Introduction to Solder Paste Printing
Solder paste printing is a crucial step in the surface mount technology (SMT) assembly process. It involves depositing solder paste onto printed circuit boards (PCBs) using a stencil and a squeegee. The quality of the solder paste printing process directly affects the reliability and functionality of the final electronic product. In this article, we will discuss some valuable tips for achieving optimal solder paste printing results.
The Importance of Solder Paste Printing
Solder paste printing is essential for several reasons:
- It ensures proper electrical connections between components and the PCB.
- It provides mechanical support for components during the reflow soldering process.
- It helps to prevent component shifting and tombstoning.
- It contributes to the overall quality and reliability of the assembled PCB.
Factors Affecting Solder Paste Printing Quality
Several factors can impact the quality of solder paste printing, including:
Stencil Design
The stencil design is a critical factor in achieving consistent and accurate solder paste deposits. The stencil aperture size, shape, and thickness should be optimized based on the component package type, pad size, and pitch. The stencil material, such as stainless steel or nickel, should be selected based on the desired durability and print definition.
Solder Paste Properties
The solder paste properties, such as viscosity, particle size distribution, and flux activity, can significantly influence the printing process. The solder paste should have the appropriate rheological properties to ensure good printability, slump resistance, and tack time. The paste should also be compatible with the selected stencil and PCB surface finish.
Printer Settings
The solder paste printer settings, such as squeegee pressure, speed, and angle, should be optimized to achieve consistent paste deposits. The print gap between the stencil and PCB should be set correctly to prevent smearing or insufficient paste transfer. The printer alignment and calibration should be regularly checked and adjusted to maintain high printing accuracy.
Environmental Conditions
Environmental conditions, such as temperature and humidity, can affect the solder paste printing process. The ideal temperature range for solder paste printing is typically between 20-25°C (68-77°F), and the relative humidity should be controlled between 30-60%. Excessive temperature or humidity can cause paste slumping, drying, or poor release from the stencil.
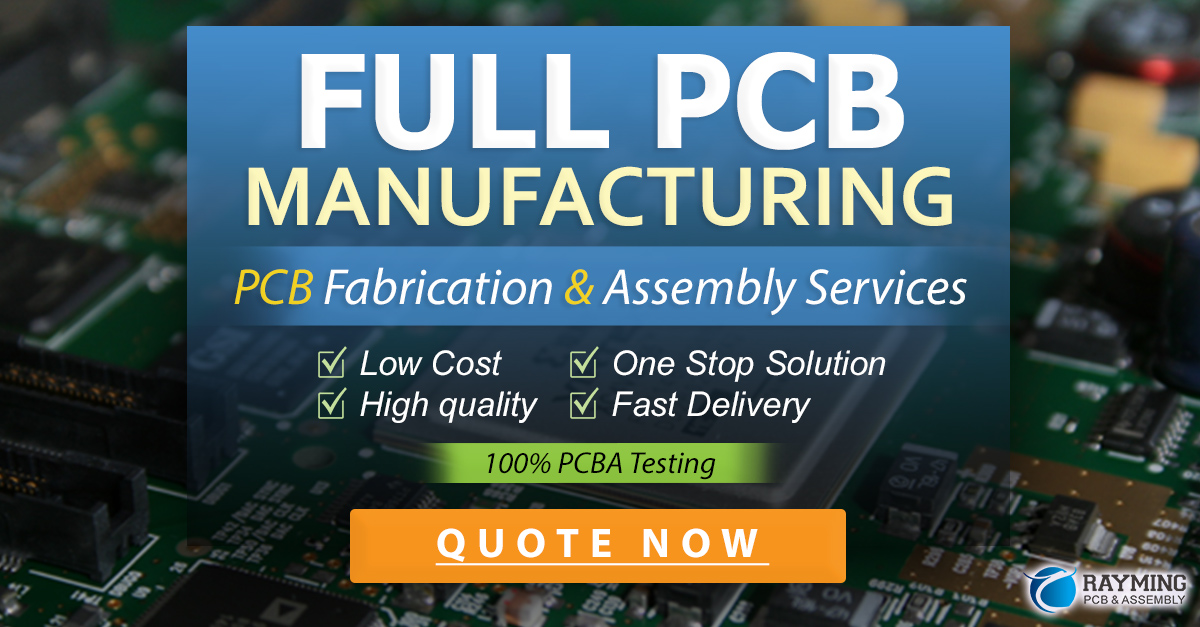
Best Practices for Solder Paste Printing
To achieve optimal solder paste printing results, consider the following best practices:
Stencil Maintenance
Regular stencil cleaning and maintenance are essential for consistent printing quality. The stencil should be cleaned using appropriate solvents and methods to remove solder paste residue and prevent aperture clogging. The stencil should also be inspected for damage, such as bent or broken apertures, and replaced when necessary.
