What is Soldermask?
Soldermask, also known as solder resist or solder mask, is a thin layer of polymer applied to the surface of a PCB. Its primary purpose is to protect the copper traces and pads from oxidation, prevent solder bridges during the soldering process, and provide electrical insulation. Soldermask is available in various colors, with green being the most common in traditional PCB manufacturing. However, when it comes to LED PCB applications, white soldermask has gained significant popularity.
Advantages of White Soldermask in LED PCB Applications
1. Enhanced Light Reflection
One of the main reasons for using white soldermask in LED PCB applications is its superior light reflection properties. LEDs are designed to emit light, and the soldermask color can greatly influence how effectively that light is reflected and distributed. White soldermask has a high reflectivity, meaning it can reflect a significant portion of the light emitted by the LEDs back towards the intended direction. This enhanced light reflection results in improved brightness and more efficient use of the available light output.
2. Improved Contrast and Visibility
Another advantage of white soldermask in LED PCB applications is the improved contrast and visibility it provides. When LEDs are mounted on a white background, the contrast between the LED and the surrounding area is heightened, making the LEDs more visually prominent. This increased contrast enhances the overall aesthetics of the LED PCB and makes it easier for users to perceive the light emitted by the LEDs. In applications where visual clarity is crucial, such as in automotive lighting or signage, white soldermask offers a distinct advantage.
3. Better Heat Dissipation
Heat management is a critical aspect of LED PCB design. LEDs generate heat during operation, and if this heat is not effectively dissipated, it can lead to reduced performance, shortened lifespan, and even premature failure of the LEDs. White soldermask can contribute to better heat dissipation in LED PCBs. The white color has a higher albedo, meaning it reflects more of the incident light and heat compared to darker colors. By reflecting heat away from the PCB surface, white soldermask helps in maintaining a cooler operating temperature for the LEDs, thereby improving their performance and longevity.
4. Aesthetic Appeal
In addition to its functional benefits, white soldermask also offers an aesthetic appeal in LED PCB applications. The clean and bright appearance of white soldermask can enhance the overall look of the PCB, making it visually appealing and professional. This is particularly important in applications where the LED PCB is visible to end-users, such as in consumer electronics or architectural lighting. The white soldermask provides a neutral background that complements the colors of the LEDs and creates a cohesive visual experience.
Considerations for Using White Soldermask
While white soldermask offers numerous benefits in LED PCB applications, there are a few considerations to keep in mind when designing and manufacturing PCBs with this material.
1. Cleanliness and Handling
White soldermask is more susceptible to showing dirt, dust, and fingerprints compared to darker colors. During the manufacturing process and subsequent handling, extra care must be taken to maintain cleanliness and avoid contamination. Proper handling procedures, such as wearing gloves and working in a clean environment, are essential to ensure the pristine appearance of the white soldermask.
2. Silk Screen Legibility
When using white soldermask, the choice of silk screen color becomes an important consideration. Traditional white silk screen may not provide sufficient contrast against the white background, making it difficult to read any text or markings on the PCB. To ensure legibility, it is recommended to use a dark color, such as black or dark blue, for the silk screen when working with white soldermask. This contrast enhancement improves the readability of any text or symbols printed on the PCB surface.
3. Cost Implications
While white soldermask is widely available and used in the PCB industry, it may come with a slightly higher cost compared to the more common green soldermask. The price difference can vary depending on the PCB manufacturer and the specific manufacturing processes involved. However, the added cost is often justified by the benefits white soldermask brings to LED PCB applications, such as improved light reflection, contrast, and aesthetic appeal.
