Key Elements of a PCB fabrication drawing
A well-crafted PCB fabrication drawing should include the following elements:
- Board outline and dimensions
- Layer stackup information
- Material specifications
- Copper weights and trace widths
- Drill sizes and locations
- Solder mask and silkscreen requirements
- Surface finish specifications
- Mechanical features
- Fabrication notes and special requirements
- Revision history and approval signatures
Let’s dive deeper into each of these elements and their significance in the PCB manufacturing process.
1. Board Outline and Dimensions
The board outline and dimensions are the foundation of the PCB fabrication drawing. They define the physical size and shape of the board, including any cutouts, notches, or unique features. The dimensions should be clearly labeled, typically in millimeters or inches, and include tolerances where applicable.
When specifying board dimensions, consider the following:
- Overall board size (length, width, and thickness)
- Mounting hole locations and sizes
- Edge connector or castellated hole requirements
- Milling or routing features
- Panelization or array layout for multi-board fabrication
2. Layer Stackup Information
The layer stackup describes the arrangement of conductive and insulating layers within the PCB. It is crucial for determining the board’s electrical properties, such as impedance and signal integrity. The layer stackup should include the following information:
- Number of layers and their arrangement (e.g., signal, ground, power)
- Dielectric material type and thickness between layers
- Copper foil thickness for each layer
- Impedance requirements for controlled impedance designs
A clear and concise layer stackup table helps the manufacturer understand the board’s structure and ensures proper fabrication.
Example Layer Stackup Table:
Layer | Material | Thickness (mm) | Copper Weight (oz) |
---|---|---|---|
Top Copper | FR-4 | 0.035 | 1 |
Dielectric 1 | FR-4 | 0.2 | – |
Inner Copper 1 | FR-4 | 0.035 | 0.5 |
Dielectric 2 | FR-4 | 0.2 | – |
Inner Copper 2 | FR-4 | 0.035 | 0.5 |
Dielectric 3 | FR-4 | 0.2 | – |
Bottom Copper | FR-4 | 0.035 | 1 |
3. Material Specifications
The choice of materials used in a PCB can significantly impact its performance, reliability, and cost. The fabrication drawing should clearly specify the materials required for the board, including:
- Base material (e.g., FR-4, Rogers, Polyimide)
- Laminate and prepreg materials for multi-layer boards
- Copper foil type (e.g., electrodeposited, rolled annealed)
- Solder mask material and color
- Silkscreen ink color
- Conformal coating or other special materials
Providing detailed material specifications ensures that the manufacturer uses the appropriate materials to meet the design requirements.
4. Copper Weights and Trace Widths
Copper weights and trace widths are critical factors in determining the current-carrying capacity and impedance of the PCB traces. The fabrication drawing should specify the following:
- Copper weight for each layer (typically in ounces per square foot)
- Minimum and maximum trace widths and spacing
- Controlled impedance requirements (if applicable)
These specifications help the manufacturer set up their processes and ensure that the PCB meets the desired electrical characteristics.
Trace Width and Spacing Table Example:
Trace Type | Minimum Width (mm) | Nominal Width (mm) | Maximum Width (mm) | Minimum Spacing (mm) |
---|---|---|---|---|
Signal | 0.15 | 0.2 | 0.25 | 0.15 |
Power | 0.3 | 0.4 | 0.5 | 0.2 |
Ground | 0.3 | 0.4 | 0.5 | 0.2 |
5. Drill Sizes and Locations
Drilled holes are used for through-hole component mounting, vias, and mechanical features. The fabrication drawing must include detailed information about the drill sizes and locations, such as:
- Finished hole sizes and tolerances
- Plated or non-plated hole specifications
- Vias and micro-vias
- Blind and buried vias (if applicable)
- Mechanical holes (mounting, alignment, etc.)
A drill table or drill drawing can be used to communicate this information effectively to the manufacturer.
Example Drill Table:
Drill Size | Finished Hole Size (mm) | Tolerance (mm) | Plating | Quantity |
---|---|---|---|---|
D1 | 0.5 | ±0.05 | Plated | 250 |
D2 | 0.8 | ±0.05 | Plated | 100 |
D3 | 1.0 | ±0.05 | Non-plated | 4 |
D4 | 3.0 | ±0.1 | Non-plated | 4 |
6. Solder Mask and Silkscreen Requirements
Solder mask and silkscreen are essential for protecting the PCB and providing useful information for assembly and identification. The fabrication drawing should specify:
- Solder mask color and finish (matte or glossy)
- Solder mask apertures and clearances
- Silkscreen color and finish
- Silkscreen text, logos, and symbols
- Minimum silkscreen text size and line width
Clear communication of these requirements ensures that the final PCB has the desired appearance and protection.
7. Surface Finish Specifications
The surface finish on a PCB protects the exposed copper and enhances solderability. The fabrication drawing should clearly specify the required surface finish, such as:
- Hot Air Solder Leveling (HASL)
- Electroless Nickel Immersion Gold (ENIG)
- Immersion Silver (IAg)
- Immersion Tin (ISn)
- Organic Solderability Preservative (OSP)
Each surface finish has its advantages and limitations, and the choice depends on the specific application and assembly requirements.
8. Mechanical Features
In addition to electrical requirements, the fabrication drawing should include any mechanical features necessary for the PCB’s intended use, such as:
- Board thickness and tolerances
- Chamfers and bevels
- Slots, cutouts, and openings
- Countersinks and counterbores
- Edge connectors and castellations
- Stiffeners or supports
Clearly communicating these mechanical features helps ensure proper fit and function in the final application.