Paste Storage and Handling
Solder paste should be stored and handled according to the manufacturer’s recommendations. The paste should be refrigerated when not in use and allowed to reach room temperature before printing. The paste container should be gently stirred or mixed to ensure homogeneity before use. Expired or contaminated paste should be discarded to prevent printing defects.
Print Parameter Optimization
The solder paste printing parameters should be optimized through a systematic approach, such as design of experiments (DOE) or statistical process control (SPC). The optimal settings should be determined based on the specific stencil, paste, and PCB characteristics. The print parameters should be regularly monitored and adjusted to maintain process stability and repeatability.
Inspection and Feedback
Solder paste printing quality should be regularly inspected using automated or manual methods, such as 2D or 3D solder paste inspection (SPI) systems. The inspection data should be analyzed to identify process trends, variations, and defects. The feedback from the inspection should be used to make necessary adjustments to the printing process and improve overall quality.
Common Solder Paste Printing Defects and Solutions
Despite following best practices, solder paste printing defects can still occur. Some common defects and their solutions include:
Defect | Description | Causes | Solutions |
---|---|---|---|
Insufficient paste | Inadequate paste volume on pads | – Stencil aperture clogging – Low squeegee pressure – Paste drying or poor release |
– Clean or replace stencil – Increase squeegee pressure – Check paste viscosity and storage conditions |
Excessive paste | Excess paste volume on pads | – Stencil aperture oversize – High squeegee pressure – Slow print speed |
– Reduce stencil aperture size – Decrease squeegee pressure – Increase print speed |
Bridging | Paste connecting adjacent pads | – Stencil aperture proximity – Paste slumping or poor release – Excessive paste volume |
– Increase stencil aperture spacing – Check paste rheology and storage conditions – Reduce stencil aperture size or thickness |
Scooping | Concave paste surface on pads | – Stencil aperture shape – Paste rheology or particle size – Squeegee blade wear |
– Optimize stencil aperture shape – Check paste properties and compatibility – Replace squeegee blade |
Frequently Asked Questions (FAQ)
-
What is the optimal stencil thickness for solder paste printing?
The optimal stencil thickness depends on the component package type, pad size, and pitch. Generally, a stencil thickness of 0.1-0.15 mm (4-6 mils) is suitable for most SMT applications. However, finer pitch components may require thinner stencils, while larger components may benefit from thicker stencils. -
How often should I clean my stencil during solder paste printing?
The frequency of stencil cleaning depends on the solder paste type, printing volume, and environmental conditions. As a general rule, the stencil should be cleaned every 4-8 hours of continuous printing or after every shift. However, if the solder paste is prone to drying or clogging, more frequent cleaning may be necessary. -
Can I reuse solder paste that has been out of the refrigerator for a while?
It is not recommended to reuse solder paste that has been left out at room temperature for an extended period. Solder paste has a limited shelf life and can degrade over time, leading to poor printing and soldering quality. Always follow the manufacturer’s storage and handling guidelines to ensure optimal paste performance. -
What is the ideal print speed for solder paste printing?
The ideal print speed depends on the solder paste properties, stencil design, and PCB characteristics. Generally, a print speed of 20-50 mm/s is suitable for most SMT applications. However, the optimal print speed should be determined through experimentation and process optimization. Too slow of a print speed may cause paste drying and poor release, while too fast of a speed may result in incomplete paste transfer. -
How can I prevent solder paste from slumping or spreading after printing?
To prevent solder paste slumping or spreading, ensure that the paste has the appropriate rheological properties, such as good tackiness and yield stress. The stencil aperture design should also be optimized to prevent paste bridging or excessive deposit volume. Additionally, maintain proper environmental conditions, such as temperature and humidity, to prevent paste drying or slumping.
Conclusion
Solder paste printing is a critical process in SMT assembly that requires careful control and optimization. By understanding the factors affecting printing quality and following best practices, manufacturers can achieve consistent and reliable solder paste deposits. Regular inspection, maintenance, and process optimization are essential for identifying and preventing printing defects. With the right tools, techniques, and expertise, solder paste printing can contribute to the overall success and quality of the final electronic product.
Leave a Reply