Introduction to Printed Circuit Boards (PCBs)
A Printed Circuit Board (PCB) is a fundamental component in modern electronic devices. It is a flat board made of insulating materials, such as fiberglass or composite epoxy, with conductive pathways etched or printed onto its surface. These pathways, also known as traces, connect various electronic components, such as resistors, capacitors, and integrated circuits (ICs), to form a complete electrical circuit.
PCBs have revolutionized the electronics industry by providing a reliable, compact, and cost-effective way to assemble and manufacture electronic devices. They are used in a wide range of applications, from simple consumer electronics to complex aerospace and military systems.
History of PCBs
The concept of printed circuits dates back to the early 20th century. In 1903, Albert Hanson, a German inventor, filed a patent for a method of creating conductive pathways on an insulating material. However, it wasn’t until the 1940s that PCBs began to gain widespread use in the electronics industry.
During World War II, the United States military heavily invested in the development of PCB technology to improve the reliability and efficiency of their electronic systems. In 1946, the first double-sided PCB was developed, allowing for more complex circuits to be created.
Throughout the 1950s and 1960s, PCB manufacturing techniques continued to advance, with the introduction of through-hole technology and the use of photographic methods for creating circuit patterns. By the 1970s, PCBs had become an essential component in the rapidly growing consumer electronics market.
Types of PCBs
There are several types of PCBs, each with its own unique characteristics and manufacturing process. The most common types include:
Single-sided PCBs
Single-sided PCBs have conductive traces on only one side of the insulating substrate. They are the simplest and most cost-effective type of PCB, often used in low-complexity electronic devices and prototypes.
Double-sided PCBs
Double-sided PCBs have conductive traces on both sides of the insulating substrate, allowing for more complex circuits and higher component density. The two sides are connected using through-hole technology or vias.
Multi-layer PCBs
Multi-layer PCBs consist of three or more conductive layers separated by insulating layers. They offer the highest level of complexity and component density, making them ideal for advanced electronic systems, such as smartphones, computers, and aerospace applications.
Type of PCB | Layers | Complexity | Cost |
---|---|---|---|
Single-sided | 1 | Low | Low |
Double-sided | 2 | Medium | Medium |
Multi-layer | 3+ | High | High |
Flexible PCBs
Flexible PCBs (FPCBs) are made using flexible insulating materials, such as polyimide or PEEK. They can bend and fold to fit into confined spaces or conform to unique shapes, making them ideal for wearable electronics, medical devices, and aerospace applications.
Rigid-Flex PCBs
Rigid-Flex PCBs combine the benefits of both rigid and flexible PCBs. They consist of rigid PCB sections connected by flexible PCB sections, allowing for three-dimensional assembly and improved reliability in applications that require both stability and flexibility.
PCB Manufacturing Process
The PCB manufacturing process involves several steps, each requiring precision and attention to detail. The main stages include:
-
Design: The PCB design is created using electronic design automation (EDA) software, such as Altium Designer or KiCad. The design includes the circuit schematic, component placement, and routing of conductive traces.
-
Printing: The PCB design is printed onto a transparent film or directly onto the PCB substrate using a photoplotter or inkjet printer.
-
Etching: The PCB substrate is coated with a photoresist layer and exposed to UV light through the printed film. The exposed areas of the photoresist are then removed, leaving the desired circuit pattern. The unwanted copper is etched away using a chemical solution, typically ferric chloride or ammonium persulfate.
-
Drilling: Holes are drilled into the PCB substrate to accommodate through-hole components and vias. This is typically done using computer-controlled drilling machines.
-
Plating: The drilled holes are plated with a conductive material, such as copper, to ensure electrical connectivity between layers.
-
Solder Mask Application: A solder mask layer is applied to the PCB surface to protect the copper traces from oxidation and prevent solder bridges during the assembly process. The solder mask also provides insulation and improves the PCB’s appearance.
-
Silkscreen Printing: A silkscreen layer is printed onto the PCB surface to add text, logos, and component identifiers. This helps with the assembly process and makes the PCB easier to understand and troubleshoot.
