Understanding SMT Tombstoning
SMT (Surface Mount Technology) tombstoning is a manufacturing defect that occurs during the Reflow Soldering process of surface-mounted components. It is characterized by one end of a component lifting off the PCB (Printed Circuit Board) pad, while the other end remains soldered, causing the component to stand up like a tombstone. This issue can lead to poor electrical connections, reduced reliability, and even complete failure of the affected component and the entire PCB Assembly.
Causes of SMT Tombstoning
There are several factors that can contribute to the occurrence of SMT tombstoning:
-
Uneven heating: If one end of a component heats up faster than the other during the reflow process, it can cause the solder to melt and surface tension to pull the component upright.
-
Component size and shape: Smaller, lightweight components with a high center of gravity, such as capacitors and resistors, are more susceptible to tombstoning.
-
PCB pad design: Unequal pad sizes or improper placement can lead to uneven solder joint formation, increasing the risk of tombstoning.
-
Solder paste inconsistencies: Variations in solder paste volume, composition, or application can result in uneven solder joint formation and tombstoning.
-
Reflow profile issues: Incorrect reflow temperature profiles, such as rapid heating or cooling rates, can cause uneven solder melting and component lifting.
Preventing SMT Tombstoning
To minimize the occurrence of SMT tombstoning, several preventive measures can be implemented:
- PCB design optimization:
- Ensure equal pad sizes for component leads
- Maintain proper pad spacing and placement
-
Use solder thieves to balance solder distribution
-
Component selection:
- Choose components with a lower center of gravity
- Use larger, heavier components when possible
-
Consider alternative component packages less prone to tombstoning
-
Solder paste management:
- Ensure consistent solder paste volume and composition
- Use appropriate stencil design and thickness
-
Regularly maintain and calibrate solder paste printing equipment
-
Reflow profile optimization:
- Develop and implement a well-balanced reflow temperature profile
- Avoid rapid heating or cooling rates
- Monitor and control reflow oven performance
Detecting and Correcting SMT Tombstoning
Detection Methods
-
Visual inspection: Trained operators can identify tombstoned components through manual visual inspection using magnification tools.
-
Automated optical inspection (AOI): AOI systems use high-resolution cameras and advanced image processing algorithms to detect tombstoned components and other assembly defects.
-
X-ray inspection: For components with hidden leads or solder joints, X-ray inspection can be used to detect tombstoning and other internal defects.
Correction Techniques
-
Manual rework: Skilled technicians can manually reposition and resolder tombstoned components using Soldering Irons and other tools.
-
Localized reflow: Applying focused heat to the affected area using a hot air pencil or laser can allow the component to settle back onto the pads.
-
Component replacement: In some cases, the tombstoned component may need to be removed and replaced with a new one to ensure proper functionality and reliability.
Case Studies and Examples
Case Study 1: Tombstoning in Chip Resistors
A manufacturing facility experienced a high rate of tombstoning in their 0402 chip resistors. Upon investigation, it was found that the solder paste printing process was inconsistent, resulting in uneven solder deposits on the pads. By adjusting the stencil design and improving the solder paste printing process control, the tombstoning rate was significantly reduced.
Case Study 2: Pad Design Optimization
An electronics company was facing tombstoning issues with their small outline transistor (SOT) components. Analysis of the PCB design revealed that the pad sizes for the component leads were unequal, leading to uneven solder joint formation. By redesigning the pads to have equal sizes and optimizing the placement, the tombstoning issue was resolved, and the overall assembly yield improved.
