Introduction to Aluminum PCB
Aluminum PCBs are a type of printed circuit board that uses aluminum as the base material instead of the traditional FR-4 or other rigid substrates. These PCBs offer unique properties and advantages that make them suitable for specific applications where flexibility, heat dissipation, and weight reduction are crucial factors.
Definition of Aluminum PCB
An aluminum PCB is a printed circuit board that utilizes an aluminum substrate as the base material. The aluminum substrate is typically coated with a dielectric layer, such as polyimide or epoxy, to provide electrical insulation between the conductive traces and the aluminum base.
Differences between Aluminum PCB and FPC
It is important to note that aluminum PCBs are not the same as flexible printed circuits (FPCs). While both types of PCBs offer flexibility, they differ in their base materials and manufacturing processes.
Feature | Aluminum PCB | FPC |
---|---|---|
Base Material | Aluminum | Polyimide or other flexible substrates |
Flexibility | Moderate | High |
Heat Dissipation | Excellent | Poor |
Weight | Lightweight | Lightweight |
Thickness | Thicker than FPCs | Very thin |
Application | Heat-sensitive devices, LED lighting, automotive electronics | Wearable devices, medical equipment, consumer electronics |
Advantages of Aluminum PCB
Aluminum PCBs offer several advantages over traditional rigid PCBs and FPCs. These benefits make them suitable for specific applications where their unique properties are required.
Excellent Heat Dissipation
One of the most significant advantages of aluminum PCBs is their excellent heat dissipation capabilities. Aluminum is a highly thermally conductive material, which means it can efficiently transfer heat away from electronic components. This property is particularly useful in applications where heat generation is a concern, such as high-power LEDs, power electronics, and automotive electronics.
Lightweight and Durable
Aluminum PCBs are lightweight compared to traditional FR-4 PCBs due to the lower density of aluminum. This weight reduction is beneficial in applications where every gram counts, such as in aerospace and automotive industries. Despite being lightweight, aluminum PCBs are also durable and can withstand harsh environmental conditions.
Flexibility and Bendability
Unlike rigid PCBs, aluminum PCBs offer a degree of flexibility and bendability. The aluminum substrate can be bent to a certain extent without causing damage to the circuit traces. This flexibility allows for more design freedom and the ability to conform to irregular shapes and spaces.
Cost-Effective Solution
Aluminum PCBs can be a cost-effective solution for certain applications. While the raw material cost of aluminum may be higher than traditional PCB substrates, the overall cost can be lower when considering factors such as reduced weight, improved thermal management, and simplified assembly processes.
Manufacturing Process of Aluminum PCB
The manufacturing process of aluminum PCBs differs from that of traditional PCBs due to the unique properties of the aluminum substrate. Here are the key steps involved in the production of aluminum PCBs:
-
Substrate Preparation: The aluminum substrate is cleaned and treated to ensure proper adhesion of the dielectric layer.
-
Dielectric Layer Application: A dielectric layer, such as polyimide or epoxy, is applied to the aluminum substrate to provide electrical insulation.
-
Circuit Patterning: The desired circuit pattern is created on the dielectric layer using various methods, such as screen printing, photolithography, or etching.
-
Protective Coating: A protective coating, such as soldermask, is applied to the circuit traces to protect them from environmental factors and enhance the PCB’s durability.
-
Surface Finishing: The exposed copper traces are plated with a surface finish, such as HASL, ENIG, or OSP, to prevent oxidation and improve solderability.
-
Cutting and Forming: The aluminum PCB panel is cut and formed into the desired shape and size using methods like punching, routing, or laser cutting.
