Introduction to PCBs
A Printed Circuit Board (PCB) is a fundamental component in modern electronics. It serves as a base for mounting and interconnecting electronic components to create a functional electronic device. PCBs have revolutionized the electronics industry by providing a reliable, compact, and cost-effective solution for circuit design and manufacturing.
What is a PCB?
A PCB is a thin board made of insulating materials, such as fiberglass or composite epoxy, with conductive copper traces printed on its surface. These traces are designed to connect various electronic components, such as resistors, capacitors, integrated circuits (ICs), and connectors, according to a specific circuit diagram. PCBs can be single-sided (with copper traces on one side), double-sided (with traces on both sides), or multi-layered (with traces on multiple layers separated by insulating material).
Advantages of Using PCBs
PCBs offer several advantages over traditional point-to-point wiring:
-
Compact size: PCBs allow for a much smaller footprint compared to point-to-point wiring, enabling the creation of smaller and more portable electronic devices.
-
Reliability: The use of PCBs reduces the risk of loose connections and short circuits, resulting in more reliable electronic devices.
-
Consistency: PCBs ensure consistent and precise connections between components, which is crucial for maintaining the desired performance of the electronic device.
-
Cost-effective: Mass production of PCBs is more cost-effective than point-to-point wiring, as it reduces assembly time and minimizes the risk of human error.
-
Improved signal integrity: PCBs can be designed to minimize electromagnetic interference (EMI) and ensure better signal integrity, especially in high-frequency applications.
What is a Blank PCB?
A blank PCB, also known as a bare PCB or a Prototype PCB, is a printed circuit board without any electronic components mounted on it. It consists of the insulating substrate material and the conductive copper traces that form the interconnections between the component mounting locations.
Uses of Blank PCBs
Blank PCBs serve several purposes in the electronics industry:
-
Prototyping: Blank PCBs are often used for prototyping new electronic designs. Engineers can quickly test and validate their circuit designs by mounting components on a blank PCB and checking for functionality.
-
Small-scale production: For low-volume production runs, using blank PCBs can be more cost-effective than ordering fully assembled PCBs from a manufacturer.
-
Educational purposes: Blank PCBs are used in educational settings to teach students about electronic circuits and PCB assembly techniques.
-
Customization: Some electronic projects may require specific PCB designs that are not readily available as pre-assembled boards. In such cases, using blank PCBs allows for complete customization of the circuit layout.
How to Make a Blank PCB
Creating a blank PCB involves several steps, from designing the circuit to the final fabrication of the board. The following sections will guide you through the process of making a blank PCB.
Step 1: Circuit Design
The first step in creating a blank PCB is to design the electronic circuit. This involves:
-
Schematic capture: Create a schematic diagram of your circuit using Electronic Design Automation (EDA) software, such as KiCad, Eagle, or Altium Designer. The schematic represents the logical connections between the electronic components.
-
Component selection: Choose the appropriate electronic components for your circuit based on their specifications, such as voltage rating, current rating, and package size.
-
Netlist generation: Generate a netlist from the schematic, which is a text file that describes the connections between the components.
Step 2: PCB Layout
Once the circuit design is complete, the next step is to create the PCB layout. This involves:
-
Importing the netlist: Import the netlist generated from the schematic into the PCB layout software.
-
Placing components: Arrange the components on the PCB based on their physical dimensions and the desired placement for optimal performance and ease of assembly.
-
Routing traces: Use the PCB layout software to route the copper traces between the component pads according to the netlist. Ensure that the traces are of appropriate width and follow the design rules specified by the PCB manufacturer.
-
Adding vias: Place vias (vertical interconnect access) to connect traces on different layers of the PCB, if required.
-
Applying design rules: Verify that the PCB layout adheres to the design rules, such as minimum trace width, minimum clearance between traces, and minimum drill size for vias.
-
Generating Gerber files: Export the PCB layout as Gerber files, which are industry-standard files used by PCB manufacturers to fabricate the board.
Step 3: PCB Fabrication
The final step in making a blank PCB is the fabrication process. This can be done either by sending the Gerber files to a professional PCB manufacturer or by using in-house PCB fabrication equipment.
Professional PCB Manufacturing
-
Choose a PCB manufacturer: Select a reputable PCB manufacturer that offers the desired PCB specifications, such as the number of layers, material type, and surface finish.
-
Submit Gerber files: Send the Gerber files generated from the PCB layout software to the chosen manufacturer.
-
Specify requirements: Provide the manufacturer with any additional requirements, such as the desired quantity, lead time, and shipping method.
-
Receive the manufactured PCBs: The manufacturer will fabricate the blank PCBs according to your specifications and ship them to you.
In-House PCB Fabrication
For those who have access to PCB fabrication equipment, blank PCBs can be made in-house using the following process:
-
Print the PCB artwork: Use a laser printer to print the PCB artwork on a transparent film or directly onto a photoresist-coated copper board.
-
Expose the photoresist: Place the printed artwork on top of the photoresist-coated copper board and expose it to UV light for a specific duration.
