Introduction
Printed Circuit Board (PCB) assembly is a complex process that requires rigorous testing to ensure the quality and reliability of the final product. PCB Testing is crucial for identifying defects, ensuring functionality, and meeting industry standards. In this article, we will explore 13 effective test methods for PCB Assembly, their importance, and how they contribute to the overall quality of the PCB.
The Importance of PCB Testing
PCB testing is an essential step in the manufacturing process, as it helps to identify and rectify any issues before the PCB is used in the final product. Some of the key reasons why PCB testing is important include:
- Ensuring functionality: PCB testing verifies that the board functions as intended, meeting all the specified requirements.
- Identifying defects: Testing helps to identify any manufacturing defects, such as short circuits, open circuits, or incorrect component placement.
- Meeting industry standards: PCB testing ensures that the board meets the required industry standards, such as IPC (Association Connecting Electronics Industries) standards.
- Reducing costs: Early detection of defects through testing can save significant costs associated with repairs or replacements later in the product lifecycle.
- Enhancing reliability: Thorough testing improves the overall reliability of the PCB, reducing the likelihood of failures during operation.
13 Effective Test Methods for PCB Assembly
1. Visual Inspection
Visual inspection is the first and most basic test method for PCB assembly. It involves examining the board with the naked eye or using magnification tools to identify any visible defects, such as:
- Solder bridges
- Cold solder joints
- Damaged components
- Incorrect component placement
- Contamination or foreign objects
While visual inspection is a simple method, it is essential for catching obvious defects early in the testing process.
2. Automated Optical Inspection (AOI)
Automated Optical Inspection (AOI) is a more advanced form of visual inspection that uses cameras and image processing software to examine the PCB. AOI systems can quickly and accurately detect a wide range of defects, including:
- Solder defects (e.g., bridges, insufficient solder, tombstoning)
- Component defects (e.g., missing, shifted, or rotated components)
- Polarity errors
- Incorrect component values
AOI is particularly useful for high-volume production, as it can inspect boards much faster than manual visual inspection.
3. X-Ray Inspection
X-ray inspection is a non-destructive testing method that uses X-rays to examine the internal structure of the PCB. This method is particularly useful for inspecting:
- Ball Grid Array (BGA) connections
- Flip-chip devices
- Through-hole solder joints
- Voids or cracks in solder joints
X-ray inspection can reveal defects that are not visible from the surface of the board, making it a valuable tool for ensuring the quality of complex assemblies.
4. In-Circuit Testing (ICT)
In-Circuit Testing (ICT) is a method that uses a bed-of-nails fixture to make electrical contact with specific points on the PCB. ICT can test for:
- Short circuits
- Open circuits
- Resistance values
- Capacitance values
- Inductance values
- Diode polarity
- Transistor functionality
ICT is an effective way to verify the correct assembly of the board and ensure that all components are functioning as expected.
5. Flying Probe Testing
Flying probe testing is an alternative to ICT that uses movable probes instead of a fixed bed-of-nails fixture. The probes can be programmed to make contact with specific points on the PCB, allowing for greater flexibility in testing. Flying probe testing can perform many of the same tests as ICT, including:
- Continuity testing
- Resistance measurement
- Capacitance measurement
- Inductance measurement
- Diode and transistor testing
Flying probe testing is particularly useful for low-volume production or prototypes, where creating a dedicated ICT fixture may not be cost-effective.
6. Boundary Scan Testing
Boundary scan testing, also known as JTAG (Joint Test Action Group) testing, is a method that uses special circuitry built into the components on the PCB to test for defects. Boundary scan testing can detect:
- Open circuits
- Short circuits
- Stuck-at faults
- Delay faults
Boundary scan testing is particularly useful for testing complex digital circuits, such as microprocessors and FPGAs, which may be difficult to test using other methods.
7. Functional Testing
Functional testing involves testing the PCB to ensure that it performs its intended function correctly. This may include:
- Power-on testing
- Programming and configuration testing
- Signal integrity testing
- Communication protocol testing
- Environmental testing (e.g., temperature, humidity, vibration)
Functional testing is essential for verifying that the PCB meets all the specified requirements and will perform reliably in its intended application.
