts and environmental factors. This can be done using heat-shrink tubing, insulation sleeves, or other suitable materials. In some cases, additional shielding may be applied to the wire harness to mitigate EMI or RFI.
Step 6: Routing and Bundling
The insulated wires are then routed and bundled according to the designed layout. This process involves organizing the wires into groups, securing them with cable ties or tape, and ensuring proper spacing and strain relief. The goal is to create a neat and compact wire harness that is easy to install and maintain.
Harness Diameter (mm) | Cable Tie Width (mm) |
---|---|
0-10 | 2.5 |
10-20 | 3.6 |
20-30 | 4.8 |
30-40 | 7.6 |
40+ | 9.0 |
Step 7: Testing and Quality Control
Before the wire harness is considered complete, it undergoes rigorous testing and quality control procedures. This includes continuity testing to ensure proper electrical connections, insulation resistance testing to verify the integrity of the insulation, and high-voltage testing to check for any leakage or breakdown. Visual inspections are also performed to ensure the overall quality and conformance to the design specifications.
Step 8: Labeling and Packaging
Once the wire harness has passed all the necessary tests, it is labeled for identification purposes. This may include applying heat-shrink labels, printing directly on the insulation, or using adhesive labels. The labeling provides information such as the part number, revision level, and any relevant safety or handling instructions. Finally, the wire harness is packaged for storage or transportation, ensuring adequate protection against damage.
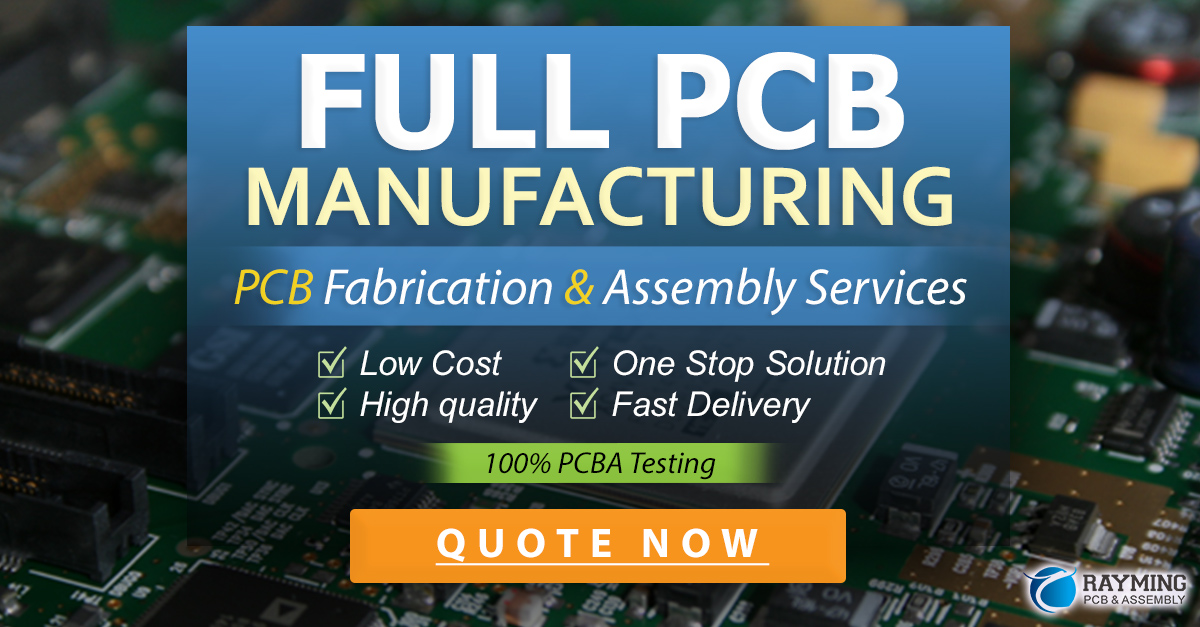
Best Practices in Wire Harness Manufacturing
To ensure the highest quality and reliability of wire harnesses, manufacturers should adhere to the following best practices:
-
Use high-quality materials: Select wires, connectors, and terminals that meet or exceed the requirements for the intended application. Consider factors such as temperature rating, current carrying capacity, and environmental resistance.
-
Follow industry standards: Adhere to relevant industry standards and regulations, such as IPC/WHMA-A-620 (Requirements and Acceptance for Cable and Wire Harness Assemblies), to ensure consistency and compliance.
-
Implement robust quality control: Establish a comprehensive quality control system that includes regular inspections, testing, and documentation. This helps identify and address any issues early in the manufacturing process.
-
Invest in automation: Utilize automated equipment and processes where possible to improve efficiency, consistency, and repeatability. This can include wire cutting, stripping, crimping, and testing.
-
Provide adequate training: Ensure that all personnel involved in the wire harness manufacturing process are properly trained and qualified. This includes knowledge of the specific materials, tools, and techniques used.
-
Continuously improve: Foster a culture of continuous improvement, encouraging employees to identify and suggest ways to optimize the manufacturing process, reduce waste, and enhance quality.
Frequently Asked Questions (FAQ)
- What is the difference between a wire harness and a cable assembly?
-
A wire harness is a collection of wires or cables bundled together to transmit signals or electrical power, often with connectors at the ends. A cable assembly, on the other hand, typically consists of a single cable with connectors at one or both ends.
-
How do I choose the right wire gauge for my wire harness?
-
The choice of wire gauge depends on the current carrying capacity required for the application. Refer to industry standards such as the American Wire Gauge (AWG) table to select the appropriate gauge based on the expected current load and temperature rating.
-
Can wire harnesses be customized for specific applications?
-
Yes, wire harnesses can be custom-designed and manufactured to meet specific application requirements. This involves tailoring the layout, materials, and components to suit the intended use case.
-
How can I ensure the durability of my wire harness?
-
To ensure durability, use high-quality materials that are rated for the expected operating conditions (e.g., temperature, humidity, chemical exposure). Additionally, apply appropriate insulation, shielding, and strain relief to protect the wires and connections from mechanical stress and environmental factors.
-
What are the common challenges in wire harness manufacturing, and how can they be addressed?
- Common challenges include managing complex designs, ensuring consistent quality, and minimizing production time and costs. These can be addressed by implementing standardized processes, investing in automation, providing thorough employee training, and continuously monitoring and improving the manufacturing process.
Conclusion
Wire harness manufacturing is a critical process that directly impacts the performance, reliability, and safety of various electrical and electronic systems. By understanding the step-by-step process, from design and material selection to assembly and testing, manufacturers can ensure the production of high-quality wire harnesses that meet the stringent requirements of diverse industries.
By adhering to best practices, investing in automation, and fostering a culture of continuous improvement, wire harness manufacturers can streamline their processes, reduce errors, and deliver products that exceed customer expectations. As technology advances and applications become more complex, the importance of robust and reliable wire harnesses will only continue to grow, making it crucial for manufacturers to stay at the forefront of this evolving industry.
Leave a Reply