Introduction to Via covering
Via covering is an essential technique used in the manufacturing of printed circuit boards (PCBs) to ensure the proper functioning and reliability of the board. In PCB Design, vias are small holes drilled through the board to create electrical connections between different layers. Via covering involves the process of filling or covering these holes with a conductive material, such as copper or a specialized Via Filling ink, to prevent issues like signal interference, physical damage, and contamination.
The Importance of Via Covering
Via covering plays a crucial role in the performance and longevity of PCBs. Some of the key reasons why via covering is important include:
-
Signal Integrity: Uncovered vias can act as antennas, causing signal interference and degrading the overall performance of the PCB. By covering the vias, this interference is minimized, ensuring better signal integrity.
-
Physical Protection: Exposed vias are vulnerable to physical damage, such as scratches or impacts, which can lead to broken connections and board failure. Via covering provides an extra layer of protection, increasing the durability of the PCB.
-
Contamination Prevention: Open vias can accumulate dust, moisture, and other contaminants, which can cause short circuits or corrosion. Covering the vias helps prevent the ingress of these contaminants, enhancing the reliability of the PCB.
-
Improved Manufacturing Process: Via covering allows for a smoother and more efficient PCB manufacturing process. Covered vias provide a flat surface for subsequent layers to be built upon, reducing the risk of defects and improving the overall quality of the board.
Methods of Via Covering
There are several methods used for via covering in PCB manufacturing. The choice of method depends on factors such as the desired performance, cost, and manufacturing capabilities. Some of the most common via covering methods include:
1. Via Filling
Via filling involves completely filling the via hole with a conductive material, creating a solid connection between the layers. This method provides excellent signal integrity and physical protection. There are two main types of via filling:
a. Conductive Epoxy Filling: In this method, a conductive epoxy paste is dispensed into the via hole and then cured using heat. This creates a solid, conductive connection between the layers. Conductive epoxy filling is often used for high-density PCBs and applications that require superior electrical performance.
b. Copper Plating: Copper plating involves electroplating the via hole with copper until it is completely filled. This method provides a highly conductive and robust connection between the layers. Copper plating is commonly used in high-reliability applications, such as aerospace and military electronics.
2. Via Capping
Via capping is a method where a thin layer of conductive material is applied over the top and bottom of the via, rather than filling it completely. This method is less expensive and faster than via filling, making it a popular choice for many PCB Manufacturers. There are two main types of via capping:
a. Copper Capping: In this method, a thin layer of copper is electroplated over the top and bottom of the via. This creates a conductive cap that covers the via hole, providing protection and improving signal integrity. Copper capping is often used in high-frequency applications and designs that require controlled impedance.
b. Organic Solderability Preservative (OSP) Capping: OSP capping involves applying a thin, organic coating over the via. This coating acts as a protective barrier, preventing oxidation and contamination of the exposed copper. OSP capping is a cost-effective option for PCBs that do not require the same level of performance as those with copper capping.
3. Via Tenting
Via tenting is a method where the via is covered by the solder mask layer during the PCB Fabrication process. In this method, the solder mask is applied over the via, creating a tent-like structure that covers the hole. Via tenting is a simple and inexpensive method of via covering, but it does not provide the same level of protection and performance as via filling or capping.
Factors to Consider When Choosing a Via Covering Method
When selecting a via covering method for a PCB design, there are several factors to consider. These include:
-
Electrical Performance: The desired electrical performance of the PCB should be a key consideration when choosing a via covering method. For high-frequency or high-speed applications, via filling or copper capping may be necessary to ensure optimal signal integrity.
-
Physical Protection: The level of physical protection required for the PCB will influence the choice of via covering method. For applications that require high durability, such as those exposed to harsh environments, via filling may be the best option.
-
Manufacturing Cost: The cost of the via covering method should be considered in relation to the overall project budget. Via filling and copper capping are generally more expensive than OSP capping or via tenting.
-
Manufacturing Capabilities: The chosen via covering method must be compatible with the capabilities of the PCB manufacturer. Some methods, such as copper plating, require specialized equipment and expertise.
-
Design Constraints: The PCB design itself may dictate the choice of via covering method. For example, high-density designs with small via sizes may require via filling to ensure proper connections between layers.
