Introduction to PCB Soldermask Testing
Printed Circuit Board (PCB) soldermask is a protective layer applied to the copper traces of a PCB to prevent oxidation, provide electrical insulation, and improve the overall reliability of the board. Proper soldermask application is crucial for ensuring the functionality and longevity of the PCB. This article will discuss various methods and techniques used to test PCB soldermask, ensuring its quality and adherence to industry standards.
Importance of PCB Soldermask Testing
PCB soldermask testing is essential for several reasons:
- Ensuring proper insulation: Soldermask acts as an insulating layer, preventing short circuits between adjacent traces and components.
- Protecting against oxidation: Exposed copper traces can oxidize, leading to reduced conductivity and potential signal integrity issues.
- Improving solderability: Soldermask helps to define the solderable areas on the PCB, ensuring proper solder joint formation during the assembly process.
- Enhancing durability: A well-applied soldermask layer protects the PCB from mechanical damage, moisture, and other environmental factors.
By conducting thorough PCB soldermask testing, manufacturers can identify and address any issues related to soldermask application, ultimately improving the quality and reliability of the final product.
Types of PCB Soldermask
Before delving into the testing methods, it’s important to understand the different types of soldermask available:
- Liquid Photoimageable Soldermask (LPISM): LPISM is the most common type of soldermask used in PCB manufacturing. It is applied as a liquid and then exposed to UV light through a photomask to create the desired pattern.
- Dry Film Soldermask (DFSM): DFSM is a solid film that is laminated onto the PCB surface and then exposed to UV light through a photomask. It offers a more uniform thickness compared to LPISM.
- Epoxy Liquid Soldermask: This type of soldermask is applied as a liquid and then cured using heat. It provides excellent chemical resistance and is often used in high-reliability applications.
The choice of soldermask type depends on factors such as the PCB’s intended application, manufacturing process, and cost considerations.
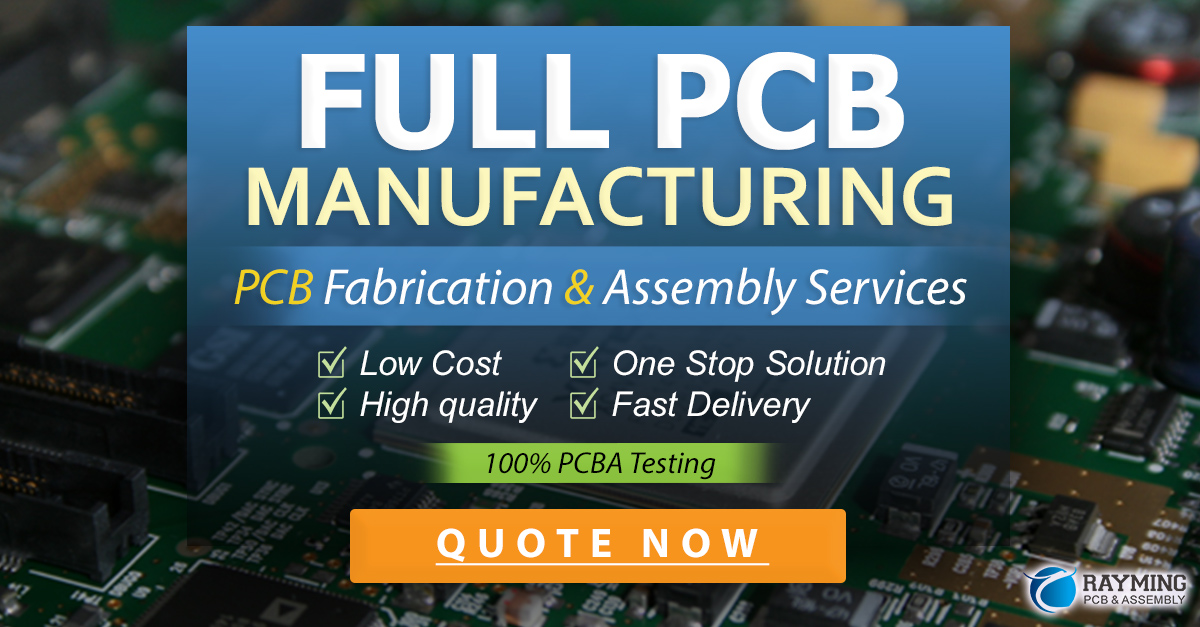
Visual Inspection
Visual inspection is the first step in evaluating the quality of the soldermask application. This can be done with the naked eye or using magnification tools such as a microscope or digital microscope.
