Understanding PCB Tolerances and Their Importance
Printed Circuit Boards (PCBs) are the backbone of modern electronic devices, connecting various components and ensuring proper functionality. To guarantee the reliability and performance of these devices, it is crucial to maintain strict tolerances during the PCB manufacturing process. In this comprehensive article, we will delve into the world of PCB tolerances, exploring their significance, types, and the factors that influence them.
What are PCB Tolerances?
PCB tolerances refer to the acceptable variations in the dimensions, positions, and properties of the various features on a printed circuit board. These features include traces, pads, holes, and spacing between components. Tolerances are essential to ensure that the manufactured PCB matches the original design intent and functions as intended.
Why are PCB Tolerances Important?
Maintaining proper PCB tolerances is crucial for several reasons:
- Functionality: Accurate tolerances ensure that components fit correctly and the PCB functions as designed.
- Reliability: Tight tolerances minimize the risk of short circuits, open circuits, and other defects that can lead to device failure.
- Compatibility: Consistent tolerances allow for seamless integration of PCBs with other components and systems.
- Manufacturing efficiency: Well-defined tolerances streamline the production process, reducing errors and improving yield.
Types of PCB Tolerances
There are several types of tolerances that must be considered during PCB Design and manufacturing:
1. Dimensional Tolerances
Dimensional tolerances refer to the acceptable variations in the physical dimensions of the PCB and its features. These include:
- Board size and thickness
- Trace width and spacing
- Pad size and shape
- Hole size and position
The table below shows typical dimensional tolerances for various PCB features:
Feature | Tolerance |
---|---|
Board size | ±0.25 mm |
Board thickness | ±10% |
Trace width | ±0.05 mm |
Trace spacing | ±0.05 mm |
Pad size | ±0.05 mm |
Hole size | ±0.05 mm |
Hole position | ±0.1 mm |
2. Electrical Tolerances
Electrical tolerances deal with the acceptable variations in the electrical properties of the PCB, such as:
- Impedance
- Resistance
- Capacitance
- Inductance
Maintaining tight electrical tolerances is crucial for high-speed and high-frequency applications, where signal integrity is paramount.
3. Material Tolerances
Material tolerances refer to the acceptable variations in the properties of the materials used in PCB manufacturing, including:
- Substrate thickness and dielectric constant
- Copper foil thickness and conductivity
- Solder mask thickness and coverage
- Silkscreen thickness and adhesion
Consistent material properties ensure reliable performance and longevity of the PCB.
Factors Affecting PCB Tolerances
Several factors can influence the achievable tolerances in PCB manufacturing:
1. Manufacturing Process
The chosen manufacturing process, such as etching, drilling, or plating, can impact the achievable tolerances. Advanced processes like high-density interconnect (HDI) and microvias allow for tighter tolerances compared to traditional methods.
2. Material Selection
The materials used in PCB Fabrication, such as the substrate, copper foil, and solder mask, can affect the tolerances. High-quality materials with consistent properties enable tighter tolerances and better performance.
3. Design Complexity
The complexity of the PCB design, including the number of layers, component density, and feature sizes, can influence the achievable tolerances. More complex designs may require looser tolerances to ensure manufacturability and reliability.
4. Equipment and Tooling
The accuracy and precision of the equipment and tooling used in PCB manufacturing play a significant role in maintaining tight tolerances. Regular maintenance and calibration of equipment are essential to ensure consistent results.
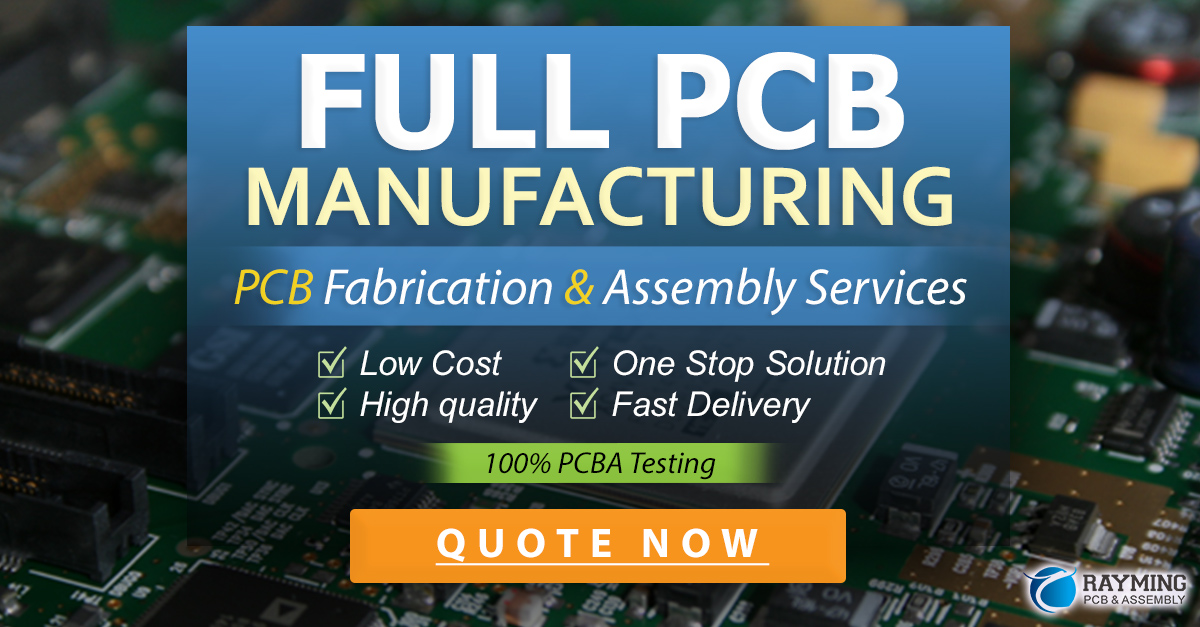
Designing for PCB Tolerances
To ensure the successful manufacture and performance of a PCB, designers must consider tolerances throughout the design process:
1. Choose Appropriate Feature Sizes
Select trace widths, pad sizes, and hole diameters that are compatible with the desired tolerances and manufacturing capabilities. Avoid pushing the limits of the manufacturing process to minimize the risk of defects.
