Introduction to Solder Paste Data Preparation
Solder paste data preparation is a crucial step in the surface mount technology (SMT) assembly process. It involves gathering and analyzing data related to Solder Paste Printing to ensure optimal performance and quality of the final assembled product. Proper solder paste data preparation can help identify potential issues, improve process control, and ultimately lead to higher yields and reduced defects.
In this article, we will delve into the various aspects of solder paste data preparation, including:
- Types of data to collect
- Data collection methods
- Data analysis techniques
- Best practices for data preparation
- Frequently asked questions (FAQ) about solder paste data preparation
Types of Data to Collect for Solder Paste Printing
When preparing data for solder paste printing, it is essential to collect relevant information that can provide insights into the process performance and help identify areas for improvement. Some of the key types of data to collect include:
1. Solder Paste Volume
Solder paste volume refers to the amount of solder paste deposited on the printed circuit board (PCB) pads during the printing process. It is a critical parameter that directly affects the quality of the solder joints and the overall reliability of the assembled product. Data on solder paste volume can be collected using 3D solder paste inspection (SPI) systems or other measurement techniques.
2. Solder Paste Height
Solder paste height is another important parameter that influences the quality of the solder joints. It refers to the vertical dimension of the solder paste deposit on the PCB Pads. Data on solder paste height can be collected using SPI systems or other measurement methods, such as cross-sectioning and microscopy.
3. Solder Paste Area
Solder paste area refers to the two-dimensional coverage of the solder paste deposit on the PCB pads. It is an important factor that affects the wetting and spreading of the solder during the reflow process. Data on solder paste area can be collected using SPI systems or other imaging techniques.
4. Solder Paste Offset
Solder paste offset refers to the positional accuracy of the solder paste deposit relative to the PCB pads. It is important to ensure that the solder paste is deposited within the specified tolerances to avoid issues such as bridging or insufficient solder joint formation. Data on solder paste offset can be collected using SPI systems or other measurement techniques.
5. Stencil Aperture Measurements
Stencil aperture measurements refer to the dimensions and geometry of the openings in the solder paste stencil through which the solder paste is deposited onto the PCB pads. These measurements are critical for ensuring consistent and accurate solder paste printing. Data on stencil aperture measurements can be collected using specialized measurement tools or imaging systems.
Here is a table summarizing the types of data to collect for solder paste printing:
Data Type | Description | Collection Methods |
---|---|---|
Solder Paste Volume | Amount of solder paste deposited on PCB pads | 3D SPI systems, other measurement techniques |
Solder Paste Height | Vertical dimension of solder paste deposit on PCB pads | SPI systems, cross-sectioning, microscopy |
Solder Paste Area | 2D coverage of solder paste deposit on PCB pads | SPI systems, imaging techniques |
Solder Paste Offset | Positional accuracy of solder paste deposit relative to PCB pads | SPI systems, other measurement techniques |
Stencil Aperture Measurements | Dimensions and geometry of openings in solder paste stencil | Specialized measurement tools, imaging systems |
Data Collection Methods for Solder Paste Printing
Collecting accurate and reliable data is essential for effective solder paste data preparation. There are various methods and tools available for collecting data related to solder paste printing, including:
1. 3D Solder Paste Inspection (SPI) Systems
3D SPI systems are automated inspection machines that use structured light or laser scanning techniques to measure the volume, height, and area of solder paste deposits on PCB pads. These systems provide high-resolution, non-contact measurements and can quickly inspect large numbers of PCBs. SPI systems generate detailed data reports that can be used for process analysis and optimization.
2. 2D Solder Paste Inspection Systems
2D SPI systems are simpler and less expensive than their 3D counterparts. They use imaging techniques, such as machine vision or area scan cameras, to measure the area and positional accuracy of solder paste deposits on PCB pads. While 2D SPI systems do not provide volumetric measurements, they can still provide valuable data for process monitoring and control.
3. Cross-Sectioning and Microscopy
Cross-sectioning and microscopy involve physically cutting through the solder paste deposit and examining the cross-section under a microscope. This method provides a detailed view of the solder paste height and shape, allowing for accurate measurements. However, cross-sectioning is a destructive technique and is typically used for offline analysis or process validation rather than real-time data collection.
4. Manual Measurement Tools
Manual measurement tools, such as calipers or micrometers, can be used to measure the dimensions of solder paste deposits or stencil apertures. While these methods are simple and low-cost, they are time-consuming and prone to human error. Manual measurements are generally not suitable for high-volume production environments.
5. Stencil Aperture Measurement Systems
Stencil aperture measurement systems are specialized tools designed to accurately measure the dimensions and geometry of the openings in solder paste stencils. These systems use optical or contact measurement techniques to provide detailed data on aperture size, shape, and position. Accurate stencil aperture measurements are critical for ensuring consistent solder paste printing performance.
