What is PCB Soldermask?
PCB soldermask, also known as solder resist or solder mask, is a thin layer of polymer applied to the copper traces of a printed circuit board (PCB). Its primary purpose is to protect the copper traces from oxidation, prevent solder bridges from forming between closely spaced pads, and provide electrical insulation.
Soldermask is typically applied using screen printing or photo imaging techniques. The most common colors for soldermask are green, red, blue, black, and white, although other colors are available for specific applications.
The Importance of Soldermask in PCB Manufacturing
Soldermask plays a crucial role in the PCB manufacturing process for several reasons:
-
Protection against oxidation: Copper traces on a PCB can easily oxidize when exposed to air, leading to reduced conductivity and potential electrical issues. Soldermask acts as a barrier, preventing oxidation and maintaining the integrity of the copper traces.
-
Preventing solder bridges: During the soldering process, molten solder can inadvertently connect adjacent pads or traces, causing short circuits. Soldermask covers the areas between pads and traces, preventing solder from adhering to unintended locations and minimizing the risk of solder bridges.
-
Electrical insulation: Soldermask provides electrical insulation between copper traces, preventing unintended current flow and reducing the risk of electrical shorts.
-
Improved aesthetics: Soldermask gives PCBs a clean, professional appearance by covering the exposed copper traces and providing a consistent color across the board.
-
Enhancing durability: Soldermask protects the PCB from physical damage, such as scratches and abrasions, which can occur during handling and assembly.
Common Problems with PCB Soldermask
Despite its importance in PCB manufacturing, soldermask can present several challenges and issues. Some of the most common problems include:
1. Pinholes
Pinholes are small, circular openings in the soldermask that expose the underlying copper. These defects can occur due to various reasons, such as:
- Contamination on the PCB surface before applying soldermask
- Improper curing of the soldermask
- Air bubbles trapped in the soldermask during application
Pinholes can lead to several issues, including:
- Oxidation of the exposed copper
- Solder bridges forming during the soldering process
- Reduced electrical insulation
Solutions for Pinholes
To minimize the occurrence of pinholes and address their effects, consider the following solutions:
-
Ensure proper cleaning: Thoroughly clean the PCB surface before applying soldermask to remove any contaminants that may cause pinholes.
-
Optimize soldermask application: Fine-tune the soldermask application process to minimize air bubbles and ensure even coverage. This may involve adjusting the screen printing or photo imaging parameters.
-
Adequate curing: Follow the manufacturer’s recommended curing times and temperatures to ensure the soldermask is fully cured and adheres properly to the PCB.
-
Touch-up and repair: For small pinholes, use a soldermask pen or brush to manually fill in the openings. For larger areas, consider applying a secondary soldermask layer.
2. Soldermask Adhesion Issues
Soldermask adhesion problems occur when the soldermask fails to bond properly to the PCB surface, leading to peeling, flaking, or lifting. Poor adhesion can be caused by:
- Inadequate surface preparation before applying soldermask
- Incompatibility between the soldermask and the PCB substrate material
- Improper curing of the soldermask
- Exposure to extreme temperatures or harsh chemicals
Soldermask adhesion issues can result in:
- Exposed copper traces, leading to oxidation and reduced conductivity
- Solder bridges forming during the soldering process
- Reduced protection against physical damage
Solutions for Soldermask Adhesion Issues
To improve soldermask adhesion and prevent related problems, consider these solutions:
-
Proper surface preparation: Ensure the PCB surface is clean, dry, and free of contaminants before applying soldermask. Use appropriate cleaning agents and techniques recommended by the soldermask manufacturer.
-
Compatibility check: Verify that the chosen soldermask is compatible with the PCB substrate material. Consult with the soldermask manufacturer or your PCB fabrication partner for guidance.
-
Optimized curing process: Follow the manufacturer’s recommended curing times and temperatures to ensure proper adhesion. Avoid over- or under-curing the soldermask.
-
Environmental control: Store and handle PCBs in a controlled environment to minimize exposure to extreme temperatures, humidity, and harsh chemicals that can degrade soldermask adhesion.
3. Soldermask Thickness Variations
Inconsistent soldermask thickness can lead to various issues, such as:
- Inadequate insulation between copper traces
- Difficulty in achieving proper solder joint formation
- Aesthetic inconsistencies
Thickness variations can occur due to:
- Uneven screen printing or photo imaging
- Incorrect soldermask viscosity
- Improper curing
Solutions for Soldermask Thickness Variations
To maintain consistent soldermask thickness and avoid related issues, consider these solutions:
-
Process optimization: Fine-tune the screen printing or photo imaging process to ensure even soldermask application. This may involve adjusting the screen mesh, emulsion thickness, or exposure time.
