Introduction to Aluminum PCB Boards
Aluminum PCB (Printed Circuit Board) is a type of PCB that uses aluminum as the base material instead of the traditional FR-4 (Flame Retardant-4) or other materials. Aluminum PCBs have gained popularity in recent years due to their unique properties and advantages over traditional PCBs. In this comprehensive guide, we will explore the properties, manufacturing process, applications, and frequently asked questions about aluminum PCB boards.
What is an Aluminum PCB?
An aluminum PCB is a printed circuit board that uses aluminum as the base material for the substrate. The aluminum substrate is typically covered with a thin layer of dielectric material, such as polyimide or epoxy, which acts as an insulator between the aluminum and the copper traces. The copper traces are then etched onto the dielectric layer to create the desired circuit pattern.
Advantages of Aluminum PCBs
Aluminum PCBs offer several advantages over traditional PCBs:
-
Excellent thermal conductivity: Aluminum has a high thermal conductivity, which means it can dissipate heat more efficiently than FR-4 or other materials. This makes aluminum PCBs ideal for applications that generate a lot of heat, such as power electronics and LED lighting.
-
Lightweight: Aluminum is a lightweight material compared to other metals, which makes aluminum PCBs lighter than traditional PCBs. This is particularly useful in applications where weight is a critical factor, such as aerospace and automotive industries.
-
High strength and durability: Aluminum is a strong and durable material that can withstand harsh environments and mechanical stress. This makes aluminum PCBs more resistant to vibration, shock, and other physical stresses than traditional PCBs.
-
Cost-effective: Aluminum is a relatively inexpensive material compared to other metals, which makes aluminum PCBs more cost-effective than traditional PCBs, especially for high-volume production.
Disadvantages of Aluminum PCBs
Despite their many advantages, aluminum PCBs also have some disadvantages:
-
Limited flexibility: Aluminum is a rigid material, which means aluminum PCBs are less flexible than traditional PCBs. This can be a problem in applications that require a certain degree of flexibility, such as wearable devices.
-
Difficult to solder: Aluminum is a difficult material to solder due to its high thermal conductivity and oxidation properties. This can make the assembly process more challenging and require specialized equipment and techniques.
-
Limited electrical insulation: The dielectric layer used in aluminum PCBs is typically thinner than in traditional PCBs, which can limit the electrical insulation properties of the board. This can be a problem in high-voltage applications or in environments with high electromagnetic interference (EMI).
Manufacturing Process of Aluminum PCBs
The manufacturing process of aluminum PCBs is similar to that of traditional PCBs, with some additional steps and considerations:
-
Substrate preparation: The aluminum substrate is cleaned and treated to remove any impurities and improve adhesion of the dielectric layer.
-
Dielectric layer application: The dielectric layer, typically polyimide or epoxy, is applied to the aluminum substrate using a lamination process. The thickness of the dielectric layer can vary depending on the application and the required electrical insulation properties.
-
Copper foil lamination: A thin layer of copper foil is laminated onto the dielectric layer using heat and pressure. The thickness of the copper foil can vary depending on the current carrying requirements of the circuit.
-
Circuit patterning: The desired circuit pattern is transferred onto the copper foil using a photolithography process. The unwanted copper is then etched away using a chemical etching process, leaving only the desired circuit pattern.
-
Drilling and plating: Holes are drilled through the aluminum PCB to create vias and other interconnections. The holes are then plated with copper to create electrical connections between the layers.
-
Surface finishing: The exposed copper traces are coated with a protective layer, such as HASL (Hot Air Solder Leveling), ENIG (Electroless Nickel Immersion Gold), or OSP (Organic Solderability Preservative), to prevent oxidation and improve solderability.
-
Solder mask and silkscreen: A solder mask layer is applied to the surface of the aluminum PCB to protect the copper traces and prevent short circuits. A silkscreen layer is then applied to add component designators, logos, and other markings.
