Introduction to SolderMask and Its Role in PCB Manufacturing
SolderMask, also known as solder resist or solder stop mask, is a thin protective layer applied to the copper traces of a printed circuit board (PCB). Its primary purpose is to prevent solder bridges from forming between closely spaced solder pads during the soldering process. SolderMask also provides protection against oxidation and contamination of the copper traces, enhancing the PCB’s durability and reliability.
In PCB manufacturing, SolderMask is a crucial component that has undergone significant advancements over the years. This article will explore the progress made in SolderMask technology and its impact on the PCB universe.
The Evolution of SolderMask Materials
Early SolderMask Materials
In the early days of PCB manufacturing, SolderMask materials were limited to screen-printed epoxy or UV-curable inks. These materials had several limitations, such as poor resolution, inconsistent thickness, and limited color options. Additionally, they were prone to cracking and peeling, which could lead to solder bridges and other defects.
Modern SolderMask Materials
With advancements in material science, modern SolderMask materials have overcome many of the limitations of their predecessors. Today, the most common SolderMask materials include:
- Liquid PhotoImageable (LPI) SolderMask
- LPI SolderMask is a UV-curable polymer that offers excellent resolution, consistency, and durability.
- It allows for thinner application and finer feature definition compared to traditional screen-printed SolderMask.
-
LPI SolderMask is available in a variety of colors, including green, blue, red, yellow, black, and white.
-
Dry Film SolderMask
- Dry Film SolderMask is a photopolymer film that is laminated onto the PCB surface and then exposed and developed.
- It offers excellent thickness control and uniformity, making it suitable for high-density PCB designs.
- Dry Film SolderMask is available in various colors and can be used for both rigid and flexible PCBs.
The following table compares the properties of LPI and Dry Film SolderMask:
Property | LPI SolderMask | Dry Film SolderMask |
---|---|---|
Application Method | Spray or Curtain Coating | Lamination |
Thickness Control | Good | Excellent |
Resolution | Excellent | Good |
Flexibility | Good | Excellent |
Suitability for HDI PCBs | Excellent | Good |
Advancements in SolderMask Application Techniques
Spray Coating
Spray coating is a common method for applying LPI SolderMask to PCBs. In this process, the liquid SolderMask is atomized and sprayed onto the PCB surface using a spray nozzle. Advancements in spray coating technology have led to more precise control over the Soldermask Thickness and improved uniformity.
Curtain Coating
Curtain coating is another method for applying LPI SolderMask, particularly suitable for high-volume production. In this process, a continuous curtain of liquid SolderMask is formed and falls onto the moving PCB surface. Curtain coating offers excellent thickness control and uniformity, and it is capable of coating both sides of the PCB simultaneously.
Inkjet Printing
Inkjet printing is an emerging technology for SolderMask application that offers several advantages over traditional methods. With inkjet printing, the SolderMask is selectively deposited onto the PCB surface using a high-resolution inkjet printhead. This allows for precise control over the SolderMask thickness and enables the creation of fine features and custom patterns.
