The Importance of PCB Design in Electronics
PCB design plays a crucial role in the development of electronic devices. A well-designed PCB ensures:
- Proper functionality of the electronic circuit
- Optimal performance and reliability
- Efficient use of space and resources
- Ease of manufacturing and assembly
- Compliance with industry standards and regulations
Key Aspects of PCB Design
-
Schematic Design: The first step in PCB design is creating a schematic diagram that represents the electrical connections and components of the circuit. This is done using Electronic Design Automation (EDA) software.
-
Component Selection: Choosing the right components for the PCB is essential. Factors such as functionality, size, power requirements, and cost are considered when selecting components.
-
PCB Layout: Once the schematic is finalized, the PCB layout process begins. This involves placing components on the board and routing the traces to connect them according to the schematic.
-
Design Rule Check (DRC): DRC is performed to ensure that the PCB layout adheres to the design rules specified by the manufacturer. These rules include minimum trace width, spacing between components, and hole sizes, among others.
-
Gerber File Generation: After the PCB layout is complete and has passed the DRC, Gerber files are generated. These files contain the necessary information for manufacturing the PCB, including the copper layers, solder mask, and silkscreen.
PCB Design Software and Tools
There are various software tools available for PCB design, ranging from free and open-source to professional-grade commercial solutions. Some popular PCB design software include:
- Altium Designer
- KiCad
- Eagle
- OrCAD
- Cadence Allegro
These tools offer features such as schematic capture, PCB layout, 3D visualization, and simulation capabilities to aid in the design process.
PCB Manufacturing Process
Once the PCB design is complete, and the Gerber files are generated, the manufacturing process begins. The typical steps in PCB manufacturing include:
-
PCB Fabrication: The PCB is fabricated using a multi-step process that involves printing the copper traces, drilling holes, and applying solder mask and silkscreen.
-
Component Placement: The components are placed on the PCB using automated pick-and-place machines or manual assembly, depending on the complexity and quantity of the boards.
-
Soldering: The components are soldered onto the PCB using methods such as wave soldering, reflow soldering, or hand soldering.
-
Inspection and Testing: The assembled PCBs undergo various inspections and tests to ensure proper functionality and quality. This may include visual inspection, automated optical inspection (AOI), and functional testing.
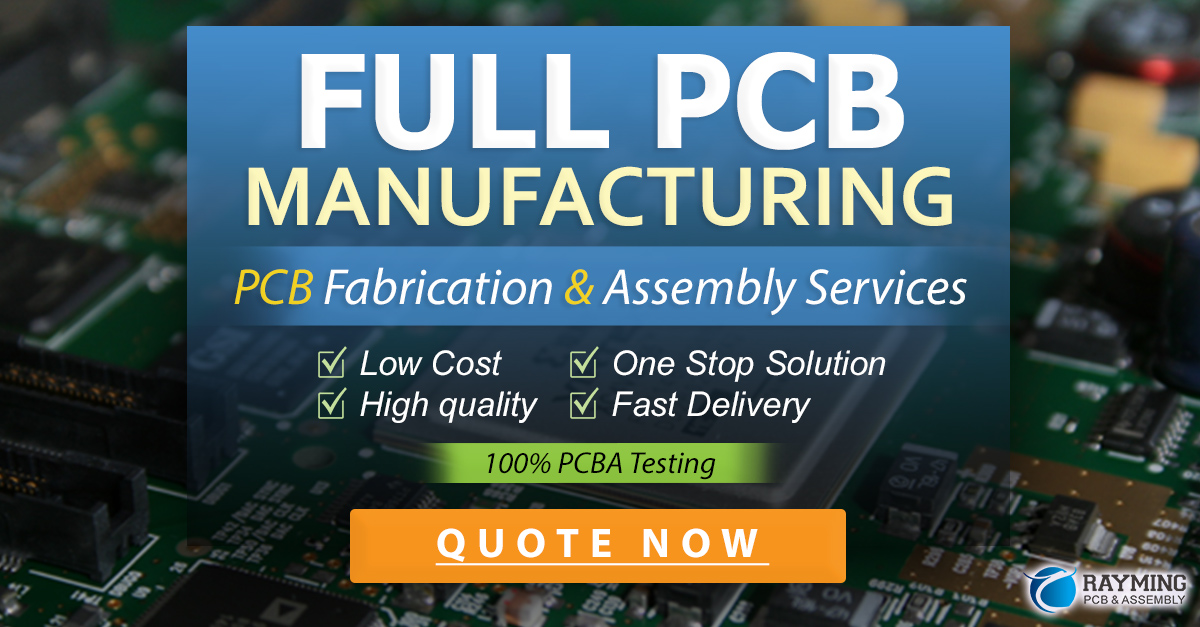
PCB Design Considerations
When designing a PCB, several factors need to be considered to ensure optimal performance and reliability:
Signal Integrity
Signal integrity refers to the quality of the electrical signals transmitted through the PCB. Factors such as trace impedance, crosstalk, and electromagnetic interference (EMI) can affect signal integrity. Proper PCB layout techniques, such as careful routing, use of ground planes, and appropriate trace widths, can help maintain signal integrity.
