Introduction to Acid Traps in PCBs
In the world of printed circuit board (PCB) manufacturing, acid traps are a common phenomenon that can lead to various issues during the fabrication process. An acid trap, also known as an “etch trap” or “copper trap,” is an unintended design feature that can cause problems during the etching process of PCB production. This article will delve into the concept of acid traps, their causes, effects, and ways to prevent them.
What is an Acid Trap?
An acid trap is a design feature in a PCB where the geometry of the copper traces and pads creates a narrow, confined space that can trap the etching solution during the manufacturing process. These traps can occur when there is insufficient space between copper features or when the design includes acute angles or narrow channels.
When the etching solution becomes trapped in these confined spaces, it can lead to incomplete etching, resulting in unwanted copper remnants on the PCB. These remnants can cause short circuits, poor electrical performance, and reduced reliability of the finished product.
Common Causes of Acid Traps
- Narrow spacing between copper features
- Acute angles in copper traces
- Insufficient etch factor
- Improper design rules adherence
The Etching Process in PCB Manufacturing
To understand the impact of acid traps on PCB manufacturing, it’s essential to have a basic understanding of the etching process. Etching is a critical step in PCB fabrication, where unwanted copper is removed from the substrate to create the desired circuit pattern.
Steps in the Etching Process
- Applying the etch resist: A photoresist layer is applied to the copper-clad substrate and exposed to UV light through a photomask, hardening the resist in the desired pattern.
- Developing the photoresist: The unexposed photoresist is removed, leaving behind the hardened resist in the desired circuit pattern.
- Etching the copper: The PCB is exposed to an etching solution, typically ferric chloride or ammonium persulfate, which removes the unwanted copper not protected by the hardened photoresist.
- Stripping the photoresist: After etching, the remaining photoresist is removed, leaving behind the desired copper circuit pattern.
Etch Factors and Their Importance
The etch factor is a critical consideration in PCB design and manufacturing. It refers to the ratio of the etch depth to the undercut (the amount of copper removed beneath the etch resist). A higher etch factor means a more precise and controlled etching process.
Etch Factor | Etch Depth | Undercut |
---|---|---|
1:1 | 1 mil | 1 mil |
2:1 | 2 mil | 1 mil |
3:1 | 3 mil | 1 mil |
Achieving a high etch factor is essential for preventing acid traps and ensuring the accuracy of the final circuit pattern.
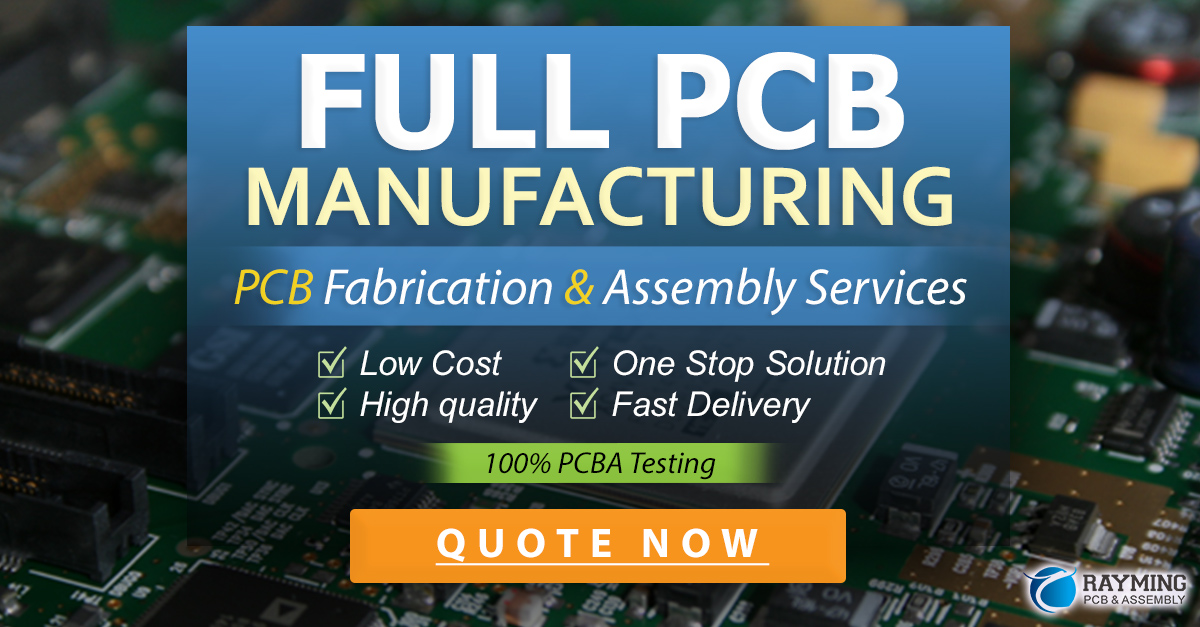
Effects of Acid Traps on PCB Performance
Acid traps can have several negative effects on the performance and reliability of a PCB:
- Short circuits: Copper remnants left behind by acid traps can create unintended connections between traces, leading to short circuits and device malfunction.
- Reduced electrical performance: Acid traps can alter the intended impedance of traces, leading to signal integrity issues and reduced electrical performance.
