Introduction to PCB and Its Importance
Printed circuit boards (PCBs) are essential components in modern electronics. They provide a platform for electrical components to be mounted and connected, forming a complete circuit. PCBs are used in a wide range of applications, from consumer electronics to industrial equipment and aerospace systems.
Ensuring the quality and reliability of PCBs is crucial for the proper functioning and longevity of electronic devices. In this comprehensive guide, we will discuss various aspects of PCB design, manufacturing, and testing to help you ensure the quality of your PCBs.
Understanding PCB Design Fundamentals
PCB Layers and Their Functions
PCBs are made up of multiple layers, each serving a specific purpose. The most common PCB layers include:
- Copper layers: These are the conductive layers that carry electrical signals and power.
- Substrate: The insulating material, typically fiberglass, that separates the copper layers.
- Solder mask: A protective layer that covers the copper traces, preventing short circuits and oxidation.
- Silkscreen: A layer that contains text and symbols for component identification and assembly instructions.
Choosing the Right PCB Material
Selecting the appropriate PCB material is essential for ensuring the performance and reliability of your board. Factors to consider when choosing PCB materials include:
- Dielectric constant
- Thermal conductivity
- Coefficient of thermal expansion (CTE)
- Moisture resistance
- Cost
Some common PCB materials include:
Material | Dielectric Constant | Thermal Conductivity (W/mK) | CTE (ppm/°C) |
---|---|---|---|
FR-4 | 4.5 – 4.7 | 0.3 – 0.4 | 12 – 18 |
Rogers 4003 | 3.38 | 0.71 | 11 |
Polyimide | 3.5 – 4.0 | 0.2 – 0.3 | 12 – 20 |
PCB Design Rules and Best Practices
To ensure the manufacturability and reliability of your PCBs, it is essential to follow design rules and best practices. Some key considerations include:
- Trace width and spacing
- Via size and placement
- Copper pour and ground planes
- Component placement and orientation
- Electromagnetic interference (EMI) and signal integrity
PCB Manufacturing Process
PCB Fabrication Steps
The PCB manufacturing process involves several steps, each critical to ensuring the quality of the final product. The main steps in PCB fabrication include:
- Copper deposition and patterning
- Lamination of layers
- Drilling and plating through-holes
- Solder mask and silkscreen application
- Surface finish application
Quality Control in PCB Manufacturing
Quality control is essential throughout the PCB manufacturing process to ensure that the boards meet the required specifications and performance criteria. Some key quality control measures include:
- Automated optical inspection (AOI)
- X-ray inspection
- Electrical testing
- Microsectioning and cross-sectioning
- Ionic contamination testing
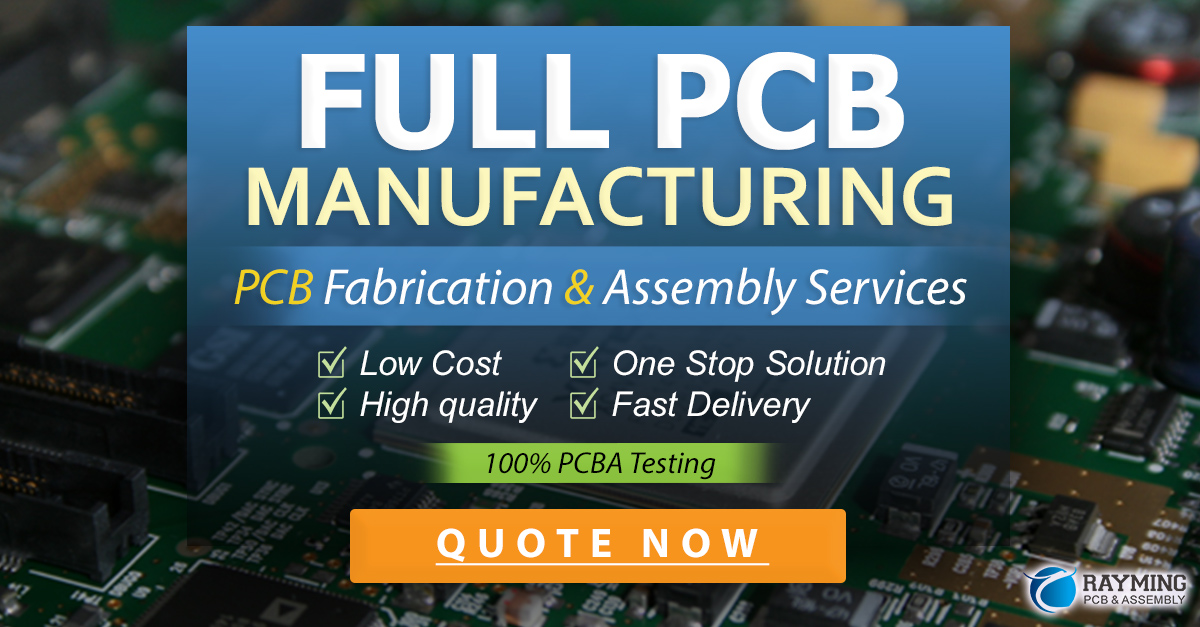
PCB Testing and Inspection
In-Circuit Testing (ICT)
In-circuit testing is a method of testing individual components on a PCB to ensure their functionality and correct placement. ICT involves using a bed-of-nails fixture to make contact with test points on the PCB, allowing for the measurement of component values and the detection of short circuits or open connections.