Here is a table comparing the various data collection methods for solder paste printing:
Method | Advantages | Disadvantages |
---|---|---|
3D Solder Paste Inspection (SPI) Systems | High-resolution, non-contact measurements, automated inspection, detailed data reports | Higher cost, complexity |
2D Solder Paste Inspection Systems | Lower cost, simpler than 3D systems, suitable for area and position measurements | Limited to 2D measurements, no volumetric data |
Cross-Sectioning and Microscopy | Detailed view of solder paste height and shape, accurate measurements | Destructive technique, offline analysis, time-consuming |
Manual Measurement Tools | Simple, low-cost | Time-consuming, prone to human error, not suitable for high-volume production |
Stencil Aperture Measurement Systems | Accurate measurements of stencil aperture dimensions and geometry | Specialized equipment, additional cost |
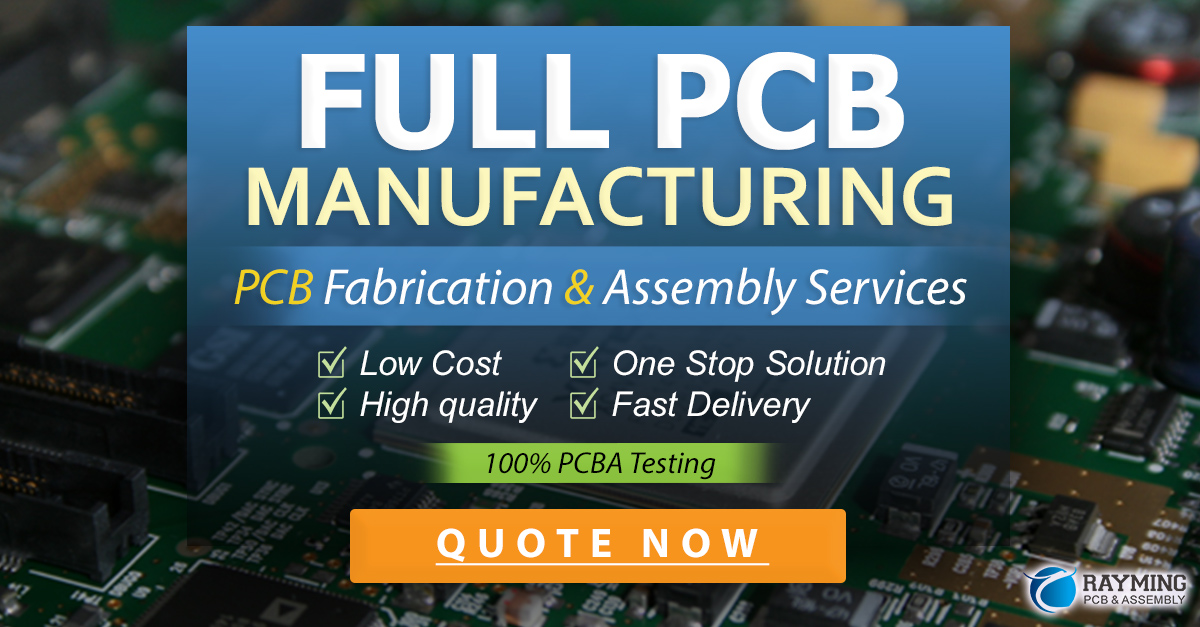
Data Analysis Techniques for Solder Paste Printing
Once the solder paste printing data has been collected, it is important to analyze the data to gain insights into the process performance and identify potential issues. There are several data analysis techniques that can be used for solder paste data preparation, including:
1. Statistical Process Control (SPC)
SPC is a method of monitoring and controlling a process through statistical analysis. It involves collecting data on process parameters, such as solder paste volume or height, and using control charts to identify trends, variations, and out-of-control conditions. SPC can help detect process shifts, reduce variability, and improve overall process performance.
2. Capability Analysis
Capability analysis is a technique used to assess the ability of a process to meet specified requirements or tolerances. It involves comparing the process data, such as solder paste volume or offset, to the specified limits and calculating capability indices, such as Cp and Cpk. Capability analysis can help determine if the process is capable of consistently producing products that meet the required specifications.
3. Design of Experiments (DOE)
DOE is a structured approach to systematically varying process parameters to identify their effects on the output variables. In the context of solder paste printing, DOE can be used to optimize process settings, such as stencil aperture dimensions, print speed, or squeegee pressure, to achieve the desired solder paste deposit characteristics. DOE helps identify the most influential factors and their interactions, allowing for process optimization and robustness.
4. Machine Learning and Predictive Analytics
Machine learning and predictive analytics involve using advanced algorithms and statistical models to analyze large amounts of process data and identify patterns, correlations, and trends. These techniques can be applied to solder paste printing data to predict process performance, identify potential defects, and optimize process parameters in real-time. Machine learning models can be trained on historical data and continuously updated with new data to improve their accuracy and adaptability.
Here is a table summarizing the data analysis techniques for solder paste printing:
Technique | Description | Benefits |
---|---|---|
Statistical Process Control (SPC) | Monitoring and controlling process through statistical analysis | Detects process shifts, reduces variability, improves performance |
Capability Analysis | Assessing process ability to meet specified requirements | Determines if process is capable of meeting specifications |
Design of Experiments (DOE) | Systematically varying parameters to identify effects on output | Optimizes process settings, improves robustness |
Machine Learning and Predictive Analytics | Analyzing large amounts of data to identify patterns and trends | Predicts performance, identifies defects, optimizes parameters in real-time |
Best Practices for Solder Paste Data Preparation
To ensure effective solder paste data preparation, it is important to follow best practices that promote data accuracy, consistency, and usefulness. Some of the key best practices include:
1. Establish Clear Data Collection Procedures
Develop and document clear procedures for collecting solder paste printing data, including the types of data to collect, the measurement methods to use, and the frequency of data collection. Ensure that all personnel involved in data collection are properly trained and follow the established procedures consistently.