8. Burn-In Testing
Burn-in testing involves subjecting the PCB to elevated temperatures and operating conditions for an extended period to identify any early-life failures. Burn-in testing can help to identify:
- Component defects
- Solder joint failures
- Thermal stress issues
- Intermittent faults
By exposing the PCB to stress conditions, burn-in testing can help to improve the overall reliability of the final product.
9. Thermal Imaging
Thermal imaging, also known as infrared (IR) thermography, is a non-contact testing method that uses an IR camera to measure the temperature distribution across the PCB. Thermal imaging can help to identify:
- Hot spots caused by component failures or design issues
- Cooling system inefficiencies
- Power dissipation problems
Thermal imaging is particularly useful for identifying thermal management issues that may affect the long-term reliability of the PCB.
10. 3D Automated X-Ray Inspection (3D AXI)
3D Automated X-Ray Inspection (3D AXI) is an advanced form of X-ray inspection that uses computed tomography (CT) to create a three-dimensional image of the PCB. 3D AXI can detect:
- Solder joint defects (e.g., voids, cracks, insufficient solder)
- BGA and QFN (Quad Flat No-lead) defects
- Passive component defects (e.g., capacitors, resistors)
3D AXI provides a more comprehensive view of the PCB than traditional 2D X-ray inspection, allowing for more accurate defect detection.
11. Electromagnetic Compatibility (EMC) Testing
Electromagnetic Compatibility (EMC) testing ensures that the PCB does not emit excessive electromagnetic interference (EMI) and can function properly in the presence of external electromagnetic fields. EMC testing may include:
- Radiated emissions testing
- Conducted emissions testing
- Electromagnetic susceptibility testing
- Electrostatic discharge (ESD) testing
EMC testing is crucial for ensuring that the PCB complies with relevant regulations and will not cause or be affected by electromagnetic interference in its intended operating environment.
12. Acoustic Microscopy
Acoustic microscopy is a non-destructive testing method that uses high-frequency sound waves to create images of the internal structure of the PCB. Acoustic microscopy can detect:
- Delamination
- Voids
- Cracks
- Disbonds
Acoustic microscopy is particularly useful for inspecting multi-layer PCBs and identifying defects that may not be visible using other testing methods.
13. Interconnect Stress Testing (IST)
Interconnect Stress Testing (IST) is a method that applies mechanical stress to the PCB to simulate the stresses that the board may experience during assembly, shipping, or operation. IST can help to identify:
- Weak solder joints
- Component lead failures
- Trace or via failures
By subjecting the PCB to controlled stress conditions, IST can help to ensure that the board will remain reliable throughout its intended lifecycle.
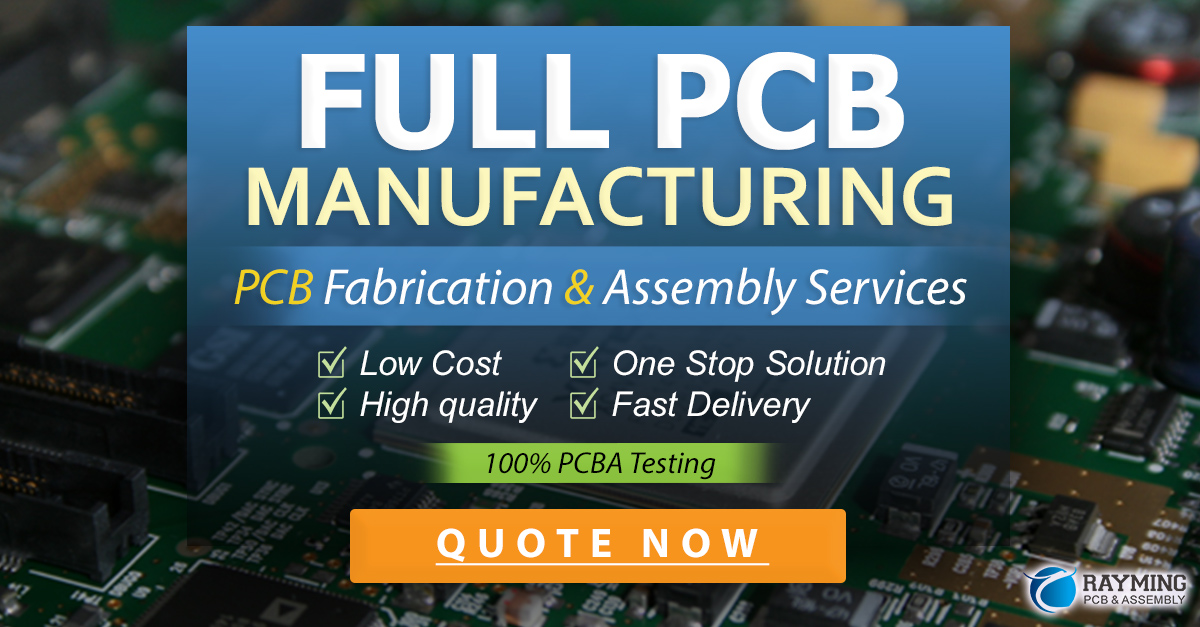
Frequently Asked Questions (FAQ)
- What is the difference between AOI and visual inspection?
