Introduction to PCBA Testing
Printed Circuit Board Assembly (PCBA) is a crucial process in the manufacturing of electronic devices. It involves the assembly of various components onto a printed circuit board (PCB) to create a functional electronic circuit. To ensure the quality and reliability of the assembled PCBs, it is essential to perform thorough testing at different stages of the assembly process. In this article, we will discuss eight common PCBA testing methods and their importance in the manufacturing process.
Why is PCBA Testing Important?
PCBA testing is critical for several reasons:
-
Quality Assurance: Testing helps identify defects and issues in the assembled PCBs, ensuring that only high-quality products reach the end-users.
-
Reliability: Thorough testing ensures that the assembled PCBs can withstand various environmental conditions and perform reliably over their intended lifespan.
-
Cost Reduction: Identifying and fixing issues early in the manufacturing process helps reduce the cost of rework and minimize product returns.
-
Compliance: PCBA testing helps ensure that the assembled PCBs meet industry standards and regulatory requirements.
Eight Common PCBA Testing Methods
1. Visual Inspection
Visual inspection is the first step in PCBA testing. It involves examining the assembled PCB for any visible defects, such as incorrect component placement, solder bridges, or damaged components. This inspection can be performed manually by trained operators or using automated optical inspection (AOI) systems.
Manual Visual Inspection
In manual visual inspection, operators use magnifying glasses or microscopes to examine the PCB for defects. This method is suitable for low-volume production or prototypes where the cost of automated systems may not be justified.
Automated Optical Inspection (AOI)
AOI systems use high-resolution cameras and advanced image processing algorithms to inspect the assembled PCBs. These systems can quickly identify defects and provide detailed reports on the inspection results. AOI is ideal for high-volume production, as it can significantly reduce the time and cost of visual inspection.
2. In-Circuit Testing (ICT)
In-Circuit Testing (ICT) is a method used to test the functionality of individual components on the assembled PCB. It involves using a bed-of-nails fixture to make electrical contact with the PCB and test each component separately. ICT can identify issues such as incorrect component values, open or short circuits, and missing components.
Advantages of ICT
- Tests individual components thoroughly
- Can identify issues that may not be detected by other testing methods
- Provides detailed diagnostic information
Disadvantages of ICT
- Requires a custom bed-of-nails fixture for each PCB design
- May not be suitable for high-density or complex PCBs
- Can be time-consuming and expensive for high-volume production
3. Flying Probe Testing
Flying Probe Testing is an alternative to ICT that does not require a custom bed-of-nails fixture. Instead, it uses a set of movable probes to make electrical contact with the PCB and test individual components. Flying Probe Testing is more flexible than ICT and can be used for a wide range of PCB designs.
Advantages of Flying Probe Testing
- Does not require a custom fixture
- Can test a wide range of PCB designs
- Offers good test coverage and diagnostic capabilities
Disadvantages of Flying Probe Testing
- Slower than ICT for high-volume production
- May not be able to test all components due to limited access
- Can be more expensive than ICT for simple PCB designs
4. Boundary Scan Testing
Boundary Scan Testing, also known as JTAG testing, is a method used to test the interconnections between integrated circuits (ICs) on the assembled PCB. It involves using a special test access port (TAP) on the ICs to control and observe the inputs and outputs of each IC. Boundary Scan Testing can identify issues such as open or short circuits, stuck-at faults, and incorrect interconnections.
Advantages of Boundary Scan Testing
- Can test complex PCBs with high-density interconnections
- Does not require physical access to the PCB
- Can be used for in-system programming and debugging
Disadvantages of Boundary Scan Testing
- Requires ICs with built-in JTAG support
- May not be able to test all components on the PCB
- Requires specialized software and hardware tools
5. Functional Testing
Functional Testing is a method used to verify that the assembled PCB performs its intended functions correctly. It involves applying input signals to the PCB and measuring the output signals to ensure that they meet the specified requirements. Functional Testing can be performed manually or using automated test equipment (ATE).
