Introduction to PCB Soldermask
Printed Circuit Boards (PCBs) are essential components in modern electronic devices, ranging from smartphones and computers to industrial equipment and medical devices. During the PCB fabrication process, one crucial step is the application of soldermask, which serves multiple purposes. Soldermask, also known as solder resist or solder stop, is a thin layer of polymer applied to the copper traces of a PCB to protect them from oxidation, prevent solder bridges, and provide electrical insulation.
While soldermask comes in various colors, including red, blue, yellow, black, and white, green is by far the most commonly used color in PCB fabrication. In this article, we will explore the reasons behind the popularity of green soldermask and its advantages over other colors.
The History of Green Soldermask
The use of green soldermask dates back to the early days of PCB manufacturing. In the 1960s, when PCBs were first introduced, there was no standardized color for soldermask. However, as the industry grew and PCB fabrication techniques evolved, green emerged as the preferred choice for several reasons.
One of the primary reasons for the adoption of green soldermask was its compatibility with the materials and processes used in PCB fabrication. Green soldermask provided excellent adhesion to the copper traces and was resistant to the chemicals used in the manufacturing process. Additionally, green soldermask offered good contrast against the copper traces, making it easier for operators to inspect the boards for defects.
Advantages of Green Soldermask
1. Improved Visibility and Inspection
One of the most significant advantages of green soldermask is its high visibility, which facilitates easier inspection of the PCB during and after the fabrication process. The green color provides excellent contrast against the copper traces, making it easier for operators to spot any defects, such as solder bridges, incomplete coverage, or pinholes.
The table below compares the visibility of different soldermask colors against copper traces:
Soldermask Color | Contrast Against Copper | Visibility |
---|---|---|
Green | High | Excellent |
Red | Medium | Good |
Blue | Low | Fair |
Yellow | Low | Fair |
Black | High | Good |
White | High | Good |
As evident from the table, green soldermask offers the best visibility among all colors, making it the preferred choice for PCB inspection.
2. Enhanced Durability and Protection
Green soldermask is known for its excellent durability and protection against environmental factors. The polymer used in green soldermask is resistant to UV radiation, moisture, and chemicals, ensuring that the PCB remains protected throughout its lifespan.
Furthermore, green soldermask provides superior insulation properties, preventing short circuits and electrical leakage between adjacent traces. This is particularly important in high-density PCB designs, where the spacing between traces is minimal.
3. Compatibility with Various Manufacturing Processes
Green soldermask is compatible with a wide range of PCB manufacturing processes, including:
- Screen Printing
- Liquid Photoimageable (LPI) Soldermask
- Dry Film Soldermask
This versatility makes green soldermask a cost-effective choice for PCB manufacturers, as they can use the same material across different fabrication techniques without the need for specialized equipment or processes.
4. Aesthetic Appeal
While the primary purpose of soldermask is functional, the aesthetic appeal of green soldermask cannot be overlooked. The green color gives PCBs a professional and polished look, which is particularly important for consumer electronics and other products where visual appearance is a key consideration.
Moreover, the use of green soldermask has become so widespread that it is now synonymous with PCBs. When most people think of a PCB, they picture a green board with copper traces, making green soldermask a recognizable industry standard.
