Understanding PCB Pads
Definition and Purpose
PCB pads are the conductive surfaces on a printed circuit board where electronic components are attached. They serve as the connection points between the components and the copper traces that form the electrical pathways on the PCB. Pads are typically made of copper and are plated with a protective finish, such as gold, silver, or tin, to prevent oxidation and improve solderability.
The primary purpose of PCB pads is to provide a reliable and secure connection between the components and the PCB. They also help to distribute heat generated by the components and facilitate the transfer of electrical signals.
Types of PCB Pads
There are several types of PCB pads, each designed for specific components and connection methods. Some of the most common types include:
-
SMD (Surface Mount Device) Pads: These pads are used for surface-mounted components, such as resistors, capacitors, and integrated circuits. SMD pads are typically smaller than through-hole pads and are designed to accommodate the specific package size and pin configuration of the component.
-
Through-Hole Pads: These pads are used for through-hole components, such as connectors, switches, and some types of capacitors and resistors. Through-hole pads have a hole drilled through the center, allowing the component leads to pass through the PCB and be soldered on the opposite side.
-
BGA (Ball Grid Array) Pads: These pads are used for BGA components, which have an array of solder balls on the underside of the package. BGA pads are arranged in a grid pattern and require precise alignment and soldering techniques.
-
Castellated Pads: These pads are used for edge-mounted components or for connecting multiple PCBs together. Castellated pads have a half-hole drilled at the edge of the PCB, allowing for a strong mechanical and electrical connection.
Pad Shapes and Sizes
PCB pads come in various shapes and sizes, depending on the component and the specific requirements of the circuit. Some common pad shapes include:
-
Circular Pads: These are the most common pad shape and are used for through-hole components and some surface-mounted devices.
-
Rectangular Pads: These pads are often used for surface-mounted components, such as chip resistors and capacitors.
-
Oval Pads: These pads are sometimes used for through-hole components to allow for slight misalignment during assembly.
-
Custom Shapes: In some cases, pads may be designed with custom shapes to accommodate unique component packages or to optimize the electrical or thermal performance of the circuit.
Pad sizes are typically determined by the component manufacturer’s specifications and the PCB design standards, such as the IPC (Institute for Printed Circuits) guidelines. It is essential to choose the appropriate pad size to ensure proper soldering and reliable connections.
Designing PCB Pads
Pad Layout and Placement
When designing a PCB, the layout and placement of the pads are critical factors in ensuring the proper functioning and reliability of the circuit. Some key considerations for pad layout and placement include:
-
Component Orientation: Pads should be oriented to match the component’s package and pin configuration. This ensures proper alignment and reduces the risk of assembly errors.
-
Pad Spacing: Pads should be spaced appropriately to prevent short circuits and to allow for adequate soldering. The spacing between pads is typically determined by the PCB design standards and the component manufacturer’s recommendations.
-
Thermal Considerations: For components that generate significant heat, such as power transistors or voltage regulators, the pads should be designed to facilitate heat dissipation. This may involve using larger pads, adding thermal vias, or incorporating heat sinks.
-
Signal Integrity: For high-speed or sensitive circuits, the placement and routing of pads can impact signal integrity. It is essential to consider factors such as trace length, impedance matching, and crosstalk when designing the pad layout.
Pad-to-Trace Ratios
The ratio between the pad size and the width of the connected trace is an important consideration in PCB design. This ratio, known as the pad-to-trace ratio, affects the electrical and mechanical properties of the connection.
A general guideline is to maintain a pad-to-trace ratio of at least 2:1, meaning the pad diameter should be at least twice the width of the connected trace. This ensures a strong mechanical connection and reduces the risk of trace breakage or pad lift-off during soldering or handling.
However, in some cases, such as high-current or high-frequency circuits, a larger pad-to-trace ratio may be necessary to accommodate the increased current flow or to maintain signal integrity.
Solder Mask and Pad Clearance
Solder mask is a protective coating applied to the PCB surface, covering the copper traces while leaving the pads exposed for soldering. The solder mask helps to prevent short circuits, protects the traces from oxidation, and improves the aesthetics of the PCB.
When designing pads, it is essential to consider the solder mask clearance, which is the distance between the edge of the pad and the opening in the solder mask. The solder mask clearance should be sufficient to allow for proper solder wetting and to prevent solder bridges between adjacent pads.
