Introduction to USB PCBs
A USB PCB, or Universal Serial Bus Printed Circuit Board, is the core component that enables communication and power transfer between a USB host and peripheral device. USB has become the most widely used serial interface standard for connecting computers to external devices. Virtually every electronic gadget we use today, from smartphones to external hard drives, relies on USB connectivity enabled by a well-designed USB PCB.
USB PCBs contain the circuitry and components necessary to implement the USB protocol for transmitting data and power. They are found inside the USB peripheral device itself and handle all the low-level signaling and power management required for USB communication. The PCB layout and component selection are critical to ensuring proper functionality, signal integrity, and adherence to USB specifications.
In this comprehensive article, we will dive deep into USB PCBs, exploring their role, types, design considerations, manufacturing process, and testing procedures. Whether you are an electronic engineer, PCB designer, or technology enthusiast, understanding USB PCBs is essential in today’s world of ubiquitous USB devices.
Types of USB PCBs
USB PCBs come in various types, each designed for a specific USB standard and application. The most common types of USB PCBs include:
USB 2.0 PCBs
USB 2.0 is the most widely adopted USB standard, released in 2000. It supports data transfer rates up to 480 Mbps. USB 2.0 PCBs are found in a vast array of devices, including:
- Flash drives
- External hard drives
- Computer peripherals (mice, keyboards, etc.)
- Smartphones (for charging and data transfer)
USB 2.0 PCBs typically have a 4-layer stack-up, with power and ground planes for improved signal integrity.
USB 3.0 PCBs
USB 3.0, also known as SuperSpeed USB, was introduced in 2008. It offers significantly higher data transfer rates up to 5 Gbps. USB 3.0 PCBs are commonly found in:
- External solid-state drives (SSDs)
- High-performance external hard drives
- USB 3.0 hubs
- High-resolution webcams
USB 3.0 PCBs often have a 6-layer or 8-layer stack-up to accommodate the additional differential pairs required for SuperSpeed communication.
USB Type-C PCBs
USB Type-C is the latest USB connector standard, designed for reversibility and higher power delivery. USB Type-C PCBs can support various USB protocols, including USB 2.0, USB 3.0, and USB Power Delivery (USB PD). They are increasingly used in:
- Laptops and smartphones
- USB Type-C chargers
- USB Type-C hubs and docking stations
- Thunderbolt 3 devices
USB Type-C PCBs require careful design considerations for signal integrity, power management, and electromagnetic compatibility (EMC).
USB Standard | Max Data Rate | Typical PCB Layers | Common Applications |
---|---|---|---|
USB 2.0 | 480 Mbps | 4 | Flash drives, computer peripherals |
USB 3.0 | 5 Gbps | 6 or 8 | External SSDs, high-performance hard drives |
USB Type-C | Varies* | 4, 6, or 8 | Laptops, smartphones, USB PD chargers |
*USB Type-C supports multiple protocols with different data rates.
USB PCB Design Considerations
Designing a reliable and high-performance USB PCB requires careful consideration of several factors:
Schematic Design
The schematic design is the first step in USB PCB Development. It involves selecting the appropriate USB controller IC, power management components, and connectors based on the target USB standard and application requirements. The schematic should also include necessary protection circuits, such as electrostatic discharge (ESD) protection and voltage regulators.
