Introduction to Flying Probe Testing
Flying probe testing is a powerful and versatile method for conducting electrical tests on printed circuit boards (PCBs) and other electronic components. Unlike traditional bed-of-nails testing, which requires a custom-built fixture for each unique PCB design, flying probe testing uses movable probes that can adapt to different board layouts. This flexibility makes flying probe testing an increasingly popular choice for manufacturers seeking to improve efficiency, reduce costs, and enhance product quality.
In this article, we will explore the fundamentals of flying probe testing, its advantages and limitations, and its applications in various industries. We will also discuss the key considerations for implementing flying probe testing in your manufacturing process and provide insights into the future of this technology.
What is Flying Probe Testing?
Flying probe testing is an automated electrical testing method that uses movable probes to make contact with test points on a PCB or electronic component. The probes are mounted on a moving head that can traverse the surface of the board, allowing them to access any point on the board without the need for a custom-built fixture.
During the testing process, the probes make contact with the test points and perform a series of electrical measurements, such as continuity, resistance, capacitance, and voltage. The test results are then compared to a set of predefined criteria to determine whether the board meets the required specifications.
Advantages of Flying Probe Testing
Flying probe testing offers several advantages over traditional bed-of-nails testing, including:
-
Flexibility: Flying probe testing can adapt to different board layouts without the need for a custom-built fixture, making it ideal for low-volume production runs or prototypes.
-
Cost-effectiveness: By eliminating the need for custom fixtures, flying probe testing can significantly reduce the cost of electrical testing, particularly for small to medium-sized production runs.
-
Improved test coverage: Flying probe testing can access test points that may be difficult or impossible to reach with a bed-of-nails fixture, resulting in improved test coverage and higher fault detection rates.
-
Faster setup times: Since flying probe testing does not require a custom fixture, setup times are typically much faster than with bed-of-nails testing, allowing for quicker turnaround times.
-
Reduced operator intervention: Flying probe testing is highly automated, requiring minimal operator intervention, which can help to reduce the risk of human error and improve overall testing efficiency.
Limitations of Flying Probe Testing
While flying probe testing offers many advantages, it also has some limitations, including:
-
Slower test speeds: Flying probe testing is generally slower than bed-of-nails testing, particularly for high-volume production runs, due to the time required for the probes to move between test points.
-
Limited test point accessibility: Flying probe testing may not be able to access all test points on a board, particularly those that are very close together or located under components.
-
Potential for probe damage: The constant movement of the probes can cause wear and tear over time, potentially leading to probe damage and reduced testing accuracy.
-
Higher equipment costs: Flying probe test equipment is generally more expensive than bed-of-nails test equipment, which can be a significant consideration for smaller manufacturers.
Applications of Flying Probe Testing
Flying probe testing is used in a wide range of industries, including:
Aerospace and Defense
In the aerospace and defense industry, the reliability and performance of electronic components are critical. Flying probe testing is often used to test high-density, complex PCBs used in avionics, radar systems, and other mission-critical applications. The flexibility and improved test coverage offered by flying probe testing make it an ideal choice for ensuring the highest levels of quality and reliability.
Automotive
The automotive industry relies heavily on electronic components for everything from engine management systems to infotainment and advanced driver assistance systems (ADAS). Flying probe testing is used to test these components, ensuring they meet the strict quality and reliability standards required for automotive applications. The ability to quickly adapt to different board layouts makes flying probe testing particularly well-suited for the rapid pace of innovation in the automotive industry.
Medical Devices
Medical devices, such as pacemakers, defibrillators, and patient monitoring systems, require extremely high levels of reliability and performance. Flying probe testing is used to test the complex, high-density PCBs used in these devices, ensuring they meet the stringent regulatory requirements for medical equipment. The improved test coverage and reduced operator intervention offered by flying probe testing make it an ideal choice for the medical device industry.
Consumer Electronics
The consumer electronics industry is characterized by rapidly evolving product designs and short product lifecycles. Flying probe testing is often used to test prototypes and low-volume production runs of smartphones, tablets, wearables, and other consumer devices. The flexibility and cost-effectiveness of flying probe testing make it well-suited for the fast-paced nature of the consumer electronics industry.
Industrial Automation
Industrial automation systems, such as programmable logic controllers (PLCs), sensors, and actuators, rely on high-quality electronic components to ensure reliable and efficient operation. Flying probe testing is used to test these components, ensuring they meet the required specifications for industrial applications. The ability to quickly adapt to different board layouts and improved test coverage make flying probe testing an ideal choice for the industrial automation industry.
Implementing Flying Probe Testing
When considering implementing flying probe testing in your manufacturing process, there are several key factors to keep in mind:
-
Test coverage requirements: Determine the level of test coverage required for your products and ensure that flying probe testing can meet those requirements.
-
Production volume: Consider the production volume of your products and whether flying probe testing can meet your throughput requirements.
-
Board complexity: Evaluate the complexity of your PCBs and ensure that flying probe testing can effectively test all required points.
-
Equipment selection: Choose flying probe test equipment that meets your specific requirements, considering factors such as test speed, accuracy, and probe configuration.
-
operator training: Ensure that your operators are properly trained in the use of flying probe test equipment and can effectively interpret test results.
-
Integration with existing processes: Consider how flying probe testing will integrate with your existing manufacturing processes, including any necessary changes to workflow or data management systems.