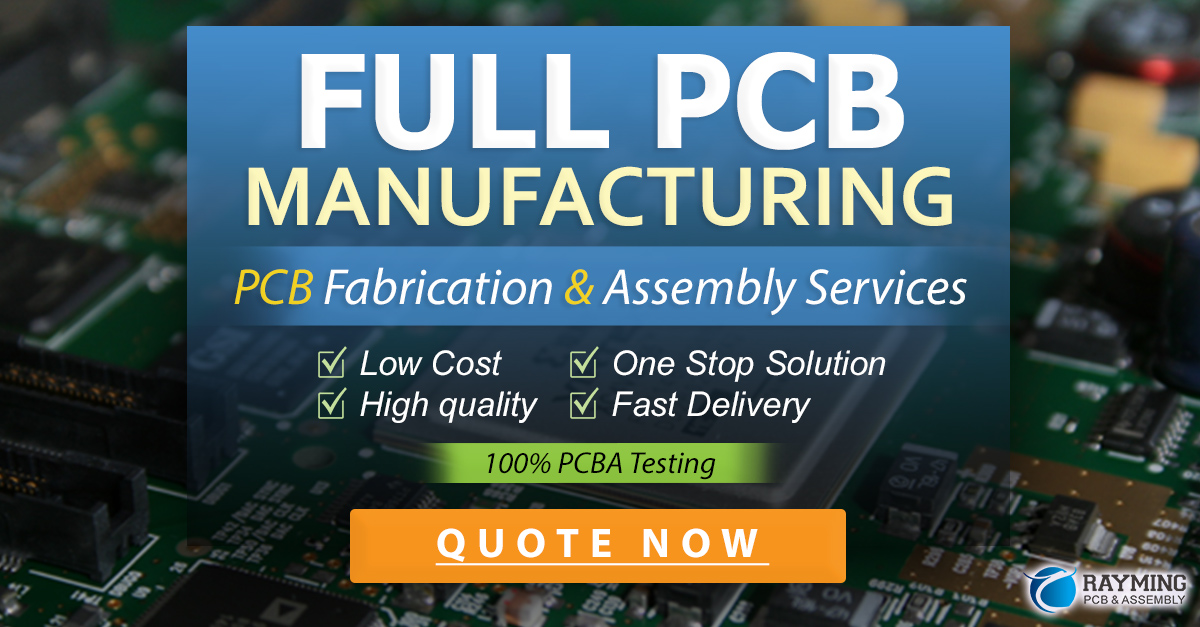
The Impact of SolderMask Progress on PCB Design and Manufacturing
Enabling High-Density Interconnect (HDI) PCBs
The advancements in SolderMask materials and application techniques have played a crucial role in enabling the production of High-Density Interconnect (HDI) PCBs. HDI PCBs feature fine pitch components, narrow trace widths, and small via sizes, which require precise and uniform SolderMask coverage.
Modern LPI and Dry Film SolderMask materials, combined with advanced application methods, allow for the creation of HDI PCBs with the following features:
- Trace widths as narrow as 50 μm
- Via diameters as small as 100 μm
- Solder pad pitches as fine as 0.4 mm
The following table compares the feature sizes of conventional and HDI PCBs:
Feature | Conventional PCB | HDI PCB |
---|---|---|
Trace Width | 100-150 μm | 50-100 μm |
Via Diameter | 200-300 μm | 100-150 μm |
Solder Pad Pitch | 0.8-1.27 mm | 0.4-0.8 mm |
Improving PCB Reliability and Durability
The progress in SolderMask technology has also contributed to improving the reliability and durability of PCBs. Modern SolderMask materials offer better adhesion to the copper surface, higher resistance to chemical and environmental factors, and improved mechanical properties.
Some of the key benefits of advanced SolderMask materials include:
- Enhanced protection against solder bridges and short circuits
- Increased resistance to moisture, chemicals, and UV radiation
- Improved thermal stability and resistance to high temperatures
- Better mechanical strength and flexibility, reducing the risk of cracking and peeling
These improvements in SolderMask properties have led to PCBs with longer lifespans and higher reliability, even in harsh operating conditions.
Enabling Advanced PCB Manufacturing Processes
The advancements in SolderMask technology have also enabled the adoption of advanced PCB manufacturing processes, such as:
- Via-in-Pad (VIP) Technology
- VIP technology involves placing vias directly in the solder pads, allowing for higher component density and improved signal integrity.
-
Modern SolderMask materials, with their excellent resolution and uniformity, enable the reliable production of VIP PCBs.
-
Embedded Components
- Embedded components, such as resistors and capacitors, are placed inside the PCB substrate to save space and improve performance.
-
Advanced SolderMask materials, with their compatibility with various lamination processes, facilitate the manufacturing of PCBs with embedded components.
-
3D PCBs
- 3D PCBs feature multiple layers of components and interconnects, arranged in a three-dimensional structure.
- The progress in SolderMask technology, particularly in terms of flexibility and conformability, has made it possible to create 3D PCBs with reliable SolderMask coverage.
Future Trends and Challenges in SolderMask Technology
Trends in SolderMask Materials
The future of SolderMask technology is expected to bring further advancements in materials, focusing on the following areas:
- Improved Environmental Friendliness
- There is a growing demand for SolderMask materials that are free from hazardous substances, such as halogen and heavy metals.
