The Role of Soldermask in PCB Manufacturing
Soldermask serves several important functions in PCB manufacturing:
-
Insulation: Soldermask acts as an insulating layer, preventing accidental short circuits between adjacent copper traces.
-
Protection: It protects the copper traces from oxidation, corrosion, and mechanical damage during handling and assembly.
-
Solder Control: Soldermask helps control the flow of molten solder during the soldering process, ensuring that solder only adheres to exposed metal surfaces such as pads and vias.
-
Aesthetics: Soldermask can be applied in various colors, improving the visual appearance of the PCB and making it easier to identify different components and regions.
Soldermask Application Process
The soldermask application process typically involves the following steps:
-
Cleaning: The PCB surface is cleaned to remove any contaminants that could affect soldermask adhesion.
-
Application: Soldermask is applied to the PCB surface using various methods, such as screen printing, curtain coating, or spray coating.
-
Curing: The applied soldermask is cured using heat, ultraviolet (UV) light, or a combination of both, depending on the type of soldermask material used.
-
Exposure: For photoimageable soldermasks, the cured layer is exposed to UV light through a photomask, which hardens the exposed areas while leaving the unexposed areas soluble.
-
Developing: The unexposed areas of the photoimageable soldermask are removed using a developer solution, revealing the desired pattern.
-
Final Curing: The remaining soldermask undergoes a final curing process to ensure complete polymerization and adhesion to the PCB surface.
Standard Soldermask Thicknesses
Soldermask thickness is typically measured in mils (thousandths of an inch) or microns (µm). The most common soldermask thicknesses used in the PCB industry are:
Thickness (mils) | Thickness (µm) |
---|---|
0.5 | 12.7 |
0.8 | 20.3 |
1.0 | 25.4 |
1.2 | 30.5 |
2.0 | 50.8 |
The choice of soldermask thickness depends on various factors, such as the PCB application, the desired level of protection, and the manufacturing capabilities of the PCB fabricator.
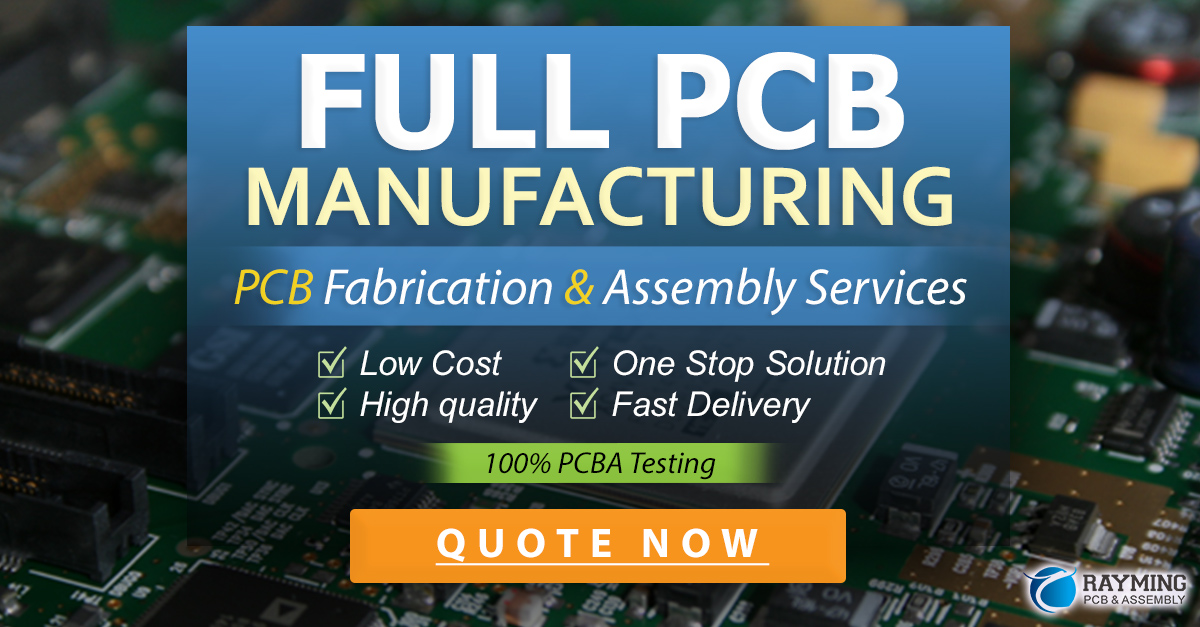
Impact of Soldermask Thickness on PCB Performance
Electrical Insulation
One of the primary functions of soldermask is to provide electrical insulation between adjacent copper traces. The thickness of the soldermask directly affects its insulating properties. A thicker soldermask layer offers better insulation, reducing the risk of short circuits and improving the overall reliability of the PCB.
