What are PCB tolerances?
PCB Tolerances are the permissible deviations from the nominal or designed values for various parameters of a PCB. These parameters include the dimensions of the board, the size and placement of components, the width and spacing of traces, and the size of holes and vias. Tolerances are specified to ensure that the manufactured PCB will function as intended, despite the inevitable variations in the manufacturing process.
Why are PCB Tolerances Important?
PCB tolerances are crucial for several reasons:
-
Functionality: PCBs must function correctly within the specified tolerances. If the tolerances are too tight, it may be difficult or expensive to manufacture the PCB. If the tolerances are too loose, the PCB may not function as intended or may fail prematurely.
-
Compatibility: PCBs must be compatible with the components that will be mounted on them. If the tolerances for component placement or hole sizes are not met, it may be difficult or impossible to assemble the PCB correctly.
-
Reliability: PCBs must be reliable over their intended lifespan. If the tolerances are not met, the PCB may be subject to mechanical stress, thermal issues, or other problems that can reduce its reliability.
-
Cost: Tighter tolerances generally require more precise manufacturing processes, which can increase the cost of the PCB. It’s important to specify tolerances that are tight enough to ensure functionality and reliability, but not so tight that they unnecessarily increase the cost.
Types of PCB Tolerances
There are several types of tolerances that must be considered when designing and manufacturing PCBs. Some of the most important types include:
Dimensional Tolerances
Dimensional tolerances refer to the acceptable range of variation in the physical dimensions of the PCB. These include the length, width, and thickness of the board, as well as the size and location of holes, slots, and cutouts. Dimensional tolerances are typically specified in absolute units, such as millimeters or inches.
For example, a PCB with a nominal length of 100mm and a tolerance of ±0.5mm could have an actual length anywhere between 99.5mm and 100.5mm.
Positional Tolerances
Positional tolerances refer to the acceptable range of variation in the placement of components and features on the PCB. These include the location of component pads, holes, and vias, as well as the spacing between traces and components. Positional tolerances are typically specified in relative units, such as millimeters or mils (thousandths of an inch).
For example, a component pad with a nominal position of (50mm, 30mm) and a tolerance of ±0.1mm could be located anywhere within a 0.2mm x 0.2mm square centered at (50mm, 30mm).
Electrical Tolerances
Electrical tolerances refer to the acceptable range of variation in the electrical properties of the PCB and its components. These include the resistance of traces, the capacitance and inductance of components, and the Dielectric Constant of the PCB material. Electrical tolerances are typically specified as a percentage of the nominal value.
For example, a resistor with a nominal value of 1kΩ and a tolerance of ±5% could have an actual resistance anywhere between 950Ω and 1050Ω.
Manufacturing Process Tolerances
Manufacturing process tolerances refer to the acceptable range of variation in the parameters of the manufacturing processes used to produce the PCB. These include the thickness of the copper layers, the width of the traces, the size of the solder mask openings, and the registration between layers. Manufacturing process tolerances are typically specified in absolute units, such as micrometers or mils.
For example, a copper layer with a nominal thickness of 35µm and a tolerance of ±5µm could have an actual thickness anywhere between 30µm and 40µm.
Designing with PCB Tolerances in Mind
To ensure that your PCB will function correctly and reliably, it’s important to design with tolerances in mind. Here are some tips for designing PCBs with appropriate tolerances:
-
Understand the manufacturing capabilities of your PCB fabricator. Different fabricators have different capabilities and tolerances. Make sure you understand what your fabricator can achieve before you start your design.
-
Use standard tolerances wherever possible. Most PCB Fabricators have standard tolerances for common parameters such as board dimensions, hole sizes, and trace widths. Using standard tolerances can help reduce the cost and lead time of your PCB.
-
Avoid tight tolerances unless necessary. Tight tolerances can increase the cost and complexity of manufacturing. Only specify tight tolerances where they are necessary for the functionality or reliability of your PCB.
-
Use CAD tools with built-in tolerance checks. Many PCB Design software packages have built-in tools for checking your design against manufacturing tolerances. Use these tools to catch any potential problems early in the design process.
-
Communicate clearly with your PCB fabricator. Make sure your fabricator understands your requirements and tolerances. Provide clear documentation and drawings, and be available to answer any questions they may have.