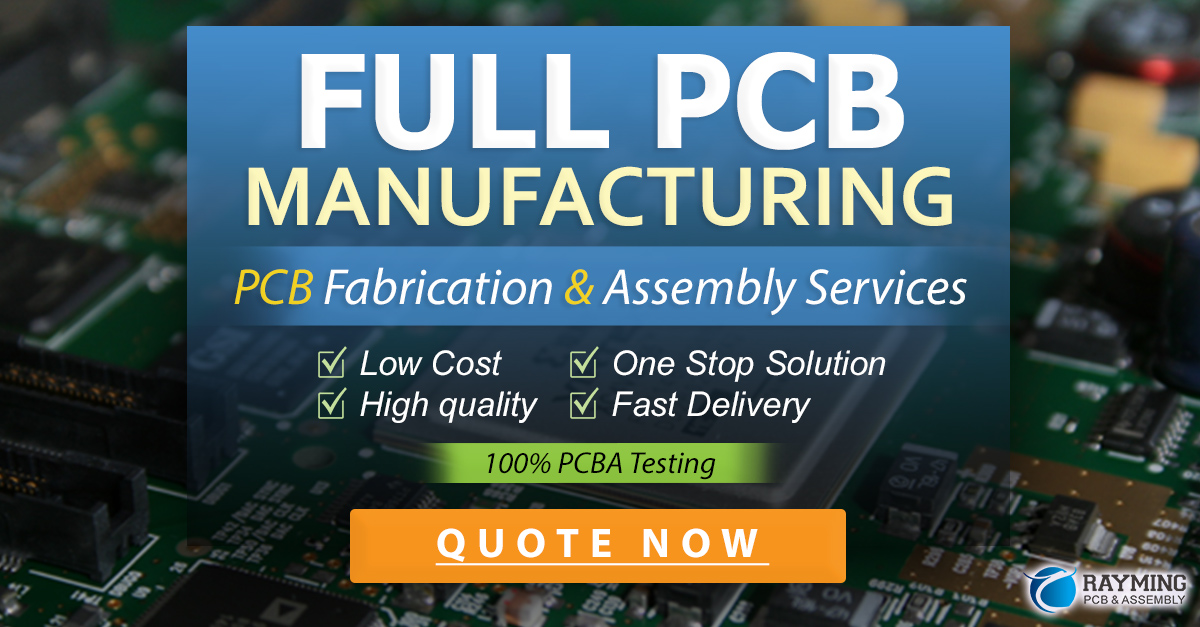
Applications of Aluminum PCB
Aluminum PCBs find applications in various industries where their unique properties are advantageous. Some common applications include:
LED Lighting
Aluminum PCBs are widely used in LED lighting applications due to their excellent heat dissipation capabilities. The aluminum substrate helps to effectively transfer heat away from the LED components, ensuring optimal performance and longevity.
Automotive Electronics
In the automotive industry, aluminum PCBs are used in various electronic systems, such as engine control units, power inverters, and battery management systems. The lightweight and durable nature of aluminum PCBs makes them suitable for the harsh automotive environment.
Power Electronics
Aluminum PCBs are employed in power electronic applications, such as power supplies, motor drives, and solar inverters. The superior thermal management properties of aluminum PCBs help to dissipate heat generated by high-power components, ensuring reliable operation.
Aerospace and Defense
The aerospace and defense industries require lightweight and durable electronic solutions. Aluminum PCBs offer weight reduction and robust performance, making them suitable for applications such as avionics, satellite systems, and military equipment.
Challenges and Considerations
While aluminum PCBs offer numerous benefits, there are also some challenges and considerations to keep in mind when designing and manufacturing them.
Thermal Expansion Mismatch
Aluminum has a higher coefficient of thermal expansion (CTE) compared to traditional PCB materials. This mismatch in thermal expansion can lead to stress and potential reliability issues if not properly addressed during the design and manufacturing stages.
Electrical Insulation
The aluminum substrate is electrically conductive, which necessitates the use of a dielectric layer to provide electrical insulation between the circuit traces and the aluminum base. The quality and integrity of the dielectric layer are critical for the proper functioning of the aluminum PCB.
Joining and Soldering
Soldering components to aluminum PCBs requires special considerations due to the differences in thermal conductivity and expansion compared to traditional PCBs. Proper soldering techniques and materials must be used to ensure reliable and durable solder joints.
Frequently Asked Questions (FAQ)
-
Q: Can aluminum PCBs be used in high-frequency applications?
A: Yes, aluminum PCBs can be used in high-frequency applications. However, proper design considerations must be taken to ensure signal integrity and minimize the impact of the aluminum substrate on the high-frequency performance. -
Q: Are aluminum PCBs more expensive than traditional PCBs?
A: The raw material cost of aluminum may be higher than traditional PCB substrates. However, the overall cost can be lower when considering factors such as reduced weight, improved thermal management, and simplified assembly processes. -
Q: How do aluminum PCBs compare to Copper PCBs in terms of thermal conductivity?
A: Aluminum has a lower thermal conductivity compared to copper. However, aluminum PCBs still offer excellent heat dissipation capabilities compared to traditional FR-4 PCBs due to the thermal conductivity of the aluminum substrate. -
Q: Can aluminum PCBs be used in harsh environments?
A: Yes, aluminum PCBs are durable and can withstand harsh environmental conditions. They are suitable for applications in industries such as automotive, aerospace, and defense, where robust performance is required. -
Q: Are there any limitations on the minimum trace width and spacing in aluminum PCBs?
A: The minimum trace width and spacing in aluminum PCBs are generally similar to those in traditional PCBs. However, the specific limitations may vary depending on the manufacturing capabilities of the PCB fabricator and the chosen dielectric material.
Conclusion
Aluminum PCBs offer a unique combination of properties, including excellent heat dissipation, flexibility, and lightweight construction. These characteristics make them suitable for a wide range of applications where thermal management, weight reduction, and design flexibility are critical factors.
While aluminum PCBs present some challenges, such as thermal expansion mismatch and the need for proper electrical insulation, these can be addressed through careful design and manufacturing considerations.
As technology advances and the demand for high-performance, lightweight, and thermally efficient electronic solutions grows, aluminum PCBs are likely to find increasing adoption across various industries. Their unique properties and advantages make them a valuable option for designers and engineers seeking to push the boundaries of electronic design and functionality.
Leave a Reply