Aspects to Examine During Visual Inspection
- Coverage: Check for any areas where the soldermask is missing, thin, or inconsistent.
- Registration: Verify that the soldermask is properly aligned with the copper traces and pads.
- Color consistency: Ensure that the soldermask color is uniform across the entire PCB surface.
- Surface defects: Look for any pinholes, bubbles, or other surface imperfections that could compromise the soldermask’s integrity.
Defect Type | Description | Potential Impact |
---|---|---|
Incomplete coverage | Areas where soldermask is missing or thin | Reduced insulation, increased risk of short circuits |
Misregistration | Soldermask not properly aligned with copper features | Exposed copper, potential solderability issues |
Color inconsistency | Variation in soldermask color across the PCB | Aesthetic concerns, may indicate process control issues |
Surface defects | Pinholes, bubbles, or other imperfections | Reduced protection, potential for contaminants to enter |
By conducting a thorough visual inspection, manufacturers can quickly identify any major soldermask defects and take corrective action before proceeding with further testing.
Automated Optical Inspection (AOI)
Automated Optical Inspection (AOI) systems can be used to supplement manual visual inspection, providing a more efficient and consistent method for detecting soldermask defects. AOI systems use high-resolution cameras and advanced image processing algorithms to scan the PCB surface and identify any anomalies.
Advantages of using AOI for soldermask inspection include:
- Speed: AOI systems can inspect PCBs much faster than manual methods, enabling higher throughput.
- Consistency: Automated inspection ensures a consistent level of scrutiny for every PCB, reducing the potential for human error.
- Traceability: AOI systems can generate detailed reports and images of any detected defects, providing a record for quality control and troubleshooting purposes.
Thickness Measurement
Measuring the thickness of the soldermask layer is crucial for ensuring proper insulation and protection of the PCB. There are several methods for measuring Soldermask Thickness, each with its own advantages and limitations.
Cross-Sectioning
Cross-sectioning involves cutting a small section of the PCB and examining the soldermask thickness under a microscope. This destructive method provides a direct measurement of the soldermask thickness at a specific location.
Advantages:
– Provides a precise measurement of soldermask thickness
– Allows for examination of the soldermask-copper interface
Limitations:
– Destructive method, rendering the sample unusable
– Only measures thickness at a single location
Eddy Current Testing
Eddy current testing is a non-destructive method that uses electromagnetic induction to measure the thickness of non-conductive coatings, such as soldermask, on conductive substrates like copper.
Advantages:
– Non-destructive, allowing for 100% inspection
– Fast and suitable for high-volume production
– Can measure thickness over a larger area compared to cross-sectioning
Limitations:
– Requires calibration standards with known soldermask thicknesses
– Sensitive to variations in the substrate’s conductivity
Optical Profiling
Optical profiling techniques, such as white light interferometry or confocal microscopy, use light to create a 3D map of the PCB surface, allowing for thickness measurements of the soldermask layer.
Advantages:
– Non-contact and non-destructive
– Provides high-resolution thickness measurements over a larger area
– Can also assess surface roughness and other topographical features
Limitations:
– Requires specialized equipment and trained operators
– May be slower than other methods, depending on the measurement area and resolution
Method | Destructive | Measurement Area | Speed | Accuracy |
---|---|---|---|---|
Cross-Sectioning | Yes | Single location | Slow | High |
Eddy Current Testing | No | Larger area | Fast | Medium |
Optical Profiling | No | Larger area | Medium | High |
The choice of thickness measurement method depends on factors such as the desired accuracy, inspection speed, and whether destructive testing is acceptable.
Adhesion Testing
Soldermask adhesion is critical for ensuring the long-term reliability of the PCB. Poor adhesion can lead to soldermask delamination, exposing the underlying copper traces to oxidation and potential damage. There are several methods for testing soldermask adhesion, each with its own merits.