Manual Functional Testing
In manual functional testing, operators use test equipment such as oscilloscopes, multimeters, and signal generators to apply input signals and measure output signals. This method is suitable for low-volume production or prototypes where the cost of automated systems may not be justified.
Automated Functional Testing
Automated functional testing uses ATE to apply input signals and measure output signals automatically. ATE can be programmed to perform a wide range of tests and can quickly test a large number of PCBs. Automated functional testing is ideal for high-volume production, as it can significantly reduce the time and cost of testing.
6. Burn-In Testing
Burn-In Testing is a method used to identify early failures in the assembled PCBs by subjecting them to elevated temperatures and voltages for an extended period. This testing helps identify components that may fail prematurely under normal operating conditions. Burn-In Testing is typically performed on a sample of the production run to ensure the reliability of the entire batch.
Advantages of Burn-In Testing
- Identifies early failures and weak components
- Improves the reliability of the assembled PCBs
- Reduces the risk of field failures and product returns
Disadvantages of Burn-In Testing
- Can be time-consuming and expensive
- May not be necessary for all types of PCBs
- Can potentially damage the PCBs if not performed correctly
7. X-Ray Inspection
X-Ray Inspection is a non-destructive testing method used to examine the internal structure of the assembled PCBs. It involves using X-rays to create a detailed image of the PCB, allowing the detection of hidden defects such as voids in solder joints, broken wire bonds, and misaligned components. X-Ray Inspection is particularly useful for inspecting high-density or multi-layer PCBs.
Advantages of X-Ray Inspection
- Can detect hidden defects that are not visible to the naked eye
- Non-destructive testing method
- Suitable for high-density and multi-layer PCBs
Disadvantages of X-Ray Inspection
- Requires specialized and expensive equipment
- May not be necessary for simple or low-density PCBs
- Requires trained operators to interpret the X-ray images
8. Environmental Testing
Environmental Testing is a method used to ensure that the assembled PCBs can withstand various environmental conditions that they may encounter during their lifetime. This testing includes subjecting the PCBs to extreme temperatures, humidity, vibration, and shock. Environmental Testing helps identify design or manufacturing weaknesses that may lead to premature failures in the field.
Common Environmental Tests
- Temperature Cycling: Exposing the PCBs to alternating high and low temperatures to simulate thermal stress.
- Humidity Testing: Subjecting the PCBs to high humidity levels to test their resistance to moisture.
- Vibration Testing: Exposing the PCBs to various vibration frequencies and amplitudes to simulate transportation and use conditions.
- Shock Testing: Subjecting the PCBs to sudden, high-intensity shocks to simulate accidental drops or impacts.
Advantages of Environmental Testing
