Introduction to LED Grow Light PCBs
LED grow lights have revolutionized the indoor gardening industry by providing an efficient and effective way to cultivate plants in controlled environments. At the heart of these lighting systems are the printed circuit boards (PCBs) that power and control the LED components. In this comprehensive guide, we will delve into the intricacies of LED grow light PCB manufacturing, exploring the key aspects that contribute to the production of high-quality and reliable PCBs.
What are LED Grow Light PCBs?
LED grow light PCBs are specially designed circuit boards that serve as the backbone of LED grow light systems. These PCBs house the LED components, drivers, and other electronic components necessary for the proper functioning of the grow lights. They are engineered to withstand the harsh conditions of indoor growing environments, such as high humidity, temperature fluctuations, and constant exposure to light.
Benefits of LED Grow Light PCBs
The use of PCBs in LED grow lights offers several advantages over traditional lighting methods:
-
Efficiency: LED grow light PCBs enable the precise control and distribution of electrical current to the LED components, ensuring optimal light output and energy efficiency.
-
Durability: PCBs are designed to be robust and resistant to environmental factors, making them ideal for use in indoor growing settings.
-
Customization: PCBs can be customized to accommodate specific LED configurations, allowing for the creation of tailored lighting solutions for different plant species and growth stages.
-
Compact Design: The integration of components onto a single PCB reduces the overall size and weight of the grow light system, making it more compact and easier to install.
PCB Design Considerations for LED Grow Lights
Choosing the Right PCB Material
The choice of PCB material is crucial for the performance and longevity of LED grow lights. The most common materials used in LED grow light PCBs are:
Material | Characteristics | Applications |
---|---|---|
FR-4 | Cost-effective, good insulation properties | General-purpose LED grow lights |
Aluminum PCB | Excellent thermal conductivity, lightweight | High-power LED grow lights |
Copper PCB | High electrical conductivity, good thermal management | High-current LED grow lights |
When selecting the PCB material, factors such as thermal management, electrical requirements, and cost should be taken into consideration.
Thermal Management
Effective thermal management is essential for LED grow light PCBs to prevent overheating and ensure optimal performance. Several techniques can be employed to dissipate heat generated by the LED components:
-
Copper Pours: Incorporating large copper pours on the PCB helps to distribute heat evenly across the board and improve thermal conductivity.
-
Thermal Vias: Placing thermal vias strategically around the LED components allows heat to be transferred from the top layer to the bottom layer of the PCB, enhancing heat dissipation.
-
Heatsinks: Attaching heatsinks to the PCB or integrating them into the design helps to absorb and dissipate heat away from the LED components.
LED Component Selection
The choice of LED components is critical for the performance and efficiency of LED grow lights. When selecting LEDs for PCB integration, consider the following factors:
-
Wavelength: Different plants require specific wavelengths of light for optimal growth. Choose LEDs that emit the appropriate wavelengths for the targeted plant species.
-
Intensity: The light intensity, measured in photosynthetic photon flux density (PPFD), should be sufficient for the desired plant growth stage.
-
Efficiency: Opt for high-efficiency LEDs to maximize light output while minimizing power consumption.
-
Reliability: Select LED components from reputable manufacturers to ensure reliability and longevity.
PCB Manufacturing Process for LED Grow Lights
PCB Fabrication
The PCB fabrication process involves several steps:
-
PCB Design: The PCB layout is designed using specialized software, taking into account the placement of components, routing of traces, and thermal management considerations.
-
Printing: The PCB design is printed onto a photoresist layer on the copper-clad laminate.
-
Etching: The exposed copper areas are etched away, leaving behind the desired circuit pattern.
-
Drilling: Holes are drilled into the PCB for component placement and mounting.
-
Plating: The PCB undergoes a plating process to add a layer of protection and improve conductivity.
-
Solder Mask Application: A solder mask is applied to the PCB to insulate and protect the copper traces.
-
Silkscreen Printing: The component labels and other markings are printed onto the PCB using silkscreen printing.
PCB Assembly
Once the PCB fabrication is complete, the next step is to assemble the components onto the board. The PCB assembly process typically involves the following steps:
-
Solder Paste Application: Solder paste is applied to the PCB pads using a stencil or screen printing method.
-
Component Placement: The LED components, drivers, and other electronic components are placed onto the PCB using automated pick-and-place machines or manual placement.
-
Reflow Soldering: The PCB is subjected to a reflow soldering process, where the solder paste melts and forms a secure connection between the components and the PCB pads.
-
Inspection: The assembled PCB undergoes visual inspection and automated optical inspection (AOI) to detect any defects or misalignments.
-
Testing: The LED grow light PCB is tested for functionality, ensuring that all components are working correctly and the light output meets the specified requirements.
