Introduction to Component Arrangement in Assembly Design
Component arrangement is a critical aspect of assembly design that involves organizing and positioning the individual parts and subassemblies within an overall assembly. The goal is to optimize factors such as functionality, ease of assembly, maintainability, and space utilization while minimizing interference and maximizing performance.
Effective component arrangement requires careful consideration of numerous factors, including:
- Functional requirements and interactions between components
- Assembly sequence and accessibility for installation and maintenance
- Space constraints and packaging efficiency
- Ergonomics and human factors
- Manufacturing and assembly processes
- Serviceability and replacement of components
- Material flow and handling
- Aesthetics and appearance
By addressing these factors through systematic planning and iterative design, engineers can develop assembly designs that are efficient, reliable, and cost-effective.
Key Principles of Component Arrangement
Several key principles guide the process of component arrangement in assembly design:
Functional Grouping
Components that work together to perform a specific function should be grouped and positioned in close proximity to each other. This functional grouping simplifies the design, reduces the complexity of interfaces, and improves the overall performance of the assembly.
Modular Design
Breaking down the assembly into smaller, self-contained modules can greatly simplify the arrangement of components. Each module can be designed, manufactured, and tested independently, allowing for parallel development and easier integration. Modular design also facilitates maintenance, upgrades, and reuse of components across different assemblies.
Accessibility and Maintainability
Components should be arranged in a way that allows for easy access during assembly, maintenance, and repair operations. This includes providing sufficient clearance for tools, considering the sequence of installation and removal, and minimizing the need for specialized equipment or complex procedures.
Space Utilization
Efficient use of available space is crucial in assembly design, especially in applications where size and weight are critical factors. Components should be arranged to minimize empty spaces, avoid interference, and optimize the overall packaging of the assembly. Techniques such as nesting, stacking, and folding can be used to make the most of limited space.
Ergonomics and Human Factors
The arrangement of components should take into account the ergonomic requirements of operators and maintenance personnel. This includes ensuring that frequently accessed components are within easy reach, providing clear visual access, and minimizing the need for awkward postures or excessive force.
Manufacturing and Assembly Processes
The arrangement of components must be compatible with the chosen manufacturing and assembly processes. This includes considering the sequence of operations, the need for fixtures and jigs, and the limitations of available equipment. Design for Assembly (DFA) principles can be applied to simplify the assembly process and reduce the number of parts and operations required.
Methods and Tools for Component Arrangement
Several methods and tools are available to support the process of component arrangement in assembly design:
Computer-Aided Design (CAD) Software
CAD software provides a powerful platform for creating, visualizing, and manipulating 3D models of assemblies and their components. Modern CAD tools offer features such as:
- Assembly modeling and constraint-based positioning
- Interference checking and clearance analysis
- Exploded views and animated assembly sequences
- Bill of Materials (BOM) generation and management
- Integration with simulation and analysis tools
CAD Software | Key Features |
---|---|
SolidWorks | Robust assembly modeling, interference detection, BOM management |
Autodesk Inventor | Advanced assembly modeling, dynamic simulation, design automation |
CATIA | Powerful assembly design tools, kinematic analysis, virtual prototyping |
Creo (Pro/ENGINEER) | Flexible assembly modeling, top-down design, associative BOM |
Using CAD software, engineers can quickly explore different component arrangements, evaluate their feasibility, and optimize the design based on various criteria.
Design for Assembly (DFA) Analysis
DFA is a systematic methodology for analyzing and improving the assemblability of a product. It involves evaluating each component and interface in terms of handling, insertion, and fastening difficulty, and identifying opportunities for simplification and standardization. DFA software tools, such as Boothroyd Dewhurst DFMA, provide quantitative metrics and guidelines for optimizing the arrangement of components.
Physical Prototyping and Mock-Ups
Building physical prototypes or mock-ups of the assembly can provide valuable insights into the practicality and ergonomics of the component arrangement. These can range from simple cardboard or foam models to fully functional prototypes using 3D printing or CNC machining. Physical prototypes allow designers to assess factors such as accessibility, clearances, and human interaction that may be difficult to evaluate in a virtual environment.