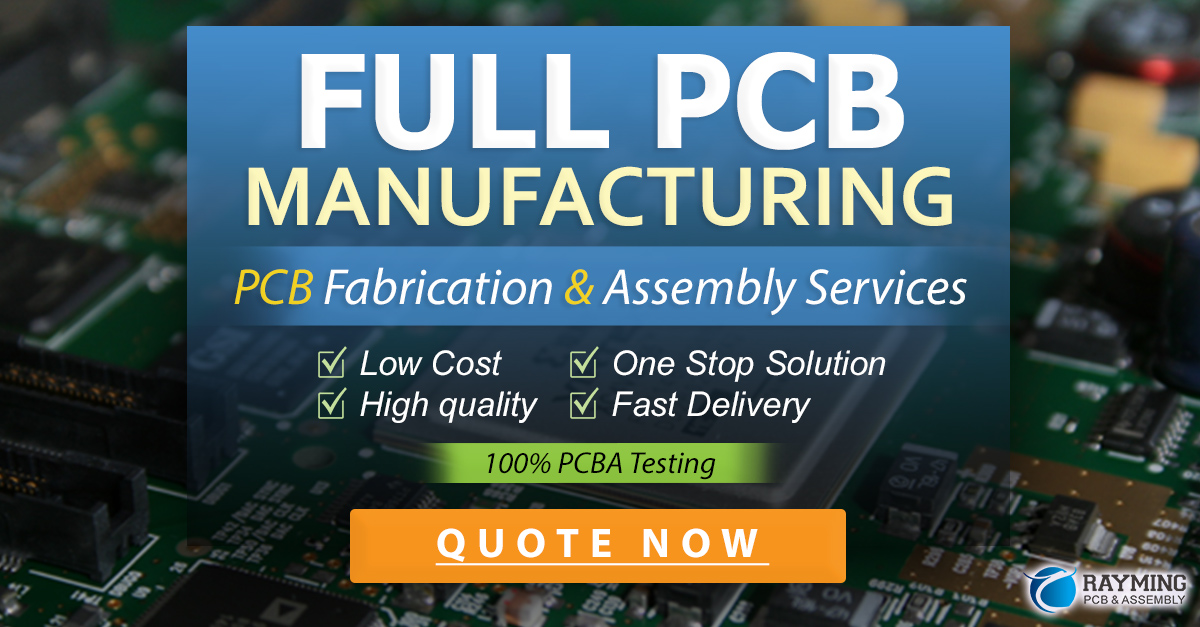
PCB Tolerances for Different Manufacturing Processes
Different PCB manufacturing processes have different capabilities and tolerances. Here are some typical tolerances for common PCB manufacturing processes:
Process | Typical Tolerances |
---|---|
Board Dimensions | ±0.15mm (6 mils) |
Hole Size | ±0.08mm (3 mils) |
Trace Width/Spacing | ±0.08mm (3 mils) |
Solder Mask Opening | ±0.10mm (4 mils) |
Silk Screen | ±0.15mm (6 mils) |
Note that these are just typical values, and actual tolerances may vary depending on the specific fabricator and process used.
FAQ
What happens if my PCB doesn’t meet the specified tolerances?
If your PCB doesn’t meet the specified tolerances, it may not function correctly or reliably. In some cases, the PCB may not be usable at all. If the tolerances are not met, you may need to rework or scrap the affected boards, which can be costly and time-consuming.
How can I ensure that my PCB meets the specified tolerances?
To ensure that your PCB meets the specified tolerances, you should:
- Design with tolerances in mind, using appropriate values for your manufacturing process.
- Use CAD tools with built-in tolerance checks to catch any potential problems early.
- Communicate clearly with your PCB fabricator and provide clear documentation and drawings.
- Consider using a reputable fabricator with a track record of meeting tight tolerances.
Can I use tighter tolerances to improve the performance of my PCB?
In some cases, using tighter tolerances can improve the performance of your PCB, particularly for high-speed or high-frequency designs. However, tighter tolerances can also increase the cost and complexity of manufacturing. It’s important to balance the benefits of tighter tolerances against the added cost and risk.
What are the most common problems caused by PCB tolerances?
Some of the most common problems caused by PCB tolerances include:
- Component misalignment or poor fit
- Incorrect hole sizes or locations
- Trace width or spacing violations
- Solder mask or silkscreen registration errors
- Electrical performance issues due to variations in trace impedance or component values
How do I choose the right tolerances for my PCB?
Choosing the right tolerances for your PCB depends on several factors, including:
- The functionality and performance requirements of your circuit
- The manufacturing capabilities of your PCB fabricator
- The cost and lead time constraints of your project
- The reliability and durability requirements of your end product
In general, it’s best to use standard tolerances wherever possible and only specify tight tolerances where necessary. It’s also a good idea to consult with your PCB fabricator early in the design process to ensure that your tolerances are achievable and cost-effective.
Conclusion
PCB tolerances are a critical aspect of PCB design and manufacturing. By understanding the types of tolerances, their importance, and how to design with them in mind, you can ensure that your PCBs will function correctly and reliably. When specifying tolerances, it’s important to balance the needs of your design with the capabilities of your manufacturing process and the cost and lead time constraints of your project. By working closely with your PCB fabricator and using appropriate design tools and techniques, you can achieve high-quality, reliable PCBs that meet your performance and cost goals.
Leave a Reply