-
Surface Finishing: A surface finish, such as HASL (Hot Air Solder Leveling), ENIG (Electroless Nickel Immersion Gold), or OSP (Organic Solderability Preservative), is applied to the exposed copper areas to prevent oxidation and improve solderability.
-
Quality Control: The manufactured PCBs undergo a series of quality control tests, including visual inspection, electrical testing, and functional testing, to ensure they meet the required specifications and performance standards.
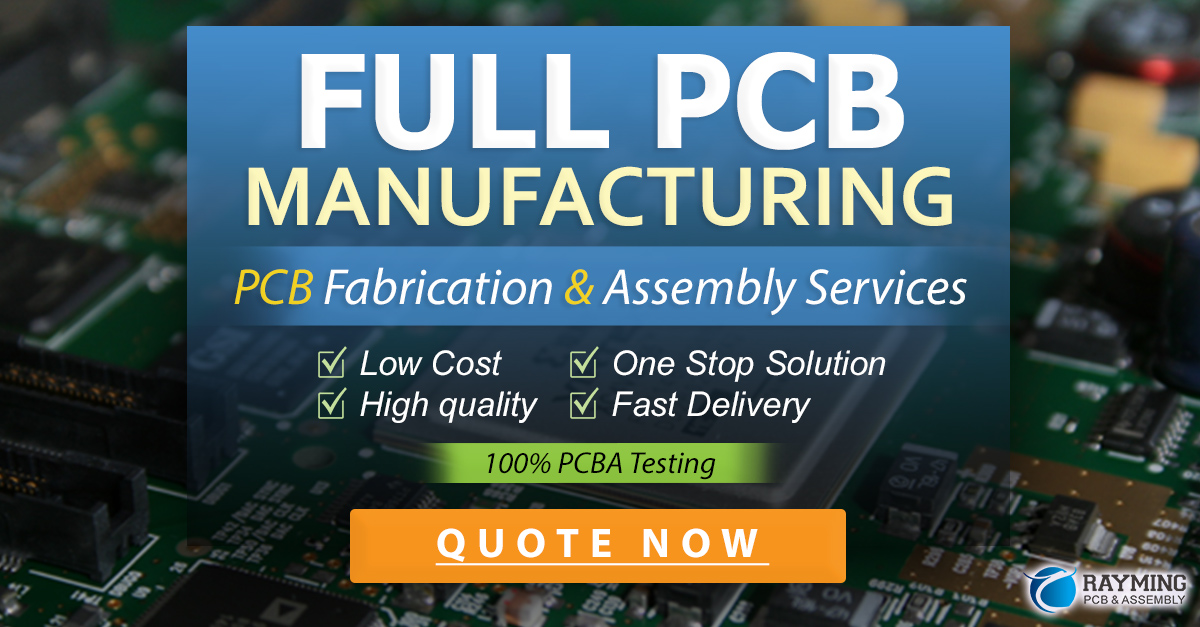
PCB Design Considerations
When designing a PCB, several factors must be taken into account to ensure optimal performance, reliability, and manufacturability. Some key considerations include:
Component Placement
Proper component placement is crucial for several reasons:
- Signal Integrity: Components should be placed to minimize the length of critical signal paths and avoid crossing sensitive signals with potential sources of interference.
- Thermal Management: Components that generate significant heat should be placed in a way that allows for efficient heat dissipation, such as near the edge of the board or with sufficient spacing between them.
- Mechanical Stability: Heavy or tall components should be placed in a way that minimizes the risk of mechanical stress or vibration-induced failures.
Routing
Routing refers to the placement and geometry of conductive traces on the PCB. Proper routing is essential for ensuring signal integrity, minimizing electromagnetic interference (EMI), and meeting manufacturability requirements.
Some important routing considerations include:
- Trace Width: The width of a trace determines its current-carrying capacity and resistance. Wider traces can carry more current and have lower resistance but take up more space on the board.
