Cost Savings and Efficiency
One of the primary drivers of Electronic Contract Manufacturing‘s popularity is the potential for significant cost savings and improved efficiency. By outsourcing production to a contract manufacturer, companies can:
- Avoid the high capital expenses associated with building and maintaining their own manufacturing facilities
- Leverage the contract manufacturer’s economies of scale and buying power for components and materials
- Benefit from the contract manufacturer’s expertise and streamlined processes to reduce production time and costs
Cost Factor | In-House Manufacturing | Contract Manufacturing |
---|---|---|
Capital expenses | High | Low |
Economies of scale | Limited | Significant |
Production efficiency | Variable | High |
Labor costs | Fixed | Flexible |
As the table illustrates, contract manufacturing offers several cost advantages over in-house production, making it an attractive option for companies looking to optimize their manufacturing spend.
Access to Expertise and Advanced Technology
Electronic contract manufacturers invest heavily in their workforce and technology to stay competitive in the market. By partnering with a contract manufacturer, OEMs gain access to:
- Highly skilled engineers and technicians with experience in the latest manufacturing techniques and quality control methods
- Advanced production equipment and automation technology that may be too expensive for individual companies to invest in
- Expertise in supply chain management, logistics, and regulatory compliance
This access to expertise and cutting-edge technology allows companies to innovate faster and bring high-quality products to market more quickly than they could on their own.
Case Study: Automotive Electronics Manufacturer
An automotive electronics manufacturer needed to quickly ramp up production of a new advanced driver assistance system (ADAS) to meet growing demand. By partnering with an electronic contract manufacturer, the company was able to:
- Leverage the contract manufacturer’s expertise in surface mount technology (SMT) and automated optical inspection (AOI) to ensure high-quality production
- Utilize the contract manufacturer’s existing relationships with component suppliers to secure favorable pricing and lead times
- Scale production rapidly to meet customer demand without investing in additional in-house capacity
As a result, the automotive electronics manufacturer was able to bring their new ADAS product to market 30% faster and at a 20% lower cost than if they had attempted to handle production in-house.
Flexibility and Scalability
Electronic contract manufacturing provides OEMs with greater flexibility and scalability compared to in-house production. Contract manufacturers can:
- Quickly adjust production volumes up or down in response to changes in demand
- Allocate resources across multiple projects to optimize capacity utilization
- Offer a range of manufacturing services, from printed circuit board assembly (PCBA) to complete box build, allowing OEMs to outsource as much or as little of the production process as needed
This flexibility and scalability is particularly valuable in today’s fast-paced, ever-changing electronics industry, where product life cycles are short and demand can fluctuate rapidly.
Adapting to Changing Market Conditions
The COVID-19 pandemic has highlighted the importance of flexibility and resilience in electronics manufacturing. Companies that relied on a single in-house production facility or a concentrated supply chain struggled to maintain operations when faced with lockdowns, component shortages, and logistical disruptions.
In contrast, OEMs that partnered with electronic contract manufacturers were often better positioned to adapt to these challenges. Contract manufacturers with geographically diversified facilities and multi-sourcing strategies for critical components were able to pivot production and keep supply chains moving, even in the face of unprecedented disruption.
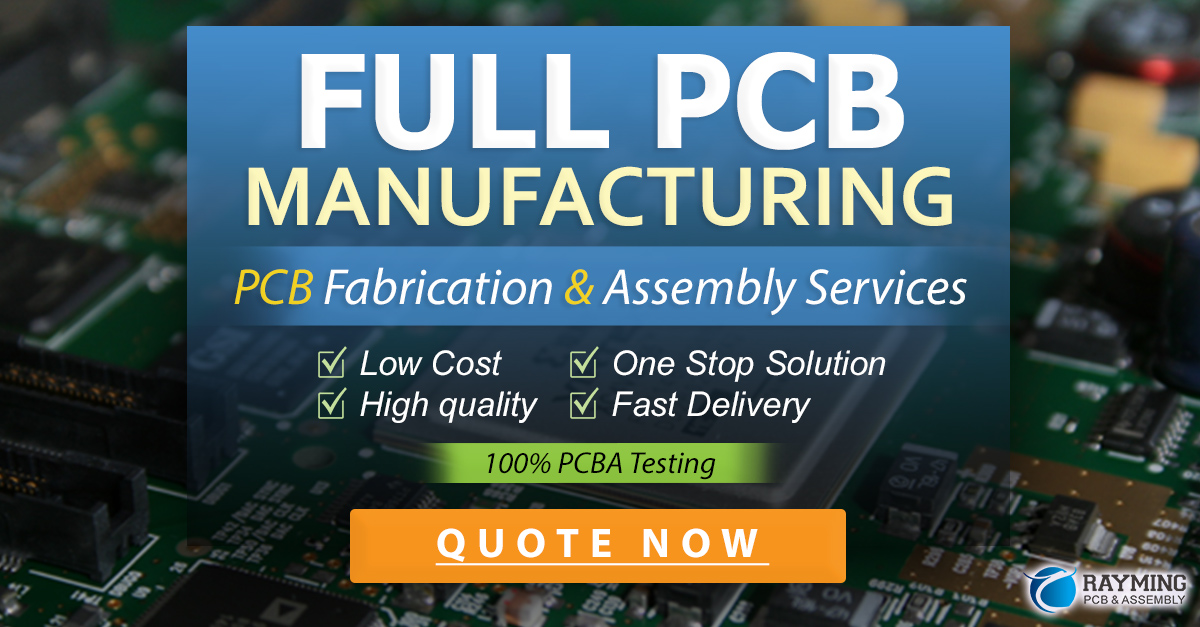
Focus on Core Competencies
By outsourcing manufacturing to a contract partner, companies can focus their resources and attention on their core competencies, such as:
- Research and development
- Product design and innovation
- Marketing and sales
- Customer service and support
This focus allows companies to differentiate themselves in the market and create sustainable competitive advantages, while leaving the complexities of manufacturing to a trusted partner.