PCB Layout
The PCB layout is critical for ensuring signal integrity and EMC compliance. Key considerations include:
- Differential pair routing for USB data lines (D+ and D-)
- Controlled impedance traces for USB high-speed signals
- Proper power plane design and decoupling capacitor placement
- Adequate ground plane and stitching vias for reduced EMI
- Connector placement and shielding
- Compliance with USB layout guidelines and recommendations
Power Management
USB PCBs must manage power efficiently to ensure proper device operation and adhere to USB power specifications. This involves:
- Selecting appropriate voltage regulators and power management ICs
- Designing power sequencing circuits for correct power-up and power-down behavior
- Implementing USB power saving modes, such as suspend and resume
- Handling USB power delivery (USB PD) negotiations for Type-C devices
Signal Integrity
Maintaining good signal integrity is essential for reliable USB communication. Signal integrity considerations include:
- Controlling impedance of USB traces (typically 90Ω differential)
- Minimizing crosstalk and interference between USB signals and other circuits
- Proper termination and matching of USB signals
- Simulation and analysis of USB signal integrity using tools like HyperLynx or Sigrity
Electromagnetic Compatibility (EMC)
USB PCBs must comply with EMC regulations to minimize electromagnetic interference (EMI) and ensure compatibility with other electronic devices. EMC considerations include:
- Proper grounding and shielding techniques
- Minimizing loop areas and current return paths
- Filtering and suppression of high-frequency noise
- Compliance with USB-IF EMC guidelines and regional EMC regulations
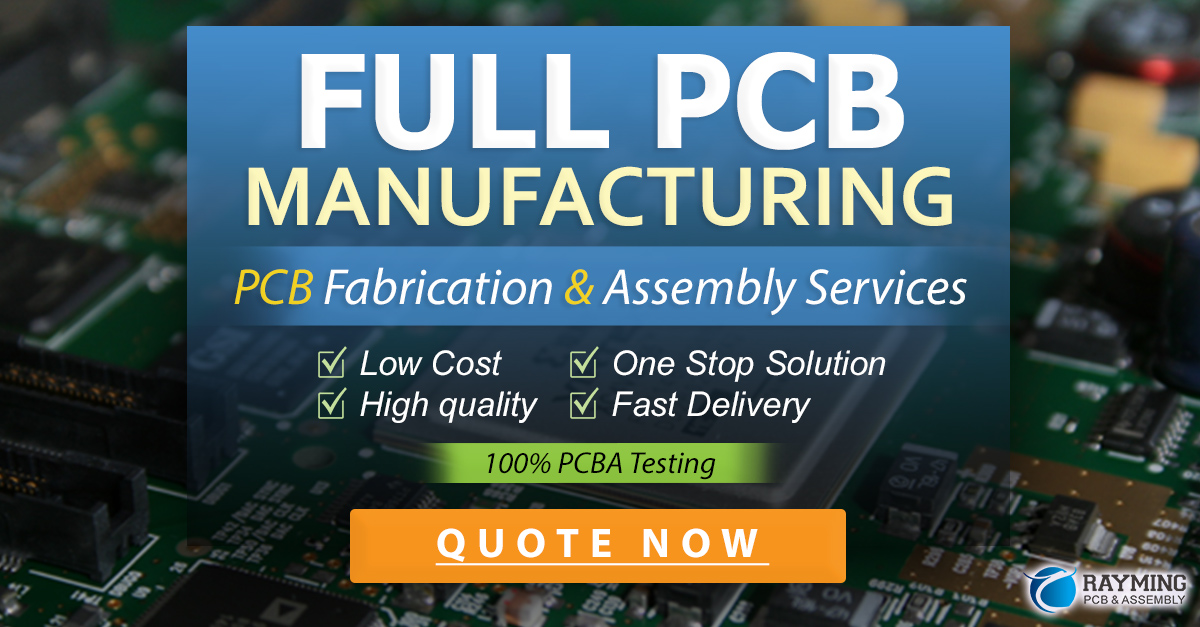
USB PCB Manufacturing Process
The manufacturing process for USB PCBs involves several key steps:
-
PCB Fabrication: The PCB design files are sent to a PCB manufacturer, who fabricates the bare PCB according to the specified layer stack-up, material, and finish requirements.
-
PCB Assembly (PCBA): The fabricated PCB undergoes assembly, where surface mount and through-hole components are soldered onto the board using automated pick-and-place machines and reflow soldering processes.
-
Inspection and Testing: The assembled USB PCB is inspected visually and undergoes automated optical inspection (AOI) to detect any soldering defects or component placement issues. Electrical testing, such as in-circuit testing (ICT) and functional testing, is performed to verify the PCB’s functionality.