9. Fabrication Notes and Special Requirements
The fabrication drawing should include any additional notes or special requirements that are essential for the manufacturing process. These may include:
- Specific manufacturing standards (e.g., IPC-A-600, IPC-6012)
- Impedance control requirements
- Controlled dielectric thickness or parallelism
- Special testing or inspection requirements
- Packaging and shipping instructions
By providing clear and comprehensive fabrication notes, designers can minimize the risk of misinterpretation and ensure that the PCB is manufactured to their exact specifications.
10. Revision History and Approval Signatures
Finally, the fabrication drawing should include a revision history table and approval signatures. The revision history tracks changes made to the drawing, including the revision number, date, and a brief description of the changes. Approval signatures from the designer, engineer, and any other relevant stakeholders indicate that the drawing has been reviewed and approved for manufacturing.
Example Revision History Table:
Revision | Date | Description | Approved By |
---|---|---|---|
A | 2023-04-01 | Initial release | J. Smith |
B | 2023-04-15 | Added impedance control requirements | J. Smith |
C | 2023-04-30 | Updated drill sizes and quantities | J. Smith |
Frequently Asked Questions (FAQ)
-
What is the purpose of a PCB fabrication drawing?
A PCB fabrication drawing provides the manufacturer with all the necessary information to produce the printed circuit board according to the designer’s specifications. It includes details such as board dimensions, layer stackup, material requirements, and drilling information. -
What are the most critical elements of a PCB fabrication drawing?
The most critical elements of a PCB fabrication drawing are the board outline and dimensions, layer stackup information, drill sizes and locations, and material specifications. These elements form the foundation for the manufacturability and functionality of the PCB. -
How do I specify controlled impedance requirements in a fabrication drawing?
Controlled impedance requirements should be clearly stated in the fabrication drawing, typically in the layer stackup table or fabrication notes. Include the target impedance value, tolerance, and any specific materials or processes required to achieve the desired impedance. -
What is the difference between plated and non-plated holes in a PCB?
Plated holes have a conductive metal coating on the inside of the hole, allowing electrical connection between layers. Non-plated holes are used for mechanical purposes, such as mounting or alignment, and do not have a conductive coating. -
Why is the revision history important in a PCB fabrication drawing?
The revision history tracks changes made to the fabrication drawing over time. It helps designers, manufacturers, and other stakeholders identify the current version of the drawing and understand any modifications that have been made. This information is crucial for ensuring that the correct version of the PCB is being manufactured.
Conclusion
A well-crafted PCB fabrication drawing is essential for ensuring the successful manufacture of a printed circuit board. By including all the necessary information, such as board dimensions, layer stackup, material specifications, and drilling requirements, designers can communicate their intent clearly to the manufacturer. This minimizes the risk of errors and delays in the production process.
When creating a PCB fabrication drawing, it is essential to use clear and concise language, provide detailed tables and illustrations, and follow industry standards and best practices. By doing so, designers can streamline the manufacturing process, reduce costs, and ensure the highest quality of their PCBs.
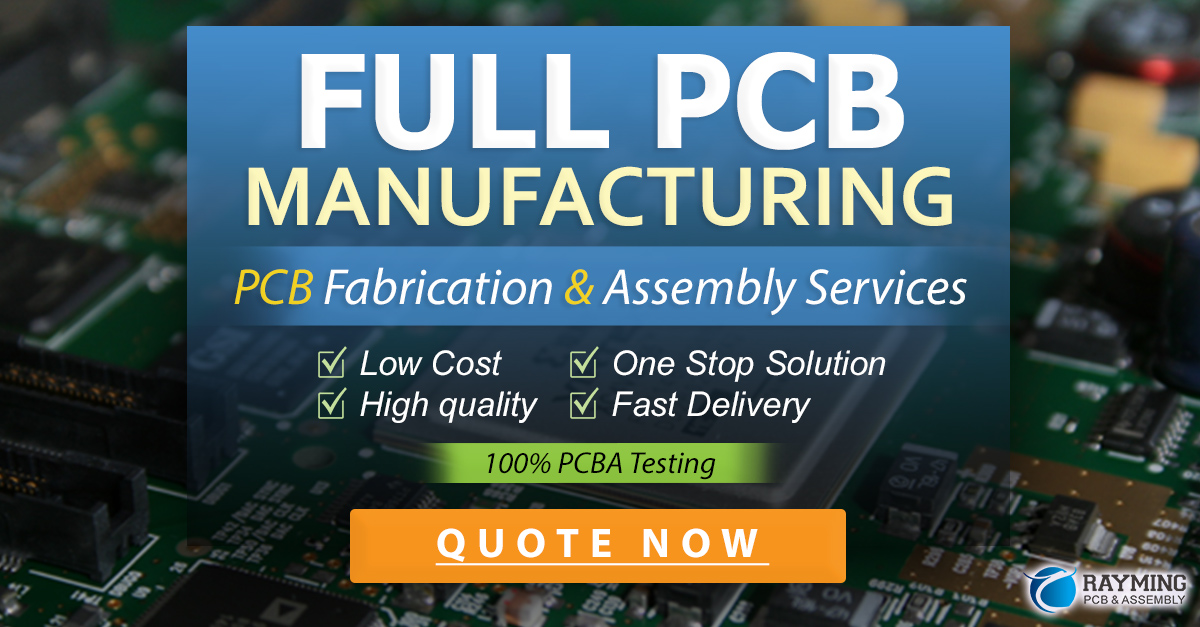
Leave a Reply