How Does the ENIG Process Work?
The ENIG process consists of several steps that ensure a uniform and reliable surface finish on the copper pads of a PCB. The process is as follows:
-
Cleaning: The PCB is thoroughly cleaned to remove any contaminants, such as dirt, grease, or oxides, from the copper surface. This step is crucial to ensure proper adhesion of the subsequent layers.
-
Microetching: The copper surface is then treated with a microetch solution to create a slightly roughened surface, which enhances the adhesion of the nickel layer.
-
Electroless Nickel Plating: The PCB is immersed in an electroless nickel plating bath, where a thin layer of nickel (typically 3-6 µm) is deposited on the copper surface through an autocatalytic chemical reaction. The nickel layer acts as a barrier between the copper and the gold layer, preventing the formation of intermetallic compounds that can lead to brittle solder joints.
-
Immersion Gold Plating: After the nickel plating, the PCB is immersed in an immersion gold plating bath, where a thin layer of gold (typically 0.05-0.2 µm) is deposited on the nickel surface through a displacement reaction. The gold layer provides excellent solderability and protects the nickel layer from oxidation.
-
Rinsing and Drying: Finally, the PCB is rinsed with deionized water and dried to remove any residual chemicals from the surface.
The entire ENIG process is carefully controlled to ensure consistent and reliable results. The thickness of the nickel and gold layers is critical to the performance of the surface finish and is typically monitored using X-ray fluorescence (XRF) or other thickness measurement techniques.
Advantages of ENIG Surface Finish
ENIG offers several advantages over other surface finishes, making it a popular choice for many applications:
-
Excellent Solderability: The gold layer provides excellent solderability, ensuring reliable and strong solder joints. The gold surface is also resistant to oxidation, which helps maintain its solderability over time.
-
Durability: The nickel layer provides a hard and durable surface that can withstand multiple soldering cycles and mechanical stresses. This makes ENIG suitable for applications that require frequent repairs or rework.
-
Corrosion Resistance: The nickel layer acts as a barrier between the copper and the environment, protecting the copper from corrosion. This is particularly important in harsh environments or applications where the PCB may be exposed to moisture or other corrosive agents.
-
Compatibility with Various Soldering Methods: ENIG is compatible with a wide range of soldering methods, including Wave Soldering, reflow soldering, and hand soldering. This versatility makes it suitable for a variety of manufacturing processes.
-
Flatness: The ENIG process results in a flat and uniform surface, which is essential for fine-pitch components and high-density interconnects. A flat surface ensures proper contact between the component leads and the PCB Pads, reducing the risk of open circuits or poor solder joints.
-
Shelf Life: ENIG has a long shelf life compared to other surface finishes, such as OSP (Organic Solderability Preservative). The gold layer protects the nickel from oxidation, allowing the PCB to be stored for extended periods without degradation of solderability.
Disadvantages of ENIG Surface Finish
While ENIG offers many benefits, it also has some limitations and potential drawbacks:
-
Cost: ENIG is more expensive than other surface finishes, such as HASL (Hot Air Solder Leveling) or OSP, due to the use of gold and the multiple processing steps involved. This can be a significant consideration for cost-sensitive applications.
-
Black Pad: One of the main concerns with ENIG is the potential for “black pad” formation. Black pad is a phenomenon where the nickel layer becomes brittle and separates from the copper surface, leading to poor solder joint strength and reliability. This issue is typically associated with excessive phosphorus content in the electroless nickel plating bath or improper process control.
-
Solder Mask Adhesion: In some cases, the ENIG process can lead to poor adhesion between the solder mask and the copper surface. This can result in solder mask lifting or peeling, which can expose the underlying copper and lead to corrosion or short circuits.
-
Gold Embrittlement: If the gold layer is too thick (>0.2 µm), it can lead to gold embrittlement of the solder joint. During soldering, the gold can dissolve into the solder and form brittle intermetallic compounds, which can reduce the mechanical strength of the solder joint.