Virtual Reality (VR) and Augmented Reality (AR)
VR and AR technologies are increasingly being used in assembly design to provide immersive, interactive experiences of the component arrangement. VR allows designers to explore and manipulate the assembly in a virtual environment, while AR overlays digital information onto physical objects or spaces. These technologies can be used for tasks such as:
- Evaluating the accessibility and ergonomics of component placement
- Simulating assembly and maintenance procedures
- Collaborating with remote teams and stakeholders
- Training operators and technicians
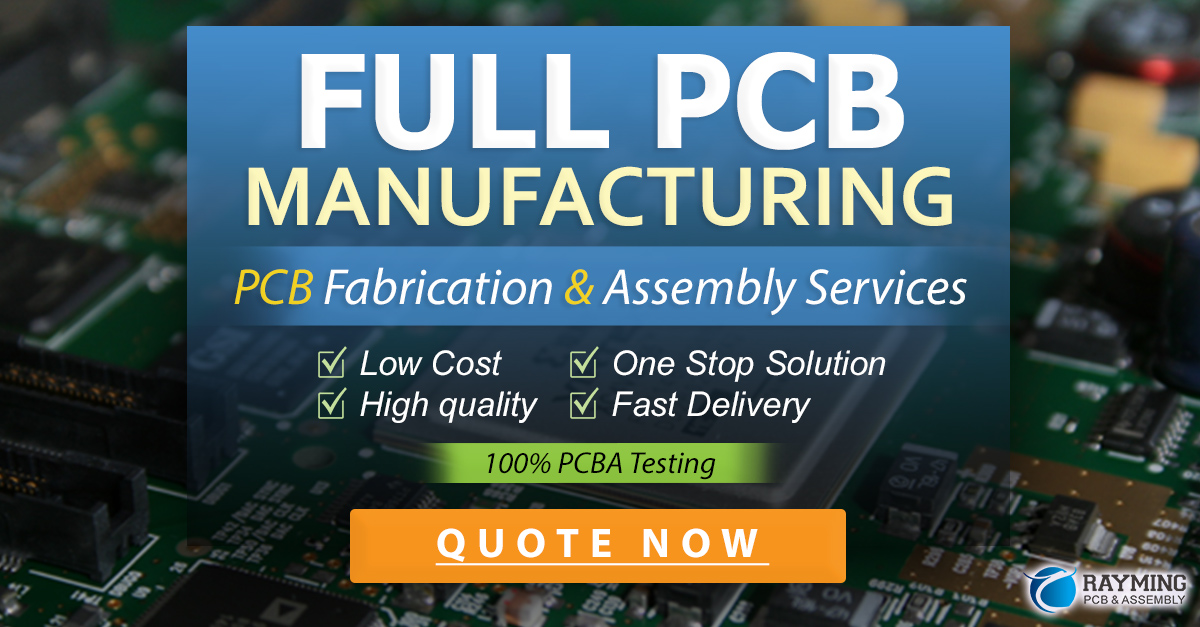
Case Studies and Examples
Automotive Engine Assembly
In the design of an automotive engine, the arrangement of components is critical for optimizing performance, efficiency, and maintainability. Key considerations include:
- Grouping of related components (e.g., intake manifold, fuel injectors, throttle body)
- Accessibility for maintenance and service (e.g., oil filter, spark plugs)
- Clearance for moving parts (e.g., crankshaft, camshafts, valves)
- Routing of hoses, wires, and cables
- Compatibility with the engine bay packaging and vehicle chassis
Component Group | Arrangement Considerations |
---|---|
Intake System | Proximity to engine, flow optimization, air filter access |
Fuel System | Injector placement, fuel rail routing, pump location |
Lubrication System | Oil pan capacity, pump placement, filter access |
Cooling System | Radiator placement, thermostat location, hose routing |
By carefully arranging the components and subsystems, engineers can create an engine assembly that is compact, efficient, and easy to maintain.