Tape Test
The tape test is a simple and widely used method for evaluating soldermask adhesion. It involves applying a piece of adhesive tape to the soldermask surface, rubbing it to ensure good contact, and then rapidly pulling the tape off at a 90-degree angle. The amount of soldermask removed by the tape provides an indication of the adhesion quality.
Advantages:
– Quick and easy to perform
– Minimal equipment required
– Suitable for spot-checking adhesion during production
Limitations:
– Qualitative rather than quantitative results
– Adhesion quality may vary depending on the tape used and the operator’s technique
Cross-Hatch Test
The cross-hatch test involves using a specialized tool to create a grid pattern of cuts through the soldermask layer, down to the underlying copper. A piece of adhesive tape is then applied over the grid and pulled off at a 90-degree angle. The percentage of soldermask remaining in the grid provides a quantitative measure of adhesion quality.
Advantages:
– Provides a more quantitative assessment of adhesion compared to the tape test
– Standardized method (e.g., ISO 2409, ASTM D3359)
– Suitable for comparing adhesion performance between different soldermask types or process conditions
Limitations:
– Destructive method, rendering the tested area unusable
– Requires specialized cross-hatch cutting tools
Peel Test
The peel test involves using a tensile testing machine to measure the force required to peel the soldermask from the copper substrate at a controlled angle and speed. This method provides a quantitative measure of adhesion strength.
Advantages:
– Quantitative results in terms of peel strength (e.g., N/mm)
– Allows for comparison of adhesion performance between different soldermask materials or process conditions
– Standardized method (e.g., IPC-TM-650 2.4.28.1)
Limitations:
– Destructive method, requiring dedicated test coupons
– Requires specialized equipment and trained operators
Method | Destructive | Results | Equipment | Standardization |
---|---|---|---|---|
Tape Test | No | Qualitative | Minimal | Low |
Cross-Hatch Test | Yes | Semi-quantitative | Moderate | High |
Peel Test | Yes | Quantitative | Significant | High |
The choice of adhesion testing method depends on factors such as the desired level of quantification, available resources, and whether destructive testing is acceptable.
Chemical Resistance Testing
PCBs may be exposed to various chemicals during the assembly process or in their end-use environment. Therefore, it is essential to evaluate the soldermask’s resistance to these chemicals to ensure long-term reliability.
Common Chemicals for Testing
- Fluxes: Rosin-based, water-soluble, and no-clean fluxes used during soldering.
- Solvents: Isopropyl alcohol (IPA), acetone, and other cleaning solvents.
- Conformal coatings: Acrylic, silicone, and urethane-based coatings used for additional protection.
- Oils and lubricants: Cutting fluids, lubricants, and other oils encountered during manufacturing or end-use.
Test Methods
-
Immersion: Immerse soldermask-coated PCB samples in the chemical of interest for a specified duration and temperature. Evaluate the soldermask for any signs of degradation, such as blistering, softening, or color change.
-
Spot testing: Apply a small amount of the chemical directly onto the soldermask surface and allow it to dwell for a specified time. Evaluate the soldermask for any localized damage or degradation.
-
Exposure and thermal cycling: Expose soldermask-coated PCB samples to the chemical of interest, followed by thermal cycling to simulate accelerated aging. Evaluate the soldermask for any signs of degradation or loss of adhesion.
Chemical Class | Test Method | Exposure Time | Temperature | Evaluation Criteria |
---|---|---|---|---|
Fluxes | Immersion | 24-48 hours | Room temperature | Blistering, softening, color change |
Solvents | Spot testing | 15-30 minutes | Room temperature | Localized damage, degradation |
Conformal coatings | Exposure and thermal cycling | 24-48 hours | -40°C to +85°C | Degradation, loss of adhesion |
Oils and lubricants | Immersion | 24-48 hours | Room temperature | Blistering, softening, color change |
By conducting chemical resistance testing, manufacturers can ensure that the selected soldermask material is compatible with the chemicals encountered during the assembly process and in the end-use environment, ultimately improving the reliability of the PCB.
Thermal Shock Testing
Thermal shock testing evaluates the soldermask’s ability to withstand rapid temperature changes, which can occur during the soldering process or in the end-use environment. Thermal stresses can cause soldermask cracking, delamination, or other failures that compromise the PCB’s reliability.
