What is a BGA chip?
A Ball Grid Array (BGA) is a type of surface-mount packaging used for integrated circuits. The bottom of a BGA chip features a grid of solder balls that connect to contact pads on a printed circuit board (PCB). This packaging allows for a high density of interconnects in a small package size.
BGA packages offer several advantages over other types of IC packaging:
- Compact size
- High connection density
- Lower thermal resistance
- Better electrical performance
Common BGA package sizes and ball counts include:
Package | Size (mm) | Ball Count |
---|---|---|
CABGA-96 | 8×8 | 96 |
CABGA-208 | 15×15 | 208 |
PBGA-225 | 27×27 | 225 |
PBGA-324 | 23×23 | 324 |
TBGA-1156 | 35×35 | 1156 |
Why do BGA chips fail?
Despite their benefits, BGA packages are susceptible to various failure modes. Some common causes of BGA failure include:
Thermal stress
The coefficient of thermal expansion (CTE) mismatch between the BGA substrate, solder balls, and PCB can lead to thermal stress during temperature cycling. Over time, this stress can cause solder joint fatigue and cracking.
Mechanical stress
Physical shock, vibration, and flexing of the PCB can put mechanical strain on BGA solder joints. This stress can cause solder balls to crack or detach from the substrate or PCB pads.
Manufacturing defects
Issues during the assembly process, such as poor soldering, insufficient solder volume, or contamination, can result in weak or defective solder joints that fail prematurely.
Electromigration
High current density can cause metal ions to migrate within the solder joints over time, leading to voids, cracks, and eventual open circuits.
Environmental factors
Exposure to moisture, corrosive chemicals, or extreme temperatures can degrade BGA solder joints and cause failure.
Symptoms of BGA failure
When a BGA chip begins to fail, it can manifest in various symptoms depending on the severity and location of the damaged solder joints. Some common signs of BGA failure include:
- Intermittent device operation
- Freezing, crashing, or boot failures
- Display artifacts or distortions
- Reduced performance
- Complete device non-functionality
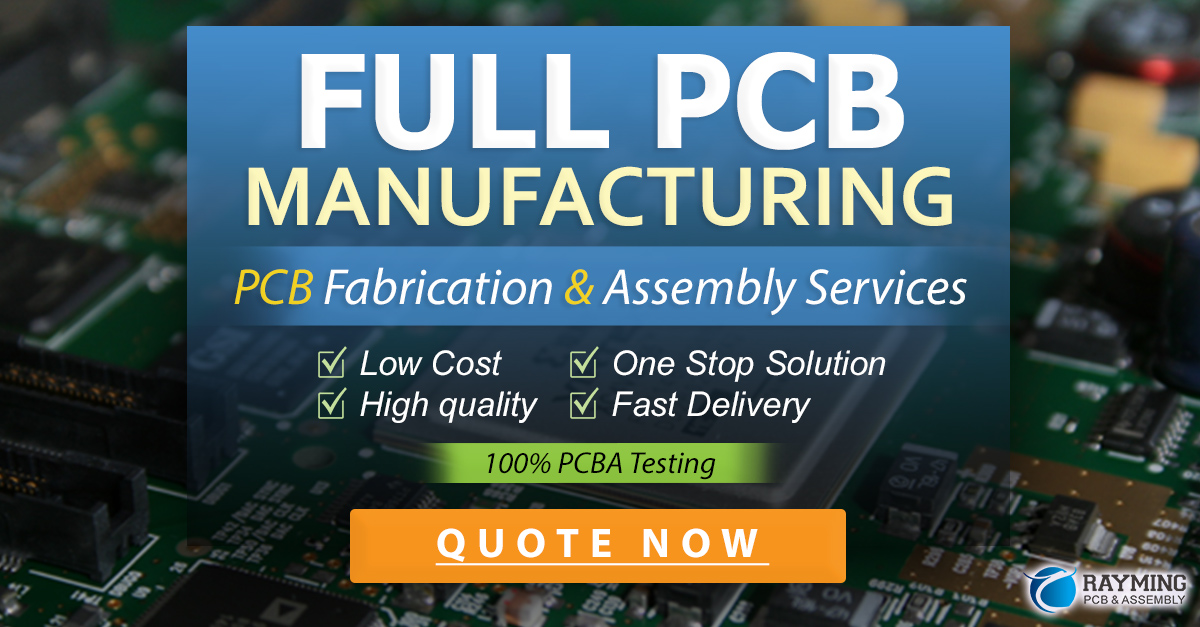
BGA failure diagnosis techniques
Diagnosing BGA failures can be challenging due to the hidden nature of the solder joints. Several techniques are used to identify and localize BGA defects:
Visual inspection
Optical microscopy can reveal visible defects such as cracked solder balls, bridging, or contamination on exposed areas of the BGA.