The typical solder mask clearance is between 0.05mm and 0.1mm, depending on the PCB manufacturer’s capabilities and the specific requirements of the design.
PCB Pad Finishes
Types of Pad Finishes
To protect the copper pads from oxidation and to enhance solderability, various surface finishes are applied to the pads. Some common pad finishes include:
-
HASL (Hot Air Solder Leveling): This is the most common and economical pad finish. The PCB is dipped in molten solder, and hot air is used to remove excess solder, creating a flat, solderable surface.
-
ENIG (Electroless Nickel Immersion Gold): This finish consists of a layer of nickel followed by a thin layer of gold. ENIG provides excellent solderability, durability, and shelf life, making it suitable for high-reliability applications.
-
OSP (Organic Solderability Preservative): This is a thin, organic coating applied to the pads to prevent oxidation. OSP is a cost-effective alternative to HASL and ENIG, but it has a limited shelf life and may require special handling during assembly.
-
Immersion Silver: This finish is similar to ENIG but uses a layer of silver instead of gold. Immersion silver offers good solderability and is less expensive than ENIG, but it may tarnish over time and has a shorter shelf life.
Choosing the Right Pad Finish
The choice of pad finish depends on several factors, including:
-
Application Requirements: High-reliability applications, such as aerospace or medical devices, may require more durable finishes like ENIG, while cost-sensitive consumer products may use HASL or OSP.
-
Component Compatibility: Some components, such as fine-pitch or BGA devices, may require specific pad finishes for optimal solderability and reliability.
-
Manufacturing Process: The choice of pad finish should be compatible with the PCB fabrication and assembly processes, including soldering methods and cleaning agents.
-
Cost and Availability: The cost and availability of different pad finishes may vary depending on the PCB manufacturer and the region.
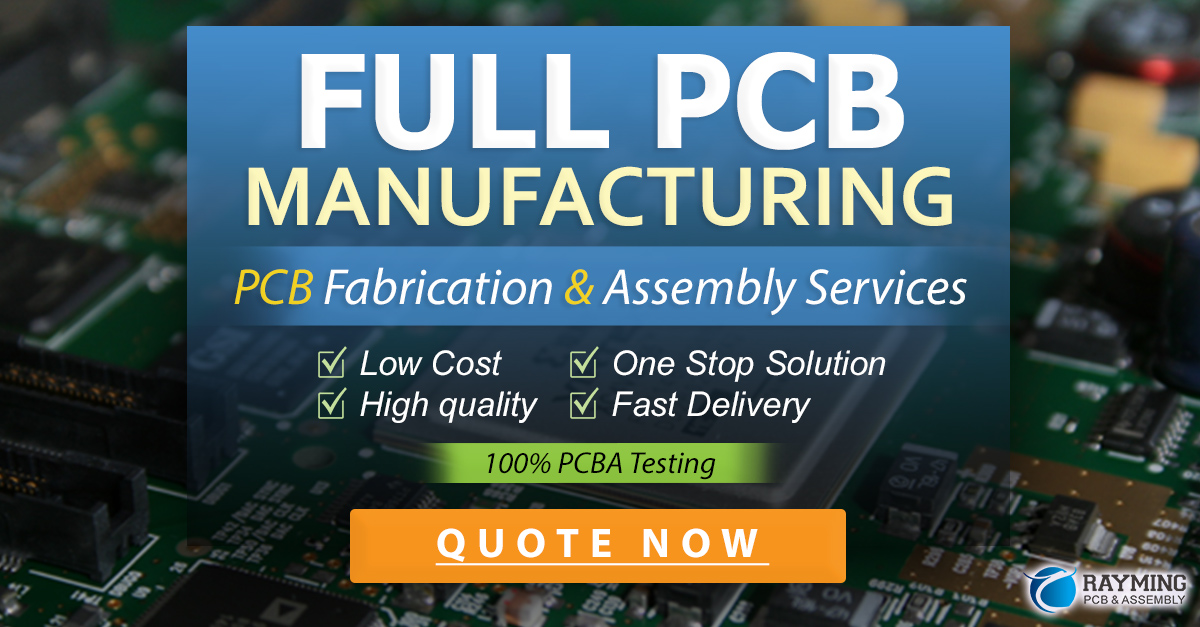
Assembly and Soldering Considerations
Soldering Techniques
The success of PCB Assembly largely depends on the proper soldering of components to the pads. There are two primary soldering techniques used in PCB assembly:
-
Wave Soldering: This method is used for through-hole components. The PCB is passed over a molten solder wave, which wets the component leads and the pads, creating a strong mechanical and electrical connection.