- Decreased reliability: PCBs with acid traps are more prone to failure over time due to the presence of unwanted copper remnants and potential short circuits.
Preventing Acid Traps in PCB Design
Preventing acid traps is crucial for ensuring the quality and reliability of PCBs. Here are some best practices for avoiding acid traps in PCB design:
Design Rules and Guidelines
-
Maintain adequate spacing between copper features: Ensure that the spacing between traces, pads, and other copper features is sufficient to prevent acid traps. The minimum spacing should be based on the capabilities of the PCB manufacturer and the desired etch factor.
-
Avoid acute angles: Whenever possible, design traces with gentle curves and avoid sharp, acute angles. Acute angles are more prone to acid traps due to the difficulty in etching the narrow, confined spaces they create.
-
Adhere to manufacturer’s design rules: Follow the PCB manufacturer’s design guidelines and rules to ensure compatibility with their fabrication processes and to minimize the risk of acid traps.
Design for Manufacturability (DFM)
Design for Manufacturability (DFM) is an approach that focuses on creating PCB designs that are optimized for the manufacturing process. By considering the limitations and capabilities of the manufacturing process during the design phase, designers can create PCBs that are less prone to issues like acid traps.
Some key aspects of DFM include:
- Collaborating with the PCB manufacturer early in the design process
- Using design rule checks (DRC) to verify adherence to manufacturer’s guidelines
- Performing thorough design reviews to identify potential manufacturability issues
PCB Layout Techniques to Avoid Acid Traps
In addition to following design rules and guidelines, there are several PCB layout techniques that can help prevent acid traps:
-
Teardrop pads: Adding teardrop-shaped copper areas at the intersection of traces and pads can help prevent acid traps by providing a smoother transition and reducing the occurrence of acute angles.
-
Hatched polygons: Using hatched polygons instead of solid copper areas can improve etching uniformity and reduce the risk of acid traps. Hatched polygons have small openings that allow the etching solution to flow more easily, preventing trapping.
-
Etch compensation: Applying etch compensation to the PCB design involves slightly oversizing the copper features to account for the expected amount of undercut during the etching process. This helps maintain the desired trace widths and spacing, reducing the risk of acid traps.
Case Studies and Examples
To illustrate the impact of acid traps on PCB manufacturing and performance, let’s look at a few case studies and examples.
Case Study 1: Smartphone Manufacturer
A smartphone manufacturer experienced a high rate of device failures due to short circuits on the main logic board. Upon investigation, it was discovered that the PCB design included several acid traps, resulting in copper remnants bridging adjacent traces.
The manufacturer worked with the PCB designer to revise the design, following DFM principles and eliminating the acid traps. The revised design resulted in a significant reduction in device failures and improved overall product quality.
Case Study 2: Automotive Electronics Supplier
An automotive electronics supplier encountered signal integrity issues in a critical sensor module. The root cause was traced back to acid traps in the PCB design, which altered the impedance of certain traces and degraded signal quality.
By redesigning the PCB to eliminate the acid traps and optimize the layout for manufacturability, the supplier was able to resolve the signal integrity issues and improve the performance and reliability of the sensor module.
Frequently Asked Questions (FAQ)
- What is the difference between an acid trap and an etch trap?
-
Acid trap and etch trap are interchangeable terms that refer to the same issue in PCB manufacturing. Both terms describe a situation where the etching solution becomes trapped in narrow, confined spaces due to the geometry of the copper features.
-
Can acid traps be fixed after the PCB has been manufactured?
-
In most cases, acid traps cannot be easily fixed once the PCB has been manufactured. The presence of unwanted copper remnants and potential short circuits may require the PCB to be scraped or reworked, which can be costly and time-consuming. It’s best to prevent acid traps during the design phase.
-
How can I check my PCB design for potential acid traps?
-
To check your PCB design for potential acid traps, you can use design rule checks (DRC) in your PCB design software. DRC tools can help identify areas where copper features are too close together or where acute angles may cause Etching Issues. Additionally, conducting thorough design reviews and collaborating with your PCB manufacturer can help identify and address potential acid traps.
-
What is the minimum spacing between copper features to avoid acid traps?
-
The minimum spacing between copper features to avoid acid traps depends on several factors, including the PCB manufacturer’s capabilities, the desired etch factor, and the specific design requirements. It’s best to consult with your PCB manufacturer and follow their design guidelines to determine the appropriate minimum spacing for your project.
-
Are there any automated tools to help prevent acid traps in PCB design?
- Yes, many PCB design software packages include tools and features to help prevent acid traps. These may include design rule checks (DRC), automated etch compensation, and layout optimization tools. However, it’s important to remember that automated tools are not a substitute for good design practices and collaboration with your PCB manufacturer.
Conclusion
Acid traps are a common issue in PCB manufacturing that can lead to various problems, including short circuits, reduced electrical performance, and decreased reliability. By understanding the causes and effects of acid traps, and following best practices for prevention, PCB designers can create designs that are optimized for manufacturability and minimize the risk of etching issues.
Effective prevention of acid traps involves adhering to design rules and guidelines, collaborating with PCB manufacturers, and implementing layout techniques such as teardrop pads, hatched polygons, and etch compensation. By taking a proactive approach to preventing acid traps, designers can ensure the quality, performance, and reliability of their PCBs.
Leave a Reply