- Ensures the reliability and durability of the assembled PCBs
- Identifies design or manufacturing weaknesses
- Reduces the risk of field failures and product returns
Disadvantages of Environmental Testing
- Can be time-consuming and expensive
- Requires specialized equipment and facilities
- May not be necessary for all types of PCBs
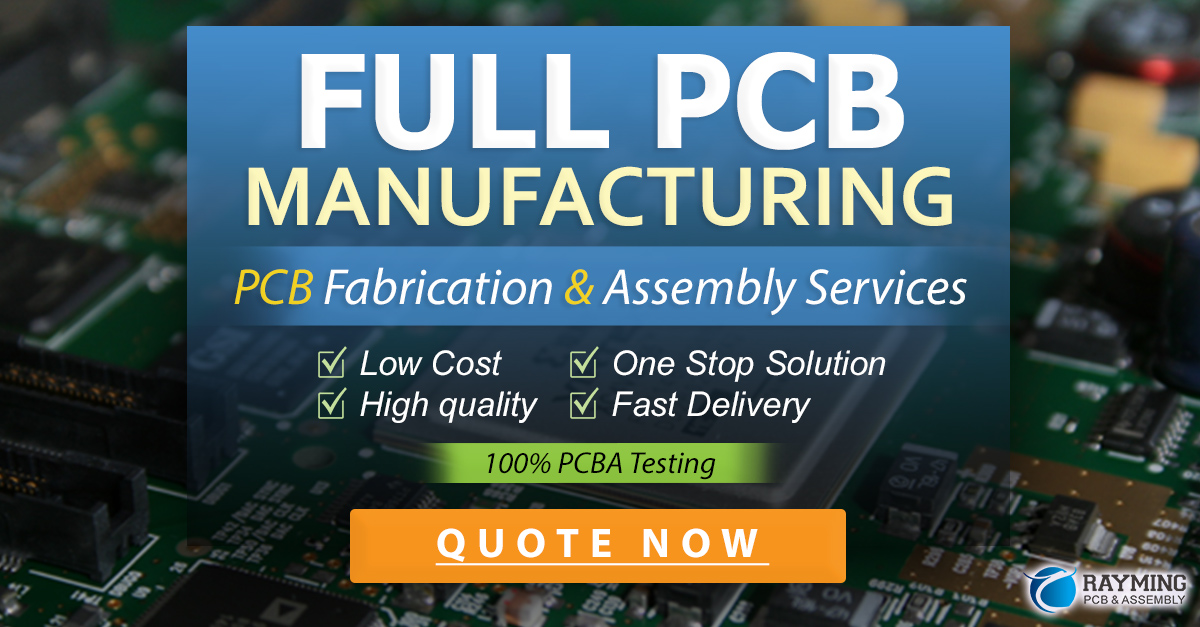
Frequently Asked Questions (FAQ)
1. What is the difference between ICT and Flying Probe Testing?
ICT requires a custom bed-of-nails fixture to make electrical contact with the PCB, while Flying Probe Testing uses movable probes. ICT is faster for high-volume production but may not be suitable for complex PCBs. Flying Probe Testing is more flexible but slower than ICT.
2. Can all components on a PCB be tested using Boundary Scan Testing?
No, Boundary Scan Testing can only test components that have built-in JTAG support. It may not be able to test all components on the PCB, such as passive components or non-JTAG ICs.
3. Is Burn-In Testing necessary for all types of PCBs?
Burn-In Testing may not be necessary for all types of PCBs, depending on their intended use and reliability requirements. It is typically performed on a sample of the production run to ensure the reliability of the entire batch.
4. What are the benefits of X-Ray Inspection?
X-Ray Inspection can detect hidden defects that are not visible to the naked eye, making it particularly useful for inspecting high-density or multi-layer PCBs. It is a non-destructive testing method that provides detailed images of the internal structure of the PCB.
5. How does Environmental Testing help improve PCB reliability?
Environmental Testing helps identify design or manufacturing weaknesses that may lead to premature failures in the field. By subjecting the PCBs to various environmental conditions, such as extreme temperatures, humidity, vibration, and shock, manufacturers can ensure that the assembled PCBs can withstand the conditions they may encounter during their lifetime.
Conclusion
PCBA testing is a critical aspect of the electronics manufacturing process, ensuring the quality, reliability, and performance of the assembled PCBs. The eight testing methods discussed in this article – Visual Inspection, In-Circuit Testing, Flying Probe Testing, Boundary Scan Testing, Functional Testing, Burn-In Testing, X-Ray Inspection, and Environmental Testing – each serve a specific purpose in identifying defects and verifying the functionality of the PCBs.
By implementing a comprehensive PCBA testing strategy that includes a combination of these methods, manufacturers can minimize the risk of product failures, reduce costs associated with rework and returns, and ultimately deliver high-quality electronic products to their customers.
As technology advances and PCBs become more complex, the importance of thorough PCBA testing will only continue to grow. Manufacturers that invest in the latest testing equipment, techniques, and trained personnel will be well-positioned to meet the evolving demands of the electronics industry and maintain a competitive edge in the market.
Leave a Reply