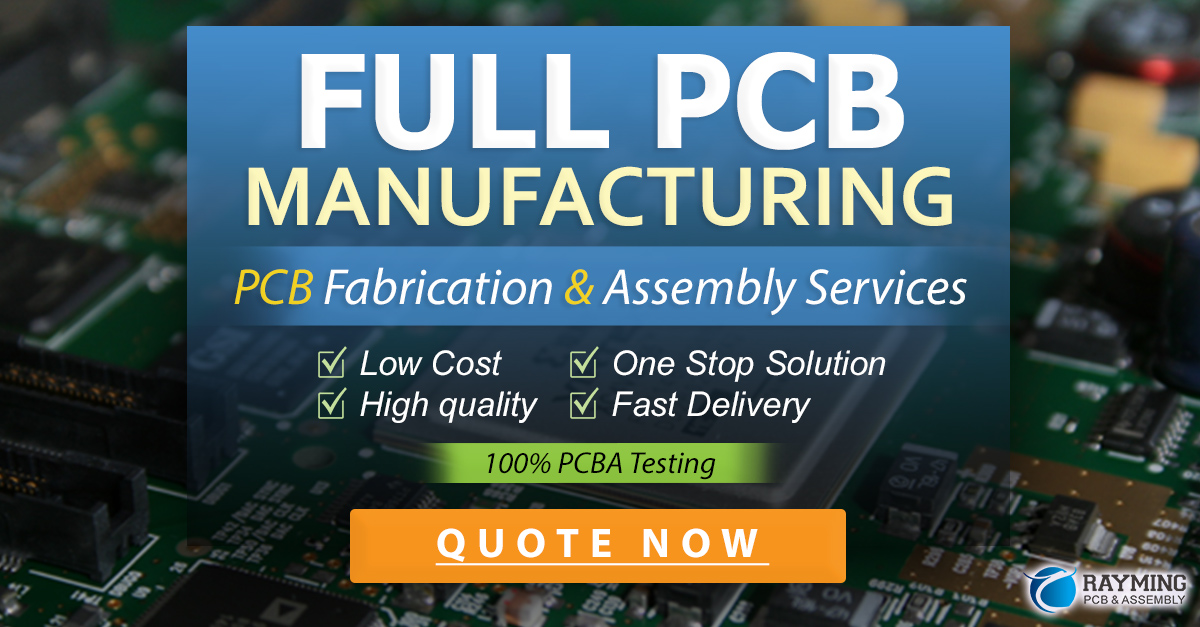
FAQ
-
What is the main cause of SMT tombstoning?
The main cause of SMT tombstoning is uneven heating of the component leads during the reflow soldering process, which can be influenced by factors such as PCB pad design, solder paste inconsistencies, and improper reflow profiles. -
Can tombstoning be completely eliminated in SMT Assembly?
While it may not be possible to completely eliminate tombstoning, implementing proper PCB design, component selection, solder paste management, and reflow profile optimization can significantly reduce its occurrence. -
What types of components are most susceptible to tombstoning?
Small, lightweight components with a high center of gravity, such as chip resistors, capacitors, and small outline transistors (SOTs), are more prone to tombstoning due to their size and shape. -
How can automated optical inspection (AOI) help detect tombstoning?
AOI systems use high-resolution cameras and advanced image processing algorithms to identify tombstoned components and other assembly defects, enabling faster and more accurate detection compared to manual visual inspection. -
Is it always necessary to replace tombstoned components?
In some cases, tombstoned components can be repositioned and resoldered using manual rework techniques or localized reflow. However, if the component or solder joint integrity is compromised, replacement may be necessary to ensure proper functionality and reliability.
Conclusion
SMT tombstoning is a common manufacturing defect that can adversely affect the quality, reliability, and performance of surface-mounted electronic assemblies. Understanding the causes, prevention techniques, and detection methods is crucial for minimizing the occurrence of tombstoning and improving overall assembly yields.
By implementing best practices in PCB design, component selection, solder paste management, and reflow profile optimization, manufacturers can significantly reduce the risk of tombstoning. Additionally, utilizing advanced inspection technologies and rework techniques can help identify and correct tombstoned components, ensuring the production of high-quality electronic products.
As the electronics industry continues to evolve, with smaller components and more complex assemblies, addressing SMT tombstoning will remain a critical aspect of manufacturing process control and quality assurance.
Factor | Impact on Tombstoning |
---|---|
Uneven heating | High |
Component size and shape | High (smaller, lightweight components more prone) |
PCB pad design | High (unequal pad sizes or improper placement) |
Solder paste inconsistencies | High (variations in volume, composition, or application) |
Reflow profile issues | High (incorrect temperature profiles, rapid heating/cooling) |
Table 1: Factors influencing SMT tombstoning and their impact levels.
By understanding and addressing these factors, manufacturers can effectively combat SMT tombstoning and improve the quality and reliability of their electronic assemblies.
Leave a Reply