Fostering Innovation
Freed from the day-to-day demands of manufacturing, companies can dedicate more time and resources to innovation and new product development. This is particularly important in the electronics industry, where rapid technological advancements and changing consumer preferences drive a constant need for new and improved products.
By leveraging the expertise and capabilities of an electronic contract manufacturer, companies can bring these innovative products to market faster and more efficiently, without sacrificing quality or performance.
Quality Assurance and Regulatory Compliance
Electronic contract manufacturers are experts in quality assurance and regulatory compliance, which are critical considerations in the electronics industry. They invest in:
- Rigorous quality control processes and testing procedures
- Certification to industry standards such as ISO 9001, ISO 13485, and AS9100
- Compliance with environmental and safety regulations, such as RoHS and REACH
- Traceability and documentation to support audits and regulatory inspections
By partnering with a contract manufacturer that adheres to these standards and regulations, OEMs can ensure that their products meet the highest levels of quality and safety, while minimizing their own compliance burden.
Standard | Description | Applicable Industries |
---|---|---|
ISO 9001 | Quality management systems | General manufacturing |
ISO 13485 | Quality management systems for medical devices | Medical devices |
AS9100 | Quality management systems for aerospace and defense | Aerospace and defense |
RoHS | Restriction of hazardous substances in electronics | Electronics manufacturing |
REACH | Registration, evaluation, and authorization of chemicals | Chemical and electronics manufacturing |
As the table shows, electronic contract manufacturers must adhere to a wide range of industry-specific standards and regulations to serve their diverse customer base.
Frequently Asked Questions (FAQ)
1. What types of products can electronic contract manufacturers produce?
Electronic contract manufacturers can produce a wide variety of products, including:
– Printed circuit board assemblies (PCBAs)
– Electronic modules and subassemblies
– Complete box build products, such as consumer electronics, medical devices, and industrial equipment
– Cables and Wire Harnesses
2. How do I choose the right electronic contract manufacturer for my project?
When selecting an electronic contract manufacturer, consider the following factors:
– Experience and expertise in your industry or product type
– Manufacturing capabilities and capacity
– Quality control processes and certifications
– Financial stability and business reputation
– Communication and customer service
3. What is the typical process for working with an electronic contract manufacturer?
The typical process for working with an electronic contract manufacturer includes:
1. Request for quotation (RFQ) and project scoping
2. Design for manufacturability (DFM) review and refinement
3. Prototyping and testing
4. Production planning and material procurement
5. Manufacturing and quality control
6. Packaging, labeling, and shipping
7. Post-production support and continuous improvement
4. How can I ensure the protection of my intellectual property when working with a contract manufacturer?
To protect your intellectual property, consider the following measures:
– Sign a non-disclosure agreement (NDA) with the contract manufacturer
– Implement contractual provisions that specify ownership of IP and confidentiality obligations
– Limit access to sensitive information and documents to only those who need it
– Conduct regular audits and inspections to ensure compliance with IP protection measures
5. What are the potential risks of outsourcing manufacturing to a contract partner?
While electronic contract manufacturing offers many benefits, there are also potential risks to consider, such as:
– Loss of control over the manufacturing process and quality
– Communication and cultural barriers, particularly when working with offshore manufacturers
– Increased supply chain complexity and potential for disruptions
– Intellectual property and data security concerns
To mitigate these risks, it’s essential to choose a reputable contract manufacturer, establish clear communication channels, and implement robust quality control and risk management processes.
Conclusion
The popularity of electronic contract manufacturing continues to grow as companies recognize the benefits of outsourcing production to specialized partners. From cost savings and increased efficiency to access to expertise and advanced technology, contract manufacturing offers a range of compelling advantages over in-house production.
As the electronics industry evolves and becomes increasingly competitive, the flexibility, scalability, and focus on core competencies that contract manufacturing enables will become even more critical to success. By partnering with the right electronic contract manufacturer, companies can position themselves to innovate faster, adapt to changing market conditions, and deliver high-quality products to their customers more efficiently than ever before.
Leave a Reply