-
Nickel Corrosion: In rare cases, the nickel layer can be susceptible to corrosion if exposed to certain aggressive chemicals or environments. This can lead to the degradation of the surface finish and compromise the reliability of the solder joint.
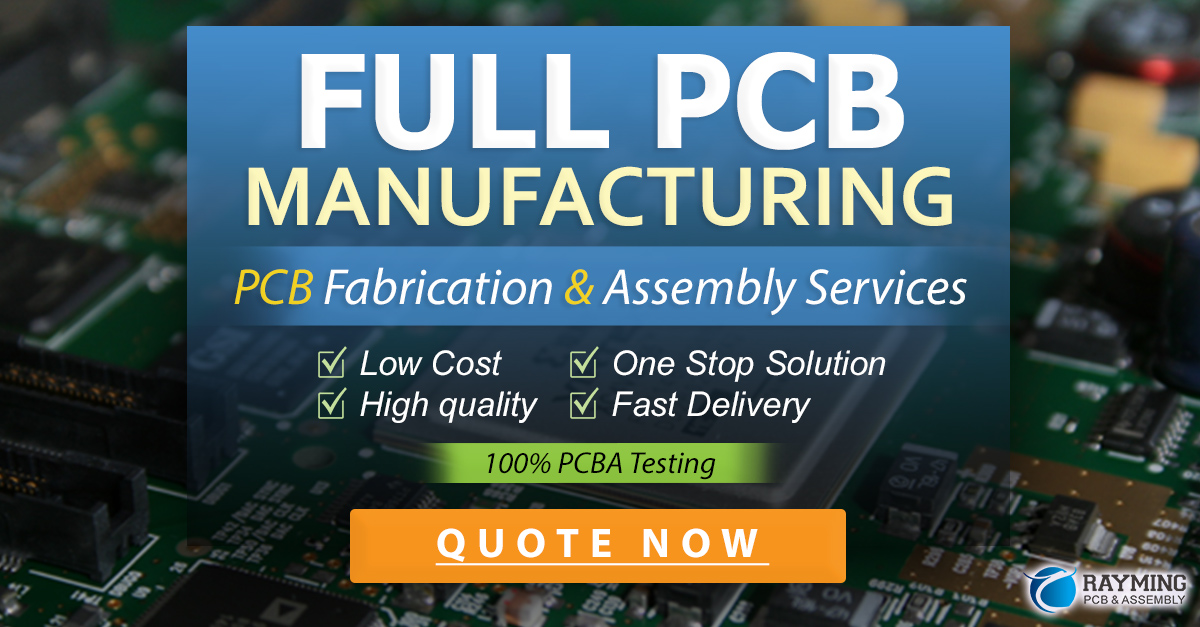
Applications of ENIG Surface Finish
ENIG is widely used in various industries and applications where high reliability, durability, and solderability are critical. Some common applications include:
-
Telecommunications: ENIG is often used in High-Frequency PCBs for telecommunications equipment, such as routers, switches, and base stations. The excellent solderability and flatness of ENIG make it suitable for fine-pitch components and high-speed signal integrity.
-
Aerospace and Defense: In aerospace and defense applications, PCBs are often exposed to harsh environments and extreme temperature variations. ENIG’s corrosion resistance and durability make it a reliable choice for these demanding applications.
-
Medical Devices: Medical devices require high reliability and long-term stability to ensure patient safety. ENIG’s excellent solderability and resistance to oxidation make it a popular choice for medical electronics, such as implantable devices and diagnostic equipment.
-
Automotive Electronics: As vehicles incorporate more electronic systems, the demand for reliable and durable PCBs increases. ENIG’s compatibility with various soldering methods and its ability to withstand multiple soldering cycles make it suitable for automotive electronics.
-
Industrial Control Systems: Industrial control systems often operate in harsh environments and require reliable and long-lasting PCBs. ENIG’s corrosion resistance and durability make it a good choice for applications such as process control, automation, and monitoring systems.