-
Viscosity control: Ensure the soldermask has the appropriate viscosity for the application method. Regularly check and adjust the viscosity according to the manufacturer’s recommendations.
-
Curing consistency: Maintain consistent curing times and temperatures across the entire PCB to ensure uniform soldermask thickness.
-
Thickness monitoring: Implement quality control measures to regularly monitor soldermask thickness using appropriate measurement tools, such as a micrometer or optical profilometer.
4. Soldermask Discoloration
Soldermask discoloration can occur over time due to exposure to various factors, such as:
- UV light
- High temperatures
- Harsh chemicals
Discoloration can lead to aesthetic issues and, in some cases, may indicate degradation of the soldermask’s protective properties.
Solutions for Soldermask Discoloration
To minimize soldermask discoloration and maintain its integrity, consider these solutions:
-
UV-resistant soldermask: For applications exposed to significant UV light, choose a UV-resistant soldermask formulation.
-
Thermal stability: Select a soldermask with good thermal stability to withstand high-temperature processes and operating conditions.
-
Chemical resistance: Opt for a soldermask that offers resistance to the specific chemicals used in your manufacturing process or end-use environment.
-
Proper storage: Store PCBs in a cool, dark place to minimize exposure to UV light and high temperatures that can accelerate discoloration.
5. Soldermask Alignment Issues
Misalignment of the soldermask layer relative to the copper traces can cause several problems, such as:
- Exposed copper on pads or traces
- Solder bridging between adjacent pads
- Difficulty in component placement and soldering
Soldermask alignment issues can arise from:
- Inaccurate screen printing or photo imaging setup
- Substrate distortion or shrinkage during processing
- Inadequate fiducial markers or alignment features
Solutions for Soldermask Alignment Issues
To ensure accurate soldermask alignment and prevent related problems, consider these solutions:
-
Proper equipment setup: Regularly calibrate and maintain screen printing or photo imaging equipment to ensure accurate alignment.
-
Substrate stability: Choose PCB substrate materials with minimal distortion or shrinkage during processing to maintain alignment accuracy.
-
Fiducial markers: Incorporate clear, easily detectable fiducial markers on the PCB design to aid in alignment during soldermask application.
-
Design considerations: Allow for adequate clearance between pads and traces to accommodate potential alignment variations without causing functional issues.
