What is PCBA?
PCBA stands for Printed Circuit Board Assembly, which is the process of assembling various electronic components onto a printed circuit board (PCB) to create a functional electronic device. A PCB is a flat board made of insulating materials, such as fiberglass or plastic, with conductive pathways printed on its surface. These pathways, also known as traces, connect the electronic components mounted on the board, allowing for the flow of electrical signals and power.
PCBAs are essential in the production of electronic devices, as they provide a compact, reliable, and efficient means of interconnecting components. They are used in a wide range of applications, from consumer electronics and automotive systems to medical devices and aerospace equipment.
Types of PCBA
There are several types of PCBA, each with its own unique characteristics and manufacturing processes. The most common types include:
1. Surface Mount Technology (SMT) PCBA
SMT PCBA involves mounting components directly onto the surface of the PCB using solder paste and a reflow oven. This method allows for smaller components and higher component density compared to through-hole mounting. SMT is widely used in the production of modern electronic devices due to its efficiency and cost-effectiveness.
2. Through-Hole Technology (THT) PCBA
THT PCBA involves inserting component leads through pre-drilled holes in the PCB and soldering them to the opposite side. This method provides a stronger mechanical connection between the components and the board, making it suitable for applications that require high reliability or are subject to mechanical stress. However, THT is less efficient and more expensive than SMT.
3. Mixed Technology PCBA
Mixed technology PCBA combines both SMT and THT methods on a single board. This approach is used when certain components are not available in SMT packages or when THT is required for specific components, such as connectors or large capacitors.
4. Flex and Rigid-flex PCBA
Flex and rigid-flex PCBAs use flexible substrates, such as polyimide, to create bendable or conformable circuits. Flex PCBAs are used in applications that require the circuit to fit into tight spaces or conform to irregular shapes, such as in wearable devices or automotive systems. Rigid-flex PCBAs combine both rigid and flexible sections, allowing for greater design flexibility and improved reliability.
Applications of PCBA
PCBAs are used in a wide range of industries and applications. Some of the most common applications include:
1. Consumer Electronics
PCBAs are found in almost all consumer electronic devices, such as smartphones, tablets, laptops, televisions, and home appliances. They enable the compact, efficient, and cost-effective design of these devices, while providing the necessary functionality and performance.
2. Automotive Electronics
Modern vehicles rely heavily on electronic systems for various functions, such as engine management, safety features, infotainment, and navigation. PCBAs are used in these systems to provide reliable and efficient control and communication between components.
3. Medical Devices
PCBAs play a crucial role in the development of medical devices, such as patient monitors, diagnostic equipment, and implantable devices. These applications require high reliability, precision, and adherence to strict regulatory standards, which can be achieved through the use of specialized PCBA Manufacturing processes and materials.
4. Aerospace and Defense
Aerospace and defense applications demand the highest levels of reliability and performance, as failure can have catastrophic consequences. PCBAs used in these applications must withstand extreme environmental conditions, such as temperature fluctuations, vibration, and radiation. Specialized PCBA manufacturing processes, such as conformal coating and underfill, are used to ensure the robustness and longevity of these circuits.
5. Industrial Control Systems
PCBAs are used in various industrial control systems, such as programmable logic controllers (PLCs), human-machine interfaces (HMIs), and sensors. These applications require rugged and reliable circuits that can operate in harsh industrial environments, such as those with high temperatures, humidity, or exposure to chemicals.