ENIG vs. Other Surface Finishes
ENIG is one of several surface finishes available for PCBs. Each surface finish has its own advantages and limitations, and the choice of surface finish depends on the specific requirements of the application. Some common surface finishes and their comparison to ENIG are:
Surface Finish | Advantages | Disadvantages | Comparison to ENIG |
---|---|---|---|
HASL | – Low cost – Good solderability – Suitable for most applications |
– Uneven surface – Thermal shock to PCB – Limited fine-pitch capability |
– ENIG has better flatness and fine-pitch capability – ENIG has longer shelf life |
OSP | – Low cost – Flat surface – Suitable for fine-pitch components |
– Limited shelf life – Sensitive to handling and storage conditions |
– ENIG has better solderability and longer shelf life – ENIG is more durable |
Immersion Tin | – Low cost – Good solderability – Suitable for press-fit connectors |
– Prone to whisker growth – Limited shelf life |
– ENIG has better shelf life and no whisker growth issues – ENIG is more expensive |
Immersion Silver | – Flat surface – Good solderability – Suitable for fine-pitch components |
– Limited shelf life – Prone to tarnishing and corrosion |
– ENIG has better corrosion resistance and longer shelf life – ENIG is more expensive |
The choice between ENIG and other surface finishes depends on factors such as cost, application requirements, soldering methods, and PCB design. In general, ENIG is preferred when high reliability, solderability, and durability are critical, while other surface finishes may be more suitable for cost-sensitive or less demanding applications.
Frequently Asked Questions (FAQ)
-
Q: What is the typical thickness of the nickel and gold layers in ENIG?
A: The typical thickness of the nickel layer in ENIG is 3-6 µm, while the gold layer is usually 0.05-0.2 µm thick. -
Q: Can ENIG be used for both through-hole and surface mount components?
A: Yes, ENIG is suitable for both through-hole and surface mount components. Its excellent solderability and flatness make it compatible with various component types and soldering methods. -
Q: How does ENIG compare to HASL in terms of cost?
A: ENIG is generally more expensive than HASL due to the use of gold and the multiple processing steps involved. However, the higher cost is often justified by ENIG’s superior performance and reliability in demanding applications. -
Q: What is black pad, and how can it be prevented in ENIG?
A: Black pad is a defect in ENIG where the nickel layer becomes brittle and separates from the copper surface, leading to poor solder joint strength. It can be prevented by maintaining proper process control, including monitoring the phosphorus content in the electroless nickel plating bath and ensuring appropriate plating times and temperatures. -
Q: Is ENIG suitable for high-frequency PCBs?
A: Yes, ENIG is often used in high-frequency PCBs due to its excellent flatness and ability to accommodate fine-pitch components. The flat surface of ENIG helps maintain signal integrity and reduces the risk of signal reflections or distortions.
Conclusion
ENIG (Electroless Nickel Immersion Gold) is a widely used surface finish in the PCB industry, offering excellent solderability, durability, and corrosion resistance. The process involves the deposition of a thin nickel layer followed by a thin gold layer on the copper pads of a PCB. ENIG’s advantages, such as compatibility with various soldering methods, flatness, and long shelf life, make it a popular choice for high-reliability applications in telecommunications, aerospace, medical devices, and automotive electronics.
However, ENIG also has some limitations, such as higher cost compared to other surface finishes, the potential for black pad formation, and the risk of gold embrittlement if the gold layer is too thick. When choosing a surface finish, it is essential to consider the specific requirements of the application, including cost, reliability, and PCB design.
By understanding the ENIG process, its advantages, and its limitations, PCB designers and manufacturers can make informed decisions when selecting a surface finish for their products. Proper process control and adherence to industry standards ensure that ENIG-coated PCBs deliver the desired performance and reliability in demanding applications.
Leave a Reply