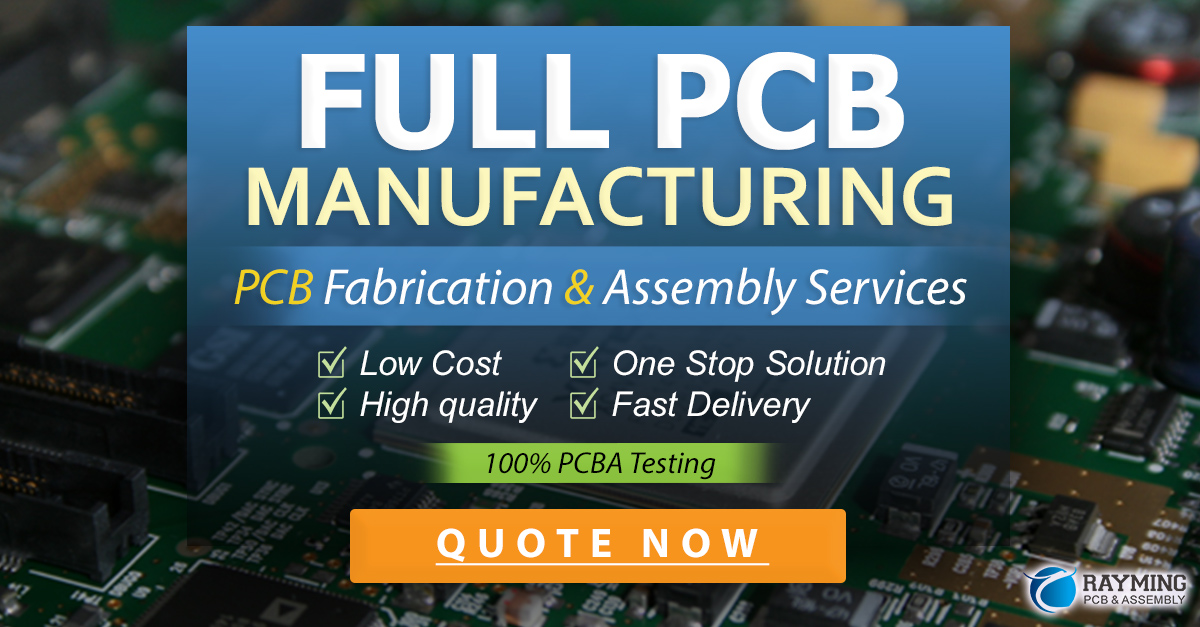
FAQ
1. What is the difference between liquid photoimageable (LPI) and dry film soldermask?
LPI soldermask is applied as a liquid using screen printing or spraying techniques and then cured using UV light. Dry film soldermask, on the other hand, is a solid film that is vacuum-laminated onto the PCB surface and then exposed and developed. LPI soldermask offers better resolution and finer pitch capabilities, while dry film soldermask provides better chemical resistance and is more suitable for high-reliability applications.
2. Can soldermask be removed from a PCB?
Yes, soldermask can be removed from a PCB using various methods, such as chemical stripping, laser ablation, or micro-abrasive blasting. However, removing soldermask can be a delicate process and may damage the underlying copper traces if not done carefully. It is essential to choose the appropriate method based on the specific soldermask material and PCB design.
3. How does soldermask affect the impedance of a PCB?
Soldermask has a dielectric constant that can impact the impedance of a PCB. The presence of soldermask on top of the copper traces can alter the effective dielectric constant of the PCB substrate, leading to changes in the characteristic impedance of the traces. To account for this effect, PCB designers must consider the soldermask’s dielectric constant and thickness when calculating and optimizing impedance-controlled traces.
4. What is the typical thickness of soldermask on a PCB?
The typical thickness of soldermask on a PCB ranges from 0.8 to 1.2 mils (20 to 30 microns). However, the actual thickness may vary depending on the specific soldermask material, application method, and PCB design requirements. Some high-performance PCBs may require thinner or thicker soldermask layers to meet specific electrical or environmental demands.
5. Can soldermask be used as a substitute for conformal coating?
While soldermask and conformal coating both provide protection for PCBs, they serve different purposes and are not interchangeable. Soldermask is primarily designed to protect the copper traces during the soldering process and provide electrical insulation. Conformal coating, on the other hand, is applied after the soldering process and offers additional protection against moisture, dust, chemicals, and other environmental factors. In some cases, PCBs may require both soldermask and conformal coating for optimal protection.
Conclusion
PCB soldermask is a critical component in the manufacturing of printed circuit boards, providing essential protection for copper traces, preventing solder bridging, and offering electrical insulation. However, soldermask is not without its challenges, and various problems can arise during the manufacturing process and the PCB’s lifecycle.
Common issues include pinholes, adhesion problems, thickness variations, discoloration, and alignment issues. By understanding these challenges and implementing appropriate solutions, such as proper surface preparation, process optimization, material selection, and quality control measures, PCB manufacturers can minimize the occurrence of soldermask-related problems and ensure the production of high-quality, reliable PCBs.
As PCB technology continues to advance, with increasing demands for miniaturization, high-speed performance, and enhanced reliability, the role of soldermask remains crucial. Ongoing research and development efforts in soldermask materials and application techniques will be essential to address the evolving needs of the electronics industry and enable the production of next-generation PCBs.
Problem | Causes | Effects | Solutions |
---|---|---|---|
Pinholes | – Contamination – Improper curing – Air bubbles |
– Oxidation – Solder bridges – Reduced insulation |
– Proper cleaning – Optimized application – Adequate curing – Touch-up and repair |
Adhesion Issues | – Inadequate surface preparation – Material incompatibility – Improper curing – Extreme temperatures or chemicals |
– Exposed copper – Solder bridges – Reduced protection |
– Proper surface preparation – Compatibility check – Optimized curing – Environmental control |
Thickness Variations | – Uneven application – Incorrect viscosity – Improper curing |
– Inadequate insulation – Soldering difficulties – Aesthetic issues |
– Process optimization – Viscosity control – Curing consistency – Thickness monitoring |
Discoloration | – UV light – High temperatures – Harsh chemicals |
– Aesthetic issues – Potential degradation |
– UV-resistant soldermask – Thermal stability – Chemical resistance – Proper storage |
Alignment Issues | – Inaccurate setup – Substrate distortion – Inadequate fiducials |
– Exposed copper – Solder bridging – Component placement difficulties |
– Proper equipment setup – Substrate stability – Fiducial markers – Design considerations |
Leave a Reply