Introduction to PCB Assembly
Printed Circuit Board (PCB) assembly is the process of mounting electronic components onto a printed circuit board to create a functional electronic device. The PCB assembly process involves several steps, including component placement, soldering, inspection, and testing. In this comprehensive guide, we will delve into the details of the PCB assembly process, covering everything from PCB design to final testing and quality control.
Understanding PCB Design
Before the PCB assembly process can begin, the PCB must be designed. The PCB design process involves creating a schematic diagram of the electronic circuit and then translating that schematic into a physical layout of the PCB. The layout includes the placement of components, the routing of traces, and the creation of solder pads and vias.
Key Considerations in PCB Design
- Component selection and placement
- Signal integrity and electromagnetic compatibility
- Power distribution and thermal management
- Manufacturing constraints and design for manufacturability
PCB Design Software
There are several software tools available for PCB design, including:
- Altium Designer
- Eagle CAD
- KiCad
- OrCAD
- Cadence Allegro
PCB Fabrication
Once the PCB design is complete, the next step is to fabricate the physical PCB. PCB fabrication involves several processes, including:
PCB Material Selection
PCBs can be made from various materials, depending on the application and the required performance characteristics. Common PCB materials include:
- FR-4 (Flame Retardant 4)
- High-Tg FR-4
- Polyimide
- Ceramic
- Metal core
PCB Lamination
The PCB lamination process involves stacking and bonding the layers of the PCB together using heat and pressure. The layers typically include:
- Copper foil
- Prepreg (pre-impregnated fiberglass)
- Core material (e.g., FR-4)
PCB Etching
After lamination, the unwanted copper is removed from the PCB using a chemical etching process. The most common etching methods are:
- Subtractive etching (e.g., ferric chloride, cupric chloride)
- Additive etching (e.g., electroless copper plating)
PCB Drilling
Holes are drilled into the PCB to accommodate through-hole components and vias. The drilling process can be done using:
- Mechanical drilling
- Laser drilling
PCB Surface Finishing
The exposed copper on the PCB is protected from oxidation and enhanced for solderability using a surface finish. Common surface finishes include:
- Hot Air Solder Leveling (HASL)
- Electroless Nickel Immersion Gold (ENIG)
- Immersion Silver
- Immersion Tin
- Organic Solderability Preservative (OSP)
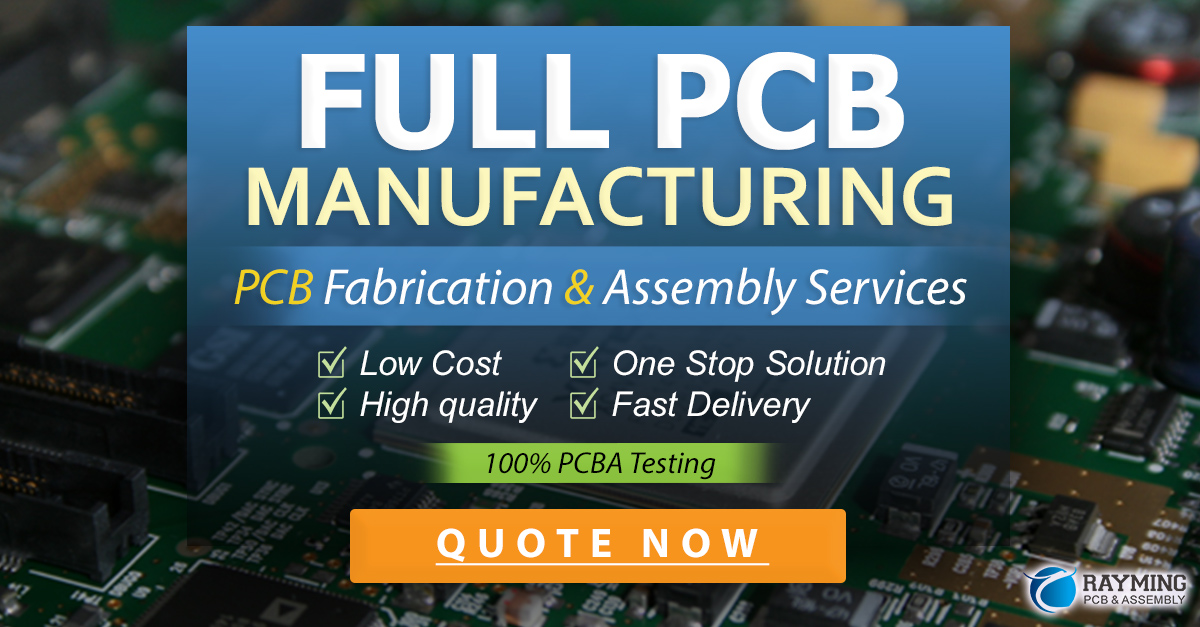
PCB Assembly Techniques
There are two primary techniques used for PCB assembly: through-hole and surface mount.
Through-Hole Assembly
In through-hole assembly, the component leads are inserted through holes drilled in the PCB and then soldered to pads on the opposite side of the board. Through-hole assembly is typically used for larger components and in applications where mechanical strength is important.
Surface Mount Assembly
Surface mount assembly involves placing components directly onto pads on the surface of the PCB and then soldering them in place. Surface mount assembly allows for smaller components and higher component density compared to through-hole assembly.
Surface Mount Assembly Subtypes
- Placement: Components are placed onto the PCB using pick-and-place machines or by hand.
- Reflow Soldering: Solder paste is applied to the PCB pads, components are placed, and then the entire assembly is heated to melt the solder and form a connection.