X-ray inspection
2D or 3D X-ray imaging allows non-destructive visualization of hidden solder joints, voids, and cracks within the BGA package.
Thermal imaging
Infrared cameras can detect abnormal heat patterns caused by increased resistance in damaged solder joints during device operation.
Boundary scan testing
For devices with built-in boundary scan architecture (e.g., JTAG), automated testing can identify failed connections between BGA balls and PCB pads.
Time-domain reflectometry (TDR)
TDR analysis measures reflected waveforms to pinpoint discontinuities in BGA solder joint connections.
The BGA Reballing process
When a BGA failure is confirmed, reballing is often necessary to repair the device. The reballing process typically involves the following steps:
- Desoldering the BGA chip
- Removing the old solder balls
- Cleaning the BGA pads
- Applying new solder paste
- Placing new solder balls
- Reflowing the solder joints
- Cleaning flux residue
- Testing and inspection
Required equipment for BGA reballing
To perform a successful BGA reball, several specialized tools and materials are needed:
- BGA Rework station with hot air and vacuum pickup
- Soldering iron and solder wick
- Solder paste stencil and squeegee
- Solder flux and cleaning solution
- Microscope or digital microscope
- Precision tweezers and brushes
- Replacement solder balls
Here is a table comparing the melting points of common solder ball alloys:
Solder Alloy | Melting Point (°C) |
---|---|
Sn63Pb37 | 183 |
Sn96.5Ag3.0Cu0.5 | 217-220 |
Sn42Bi57Ag1 | 137-139 |
AuSn20 | 280 |
Challenges in BGA reballing
Reballing a BGA chip is a delicate and precise process that requires skill, patience, and the right equipment. Some challenges that can arise during reballing include:
- Accurate alignment of the solder ball stencil
- Even solder paste application
- Precise placement of new solder balls
- Consistent reflow temperature profile
- Avoiding bridging or solder balling
- Cleaning residual flux without damaging joints
- Verification of joint integrity post-reball
Alternatives to BGA reballing
In some cases, reballing may not be the most appropriate or cost-effective solution for a failed BGA device. Alternative approaches include:
BGA rework
For localized solder joint defects, selective rework using hot air and solder paste can repair individual balls without full reballing.
BGA replacement
If the BGA chip itself is damaged, replacing it with a new component may be more practical than attempting a reball.
PCB redesign
For recurrent BGA failure issues, redesigning the PCB with improved layout, thermal management, or underfill can enhance reliability.
FAQ
- How much does BGA reballing cost?
The cost of BGA reballing varies depending on factors such as the size and complexity of the BGA package, the equipment required, and the service provider. Typical prices can range from $50 to $200 or more per chip.
- Can I reball a BGA at home?
While it is possible to reball a BGA at home with the right equipment and skills, it is not recommended for inexperienced individuals. BGA reballing requires specialized tools, precise techniques, and a controlled environment to ensure success and avoid further damage.
- How long does BGA reballing take?
The time required for BGA reballing depends on the specific chip and the technician’s experience. A skilled technician can usually complete a reball within 30 minutes to 2 hours, excluding diagnosis and testing time.
- Is BGA reballing a permanent fix?
When performed correctly, BGA reballing can be a long-lasting solution to solder joint issues. However, the longevity of the repair depends on various factors, such as the quality of the reball, the underlying cause of the failure, and the device’s operating conditions.
- Can reballing fix other BGA chip issues?
Reballing primarily addresses solder joint defects and may not resolve other issues with the BGA chip itself, such as internal die damage or programming faults. A thorough diagnosis is essential to determine if reballing is an appropriate solution for a given problem.
Leave a Reply