-
Conformal Coating and Potting: Depending on the application and environmental requirements, the USB PCB may undergo conformal coating or potting to protect the components and circuitry from moisture, dust, and other contaminants.
-
Final Assembly: The tested and coated USB PCB is then integrated into the final product enclosure and undergoes further system-level testing and validation.
USB PCB Testing and Validation
Thorough testing and validation are critical to ensuring the reliability and compliance of USB PCBs. Key testing and validation steps include:
-
USB Compliance Testing: USB-IF (USB Implementers Forum) provides a comprehensive set of compliance tests to ensure that USB devices meet the USB specifications. These tests cover electrical, protocol, and interoperability aspects of USB communication.
-
Functional Testing: USB PCBs undergo functional testing to verify that they perform the intended functionality, such as data transfer, power management, and device enumeration, as expected.
-
Reliability Testing: USB PCBs are subjected to various reliability tests to ensure their robustness and durability. These tests may include:
- Environmental stress testing (temperature, humidity, vibration, shock)
- Accelerated life testing
- Connector mating and unmating cycles
-
Electrostatic discharge (ESD) testing
-
Interoperability Testing: USB PCBs are tested for interoperability with a wide range of USB hosts and devices to ensure seamless compatibility and user experience.
-
EMC Testing: USB PCBs must pass electromagnetic compatibility (EMC) tests to ensure they do not cause electromagnetic interference and can operate reliably in the presence of external electromagnetic disturbances.
Conclusion
USB PCBs play a crucial role in enabling USB connectivity and functionality in countless electronic devices we use every day. From schematics to layout, power management to signal integrity, and manufacturing to testing, every aspect of USB PCB development requires careful consideration and adherence to USB specifications and best practices.
As USB technology continues to evolve with higher data rates, more versatile power delivery, and innovative form factors, the importance of well-designed and thoroughly tested USB PCBs will only continue to grow. By understanding the intricacies of USB PCBs, engineers and designers can create robust and reliable USB devices that meet the ever-increasing demands of the digital age.
Frequently Asked Questions (FAQ)
1. What is the difference between USB 2.0 and USB 3.0 PCBs?
USB 3.0 PCBs support much higher data transfer rates (up to 5 Gbps) compared to USB 2.0 PCBs (480 Mbps). USB 3.0 PCBs also require additional differential pairs for SuperSpeed communication and often have more layers in the PCB Stack-up to accommodate these signals.
2. Why is PCB layout critical for USB devices?
PCB layout is critical for USB devices because it directly impacts signal integrity, power integrity, and electromagnetic compatibility. Proper layout techniques, such as controlled impedance routing, power plane design, and grounding, are essential for ensuring reliable USB communication and compliance with USB specifications.
3. What is USB Type-C, and how does it differ from previous USB connectors?
USB Type-C is a reversible connector standard that supports various USB protocols, including USB 2.0, USB 3.0, and USB Power Delivery (USB PD). It differs from previous USB connectors by its symmetrical design, higher power delivery capabilities, and ability to support alternate modes, such as DisplayPort and Thunderbolt 3.
4. What are some common challenges in USB PCB design?
Common challenges in USB PCB design include maintaining signal integrity at high data rates, managing power efficiency and power delivery, ensuring electromagnetic compatibility (EMC), and complying with USB layout guidelines and specifications. Designers must also consider the specific requirements of the target USB standard and application.
5. How can I ensure my USB PCB is compliant with USB specifications?
To ensure compliance with USB specifications, follow these steps:
- Adhere to USB-IF layout guidelines and recommendations for your target USB standard.
- Perform rigorous simulations and analyses of signal integrity, power integrity, and EMC.
- Conduct comprehensive testing, including compliance testing, functional testing, reliability testing, and interoperability testing.
- Participate in USB-IF compliance programs and obtain certification for your USB device.
By following these guidelines and best practices, you can develop a robust and compliant USB PCB that meets the stringent requirements of the USB ecosystem.
Leave a Reply