Test Method
Thermal shock testing typically involves subjecting soldermask-coated PCB samples to alternating cycles of high and low temperatures, with rapid transitions between the two extremes. The test conditions are specified in industry standards, such as IPC-TM-650 2.6.7.2 or MIL-STD-202, Method 107.
A typical thermal shock test profile might include:
– High temperature: +125°C to +150°C
– Low temperature: -40°C to -55°C
– Dwell time at each temperature: 15-30 minutes
– Transition time between temperatures: <10 seconds
– Number of cycles: 100-1000
After the thermal shock testing, the soldermask is evaluated for any signs of degradation, such as cracking, blistering, or delamination. Electrical testing may also be performed to ensure that the PCB’s functionality has not been compromised.
Standard | High Temperature | Low Temperature | Dwell Time | Transition Time | Number of Cycles |
---|---|---|---|---|---|
IPC-TM-650 2.6.7.2 | +150°C | -65°C | 15 minutes | <10 seconds | 100 |
MIL-STD-202, Method 107 | +125°C | -55°C | 30 minutes | <10 seconds | 300 |
By conducting thermal shock testing, manufacturers can ensure that the soldermask material and application process are capable of withstanding the thermal stresses encountered during the soldering process and in the end-use environment, ultimately improving the reliability of the PCB.
Electrical Insulation Testing
Soldermask serves as an insulating layer between adjacent copper traces and components on the PCB. Electrical insulation testing is performed to ensure that the soldermask provides adequate insulation and prevents short circuits or leakage currents.
Dielectric Withstanding Voltage (DWV) Test
The DWV test involves applying a high voltage between adjacent copper traces or pads, with the soldermask acting as the insulating barrier. The test voltage is typically specified by industry standards, such as IPC-TM-650 2.5.7.1, and is based on the PCB’s intended application and voltage rating.
During the DWV test, the voltage is gradually increased to the specified level and held for a certain duration (e.g., 60 seconds). The soldermask is considered to have passed the test if there is no breakdown or flashover during the test duration.
Standard | Test Voltage | Duration |
---|---|---|
IPC-TM-650 2.5.7.1 | 500V + 2 × (Rated Voltage) | 60 seconds |
Insulation Resistance (IR) Test
The IR test measures the soldermask’s resistance to electrical leakage between adjacent copper traces or pads. A high-resistance meter, such as a megohmmeter, is used to apply a DC voltage between the conductors and measure the resulting current flow through the soldermask.
The test voltage and minimum acceptable resistance are typically specified by industry standards, such as IPC-TM-650 2.6.3.4. The soldermask is considered to have passed the test if the measured resistance exceeds the specified minimum value.
Standard | Test Voltage | Minimum Resistance |
---|---|---|
IPC-TM-650 2.6.3.4 | 500V DC | 500 MΩ |
By conducting electrical insulation testing, manufacturers can ensure that the soldermask provides adequate insulation between adjacent conductors, preventing short circuits and leakage currents that could compromise the PCB’s functionality and reliability.
Frequently Asked Questions (FAQ)
- What is the purpose of soldermask on a PCB?
Soldermask serves several purposes on a PCB, including: - Providing electrical insulation between adjacent copper traces and components
- Protecting the copper from oxidation and environmental damage
- Defining the solderable areas on the PCB for component attachment
-
Improving the PCB’s aesthetic appearance and legibility of markings
-
What are the most common types of soldermask used in PCB manufacturing?
The most common types of soldermask used in PCB manufacturing are: - Liquid Photoimageable Soldermask (LPISM): Applied as a liquid and patterned using UV exposure
- Dry Film Soldermask (DFSM): Applied as a solid film and patterned using UV exposure
-
Epoxy Liquid Soldermask: Applied as a liquid and cured using heat
-
What are the key factors to consider when selecting a soldermask for a PCB?
When selecting a soldermask for a PCB, key factors to consider include: - Electrical insulation properties
- Thermal and chemical resistance
- Adhesion to the copper substrate
- Compatibility with the PCB’s intended application and environment
-
Cost and ease of processing
-
How can soldermask defects impact the reliability of a PCB?
Soldermask defects can impact the reliability of a PCB in several ways: - Incomplete coverage or pinholes can lead to reduced insulation and increased risk of short circuits
- Poor adhes
Leave a Reply