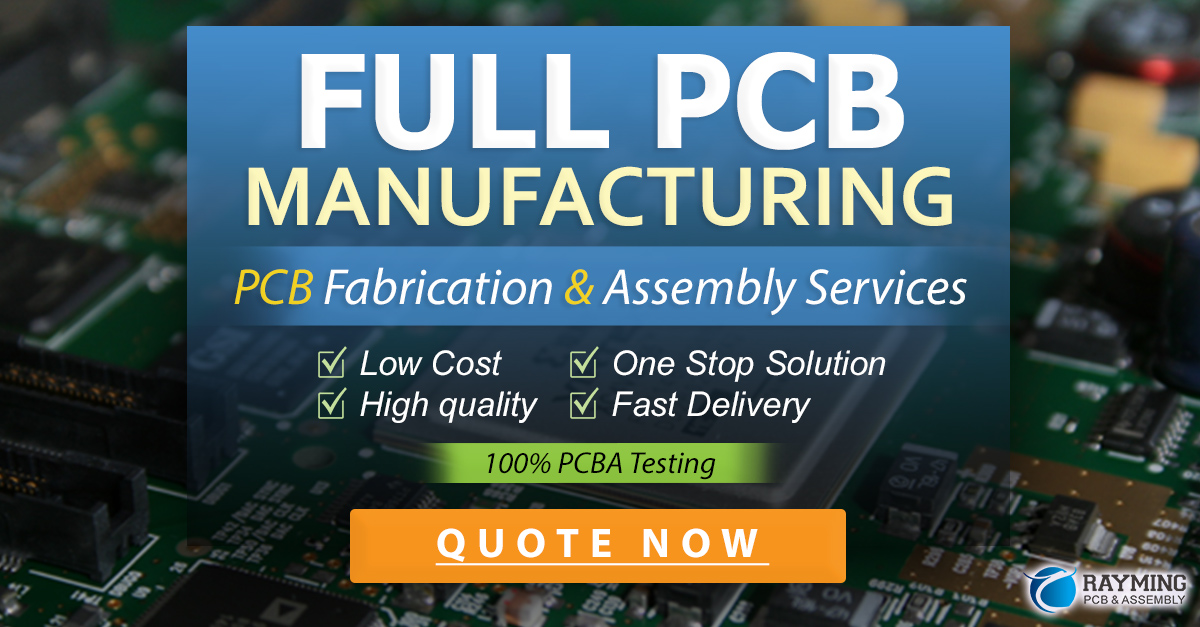
Other Soldermask Colors and Their Applications
Although green is the most common soldermask color, other colors are used in specific applications or for aesthetic purposes. Some examples include:
-
Red: Red soldermask is sometimes used in high-reliability applications, such as aerospace or military equipment, due to its high visibility and contrast against copper traces.
-
Blue: Blue soldermask is often used in PCBs for marine or outdoor applications, as it provides good UV resistance and blends well with the environment.
-
Black: Black soldermask is popular in high-end consumer electronics, such as smartphones and laptops, for its sleek and modern appearance.
-
White: White soldermask is used in LED lighting applications, as it reflects light better than other colors, improving the efficiency of the LED.
Frequently Asked Questions (FAQ)
-
Q: Is green soldermask more expensive than other colors?
A: No, green soldermask is not more expensive than other colors. In fact, due to its widespread use and compatibility with various manufacturing processes, green soldermask is often the most cost-effective option for PCB fabrication. -
Q: Can I specify a different soldermask color for my PCB?
A: Yes, most PCB manufacturers offer a range of soldermask colors to choose from. However, keep in mind that using a non-standard color may incur additional costs or longer lead times. -
Q: Does the soldermask color affect the performance of the PCB?
A: No, the soldermask color does not directly affect the electrical performance of the PCB. However, certain colors may offer better protection against environmental factors or improve the visibility of the board during inspection. -
Q: Is green soldermask environmentally friendly?
A: Modern green soldermask formulations are designed to be environmentally friendly and compliant with RoHS (Restriction of Hazardous Substances) regulations. However, it is essential to choose a reputable PCB manufacturer that adheres to strict environmental standards. -
Q: Can I mix different soldermask colors on the same PCB?
A: While it is possible to use multiple soldermask colors on a single PCB, it is not a common practice. Mixing colors may increase the complexity and cost of the fabrication process and is generally only done for specific applications or aesthetic purposes.
Conclusion
Green soldermask has become the industry standard for PCB fabrication due to its numerous advantages, including improved visibility, enhanced durability, compatibility with various manufacturing processes, and aesthetic appeal. The widespread use of green soldermask has made it a cost-effective and reliable choice for PCB manufacturers and designers alike.
While other soldermask colors are available for specific applications or aesthetic preferences, green remains the most popular choice for its proven performance and versatility. As PCB technology continues to evolve, it is likely that green soldermask will maintain its dominant position in the industry, ensuring the production of high-quality, reliable, and visually appealing printed circuit boards.
Leave a Reply