2. Use Design for Manufacturing (DFM) Guidelines
Follow established DFM guidelines to ensure that the PCB design is optimized for manufacturability. These guidelines include recommendations for minimum feature sizes, spacing, and clearances.
3. Communicate with Manufacturers
Engage with PCB Manufacturers early in the design process to discuss the desired tolerances and any specific requirements. Manufacturers can provide valuable insights and recommendations based on their experience and capabilities.
4. Perform Design Reviews
Conduct thorough design reviews to identify and address any potential tolerance issues before finalizing the design. Use Design Rule Checks (DRC) and other validation tools to ensure that the design meets the specified tolerances.
Measuring and Verifying PCB Tolerances
To ensure that manufactured PCBs meet the specified tolerances, various measurement and verification techniques are employed:
1. Visual Inspection
Visual inspection is the first line of defense in identifying gross tolerance issues, such as misaligned components or incorrect feature sizes. Automated optical inspection (AOI) systems can quickly scan PCBs for visual defects.
2. Dimensional Measurement
Dimensional measurements are performed using tools like calipers, micrometers, and coordinate measuring machines (CMMs) to verify that the physical dimensions of the PCB and its features are within the specified tolerances.
3. Electrical Testing
Electrical testing, such as continuity and resistance measurements, is conducted to ensure that the PCB meets the specified electrical tolerances. Advanced techniques like time-domain reflectometry (TDR) can be used to characterize impedance and signal integrity.
4. Statistical Process Control (SPC)
SPC techniques are used to monitor the manufacturing process and identify any trends or variations in the achieved tolerances. By collecting and analyzing data on key process parameters, manufacturers can make necessary adjustments to maintain consistent quality.
Frequently Asked Questions (FAQ)
-
What is the importance of PCB tolerances in the manufacturing process?
PCB tolerances are critical in the manufacturing process because they ensure that the manufactured PCB matches the original design intent and functions as intended. Maintaining proper tolerances guarantees the reliability, performance, and compatibility of the PCB in the final electronic device. -
What are the consequences of not adhering to PCB tolerances?
Failing to adhere to PCB tolerances can lead to various issues, such as component misfit, short circuits, open circuits, and signal integrity problems. These issues can result in device malfunction, reduced reliability, and increased manufacturing costs due to rework or scrap. -
How can designers ensure that their PCB designs are within the specified tolerances?
Designers can ensure that their PCB designs are within the specified tolerances by following design for manufacturing (DFM) guidelines, choosing appropriate feature sizes, and communicating with manufacturers throughout the design process. Conducting thorough design reviews and using validation tools like design rule checks (DRC) can also help identify and address potential tolerance issues. -
What role does material selection play in achieving tight PCB tolerances?
Material selection plays a crucial role in achieving tight PCB tolerances. The properties of the materials used, such as the substrate, copper foil, and solder mask, can affect the dimensional stability and electrical performance of the PCB. Using high-quality materials with consistent properties enables tighter tolerances and better overall performance. -
How can PCB manufacturers ensure that their products meet the specified tolerances?
PCB manufacturers employ various techniques to ensure that their products meet the specified tolerances. These include visual inspection, dimensional measurement, electrical testing, and statistical process control (SPC). By monitoring the manufacturing process and making necessary adjustments based on collected data, manufacturers can maintain consistent quality and adherence to tolerances.
Conclusion
Tolerances on printed circuit boards play a vital role in ensuring the functionality, reliability, and compatibility of electronic devices. By understanding the types of tolerances, factors affecting them, and design considerations, PCB designers and manufacturers can work together to produce high-quality boards that meet the specified requirements.
Maintaining tight tolerances requires a combination of careful design, material selection, advanced manufacturing processes, and rigorous quality control measures. As electronic devices continue to become more complex and compact, the importance of PCB tolerances will only continue to grow.
By staying informed about the latest developments in PCB manufacturing and following best practices for tolerance management, designers and manufacturers can stay ahead of the curve and deliver innovative, reliable, and high-performing electronic products to the market.
Leave a Reply