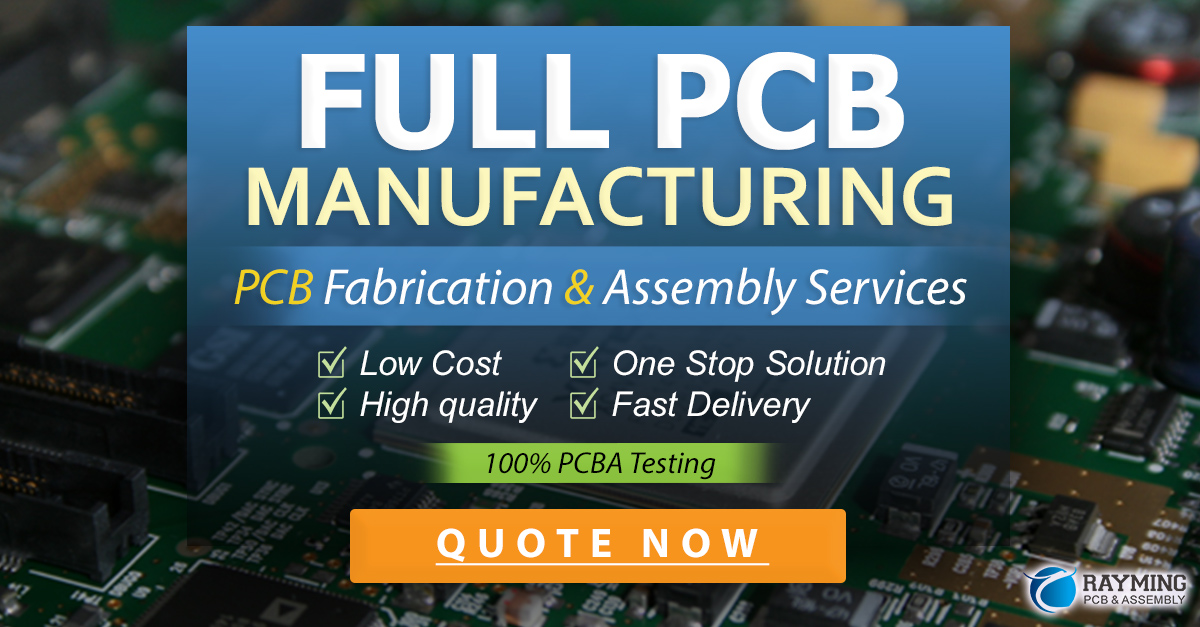
Frequently Asked Questions (FAQ)
Q1: Is white soldermask suitable for all types of LED PCBs?
A1: White soldermask is suitable for most LED PCB applications where light reflection, contrast, and aesthetics are important factors. However, the suitability may depend on the specific requirements of the application, such as the desired color temperature of the LEDs or any specific environmental conditions the PCB will be exposed to.
Q2: Can white soldermask be used in combination with other colors?
A2: Yes, white soldermask can be used in combination with other soldermask colors on the same PCB. This is often done to create specific designs or to highlight certain areas of the PCB. However, careful consideration should be given to the overall aesthetics and functionality of the PCB when using multiple soldermask colors.
Q3: Does white soldermask affect the electrical properties of the PCB?
A3: No, the choice of soldermask color does not directly affect the electrical properties of the PCB. The soldermask acts as an insulating layer and provides protection against solder bridging and oxidation, regardless of its color. The electrical performance of the PCB is determined by factors such as the PCB material, copper thickness, and trace design.
Q4: Are there any special requirements for the solder paste when using white soldermask?
A4: No, there are no special requirements for the solder paste when using white soldermask. The choice of solder paste is based on factors such as the type of components being soldered, the reflow profile, and the desired solder joint characteristics. The soldermask color does not directly influence the selection of solder paste.
Q5: Can white soldermask be used in outdoor LED PCB applications?
A5: Yes, white soldermask can be used in outdoor LED PCB applications, provided that the PCB is properly designed and protected against environmental factors such as moisture, UV radiation, and temperature fluctuations. The use of conformal coatings or encapsulation materials can provide additional protection to the PCB and ensure reliable operation in outdoor conditions.
Conclusion
White soldermask has become a popular choice in LED PCB applications due to its numerous benefits. Its superior light reflection properties, improved contrast and visibility, better heat dissipation, and aesthetic appeal make it an ideal choice for enhancing the performance and appearance of LED PCBs. When designing and manufacturing PCBs with white soldermask, considerations such as cleanliness, silk screen legibility, and potential cost implications should be taken into account.
As the demand for high-quality LED lighting solutions continues to grow, the use of white soldermask in LED PCB applications is expected to remain prevalent. By understanding the advantages and considerations associated with white soldermask, PCB designers and manufacturers can make informed decisions and create LED PCBs that meet the specific requirements of their applications while delivering optimal performance and visual appeal.
Soldermask Color | Light Reflection | Contrast | Heat Dissipation | Aesthetics |
---|---|---|---|---|
White | High | High | Good | Clean and bright |
Green | Moderate | Moderate | Moderate | Traditional |
Black | Low | Low | Poor | Sleek and modern |
Red | Low | High | Poor | Bold and vibrant |
Table 1: Comparison of different soldermask colors and their properties in LED PCB applications.
In conclusion, white soldermask offers a range of benefits in LED PCB applications, making it a preferred choice for many designers and manufacturers. By leveraging the advantages of white soldermask, LED PCBs can achieve enhanced light reflection, improved contrast and visibility, better heat dissipation, and an attractive aesthetic appearance. As the LED lighting industry continues to evolve, the use of white soldermask in PCB design is likely to remain a key factor in creating high-performance and visually appealing LED solutions.
Leave a Reply