Power Integrity
Power integrity involves ensuring that the components on the PCB receive a stable and clean power supply. This includes proper power distribution, decoupling capacitors placement, and minimizing voltage drops across the board. Proper power integrity helps prevent issues such as voltage fluctuations, noise, and ground bounce.
Thermal Management
Electronic components generate heat during operation, and excessive heat can lead to performance degradation and failure. Effective thermal management is crucial in PCB design. This can be achieved through proper component placement, use of heatsinks, and designing adequate cooling solutions such as fans or ventilation.
Electromagnetic Compatibility (EMC)
EMC refers to the ability of an electronic device to operate properly in its electromagnetic environment without causing or being affected by electromagnetic interference. PCB design plays a significant role in ensuring EMC compliance. Techniques such as proper grounding, shielding, and filtering can help mitigate EMI and improve EMC performance.
Advanced PCB Design Techniques
As electronic systems become more complex and demanding, advanced PCB design techniques are employed to meet the challenges:
High-Speed PCB Design
High-speed PCB design deals with the challenges associated with high-frequency signals and fast data rates. It involves techniques such as impedance matching, differential signaling, and careful routing to minimize signal integrity issues and ensure reliable high-speed communication.
Flexible and Rigid-Flex PCBs
Flexible and Rigid-Flex PCBs offer unique advantages in terms of space savings, weight reduction, and improved reliability. These PCBs can conform to various shapes and allow for three-dimensional packaging. Designing flexible and rigid-flex PCBs requires special considerations for material selection, bend radius, and strain relief.
HDI (High-Density Interconnect) PCBs
HDI PCBs feature higher wiring density and smaller component sizes compared to traditional PCBs. They enable the integration of more functionality into a smaller form factor. HDI PCB Design involves the use of microvias, buried and blind vias, and fine-pitch components.
PCB Stackup Design
PCB stackup refers to the arrangement of copper layers and dielectric materials in a multi-layer PCB. Proper stackup design is essential for achieving the desired electrical performance, signal integrity, and manufacturability. It involves considering factors such as layer order, dielectric thickness, and impedance control.
PCB Design Best Practices
To ensure a successful PCB design, following best practices is crucial:
-
Plan and organize the design: Start with a clear understanding of the requirements, create a detailed schematic, and plan the component placement and routing strategy.
-
Follow design rules: Adhere to the manufacturer’s design rules and guidelines to ensure manufacturability and reliability.
-
Use a consistent naming convention: Adopt a consistent naming convention for components, nets, and layers to improve readability and collaboration.
-
Keep the design modular: Break down complex designs into smaller, modular sections for easier management and troubleshooting.
-
Perform thorough reviews and checks: Regularly review the design, perform DRC checks, and verify the functionality through simulations and prototypes.
-
Document the design: Maintain clear and comprehensive documentation, including schematics, BOMs (Bill of Materials), and assembly instructions.
-
Collaborate with manufacturers: Work closely with PCB manufacturers and assembly providers to ensure smooth production and address any potential issues early in the design process.
Frequently Asked Questions (FAQ)
-
What is the difference between a schematic and a PCB layout?
A schematic represents the electrical connections and components of a circuit, while a PCB layout shows the physical placement and routing of those components on the actual printed circuit board. -
What is the purpose of a ground plane in PCB design?
A ground plane is a large area of copper on a PCB layer that serves as a common reference point for electrical signals. It helps improve signal integrity, reduces noise, and provides a low-impedance return path for currents. -
What are vias in PCB design?
Vias are small holes drilled through the PCB layers to create electrical connections between different layers. They allow signals to travel from one layer to another, enabling more complex routing and compact designs. -
What is the difference between surface mount (SMT) and through-hole (THT) components?
SMT components are mounted directly on the surface of the PCB, while THT components have leads that are inserted through holes in the PCB and soldered on the opposite side. SMT components are generally smaller and allow for higher density designs, while THT components offer stronger mechanical connections. -
What is the purpose of a solder mask on a PCB?
A solder mask is a protective layer applied to the copper traces on a PCB. It helps prevent accidental short circuits during soldering, provides insulation between adjacent traces, and protects the copper from oxidation and environmental factors.
Conclusion
PCB design and layout is a critical aspect of electronic product development. It involves the creation of a functional and efficient electronic circuit on a printed circuit board, taking into account various factors such as component placement, routing, signal integrity, power integrity, thermal management, and electromagnetic compatibility.
By following best practices, using appropriate tools and techniques, and collaborating with manufacturers, designers can create high-quality PCBs that meet the required specifications and ensure reliable performance. As technology advances and electronic systems become more complex, staying updated with the latest PCB design trends and techniques is essential for success in the field.
Aspect | Description |
---|---|
Schematic Design | Creating a schematic diagram that represents the electrical connections and components of the circuit |
Component Selection | Choosing the right components based on functionality, size, power requirements, and cost |
PCB Layout | Placing components on the board and routing traces to connect them according to the schematic |
Design Rule Check (DRC) | Ensuring the PCB layout adheres to the manufacturer’s design rules |
Gerber File Generation | Generating files that contain the necessary information for manufacturing the PCB |
By understanding the fundamentals of PCB design and layout, electronics engineers and enthusiasts can create robust and efficient electronic devices that power our modern world.
Leave a Reply