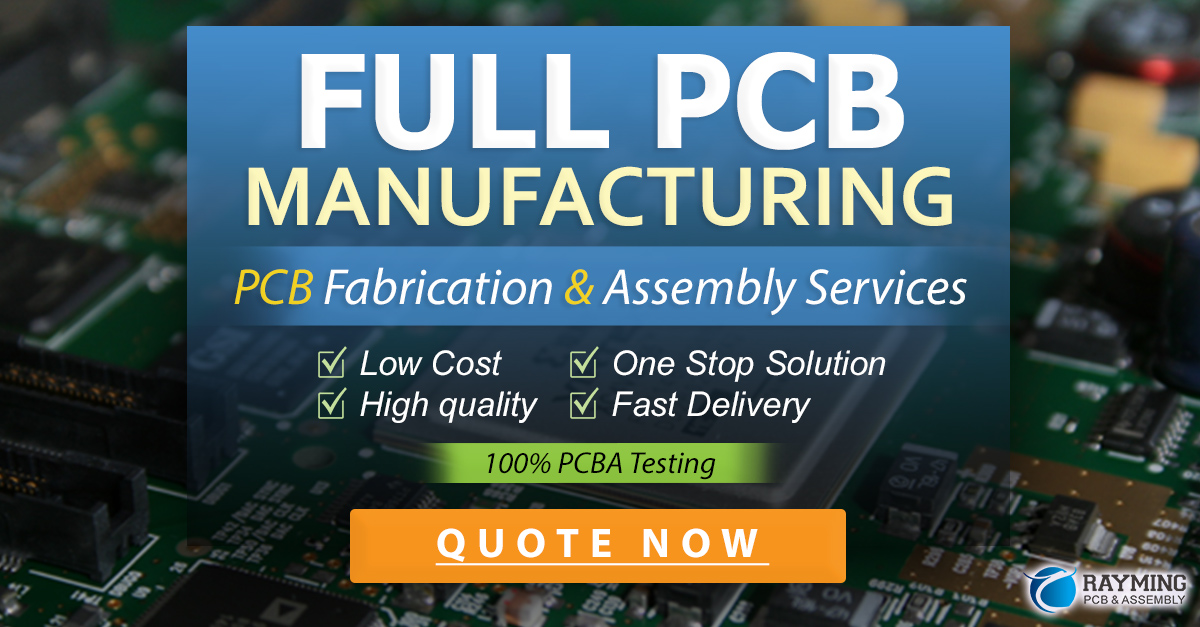
PCBA Manufacturing Process
The PCBA manufacturing process involves several steps, each of which must be carefully controlled to ensure the quality and reliability of the final product. The main steps in the PCBA manufacturing process are:
1. PCB Design and Fabrication
The first step in the PCBA process is the design and fabrication of the PCB. This involves creating a schematic diagram of the circuit, designing the PCB layout, and generating the necessary files for manufacturing. The PCB is then fabricated using a combination of photolithography, etching, and plating processes.
2. Solder Paste Application
For SMT PCBA, solder paste is applied to the PCB using a stencil printing process. The stencil is a thin metal sheet with openings that correspond to the component pads on the PCB. Solder paste is squeezed through the stencil onto the pads, depositing a precise amount of solder for each component.
3. Component Placement
The next step is to place the electronic components onto the PCB. For SMT PCBA, this is done using automated pick-and-place machines, which use vacuum nozzles to pick up components from reels or trays and place them onto the solder paste-coated pads. For THT PCBA, components are inserted manually or using automated insertion machines.
4. Reflow Soldering
After component placement, the PCB undergoes a reflow soldering process. The board is passed through a reflow oven, which heats the solder paste to its melting point, allowing it to flow and form a strong mechanical and electrical connection between the components and the PCB. The temperature profile of the reflow process must be carefully controlled to ensure proper solder joint formation and to avoid damage to the components.
5. Inspection and Testing
After soldering, the PCBA undergoes various inspection and testing procedures to ensure its quality and functionality. These may include:
- Visual inspection: Checking for visible defects, such as misaligned components, solder bridges, or insufficient solder.
- Automated Optical Inspection (AOI): Using computer vision systems to detect and classify assembly defects.
- X-ray inspection: Examining the internal structure of solder joints and components for hidden defects.
- In-Circuit Testing (ICT): Verifying the electrical connectivity and functionality of individual components and circuits using a Bed-of-Nails Test fixture.
- Functional testing: Testing the overall performance and functionality of the assembled device under real-world operating conditions.