-
Develop the photoresist: Immerse the exposed board in a developing solution to remove the unexposed photoresist, leaving behind the desired copper traces.
-
Etch the copper: Place the developed board in an etching solution, such as ferric chloride, to remove the unwanted copper, leaving behind the desired traces.
-
Remove the remaining photoresist: Use a solvent, such as acetone, to remove the remaining photoresist from the copper traces.
-
Drill holes: Use a drill press or a PCB drill to create holes for component mounting and vias, as required.
-
Apply surface finish: If desired, apply a surface finish, such as solder mask or silkscreen, to protect the copper traces and improve the aesthetics of the PCB.
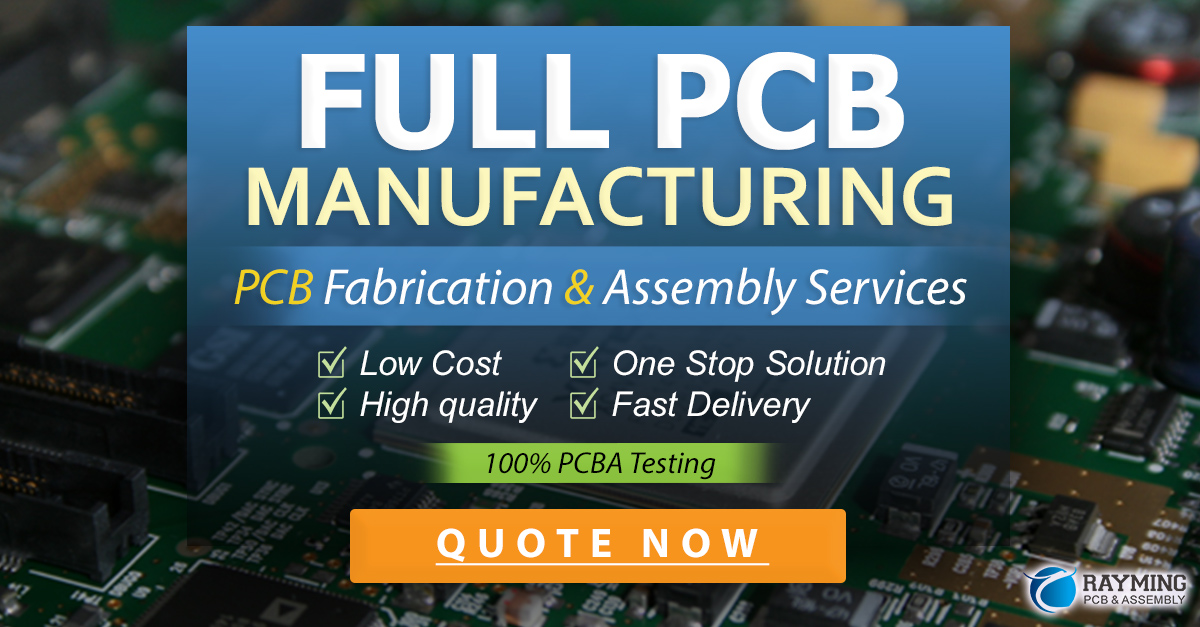
Designing for Manufacturing (DFM)
When designing a PCB, it is essential to consider the manufacturing process to ensure that the board can be fabricated efficiently and with minimal issues. This is known as Design for Manufacturing (DFM).
DFM Guidelines
-
Adhere to the manufacturer’s design rules: Follow the PCB manufacturer’s design rules, such as minimum trace width, minimum clearance, and minimum drill size, to ensure that the board can be fabricated without any issues.
-
Use standard component packages: Choose components with standard package sizes, such as surface-mount devices (SMDs) or through-hole components, to ensure compatibility with the manufacturing process.
-
Avoid acute angles: Use 45-degree angles or curves instead of 90-degree angles when routing traces to prevent acid traps during the etching process.
-
Provide adequate clearance: Ensure sufficient clearance between components, traces, and the board edge to avoid short circuits and facilitate easier assembly.
-
Use consistent trace width: Maintain consistent trace width throughout the PCB to ensure even current distribution and minimize the risk of thermal stress.
-
Include fiducial marks: Add fiducial marks to the PCB design to help align the board during the automated assembly process.
-
Consider the assembly process: Design the PCB with the assembly process in mind, ensuring that components are placed in a logical order and with sufficient space for automated pick-and-place machines.
PCB Materials
The choice of PCB material depends on the specific requirements of the electronic device, such as the operating temperature, frequency, and environmental conditions.
Common PCB Materials
-
FR-4: FR-4 is the most commonly used PCB material. It is a composite material made of woven fiberglass cloth with an epoxy resin binder. FR-4 offers good mechanical strength, electrical insulation, and thermal stability.
-
High-Tg FR-4: High-Tg FR-4 is a variant of the standard FR-4 material with a higher glass transition temperature (Tg). It is suitable for applications that require better thermal stability and resistance to high temperatures.
-
Polyimide: Polyimide is a high-performance polymer material that offers excellent thermal stability, chemical resistance, and mechanical strength. It is often used in flexible PCBs and high-temperature applications.