Medical Device Assembly
Medical devices often require complex assemblies with numerous small, precise components. The arrangement of these components must ensure reliable functionality, ease of use, and compatibility with sterilization and packaging requirements. Example considerations include:
- Grouping of components by function (e.g., sensors, actuators, power supply)
- Minimizing the number of parts and simplifying the assembly process
- Ensuring clear access for user interaction and display of information
- Providing adequate clearance for cables, tubing, and connectors
- Designing for modularity and easy replacement of components
Component Group | Arrangement Considerations |
---|---|
User Interface | Ergonomic placement of buttons, displays, and ports |
Sensing Elements | Positioning for optimal signal acquisition and noise reduction |
Actuation Mechanisms | Clearance for moving parts, alignment with force transmission |
Power and Control | Battery placement, PCB layout, cable routing |
Through careful component arrangement and iterative prototyping, medical device designers can create assemblies that are reliable, user-friendly, and suitable for mass production.
Best Practices and Guidelines
To optimize the arrangement of components in assembly design, consider the following best practices and guidelines:
- Start with a clear understanding of the functional requirements and design constraints.
- Use modular design principles to break down the assembly into manageable subassemblies.
- Group components by function and position them to minimize interfaces and complexity.
- Ensure adequate accessibility for assembly, maintenance, and repair operations.
- Optimize the use of available space while avoiding interference and leaving room for future upgrades.
- Consider the ergonomics and human factors involved in the assembly and use of the product.
- Design for compatibility with manufacturing and assembly processes, using DFA principles.
- Leverage CAD software and DFA tools to explore and evaluate different component arrangements.
- Build physical prototypes or use VR/AR technology to validate the practicality and usability of the design.
- Continuously iterate and refine the component arrangement based on feedback and analysis.
By following these best practices and adapting them to the specific needs of each project, engineers can create assembly designs that are efficient, reliable, and cost-effective.
Frequently Asked Questions (FAQ)
-
What is the importance of component arrangement in assembly design?
Component arrangement is crucial for optimizing the functionality, accessibility, and manufacturability of an assembly. It directly impacts factors such as performance, ease of assembly, maintainability, and space utilization. -
What are some key principles to consider when arranging components in an assembly?
Some key principles include functional grouping, modular design, accessibility and maintainability, space utilization, ergonomics and human factors, and compatibility with manufacturing and assembly processes. -
How can CAD software help in the process of component arrangement?
CAD software provides tools for creating, visualizing, and manipulating 3D models of assemblies and their components. It enables engineers to explore different arrangements, check for interferences, generate BOMs, and integrate with simulation and analysis tools. -
What is Design for Assembly (DFA), and how does it relate to component arrangement?
DFA is a methodology for analyzing and improving the assemblability of a product. It involves evaluating each component and interface in terms of handling, insertion, and fastening difficulty, and identifying opportunities for simplification and standardization. DFA principles guide the optimization of component arrangement for efficient assembly. -
How can physical prototyping and VR/AR technology support the evaluation of component arrangements?
Physical prototypes and mock-ups allow designers to assess factors such as accessibility, clearances, and human interaction that may be difficult to evaluate in a virtual environment. VR and AR technologies provide immersive, interactive experiences of the component arrangement, enabling tasks such as evaluating ergonomics, simulating procedures, and collaborating with remote teams.
Conclusion
The arrangement of components in assembly design is a critical aspect that directly impacts the functionality, efficiency, and manufacturability of a product. By considering key principles such as functional grouping, modular design, accessibility, space utilization, ergonomics, and manufacturing compatibility, engineers can develop assembly designs that are optimized for performance and cost-effectiveness.
The use of CAD software, DFA tools, physical prototyping, and VR/AR technology supports the process of component arrangement by enabling the exploration, evaluation, and validation of different design options. By following best practices and continuously iterating based on feedback and analysis, engineers can create assembly designs that meet the specific requirements of each project while ensuring reliability, usability, and efficiency.
As the complexity of products continues to increase and the demand for customization and rapid innovation grows, the importance of effective component arrangement in assembly design will only continue to rise. By staying up-to-date with the latest tools, techniques, and best practices, engineers can deliver assembly designs that drive success in today’s competitive market.
Leave a Reply