What is an Automotive PCB?
An Automotive PCB is a specialized type of printed circuit board designed to withstand the harsh environmental conditions found in vehicles. These PCBs are responsible for interconnecting various electronic components, such as sensors, microcontrollers, and power management devices, allowing them to communicate and function seamlessly within the vehicle’s electrical system.
Key Characteristics of Automotive PCBs
Automotive PCBs are engineered to meet stringent requirements, ensuring reliable performance in the face of extreme temperatures, vibrations, and exposure to moisture and chemicals. Some of the key characteristics of Automotive PCBs include:
- High-temperature resistance
- Vibration and shock resistance
- Moisture and chemical resistance
- Electromagnetic compatibility (EMC)
- Miniaturization and space optimization
The Role of Automotive PCBs in Modern Vehicles
Automotive PCBs play a critical role in enabling the advanced features and functionalities found in modern vehicles. From basic engine control to complex driver assistance systems, PCBs form the backbone of the vehicle’s electronic architecture.
Engine Management Systems
The engine management system (EMS) is responsible for controlling and optimizing the performance of the vehicle’s engine. Automotive PCBs within the EMS facilitate the communication between various sensors, such as the throttle position sensor, mass airflow sensor, and oxygen sensor, and the engine control unit (ECU). By processing the data from these sensors, the ECU can adjust fuel injection, ignition timing, and other parameters to ensure optimal engine performance and fuel efficiency.
Safety and Driver Assistance Systems
Modern vehicles are equipped with a wide array of safety and driver assistance features, such as anti-lock braking systems (ABS), electronic stability control (ESC), and adaptive cruise control (ACC). These systems rely on Automotive PCBs to process data from various sensors, including wheel speed sensors, accelerometers, and radar or camera modules. The PCBs enable rapid communication between these sensors and the respective control modules, allowing the vehicle to make real-time decisions and provide enhanced safety and convenience for the driver and passengers.
Infotainment and Connectivity
Automotive PCBs also play a crucial role in the infotainment and connectivity features of modern vehicles. From touchscreen displays and audio systems to Bluetooth and Wi-Fi connectivity, PCBs enable the seamless integration of these technologies into the vehicle’s electrical architecture. As consumers demand more advanced features, such as smartphone integration, mobile office solutions, and in-vehicle apps, the complexity and importance of Automotive PCBs will continue to grow.
Manufacturing Processes for Automotive PCBs
The manufacturing of Automotive PCBs involves a series of precise and tightly controlled processes to ensure the highest level of quality and reliability. These processes can be broadly categorized into three main stages: design, fabrication, and assembly.
Design
The design stage involves creating a detailed layout of the PCB, taking into account the specific requirements of the automotive application. This includes selecting the appropriate materials, determining the layer stack-up, and defining the trace widths and spacing to ensure optimal signal integrity and EMC performance. Advanced design tools, such as computer-aided design (CAD) software, are used to create a virtual representation of the PCB, which is then rigorously tested and optimized through simulations and analyses.
Fabrication
Once the design is finalized, the fabrication process begins. This involves a series of steps to create the physical PCB, including:
- Substrate preparation: The base material, typically a high-temperature FR-4 or polyimide, is cut to size and cleaned.
- Copper lamination: Thin layers of copper foil are bonded to the substrate using heat and pressure.
- Patterning: The desired circuit pattern is transferred onto the copper layers using photolithography and Etching Processes.
- Drilling: Holes are drilled through the PCB to accommodate through-hole components and facilitate inter-layer connections.
- Plating: The holes are plated with copper to create electrical connections between layers.
- Solder mask application: A protective layer of solder mask is applied to the PCB, exposing only the areas intended for component soldering.
- Surface finish: A final surface finish, such as ENIG (Electroless Nickel Immersion Gold) or HASL (Hot Air Solder Leveling), is applied to protect the exposed copper and enhance solderability.
Throughout the fabrication process, strict quality control measures are implemented to ensure that the PCBs meet the required specifications and are free from defects.
Assembly
The final stage in the manufacturing process is the assembly of electronic components onto the PCB. This involves the following steps:
- Solder Paste Printing: A precise amount of solder paste is deposited onto the PCB’s pads using a stencil or screen printing process.
- Component placement: Surface mount devices (SMDs) and through-hole components are placed onto the PCB using automated pick-and-place machines or manual assembly techniques.
- Soldering: The PCB is passed through a reflow oven, where the solder paste melts and forms electrical and mechanical connections between the components and the PCB.