2. Use Automated Data Collection Systems
Whenever possible, use automated data collection systems, such as 3D SPI machines, to collect solder paste printing data. Automated systems provide more accurate, consistent, and detailed data compared to manual methods. They also reduce the risk of human error and save time in the data collection process.
3. Implement Data Quality Checks
Implement data quality checks to ensure the accuracy and reliability of the collected data. This may involve setting up validation rules, such as range checks or cross-referencing with other data sources, to identify and eliminate erroneous or outlier data points. Regularly review and clean the data to maintain its integrity.
4. Standardize Data Formats and Storage
Standardize the formats and storage of solder paste printing data to ensure consistency and ease of access. Use a centralized database or data management system to store and organize the data in a structured manner. Ensure that the data is properly labeled, timestamped, and linked to relevant process information, such as PCB design, stencil specifications, or machine settings.
5. Collaborate with Cross-Functional Teams
Collaborate with cross-functional teams, including process engineers, quality engineers, and production personnel, to ensure that the collected data is relevant, actionable, and aligned with business objectives. Regularly review and discuss the data with the team to identify improvement opportunities and make data-driven decisions.
6. Continuously Monitor and Update Data
Continuously monitor and update the solder paste printing data to ensure its relevance and usefulness. As process conditions change or new products are introduced, review and adjust the data collection and analysis procedures accordingly. Regularly assess the effectiveness of the data preparation process and make improvements as needed.
Here is a table summarizing the best practices for solder paste data preparation:
Best Practice | Description |
---|---|
Establish Clear Data Collection Procedures | Develop and document procedures for consistent data collection |
Use Automated Data Collection Systems | Use automated systems for accurate and detailed data collection |
Implement Data Quality Checks | Set up validation rules and regularly clean the data |
Standardize Data Formats and Storage | Use a centralized database or data management system |
Collaborate with Cross-Functional Teams | Ensure data relevance and alignment with business objectives |
Continuously Monitor and Update Data | Regularly review and adjust data collection and analysis procedures |
Frequently Asked Questions (FAQ) about Solder Paste Data Preparation
1. What is the importance of solder paste data preparation?
Solder paste data preparation is important because it helps ensure the quality and reliability of the solder paste printing process, which directly impacts the performance of the assembled product. By collecting and analyzing relevant data, manufacturers can identify potential issues, optimize process parameters, and improve overall process control and yield.
2. What are the key types of data to collect for solder paste printing?
The key types of data to collect for solder paste printing include solder paste volume, height, area, offset, and stencil aperture measurements. These parameters provide insights into the amount, distribution, and positional accuracy of the solder paste deposit, which are critical factors affecting the quality of the solder joints.
3. What are the common methods for collecting solder paste printing data?
Common methods for collecting solder paste printing data include 3D and 2D solder paste inspection (SPI) systems, cross-sectioning and microscopy, manual measurement tools, and stencil aperture measurement systems. Each method has its advantages and disadvantages in terms of accuracy, speed, cost, and suitability for different production environments.
4. What are some data analysis techniques used for solder paste data preparation?
Some data analysis techniques used for solder paste data preparation include statistical process control (SPC), capability analysis, design of experiments (DOE), and machine learning and predictive analytics. These techniques help monitor and control the process, assess its capability to meet requirements, optimize process settings, and predict performance and defects.
5. What are some best practices for effective solder paste data preparation?
Some best practices for effective solder paste data preparation include establishing clear data collection procedures, using automated data collection systems, implementing data quality checks, standardizing data formats and storage, collaborating with cross-functional teams, and continuously monitoring and updating the data. Following these practices helps ensure data accuracy, consistency, and usefulness for process improvement and decision-making.
Conclusion
Solder paste data preparation is a critical aspect of the SMT Assembly process that involves collecting, analyzing, and utilizing relevant data to optimize the solder paste printing process and ensure product quality. By understanding the types of data to collect, the data collection methods available, and the data analysis techniques to apply, manufacturers can effectively prepare and use solder paste printing data to drive process improvements and achieve business objectives.
Implementing best practices, such as establishing clear procedures, using automated systems, ensuring data quality, and collaborating with cross-functional teams, is essential for successful solder paste data preparation. By continuously monitoring and updating the data, manufacturers can adapt to changing process conditions and maintain the relevance and usefulness of the data over time.
Effective solder paste data preparation empowers manufacturers to make data-driven decisions, reduce defects, improve yield, and ultimately deliver high-quality products to their customers. As the electronics industry continues to evolve and become more complex, the importance of solder paste data preparation will only continue to grow, making it a critical skill for manufacturers to master in order to stay competitive and succeed in the market.
Leave a Reply