- Wave Soldering: The PCB is passed over a molten solder wave, which selectively solders the components to the board.
PCB Assembly Process Flow
The typical PCB assembly process flow includes the following steps:
-
Solder Paste Application: Solder paste is applied to the PCB pads using a stencil or screen printing process.
-
Component Placement: Components are placed onto the PCB using pick-and-place machines or by hand.
-
Reflow Soldering: The PCB assembly is heated in a reflow oven to melt the solder paste and form a connection between the components and the PCB pads.
-
Inspection: The soldered PCB assembly is inspected for defects, such as bridging, tombstoning, or insufficient solder.
-
Through-Hole Component Insertion: If the PCB design includes through-hole components, they are inserted into the appropriate holes.
-
Wave Soldering: The PCB assembly is passed over a molten solder wave to solder the through-hole components and any remaining surface mount components.
-
Final Inspection and Testing: The completed PCB assembly undergoes a final visual inspection and functional testing to ensure proper operation and adherence to specifications.
-
Conformal Coating (Optional): A protective coating may be applied to the PCB assembly to protect against moisture, dust, and other environmental factors.
-
Packaging and Shipping: The finished PCB assemblies are packaged and shipped to the customer or the next stage of the product assembly process.
Quality Control in PCB Assembly
Quality control is critical throughout the PCB assembly process to ensure the reliability and functionality of the final product. Some common quality control techniques include:
Visual Inspection
- Manual visual inspection
- Automated optical inspection (AOI)
X-Ray Inspection
- 2D X-ray
- 3D X-ray (computed tomography)
Electrical Testing
- In-circuit testing (ICT)
- Flying probe testing
- Boundary scan testing
Environmental Testing
- Temperature cycling
- Humidity testing
- Vibration testing
- Shock testing
PCB Assembly Defects and Troubleshooting
Despite best efforts, defects can occur during the PCB assembly process. Some common defects include:
- Bridging: Unintended connection between two or more solder pads
- Tombstoning: One end of a component lifts off the PCB during reflow soldering
- Insufficient solder: Not enough solder to form a reliable connection
- Solder balls: Small spheres of solder that can cause short circuits
- Component misalignment: Components placed incorrectly on the PCB
Troubleshooting these defects involves identifying the root cause and implementing corrective actions, such as:
- Adjusting solder paste application
- Optimizing pick-and-place machine settings
- Modifying reflow oven temperature profiles
- Improving PCB design for manufacturability
PCB Assembly Automation and Industry 4.0
As the electronics industry evolves, PCB assembly processes are increasingly automated and integrated with Industry 4.0 technologies. Some examples include:
- Robotic pick-and-place machines
- Automated optical inspection systems
- Machine vision for component alignment
- Data analytics for process optimization
- Cloud-based manufacturing execution systems (MES)
These technologies enable faster, more efficient, and more reliable PCB assembly processes while also providing valuable data for continuous improvement.
Environmental Considerations in PCB Assembly
With growing concerns about environmental sustainability, PCB assembly processes are adapting to minimize their ecological impact. Some key environmental considerations include:
- Lead-free solder: Using lead-free solder alloys to reduce the use of hazardous materials
- Waste reduction: Minimizing waste through process optimization and recycling
- Energy efficiency: Implementing energy-efficient equipment and processes
- Green materials: Using eco-friendly PCB materials and finishes
Future Trends in PCB Assembly
As the electronics industry continues to evolve, PCB assembly processes are likely to see several trends in the coming years, including:
- Miniaturization: Smaller components and higher component density
- Flexible and stretchable electronics: PCBs that can bend, flex, or stretch
- Embedded components: Components embedded within the PCB layers
- 3D printing: Additive manufacturing techniques for PCB fabrication and assembly
- Smart factories: Fully integrated and automated PCB assembly lines
FAQ
1. What is the difference between through-hole and surface mount assembly?
Through-hole assembly involves inserting component leads through holes in the PCB and soldering them to pads on the opposite side, while surface mount assembly involves placing components directly onto pads on the PCB surface and soldering them in place. Surface mount assembly allows for smaller components and higher component density.
2. What is reflow soldering?
Reflow soldering is a process in which solder paste is applied to the PCB pads, components are placed, and then the entire assembly is heated in a reflow oven to melt the solder and form a connection between the components and the PCB pads.
3. What are some common PCB assembly defects?
Common PCB assembly defects include bridging (unintended connections between solder pads), tombstoning (one end of a component lifting off the PCB during reflow), insufficient solder, solder balls, and component misalignment.
4. How can PCB assembly processes be made more environmentally friendly?
PCB assembly processes can be made more environmentally friendly by using lead-free solder alloys, minimizing waste through process optimization and recycling, implementing energy-efficient equipment and processes, and using eco-friendly PCB materials and finishes.
5. What are some future trends in PCB assembly?
Future trends in PCB assembly include miniaturization, flexible and stretchable electronics, embedded components, 3D printing for PCB fabrication and assembly, and fully integrated and automated smart factories.
Conclusion
PCB assembly is a complex process that involves numerous steps, from PCB design and fabrication to component placement, soldering, inspection, and testing. By understanding the various techniques, process flows, quality control measures, and environmental considerations involved in PCB assembly, manufacturers can optimize their processes for efficiency, reliability, and sustainability.
As the electronics industry continues to advance, PCB assembly processes will evolve to incorporate new technologies, materials, and methodologies. By staying informed about these developments and adapting accordingly, manufacturers can remain competitive in an increasingly dynamic and demanding market.
Leave a Reply