However, excessively thick soldermask layers can also have drawbacks. They may increase the capacitance between traces, leading to signal integrity issues, especially at high frequencies. Thick soldermasks can also make it more challenging to achieve the desired impedance control in high-speed designs.
Solder Wetting and Joint Reliability
Soldermask thickness plays a crucial role in the solder wetting process during PCB assembly. If the soldermask is too thin, it may not provide sufficient coverage over the copper traces, leading to solder bridging and short circuits. On the other hand, if the soldermask is too thick, it can hinder the flow of molten solder, resulting in poor solder joint formation and reduced reliability.
The ideal soldermask thickness should provide a balance between adequate insulation and optimal solder wetting. It should be thick enough to prevent solder bridging while still allowing the solder to flow freely and form reliable joints.
Thermal Management
Soldermask thickness can also impact the thermal management of a PCB. A thicker soldermask layer acts as a thermal insulator, reducing the heat transfer from the copper traces to the surrounding environment. This can be beneficial in applications where the PCB needs to withstand high temperatures or where thermal insulation is desired.
However, in applications that require efficient heat dissipation, a thicker soldermask may hinder the cooling process. In such cases, a thinner soldermask or the use of thermally conductive soldermask materials may be preferred.
Mechanical Protection
Soldermask provides mechanical protection to the copper traces, shielding them from damage during handling, assembly, and operation. A thicker soldermask layer offers better protection against scratches, abrasions, and impacts. This is particularly important for PCBs that are exposed to harsh environments or subjected to frequent handling.
However, excessively thick soldermask layers can also introduce mechanical stress on the PCB, especially during thermal cycling. The difference in the coefficient of thermal expansion (CTE) between the soldermask and the underlying copper and substrate materials can lead to stress buildup and potential delamination or cracking of the soldermask.
Manufacturing Considerations
The choice of soldermask thickness also has implications for the PCB manufacturing process. Thinner soldermask layers are generally easier to apply and cure, resulting in shorter production times and lower manufacturing costs. They also allow for finer feature resolution, which is essential for high-density PCB designs.
Thicker soldermask layers, on the other hand, may require longer curing times and more precise control over the application process. They can also limit the minimum achievable feature sizes, such as the width of soldermask openings and the spacing between pads.
FAQ
-
What is the most common soldermask thickness used in the PCB industry?
The most common soldermask thicknesses are 0.8 mils (20.3 µm) and 1.0 mils (25.4 µm). These thicknesses provide a good balance between insulation, solder wetting, and manufacturability for most PCB applications. -
Can soldermask thickness affect signal integrity in high-speed PCBs?
Yes, soldermask thickness can impact signal integrity in high-speed PCBs. Excessively thick soldermask layers can increase the capacitance between traces, leading to signal degradation and potential impedance mismatch. In high-speed designs, it is essential to carefully consider the soldermask thickness and its impact on signal propagation. -
How does soldermask thickness influence thermal management in PCBs?
Soldermask acts as a thermal insulator, and its thickness can affect heat transfer from the copper traces to the surrounding environment. A thicker soldermask layer provides better thermal insulation, which can be beneficial in applications where high temperatures need to be withstood. However, in applications requiring efficient heat dissipation, a thinner soldermask or thermally conductive soldermask materials may be preferred. -
What are the challenges associated with applying thick soldermask layers?
Applying thick soldermask layers can present several challenges in PCB manufacturing. Thicker layers may require longer curing times and more precise control over the application process. They can also limit the minimum achievable feature sizes, such as the width of soldermask openings and the spacing between pads. Additionally, thick soldermask layers can introduce mechanical stress on the PCB during thermal cycling, potentially leading to delamination or cracking. -
How can PCB designers choose the appropriate soldermask thickness for their application?
When selecting the appropriate soldermask thickness, PCB designers should consider factors such as the desired level of insulation, solder wetting requirements, thermal management needs, and mechanical protection. They should also take into account the manufacturing capabilities of their PCB fabricator and any specific design constraints, such as high-speed signal integrity or fine-pitch component placement. Consulting with the PCB manufacturer and following industry guidelines can help designers make informed decisions regarding soldermask thickness.
Conclusion
Soldermask thickness is a critical parameter in PCB manufacturing that significantly impacts the performance, reliability, and manufacturability of printed circuit boards. The choice of soldermask thickness involves balancing various factors, such as electrical insulation, solder wetting, thermal management, mechanical protection, and manufacturing considerations.
PCB designers must carefully evaluate their specific application requirements and consult with their PCB fabricator to determine the optimal soldermask thickness. By understanding the implications of soldermask thickness on PCB performance and manufacturability, designers can make informed decisions that ensure the reliability and functionality of their electronic products.
As PCB technology continues to advance, with increasing miniaturization and higher performance demands, the role of soldermask thickness becomes even more crucial. Ongoing research and development in soldermask materials and application techniques will further enhance the capabilities of PCBs and enable the creation of more sophisticated and reliable electronic devices.
Leave a Reply