-
Reflow Soldering: This method is used for surface-mounted components. Solder paste, a mixture of tiny solder particles and flux, is applied to the pads using a stencil. The components are then placed on the pads, and the PCB is heated in a reflow oven, melting the solder and forming a connection between the components and the pads.
Solder Joint Inspection
After soldering, it is essential to inspect the solder joints to ensure proper connections and to identify any defects. Some common solder joint defects include:
-
Bridging: This occurs when excess solder creates an unintended connection between adjacent pads or traces.
-
Cold Joints: These are weak, unreliable connections caused by insufficient heat, improper solder flow, or contamination.
-
Tombstoning: This happens when a surface-mounted component stands up on one end due to uneven heating or pad design issues.
Solder joint inspection can be performed visually using magnification or through automated optical inspection (AOI) systems, which use cameras and image processing algorithms to detect defects.
Rework and Repair
In some cases, solder joints may need to be reworked or repaired due to defects or component failures. Rework involves removing the defective component, cleaning the pads, and resoldering a new component in its place. This process requires skilled technicians and specialized tools, such as soldering irons, desoldering pumps, and hot air rework stations.
When reworking or repairing PCBs, it is essential to follow best practices to avoid damaging the pads or neighboring components. This includes using the appropriate temperature settings, applying flux to promote solder flow, and taking care not to apply excessive force when removing or replacing components.
FAQ
-
What is the difference between SMD and through-hole pads?
SMD (surface-mount device) pads are designed for components that are soldered directly onto the surface of the PCB, while through-hole pads have holes drilled through the board for component leads to pass through and be soldered on the opposite side. -
Why are there different pad shapes and sizes?
Different pad shapes and sizes are used to accommodate various component packages and pin configurations. They also help to optimize the electrical and mechanical properties of the connection, such as current-carrying capacity and mechanical strength. -
What is the purpose of solder mask on PCB pads?
Solder mask is a protective coating that covers the copper traces on a PCB while leaving the pads exposed for soldering. It helps to prevent short circuits, protects the traces from oxidation, and improves the aesthetics of the PCB. -
How do I choose the right pad finish for my PCB?
The choice of pad finish depends on several factors, including the application requirements, component compatibility, manufacturing process, and cost. Common pad finishes include HASL, ENIG, OSP, and immersion silver, each with its own advantages and limitations. -
What should I do if I encounter solder joint defects during assembly?
If solder joint defects are found during assembly, they should be reworked or repaired to ensure proper connections and reliable operation. This involves removing the defective component, cleaning the pads, and resoldering a new component using appropriate techniques and tools. It is essential to follow best practices to avoid damaging the pads or neighboring components during the rework process.
Pad Type | Description |
---|---|
SMD Pads | Used for surface-mounted components; smaller than through-hole pads |
Through-Hole Pads | Have a hole drilled through the center for component leads to pass through |
BGA Pads | Arranged in a grid pattern for ball grid array components |
Castellated Pads | Half-hole drilled at the edge of the PCB for edge-mounted components |
Pad Shape | Description |
---|---|
Circular | Most common; used for through-hole and some surface-mounted components |
Rectangular | Often used for surface-mounted components like chip resistors and capacitors |
Oval | Sometimes used for through-hole components to allow for slight misalignment |
Custom Shapes | Designed for unique component packages or to optimize electrical/thermal performance |
Pad Finish | Description |
---|---|
HASL | Hot Air Solder Leveling; most common and economical finish |
ENIG | Electroless Nickel Immersion Gold; excellent solderability, durability, and shelf life |
OSP | Organic Solderability Preservative; cost-effective but limited shelf life |
Immersion Silver | Similar to ENIG but uses silver instead of gold; less expensive but may tarnish over time |
In conclusion, PCB pads are a critical component of electronic circuit design and manufacturing. They serve as the connection points between components and the copper traces on the PCB, ensuring reliable electrical and mechanical connections. Designing PCB pads involves considering factors such as component compatibility, pad shape and size, solder mask clearance, and pad finish. Proper soldering techniques, inspection, and rework processes are essential for ensuring the quality and reliability of the assembled PCB. By understanding the various aspects of PCB pads and following best practices in design and assembly, engineers and technicians can create robust and high-performing electronic devices.
Leave a Reply