-
AOI is an automated process that uses cameras and image processing software to inspect the PCB, while visual inspection is a manual process performed by a human operator. AOI is faster and more consistent than visual inspection but may not catch all defects that a skilled human inspector would.
-
Can X-ray inspection detect all types of defects?
-
X-ray inspection is particularly useful for detecting defects in hidden or obscured areas of the PCB, such as BGA connections and through-hole solder joints. However, it may not detect all surface-level defects, such as component placement errors or solder bridges.
-
Is boundary scan testing applicable to all types of components?
-
Boundary scan testing requires special circuitry to be built into the components on the PCB. While many modern digital components, such as microprocessors and FPGAs, include boundary scan functionality, some analog and passive components may not be compatible with this testing method.
-
How does thermal imaging differ from traditional temperature testing?
-
Thermal imaging provides a non-contact, two-dimensional map of the temperature distribution across the PCB, allowing for quick identification of hot spots and thermal management issues. Traditional temperature testing, such as using thermocouples or resistance temperature detectors (RTDs), measures the temperature at specific points on the board and may not provide a complete picture of the thermal profile.
-
Is EMC testing required for all PCBs?
- The requirement for EMC testing depends on the intended application and the relevant regulations. Many industries, such as automotive, aerospace, and medical devices, have strict EMC requirements that PCBs must meet. However, some low-power or non-critical applications may not require extensive EMC testing.
Conclusion
Effective PCB testing is essential for ensuring the quality, reliability, and functionality of printed circuit board assemblies. The 13 test methods discussed in this article, ranging from visual inspection to advanced techniques like 3D AXI and acoustic microscopy, provide a comprehensive approach to identifying defects and verifying the performance of PCBs.
By implementing a combination of these test methods, manufacturers can catch defects early in the production process, reduce costs associated with repairs and replacements, and ultimately deliver high-quality products to their customers. As PCB technology continues to evolve, it is crucial for manufacturers to stay up-to-date with the latest testing methods and best practices to maintain a competitive edge in the industry.
Test Method | Detects |
---|---|
Visual Inspection | Solder bridges, cold solder joints, damaged components, incorrect component placement, contamination |
Automated Optical Inspection (AOI) | Solder defects, component defects, polarity errors, incorrect component values |
X-Ray Inspection | BGA connections, flip-chip devices, through-hole solder joints, voids, cracks |
In-Circuit Testing (ICT) | Short circuits, open circuits, resistance values, capacitance values, inductance values, diode polarity, transistor functionality |
Flying Probe Testing | Continuity, resistance, capacitance, inductance, diode and transistor functionality |
Boundary Scan Testing | Open circuits, short circuits, stuck-at faults, delay faults |
Functional Testing | Power-on, programming and configuration, signal integrity, communication protocol, environmental factors |
Burn-In Testing | Component defects, solder joint failures, thermal stress issues, intermittent faults |
Thermal Imaging | Hot spots, cooling system inefficiencies, power dissipation problems |
3D Automated X-Ray Inspection (3D AXI) | Solder joint defects, BGA and QFN defects, passive component defects |
Electromagnetic Compatibility (EMC) Testing | Radiated emissions, conducted emissions, electromagnetic susceptibility, electrostatic discharge |
Acoustic Microscopy | Delamination, voids, cracks, disbonds |
Interconnect Stress Testing (IST) | Weak solder joints, component lead failures, trace or via failures |
Leave a Reply