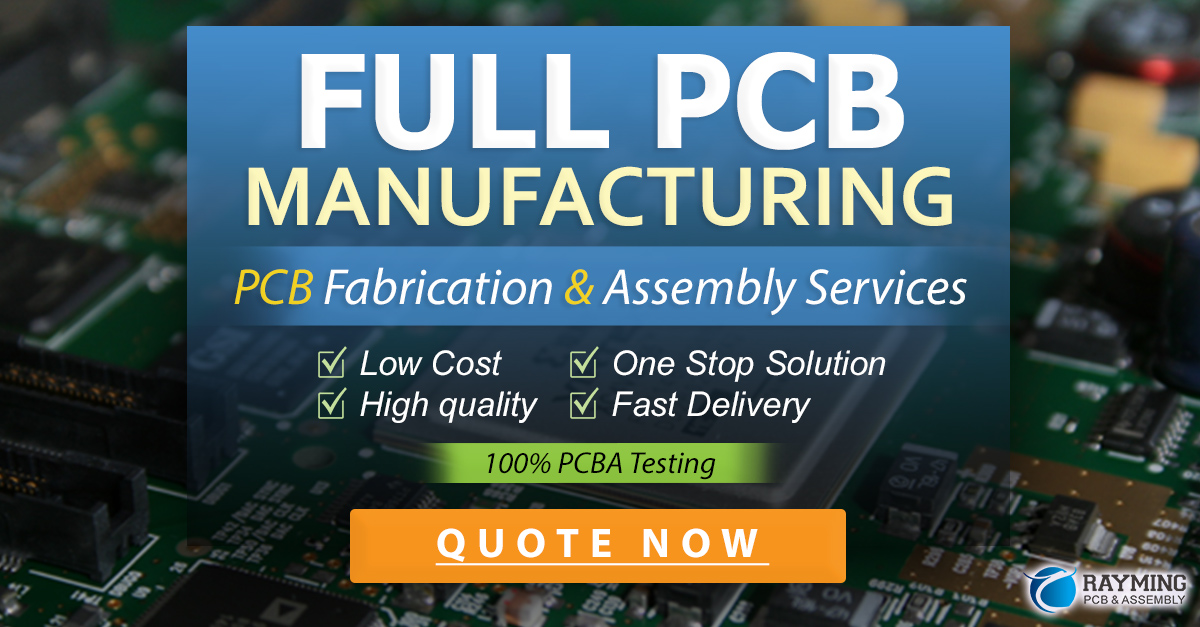
Quality Control and Testing
To ensure the reliability and performance of LED grow light PCBs, rigorous quality control measures and testing procedures are implemented throughout the manufacturing process.
Visual Inspection
Visual inspection is performed at various stages of PCB fabrication and assembly to identify any visible defects, such as scratches, cracks, or missing components. This process can be done manually or using automated optical inspection (AOI) systems.
Automated Optical Inspection (AOI)
AOI systems use high-resolution cameras and advanced image processing algorithms to detect and analyze PCB defects. These systems can identify issues such as component misalignment, solder bridges, and missing or incorrect components.
Functional Testing
Functional testing is conducted to verify that the LED grow light PCB operates as intended. This involves powering up the PCB and measuring the light output, power consumption, and other critical parameters. Functional testing helps to identify any performance issues or defects that may not be visible during visual inspection.
Burn-In Testing
Burn-in testing involves running the LED grow light PCB under normal operating conditions for an extended period to identify any early failures or performance degradation. This process helps to weed out any PCBs that may have latent defects or weaknesses.
Troubleshooting and Maintenance
Despite rigorous quality control measures, issues may arise with LED grow light PCBs during operation. Common problems include:
-
LED Failure: Individual LED components may fail due to manufacturing defects, overheating, or electrical stress.
-
Driver Issues: LED drivers may malfunction, causing flickering, dimming, or complete failure of the grow lights.
-
Connectivity Problems: Poor solder joints or damaged traces can lead to intermittent or complete loss of connectivity between components.
To troubleshoot and maintain LED grow light PCBs, consider the following tips:
-
Regular Inspections: Periodically inspect the PCBs for any signs of damage, corrosion, or component failure.
-
Proper Cleaning: Clean the PCBs regularly to remove any dust, debris, or moisture that may accumulate over time.
-
Timely Repairs: If any issues are identified, address them promptly to prevent further damage or performance degradation.
-
Adequate Cooling: Ensure that the grow light system has proper ventilation and cooling to prevent overheating of the PCBs and components.
FAQ
-
What is the typical lifespan of an LED grow light PCB?
The lifespan of an LED grow light PCB depends on various factors, such as the quality of components, thermal management, and operating conditions. On average, a well-designed and maintained PCB can last between 50,000 to 100,000 hours. -
Can I customize the LED configuration on a grow light PCB?
Yes, LED grow light PCBs can be customized to accommodate specific LED configurations based on the desired light spectrum, intensity, and coverage area. Manufacturers can work with you to design a PCB that meets your specific requirements. -
How often should I replace my LED grow light PCBs?
The replacement frequency of LED grow light PCBs depends on their performance and condition. If you notice a significant decrease in light output, inconsistent performance, or visible damage to the PCB, it may be time to consider a replacement. -
Can I repair a damaged LED grow light PCB?
In some cases, minor issues such as loose connections or damaged components can be repaired. However, attempting to repair a PCB without proper knowledge and tools can cause further damage. It is generally recommended to seek professional assistance or replace the PCB if it is severely damaged. -
How can I ensure the longevity of my LED grow light PCBs?
To maximize the lifespan of your LED grow light PCBs, follow these best practices: - Ensure proper thermal management to prevent overheating
- Use high-quality components from reputable manufacturers
- Regularly inspect and clean the PCBs
- Operate the grow lights within the recommended parameters
- Provide adequate ventilation and cooling for the entire grow light system
Conclusion
LED grow light PCB manufacturing is a complex process that involves careful design, material selection, fabrication, assembly, and testing. By understanding the key considerations and best practices involved in PCB manufacturing, you can ensure the production of high-quality and reliable LED grow light PCBs that meet the specific requirements of your indoor growing application.
From choosing the right PCB material and LED components to implementing effective thermal management and quality control measures, each step of the manufacturing process plays a crucial role in determining the performance and longevity of the final product.
By working with experienced PCB manufacturers and following the guidelines outlined in this ultimate guide, you can unlock the full potential of LED grow light technology and achieve optimal results in your indoor growing endeavors.
Leave a Reply