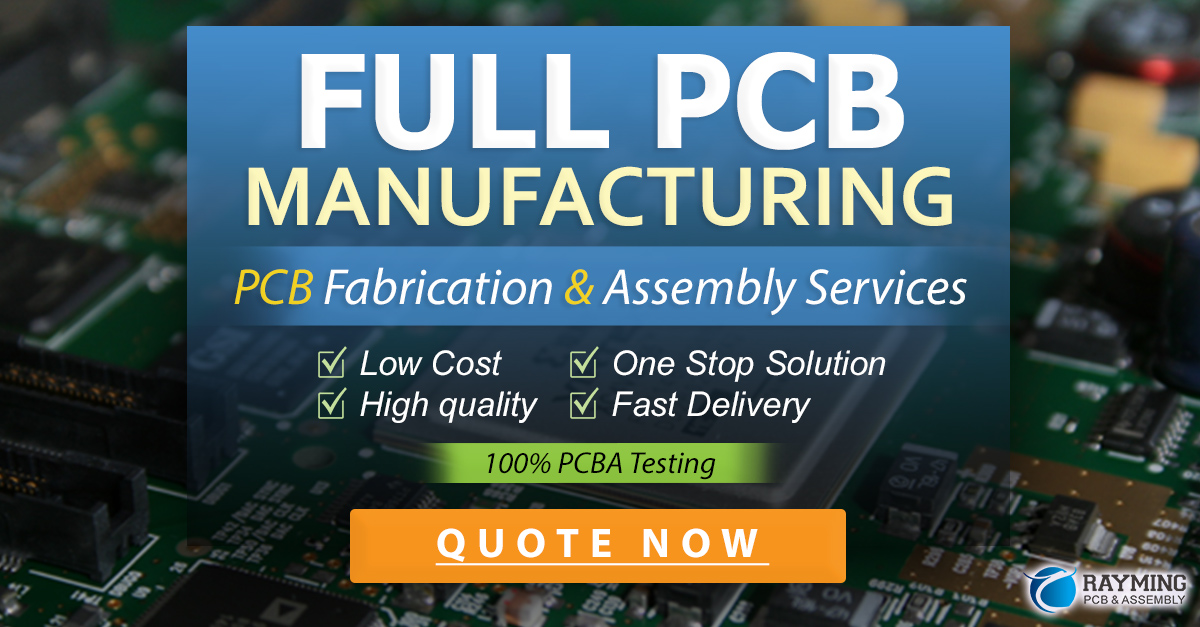
Best Practices for Via Covering in PCB Design
To ensure optimal performance and reliability of PCBs, designers should follow best practices when implementing via covering. Some of these best practices include:
-
Choose the appropriate via covering method: Select the via covering method that best suits the requirements of the PCB, considering factors such as electrical performance, physical protection, cost, and manufacturing capabilities.
-
Minimize the number of vias: Reduce the number of vias in the PCB design wherever possible. This not only simplifies the manufacturing process but also reduces the potential for signal interference and physical damage.
-
Ensure proper via size: The size of the vias should be appropriate for the chosen via covering method. For example, via filling requires larger via sizes compared to via capping to ensure complete filling of the hole.
-
Follow manufacturer guidelines: Always follow the guidelines provided by the PCB manufacturer for the chosen via covering method. This includes specifications for via size, spacing, and any special requirements for the manufacturing process.
-
Test and validate the design: Before finalizing the PCB design, test and validate the performance of the chosen via covering method. This may involve simulations, prototyping, or consultation with the PCB manufacturer to ensure the desired results are achieved.
FAQ
-
Q: What is the purpose of via covering in PCBs?
A: Via covering serves several purposes, including improving signal integrity, providing physical protection, preventing contamination, and enhancing the PCB manufacturing process. -
Q: What are the main methods of via covering?
A: The main methods of via covering are via filling (conductive epoxy or copper plating), via capping (copper or OSP), and via tenting. -
Q: Which via covering method provides the best electrical performance?
A: Via filling, particularly with copper plating, provides the best electrical performance due to the complete filling of the via hole with a highly conductive material. -
Q: Is via covering always necessary in PCB design?
A: While via covering is not always necessary, it is highly recommended for PCBs that require high reliability, durability, and signal integrity. The decision to implement via covering should be based on the specific requirements of the application. -
Q: How does via covering affect the cost of PCB manufacturing?
A: Via covering methods, such as via filling and copper capping, can increase the cost of PCB manufacturing due to the additional materials and processing steps required. However, the improved performance and reliability provided by via covering can offset these costs in the long run.
Conclusion
Via covering is a critical aspect of PCB manufacturing that ensures the proper functioning, reliability, and durability of the board. By choosing the appropriate via covering method and following best practices in PCB design, designers can create high-quality boards that meet the specific requirements of their applications. As technology continues to advance, via covering techniques will undoubtedly evolve to address the ever-increasing demands for performance and reliability in the electronics industry.
Via Covering Method | Advantages | Disadvantages |
---|---|---|
Conductive Epoxy Filling | – Excellent signal integrity – Superior electrical performance – High physical protection |
– Higher cost compared to other methods – Longer processing time |
Copper Plating | – High conductivity – Robust connection between layers – Ideal for high-reliability applications |
– Requires specialized equipment – Higher cost compared to other methods |
Copper Capping | – Improves signal integrity – Provides protection against contamination – Suitable for high-frequency applications |
– Less physical protection compared to via filling – Higher cost than OSP capping |
OSP Capping | – Cost-effective – Protects against oxidation and contamination |
– Lower performance compared to copper capping – Not suitable for high-frequency applications |
Via Tenting | – Simple and inexpensive – Quick to implement |
– Limited protection and performance compared to other methods |
By understanding the advantages and disadvantages of each via covering method, PCB designers can make informed decisions when selecting the most appropriate technique for their specific applications. This knowledge, combined with adherence to best practices and close collaboration with PCB manufacturers, will help ensure the production of high-quality, reliable PCBs that meet the demands of today’s ever-evolving electronics landscape.
Leave a Reply