- Inspection and testing: The assembLED PCB undergoes a series of inspections and tests, including automated optical inspection (AOI), X-ray inspection, and functional testing, to ensure proper assembly and functionality.
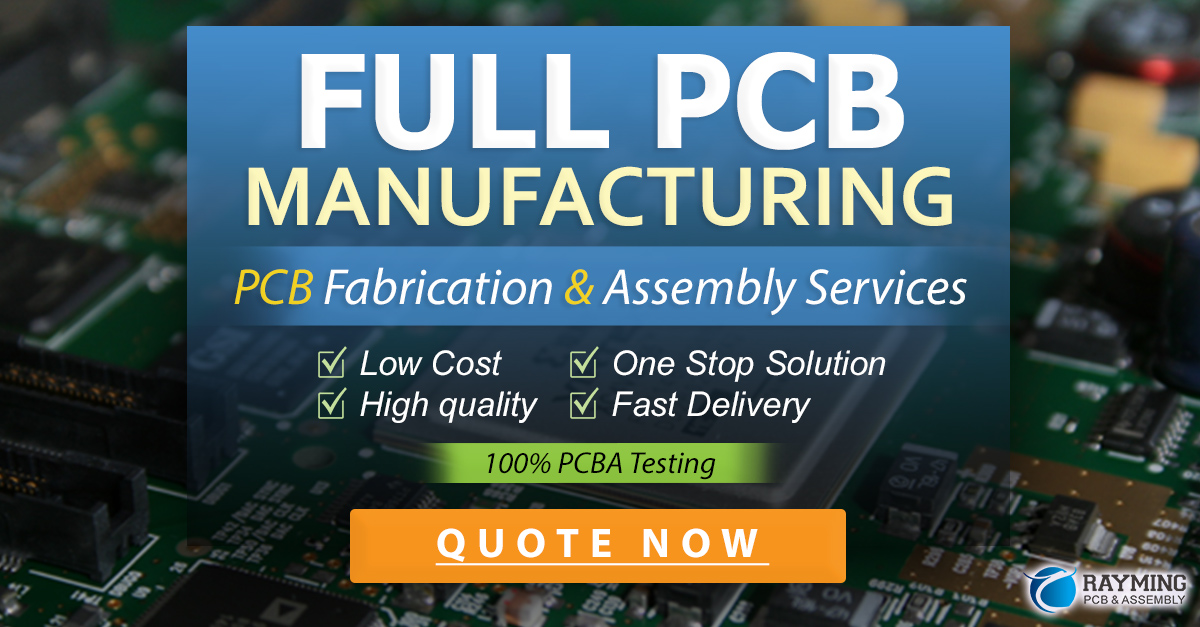
Challenges in Automotive PCB Design and Manufacturing
The design and manufacturing of Automotive PCBs present unique challenges due to the demanding environmental conditions and stringent quality requirements of the automotive industry. Some of the key challenges include:
Thermal Management
Automotive PCBs must be able to withstand extreme temperature variations, ranging from -40°C to +125°C or higher. Designing PCBs that can effectively dissipate heat and maintain reliable performance under these conditions requires careful material selection, layout optimization, and the use of advanced thermal management techniques, such as the incorporation of thermal vias and heat sinks.
Vibration and Shock Resistance
Vehicles are subjected to constant vibrations and occasional shocks during operation, which can lead to mechanical stress on the PCBs and their components. To mitigate these risks, Automotive PCBs must be designed with robust mechanical support structures, such as stiffeners and reinforcements, and use components that are rated for high vibration and shock resistance.
Electromagnetic Compatibility (EMC)
The increasing number of electronic systems in modern vehicles poses significant challenges in terms of electromagnetic compatibility. Automotive PCBs must be designed to minimize electromagnetic interference (EMI) and ensure that the vehicle’s electronic systems can operate without disrupting each other or being affected by external electromagnetic sources. This requires careful layout design, the use of shielding techniques, and adherence to strict EMC testing and validation procedures.
Miniaturization and Space Constraints
As vehicles become more compact and feature-rich, the available space for electronic systems becomes increasingly limited. Automotive PCBs must be designed to maximize functionality while minimizing their physical footprint. This often involves the use of high-density interconnect (HDI) PCBs, which feature smaller trace widths, tighter spacing, and more layers to accommodate complex circuitry in a compact form factor.