- Trace Spacing: The spacing between traces affects the board’s impedance and crosstalk characteristics. Adequate spacing must be maintained to prevent signal interference and ensure manufacturability.
- Via Placement: Vias are used to connect traces between layers on a multi-layer PCB. They should be placed strategically to minimize signal reflections and impedance discontinuities.
Grounding and Power Distribution
A well-designed grounding and power distribution system is essential for minimizing noise, ensuring signal integrity, and preventing electromagnetic compatibility (EMC) issues.
Some key considerations include:
- Ground Planes: Using continuous ground planes on one or more layers of the PCB can provide a low-impedance return path for signals and help minimize EMI.
- Power Planes: Dedicated power planes can provide a low-impedance power distribution network, minimizing voltage drops and improving power supply stability.
- Decoupling Capacitors: Placing decoupling capacitors close to ICs and other active components can help minimize power supply noise and improve signal integrity.
Electromagnetic Compatibility (EMC)
EMC refers to the ability of an electronic device to operate correctly in the presence of electromagnetic interference (EMI) and to not emit excessive EMI that could interfere with other devices.
Some PCB design techniques for improving EMC include:
- Shielding: Using conductive enclosures, such as metal shields or conductive gaskets, can help contain EMI and prevent it from affecting other components or systems.
- Filtering: Incorporating filters, such as ferrite beads or LC filters, can help suppress high-frequency noise and minimize EMI.
- Grounding: Proper grounding techniques, such as using ground planes and strategically placing ground vias, can help minimize EMI and ensure a stable reference for signals.
PCB Assembly
Once the PCBs have been manufactured, they must be assembled with the required electronic components to create a functional electronic device. The PCB assembly process typically involves the following steps:
-
Solder Paste Application: Solder paste, a mixture of tiny solder particles and flux, is applied to the PCB’s SMD (surface mount device) pads using a stencil or screen printing process.
-
Component Placement: The electronic components are placed onto the PCB, either manually or using automated pick-and-place machines. The components are held in place by the solder paste’s tacky nature.
-
Reflow Soldering: The PCB is heated in a reflow oven, causing the solder paste to melt and form a permanent electrical and mechanical connection between the components and the PCB.
-
Through-hole Component Placement: Any through-hole components are inserted into the appropriate holes on the PCB.
-
Wave Soldering: The PCB is passed over a wave of molten solder, which fills the through-holes and creates a connection between the components and the PCB.
-
Inspection and Testing: The assembled PCB undergoes visual inspection and electrical testing to ensure proper functionality and adherence to quality standards.
PCB Testing and Quality Control
To ensure the reliability and performance of PCBs, various testing and quality control methods are employed throughout the manufacturing and assembly process. Some common techniques include:
In-Circuit Testing (ICT)
ICT involves using a bed-of-nails fixture to make electrical contact with specific points on the PCB. This allows for testing of individual components and circuits, helping to identify shorts, opens, and other manufacturing defects.
Flying Probe Testing
Flying probe testing uses mobile probes to make electrical contact with the PCB, allowing for more flexible testing compared to ICT. This method is particularly useful for low-volume production or prototypes.
Functional Testing
Functional testing involves powering up the assembled PCB and verifying its operation against a set of predefined test cases. This helps ensure that the PCB performs as intended in its final application.
Automated Optical Inspection (AOI)
AOI uses high-resolution cameras and image processing algorithms to detect surface-level defects, such as missing components, incorrect component placement, or solder bridging.
X-ray Inspection
X-ray inspection allows for non-destructive examination of solder joints, particularly for BGA (ball grid array) and other high-density packages where visual inspection is difficult or impossible.
Applications of PCBs
PCBs are used in a wide range of electronic devices and systems, spanning various industries and applications. Some common examples include:
- Consumer Electronics: Smartphones, laptops, televisions, gaming consoles, and home appliances.
- Automotive: Engine control units, infotainment systems, sensor systems, and power management modules.