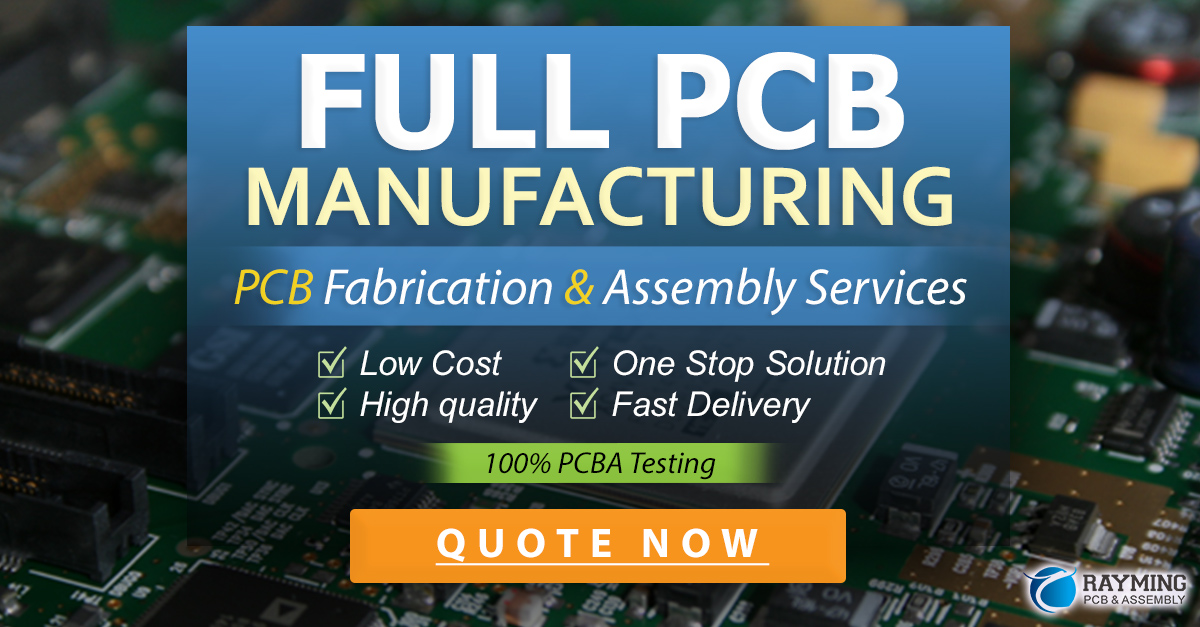
Future of Flying Probe Testing
As electronic products continue to become more complex and miniaturized, the demand for flexible and efficient testing methods will only continue to grow. Flying probe testing is well-positioned to meet this demand, with ongoing advancements in probe technology, motion control systems, and software algorithms.
Some of the key trends and developments in flying probe testing include:
-
Increased test speeds: Manufacturers are continually working to improve the speed of flying probe testing, with newer systems capable of testing up to several thousand points per minute.
-
Improved probe designs: Advances in probe technology, such as the use of high-performance alloys and coatings, are helping to reduce probe wear and improve contact reliability.
-
Enhanced software capabilities: Sophisticated software algorithms are being developed to optimize probe routing, minimize test times, and improve fault detection and diagnosis.
-
Integration with other testing methods: Flying probe testing is increasingly being used in combination with other testing methods, such as automated optical inspection (AOI) and boundary scan testing, to provide a more comprehensive and efficient testing solution.
As these trends continue to evolve, flying probe testing is likely to become an even more essential tool for manufacturers seeking to ensure the highest levels of quality and reliability in their electronic products.
Frequently Asked Questions (FAQ)
-
Q: What is the main difference between flying probe testing and bed-of-nails testing?
A: The main difference is that flying probe testing uses movable probes to make contact with test points on a PCB, while bed-of-nails testing uses a custom-built fixture with fixed probes. Flying probe testing is more flexible and can adapt to different board layouts, while bed-of-nails testing is faster for high-volume production runs. -
Q: Can flying probe testing completely replace bed-of-nails testing?
A: In many cases, flying probe testing can be used as an alternative to bed-of-nails testing, particularly for low to medium-volume production runs or products with frequently changing designs. However, for high-volume production runs, bed-of-nails testing may still be the most efficient and cost-effective option. -
Q: How does flying probe testing improve test coverage compared to bed-of-nails testing?
A: Flying probe testing can access test points that may be difficult or impossible to reach with a bed-of-nails fixture, such as those located under components or in tight spaces. This improved accessibility allows for more comprehensive testing and higher fault detection rates. -
Q: What are the key factors to consider when selecting flying probe test equipment?
A: When selecting flying probe test equipment, key factors to consider include test speed, accuracy, probe configuration, software capabilities, and compatibility with your specific PCB designs and testing requirements. It’s also important to consider the level of technical support and training provided by the equipment manufacturer. -
Q: How can manufacturers optimize their flying probe testing process for maximum efficiency?
A: To optimize flying probe testing for maximum efficiency, manufacturers should carefully plan their testing strategy, including selecting the appropriate test points, optimizing probe routing, and minimizing unnecessary movements. They should also ensure that their operators are properly trained and that their testing process is fully integrated with their overall manufacturing workflow. Regular maintenance and calibration of the testing equipment can also help to ensure optimal performance and minimize downtime.
Conclusion
Flying probe testing is a powerful and versatile method for conducting electrical tests on PCBs and electronic components. By offering flexibility, cost-effectiveness, and improved test coverage, flying probe testing has become an increasingly popular choice for manufacturers across a wide range of industries.
As electronic products continue to become more complex and miniaturized, the demand for efficient and reliable testing methods will only continue to grow. With ongoing advancements in probe technology, motion control systems, and software algorithms, flying probe testing is well-positioned to meet this demand and help manufacturers ensure the highest levels of quality and reliability in their products.
By carefully considering the key factors involved in implementing flying probe testing and staying up-to-date with the latest trends and developments in this field, manufacturers can unlock the full potential of this powerful testing method and position themselves for success in an increasingly competitive marketplace.
Leave a Reply