-
Aluminum: Aluminum PCBs are used in applications that require better heat dissipation, such as high-power LED lighting or motor control systems. The aluminum substrate helps to quickly dissipate heat away from the electronic components.
-
Ceramic: Ceramic PCBs are used in high-frequency and high-temperature applications, such as RF and microwave circuits. They offer excellent electrical insulation, thermal conductivity, and dimensional stability.
Choosing the Right PCB Material
When selecting a PCB material, consider the following factors:
-
Operating temperature: Choose a material that can withstand the expected operating temperature range of the electronic device.
-
Frequency: For high-frequency applications, select a material with a low dielectric constant and low loss tangent to minimize signal loss and distortion.
-
Mechanical requirements: Consider the mechanical stress and vibration that the PCB will be subjected to and choose a material with appropriate strength and flexibility.
-
Environmental conditions: Take into account the environmental factors, such as humidity, chemical exposure, and UV radiation, and select a material that can withstand these conditions.
-
Cost: Evaluate the cost of the PCB material in relation to the overall project budget and the required performance characteristics.
PCB Surface Finishes
A surface finish is applied to the copper traces on a PCB to protect them from oxidation and enhance the solderability of the board. The choice of surface finish depends on the specific application, the desired shelf life, and the compatibility with the assembly process.
Common PCB Surface Finishes
-
Hot Air Solder Leveling (HASL): HASL is a widely used surface finish that involves dipping the PCB in molten solder and then using hot air to level the solder on the surface. It offers good solderability and is relatively inexpensive.
-
Electroless Nickel Immersion Gold (ENIG): ENIG is a two-layer surface finish that consists of a layer of electroless nickel followed by a thin layer of immersion gold. It provides excellent solderability, corrosion resistance, and shelf life.
-
Organic Solderability Preservative (OSP): OSP is a thin, organic coating applied to the copper traces to prevent oxidation. It is a cost-effective and environmentally friendly option, but it has a limited shelf life compared to other surface finishes.
-
Immersion Silver: Immersion silver is a thin layer of silver applied to the copper traces through a chemical process. It offers good solderability and is a cost-effective alternative to ENIG.
-
Immersion Tin: Immersion tin is a thin layer of tin applied to the copper traces through a chemical process. It provides good solderability and is suitable for both leaded and lead-free assembly processes.
Choosing the Right Surface Finish
When selecting a surface finish for your PCB, consider the following factors:
-
Shelf life: If the PCBs need to be stored for an extended period before assembly, choose a surface finish with a longer shelf life, such as ENIG or immersion silver.
-
Solderability: Ensure that the selected surface finish is compatible with the soldering process and provides good wetting and joint formation.
-
Assembly process: Consider the assembly process, such as reflow soldering or wave soldering, and choose a surface finish that is compatible with the process.
-
Environmental regulations: Take into account any environmental regulations, such as the Restriction of Hazardous Substances (RoHS) directive, and select a surface finish that complies with these regulations.
-
Cost: Evaluate the cost of the surface finish in relation to the overall project budget and the required performance characteristics.
FAQ
1. What is the difference between a blank PCB and a manufactured PCB?
A blank PCB is a printed circuit board without any electronic components mounted on it, while a manufactured PCB is a fully assembled board with all the required components soldered onto it.
2. Can I design a PCB without using EDA software?
While it is possible to design a simple PCB by hand, using EDA software is highly recommended for more complex designs. EDA software helps to streamline the design process, catch errors early, and generate the necessary files for manufacturing.
3. What is the minimum trace width and clearance for a PCB?
The minimum trace width and clearance depend on the PCB manufacturer’s capabilities and the specific design requirements. Typically, for a standard PCB, the minimum trace width is around 0.15mm (6mil), and the minimum clearance is around 0.2mm (8mil). However, it is essential to consult the manufacturer’s design rules for specific guidelines.
4. How long does it take to manufacture a blank PCB?
The manufacturing time for a blank PCB depends on various factors, such as the complexity of the design, the chosen material, and the manufacturer’s workload. Generally, for a standard double-sided PCB, the manufacturing time can range from a few days to a couple of weeks.
5. Can I make a blank PCB at home?
Yes, it is possible to make a blank PCB at home using a simple etching process. However, the quality and precision of home-made PCBs may not be as good as professionally manufactured ones. Home-made PCBs are suitable for simple designs and prototyping purposes.
Conclusion
Blank PCBs are an essential component in the electronics industry, serving as the foundation for creating custom electronic devices. Understanding the process of designing and manufacturing blank PCBs is crucial for anyone involved in electronics design and development.
This article has covered the essential aspects of blank PCBs, including their uses, the design process, manufacturing techniques, and the importance of Design for Manufacturing (DFM). We have also discussed the various PCB materials and surface finishes available and the factors to consider when selecting them.
By following the guidelines and best practices outlined in this article, you can create high-quality blank PCBs that meet your specific requirements and ensure the optimal performance of your electronic devices.
Leave a Reply