- Medical Devices: Diagnostic equipment, monitoring systems, implantable devices, and prosthetics.
- Industrial Automation: Process control systems, robotics, motor drives, and power converters.
- Aerospace and Defense: Avionics, radar systems, satellite communication equipment, and military-grade electronics.
- Telecommunications: Network infrastructure, wireless base stations, routers, and switches.
Future Trends in PCB Technology
As electronic devices continue to advance and new technologies emerge, PCB design and manufacturing must adapt to keep pace. Some key trends shaping the future of PCBs include:
Miniaturization
The demand for smaller, more compact electronic devices is driving the need for higher-density PCBs with finer pitch components and more advanced packaging technologies, such as chip-scale packaging (CSP) and package-on-package (PoP).
High-Speed Design
With the increasing prevalence of high-speed digital interfaces, such as USB, PCIe, and HDMI, PCB designers must employ advanced techniques to maintain signal integrity and minimize EMI. This includes the use of controlled impedance traces, differential pairs, and high-performance laminates.
Additive Manufacturing
Additive manufacturing techniques, such as 3D printing, are being explored as a means to create PCBs with unique geometries and embedded components. This could enable new design possibilities and further miniaturization.
Embedded Intelligence
The integration of sensors, processors, and wireless connectivity into PCBs is enabling the development of smart, connected devices for the Internet of Things (IoT) and Industry 4.0 applications.
Sustainable Materials
As environmental concerns grow, there is an increasing focus on the use of sustainable and recyclable materials in PCB manufacturing. This includes the development of halogen-free laminates, lead-free solders, and biodegradable substrates.
Frequently Asked Questions (FAQ)
- What is the difference between a PCB and a PCBA?
-
A PCB (Printed Circuit Board) is the bare board without any components attached. A PCBA (Printed Circuit Board Assembly) is a PCB that has been assembled with the required electronic components, resulting in a functional electronic circuit.
-
What are the advantages of using PCBs over other wiring methods?
-
PCBs offer several advantages, including:
- Compact and space-efficient design
- Improved reliability and consistency
- Reduced wiring errors and short circuits
- Lower manufacturing costs for high-volume production
- Easier to troubleshoot and repair
-
How do I choose the right PCB material for my application?
- The choice of PCB material depends on several factors, such as:
- Operating temperature range
- Electrical performance requirements (e.g., dielectric constant, loss tangent)
- Mechanical requirements (e.g., flexibility, strength)
- Environmental conditions (e.g., humidity, chemical exposure)
- Cost and availability
-
Common PCB materials include FR-4, polyimide, PTFE, and ceramic substrates.
-
What is the typical turnaround time for PCB manufacturing?
-
The turnaround time for PCB manufacturing varies depending on the complexity of the design, the chosen manufacturer, and the production volume. For simple designs and low volumes, turnaround times can be as short as 24-48 hours. For more complex designs and higher volumes, lead times of 1-2 weeks or more are common.
-
How can I ensure the quality and reliability of my PCBs?
- To ensure the quality and reliability of your PCBs:
- Follow best practices for PCB design, including proper component placement, routing, and grounding.
- Choose reputable PCB manufacturers with established quality control processes.
- Specify appropriate testing and inspection requirements, such as ICT, AOI, and functional testing.
- Use high-quality components from trusted suppliers.
- Conduct thorough validation and reliability testing of the assembled PCBs under real-world conditions.
Conclusion
Printed Circuit Boards (PCBs) are the backbone of modern electronics, enabling the creation of compact, reliable, and cost-effective devices across a wide range of industries and applications. As technology continues to advance, PCB design and manufacturing must evolve to meet the growing demands for performance, miniaturization, and sustainability.
By understanding the fundamentals of PCBs, including their types, manufacturing processes, design considerations, and testing methods, engineers and designers can create innovative electronic solutions that shape the future of technology. As we look ahead to 2024 and beyond, the role of PCBs in enabling new technologies, such as IoT, artificial intelligence, and 5G communications, will only become more critical.
Leave a Reply