Flying Probe Testing
Flying probe testing is an alternative to ICT that uses movable probes to make contact with test points on the PCB. This method is more flexible than ICT and is suitable for low-volume production or prototype testing.
Functional Testing
Functional testing involves testing the PCB as a complete system to ensure that it performs as intended. This may include testing the board under various environmental conditions, such as temperature and humidity, to ensure its reliability and durability.
Ensuring PCB Reliability and Longevity
Thermal Management Techniques
Proper thermal management is crucial for ensuring the reliability and longevity of PCBs. Some techniques for managing heat dissipation include:
- Using high-thermal-conductivity materials
- Incorporating thermal vias and heat sinks
- Optimizing component placement and layout
Conformal Coating and Encapsulation
Conformal coating and encapsulation are methods of protecting PCBs from environmental factors such as moisture, dust, and chemical contaminants. These protective layers can help extend the life of the PCB and improve its reliability in harsh environments.
Designing for Manufacturing (DFM) and Assembly (DFA)
Designing for manufacturing and assembly involves considering the ease of fabrication and assembly during the PCB design process. By following DFM and DFA guidelines, you can reduce manufacturing costs, improve yields, and ensure the reliability of your PCBs.
Common PCB Failure Modes and How to Prevent Them
Solder Joint Failures
Solder joint failures are among the most common causes of PCB failure. These can be caused by poor soldering techniques, thermal stress, or mechanical stress. To prevent solder joint failures:
- Use appropriate solder alloys and flux
- Follow proper soldering techniques and temperature profiles
- Design for thermal expansion and mechanical stress
Copper Trace Cracking
Copper trace cracking can occur due to thermal or mechanical stress, leading to open circuits and PCB failure. To prevent copper trace cracking:
- Use appropriate trace widths and thicknesses
- Incorporate strain relief features
- Consider using Flexible PCB Materials in high-stress areas
Electrostatic Discharge (ESD) Damage
Electrostatic discharge can damage sensitive electronic components on PCBs. To protect against ESD:
- Use ESD-safe handling procedures and equipment
- Incorporate ESD protection devices on the PCB
- Design for ESD immunity
Frequently Asked Questions (FAQ)
- What is the difference between a single-sided and a double-sided PCB?
-
A single-sided PCB has components and traces on only one side of the board, while a double-sided PCB utilizes both sides for components and traces. Double-sided PCBs offer higher component density and more design flexibility.
-
What is the purpose of a ground plane in a PCB?
-
A ground plane is a large area of copper on a PCB layer that is connected to the ground (0V) of the circuit. It serves to provide a low-impedance return path for currents, reduce electromagnetic interference, and improve signal integrity.
-
How can I ensure the manufacturability of my PCB design?
-
To ensure the manufacturability of your PCB design, follow industry-standard design rules, such as minimum trace widths and spacings, via sizes, and hole diameters. Consult with your PCB manufacturer for their specific design guidelines and constraints.
-
What is the purpose of a solder mask on a PCB?
-
A solder mask is a protective layer applied to the copper traces on a PCB. It serves to prevent short circuits, protect the traces from oxidation and corrosion, and provide electrical insulation. The solder mask also helps to prevent solder bridging during the assembly process.
-
How can I test the functionality of my PCB Prototype?
- To test the functionality of your PCB prototype, you can use various methods such as in-circuit testing (ICT), flying probe testing, or functional testing. These methods allow you to verify the proper operation of individual components, check for short circuits or open connections, and ensure that the PCB performs as intended in its final application.
Conclusion
Ensuring the quality and reliability of PCBs is a multi-faceted process that involves careful design, manufacturing, and testing. By understanding PCB design fundamentals, following best practices, and implementing appropriate quality control measures, you can create PCBs that meet your performance and reliability requirements.
Proper PCB design and manufacturing not only contribute to the longevity and functionality of electronic devices but also help to reduce costs and improve time-to-market. By staying up-to-date with the latest technologies and techniques in PCB design and manufacturing, you can stay ahead of the competition and deliver high-quality, reliable products to your customers.
Leave a Reply