-
Research is underway to develop eco-friendly SolderMask formulations that maintain the same level of performance as traditional materials.
-
Enhanced Thermal and Electrical Properties
- As PCBs are used in more demanding applications, such as high-power electronics and 5G communications, there is a need for SolderMask materials with improved thermal conductivity and dielectric properties.
-
Novel SolderMask formulations incorporating ceramic fillers or conductive polymers are being explored to meet these requirements.
-
Increased Flexibility and Stretchability
- The growth of flexible and stretchable electronics has created a demand for SolderMask materials that can withstand repeated bending and stretching without cracking or delaminating.
- Researchers are developing elastomeric SolderMask materials and hybrid composites that combine the benefits of traditional and flexible materials.
Challenges in SolderMask Application and Processing
As PCB designs become more complex and feature sizes continue to shrink, SolderMask application and processing face new challenges:
- Achieving Uniform Thickness and Coverage
- With the increasing use of fine-pitch components and HDI designs, maintaining a uniform SolderMask thickness and ensuring complete coverage of the copper traces become more challenging.
-
Advancements in application methods, such as inkjet printing and electrophoretic deposition, are being explored to address these challenges.
-
Minimizing SolderMask Residues and Contamination
- SolderMask residues and contamination can lead to poor Solder Joint Quality and reduced PCB reliability.
-
Improved cleaning processes and SolderMask formulations with lower residue levels are being developed to mitigate these issues.
-
Ensuring Compatibility with New PCB Materials and Processes
- As new PCB substrate materials, such as high-frequency laminates and Metal-Core PCBs, gain popularity, SolderMask materials must be adapted to ensure compatibility and adhesion.
- Similarly, SolderMask processes need to be optimized for integration with advanced manufacturing techniques, such as 3D printing and laser drilling.
Frequently Asked Questions (FAQ)
- What is the purpose of SolderMask on a PCB?
-
SolderMask serves two main purposes on a PCB:
- It prevents solder bridges from forming between closely spaced solder pads during the soldering process.
- It protects the copper traces from oxidation, contamination, and mechanical damage, enhancing the PCB’s durability and reliability.
-
What are the most common SolderMask colors?
-
The most common SolderMask colors are green, blue, red, yellow, black, and white. Green is the most widely used color in the PCB industry, followed by blue and red.
-
Can SolderMask be applied to flexible PCBs?
-
Yes, SolderMask can be applied to flexible PCBs. Dry Film SolderMask is particularly suitable for flexible PCBs due to its excellent flexibility and conformability. LPI SolderMask can also be used on flexible PCBs, provided that the material has been formulated for flexibility.
-
How does SolderMask affect the impedance of PCB traces?
-
SolderMask can affect the impedance of PCB traces by altering the dielectric constant of the medium surrounding the traces. The thickness and dielectric properties of the SolderMask material must be taken into account when designing PCBs for controlled impedance applications.
-
What is the typical thickness of SolderMask on a PCB?
- The typical thickness of SolderMask on a PCB ranges from 10 to 50 μm, depending on the application method and the specific requirements of the PCB design. LPI SolderMask can be applied in thinner layers (10-25 μm), while Dry Film SolderMask typically has a thickness of 15-50 μm.
Conclusion
The progress in SolderMask technology has been a critical factor in the advancement of the PCB universe. From the early days of screen-printed epoxy masks to the modern LPI and Dry Film materials, SolderMask has evolved to meet the ever-increasing demands of PCB design and manufacturing.
The advancements in SolderMask materials and application techniques have enabled the production of high-density interconnect PCBs, improved PCB reliability and durability, and facilitated the adoption of advanced manufacturing processes. As PCB technology continues to evolve, further progress in SolderMask technology is expected, focusing on improved environmental friendliness, enhanced thermal and electrical properties, and increased flexibility and stretchability.
However, challenges remain in achieving uniform thickness and coverage, minimizing residues and contamination, and ensuring compatibility with new PCB materials and processes. Addressing these challenges will require ongoing research and development efforts in SolderMask materials, application methods, and processing techniques.
In conclusion, the progress in SolderMask technology has been a key enabler of the advancements in the PCB universe, and it will continue to play a crucial role in shaping the future of PCB design and manufacturing.
Leave a Reply