Reliability and Longevity
Automotive PCBs are expected to operate reliably over the entire lifespan of the vehicle, which can often exceed 10-15 years. Ensuring the long-term reliability of these PCBs requires the use of high-quality materials, robust manufacturing processes, and extensive testing and validation procedures. Accelerated life testing, thermal cycling, and environmental stress screening are just a few of the methods used to assess the reliability and durability of Automotive PCBs.
Future Trends in Automotive PCB Technology
As the automotive industry continues to evolve, driven by trends such as electrification, autonomous driving, and connected vehicles, the role of Automotive PCBs will become even more critical. Some of the key trends shaping the future of Automotive PCB technology include:
Advanced Materials
The demand for higher performance and reliability in Automotive PCBs will drive the adoption of advanced materials, such as ceramic substrates, low-loss dielectrics, and high-conductivity copper alloys. These materials will enable PCBs to operate at higher frequencies, withstand more extreme environmental conditions, and support the integration of advanced electronic systems.
Flexible and Stretchable PCBs
The increasing use of non-planar and conformal surfaces in vehicle interiors will drive the development of flexible and stretchable PCBs. These PCBs will be able to conform to complex shapes and bend or stretch without compromising their electrical performance, enabling the integration of electronics into previously inaccessible areas of the vehicle.
3D PCB Packaging
As the demand for miniaturization and high-density packaging continues to grow, 3D PCB packaging technologies will become increasingly important. These technologies, such as stacked dies, package-on-package (PoP), and embedded components, will enable the integration of multiple PCBs and components into a single, compact module, saving space and improving overall system performance.
Wireless Connectivity
The proliferation of connected vehicles and the increasing demand for in-vehicle wireless connectivity will drive the integration of wireless technologies, such as Wi-Fi, Bluetooth, and 5G, into Automotive PCBs. This will require the development of advanced antenna designs and the integration of radio frequency (RF) components onto the PCBs, posing new challenges in terms of signal integrity and EMC.
FAQ
Q1: What is the difference between an Automotive PCB and a standard PCB?
A1: Automotive PCBs are designed to withstand the harsh environmental conditions found in vehicles, such as extreme temperatures, vibrations, and exposure to moisture and chemicals. They are subject to more stringent quality and reliability requirements compared to standard PCBs used in consumer electronics or industrial applications.
Q2: What are the key materials used in Automotive PCB manufacturing?
A2: The most common base materials used in Automotive PCB manufacturing are high-temperature FR-4 and polyimide. Copper foils are used for the conductive layers, while solder masks and surface finishes, such as ENIG or HASL, are applied for protection and enhanced solderability.
Q3: How are Automotive PCBs tested for reliability?
A3: Automotive PCBs undergo rigorous testing and validation procedures to ensure their reliability and durability. These tests include accelerated life testing, thermal cycling, vibration and shock testing, and environmental stress screening. The PCBs must meet strict quality and performance standards before being approved for use in vehicles.
Q4: What are the main challenges in designing Automotive PCBs?
A4: The main challenges in designing Automotive PCBs include thermal management, vibration and shock resistance, electromagnetic compatibility (EMC), miniaturization and space constraints, and ensuring long-term reliability. Designers must carefully consider these factors and employ advanced techniques to overcome these challenges.
Q5: What are some of the future trends in Automotive PCB technology?
A5: Future trends in Automotive PCB technology include the adoption of advanced materials, the development of flexible and stretchable PCBs, the use of 3D PCB packaging technologies, and the integration of wireless connectivity solutions. These trends are driven by the increasing demands for higher performance, miniaturization, and the proliferation of connected and autonomous vehicles.
Feature | Standard PCB | Automotive PCB |
---|---|---|
Operating Temperature | -20°C to 85°C | -40°C to 125°C |
Vibration Resistance | Low | High |
Shock Resistance | Low | High |
Moisture Resistance | Moderate | High |
Chemical Resistance | Low | High |
EMC Requirements | Moderate | Stringent |
Quality Standards | General | Automotive-specific |
Reliability Expectations | 3-5 years | 10-15 years |
In conclusion, Automotive PCBs play a vital role in enabling the advanced features and functionalities of modern vehicles. From engine management systems to safety and driver assistance features, these specialized PCBs are designed to withstand the harsh environmental conditions and meet the stringent quality and reliability requirements of the automotive industry. As vehicles continue to evolve, driven by trends such as electrification and autonomous driving, the importance of Automotive PCBs will only continue to grow. By staying at the forefront of PCB design and manufacturing technologies, the automotive industry will be well-positioned to meet the challenges and opportunities of the future, delivering safer, more efficient, and more connected vehicles to consumers worldwide.
Leave a Reply