6. Conformal Coating and Potting
For applications that require additional environmental protection, the PCBA may undergo conformal coating or potting. Conformal coating involves applying a thin layer of protective material, such as acrylic, silicone, or polyurethane, over the surface of the PCBA. Potting involves encapsulating the entire PCBA in a protective resin or compound. These processes help to protect the PCBA from moisture, dust, and other environmental hazards.
7. Final Assembly and Packaging
The final step in the PCBA process is the assembly of the PCBA into the finished product or enclosure, followed by packaging and shipping. This may involve additional processes, such as cable assembly, labeling, and custom packaging, depending on the specific requirements of the application.
PCBA Quality Control and Standards
Ensuring the quality and reliability of PCBAs is critical for the success of any electronic product. Several quality control measures and industry standards are used to maintain the integrity of the PCBA manufacturing process:
1. IPC Standards
The Association Connecting Electronics Industries (IPC) is a global trade association that develops and maintains standards for the Electronic Assembly industry. Some of the key IPC standards related to PCBA include:
- IPC-A-610: Acceptability of Electronic Assemblies
- IPC-J-STD-001: Requirements for Soldered Electrical and Electronic Assemblies
- IPC-A-600: Acceptability of Printed Boards
These standards provide guidelines and criteria for evaluating the quality of PCBAs and ensuring consistency across different manufacturers and assembly processes.
2. ISO Standards
The International Organization for Standardization (ISO) develops and maintains standards for various industries, including electronics manufacturing. Some of the relevant ISO standards for PCBA include:
- ISO 9001: Quality Management Systems
- ISO 14001: Environmental Management Systems
- ISO 13485: Medical Devices – Quality Management Systems
Adherence to these standards demonstrates a manufacturer’s commitment to quality, reliability, and continuous improvement.
3. Statistical Process Control (SPC)
SPC is a method of monitoring and controlling the manufacturing process to ensure consistent quality and to identify and correct any deviations from the desired specifications. SPC involves collecting and analyzing data from various process parameters, such as solder paste deposition, component placement accuracy, and reflow oven temperature profiles. By monitoring these parameters and taking corrective actions when necessary, manufacturers can maintain a high level of quality and minimize defects.
4. Traceability
Traceability is the ability to track the history, application, and location of a PCBA throughout its lifecycle. This is particularly important for applications that require strict quality control and regulatory compliance, such as medical devices and aerospace systems. Traceability is achieved through the use of unique identifiers, such as barcodes or RFID tags, which are attached to the PCBA and linked to a database containing information about its manufacturing history, test results, and other relevant data.
Frequently Asked Questions (FAQ)
1. What is the difference between a PCB and a PCBA?
A PCB is a bare printed circuit board without any components mounted on it. A PCBA is a PCB with electronic components assembled onto it, forming a functional electronic circuit.
2. What are the advantages of SMT over THT?
SMT offers several advantages over THT, including:
- Smaller component sizes and higher component density
- Faster and more efficient assembly process
- Lower production costs for high-volume manufacturing
- Better high-frequency performance due to shorter lead lengths
3. What is the purpose of conformal coating or potting?
Conformal coating and potting are used to protect PCBAs from environmental hazards, such as moisture, dust, and chemicals. They help to improve the reliability and longevity of the PCBA, particularly in harsh operating conditions.
4. What is the role of IPC standards in PCBA manufacturing?
IPC standards provide guidelines and criteria for evaluating the quality and acceptability of PCBAs. They help to ensure consistency and reliability across different manufacturers and assembly processes, and provide a common language for communication between customers and suppliers.
5. How does traceability benefit PCBA manufacturing?
Traceability allows manufacturers to track the history, application, and location of a PCBA throughout its lifecycle. This helps to improve quality control, facilitate root cause analysis in case of failures, and ensure compliance with regulatory requirements. Traceability also enables more efficient supply chain management and inventory control.
In conclusion, PCBAs are essential components in the production of electronic devices across various industries. Understanding the types, applications, manufacturing processes, and quality control measures associated with PCBAs is crucial for designing, producing, and maintaining reliable and high-performance electronic products. As technology continues to advance, the importance of PCBAs in enabling innovation and driving progress in diverse fields will only continue to grow.
Leave a Reply