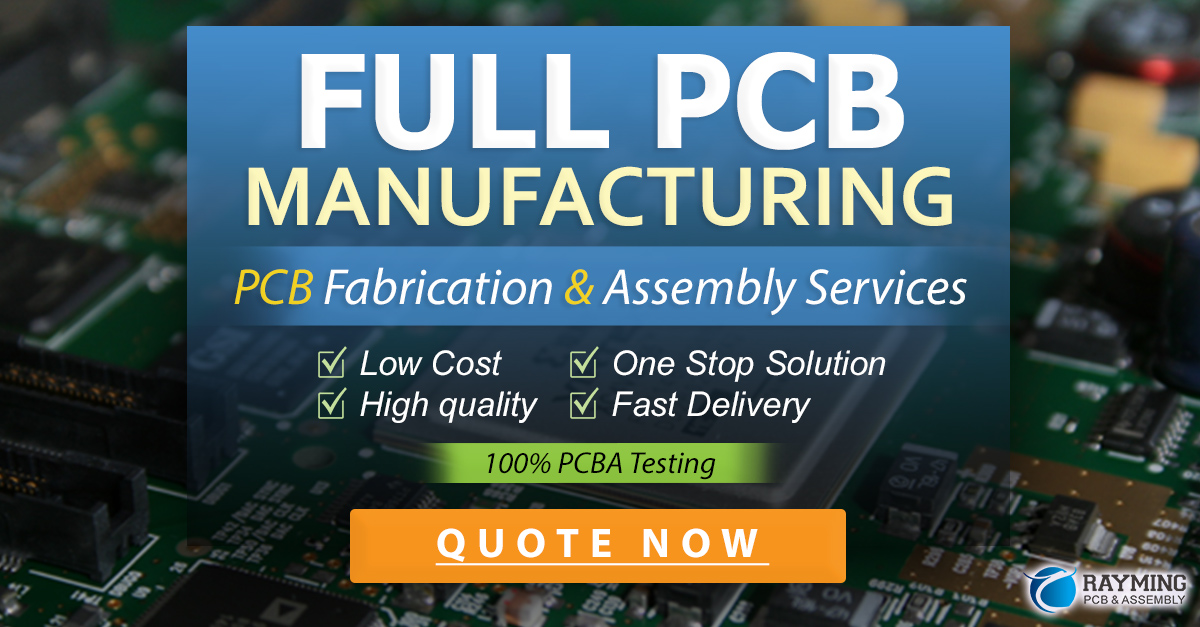
Applications of Aluminum PCBs
Aluminum PCBs are used in a wide range of applications, particularly those that require high thermal conductivity, lightweight design, or high strength and durability:
Power Electronics
Aluminum PCBs are commonly used in power electronics applications, such as:
- Power supplies
- Motor controllers
- Inverters
- Battery management systems
The high thermal conductivity of aluminum PCBs helps to dissipate heat generated by power components, such as MOSFETs, IGBTs, and diodes, which can improve the efficiency and reliability of the system.
LED Lighting
Aluminum PCBs are also used in LED lighting applications, such as:
- LED bulbs
- LED strips
- LED modules
- LED displays
The high thermal conductivity of aluminum PCBs helps to dissipate heat generated by the LEDs, which can improve the luminous efficiency and lifespan of the system. Additionally, the lightweight and high strength properties of aluminum PCBs make them ideal for applications that require a compact and durable design.
Automotive and Aerospace
Aluminum PCBs are used in automotive and aerospace applications that require high reliability and durability, such as:
- Engine control units (ECUs)
- Transmission control modules (TCMs)
- Airbag control modules
- Avionics systems
The high strength and durability of aluminum PCBs make them resistant to vibration, shock, and other physical stresses that are common in these applications. Additionally, the lightweight properties of aluminum PCBs can help to reduce the overall weight of the system, which is critical in aerospace applications.
Industrial and Medical
Aluminum PCBs are also used in industrial and medical applications that require high reliability and durability, such as:
- Industrial control systems
- Robotics and automation
- Medical imaging equipment
- Medical monitoring devices
The high thermal conductivity and strength of aluminum PCBs make them suitable for applications that generate a lot of heat or are subject to harsh environments. Additionally, the cost-effectiveness of aluminum PCBs makes them attractive for high-volume production in these industries.
Frequently Asked Questions (FAQ)
1. Can aluminum PCBs be used in high-frequency applications?
Aluminum PCBs can be used in high-frequency applications, but their performance may be limited compared to traditional PCBs. The high thermal conductivity of aluminum can cause signal integrity issues at high frequencies, such as increased insertion loss and crosstalk. Additionally, the thinner dielectric layer used in aluminum PCBs can limit their ability to handle high-frequency signals. However, these issues can be mitigated through careful design and material selection.
2. How do aluminum PCBs compare to copper PCBs in terms of cost?
Aluminum PCBs are generally more cost-effective than copper PCBs, especially for high-volume production. The raw material cost of aluminum is lower than that of copper, and the manufacturing process for aluminum PCBs is similar to that of traditional PCBs, which means that existing equipment and processes can be used. However, the cost advantage of aluminum PCBs may be offset by the additional processing steps required, such as surface treatment and plating.
3. Can aluminum PCBs be used in flexible applications?
Aluminum PCBs are generally not suitable for flexible applications due to the rigidity of the aluminum substrate. However, there are some specialized aluminum PCBs that use a thin aluminum substrate and a flexible dielectric layer, such as polyimide, to achieve a certain degree of flexibility. These flexible aluminum PCBs are used in applications that require both thermal management and flexibility, such as wearable devices and automotive electronics.
4. How do aluminum PCBs handle thermal expansion?
Aluminum has a higher coefficient of thermal expansion (CTE) than traditional PCB materials, such as FR-4. This means that aluminum PCBs can experience more thermal stress and warpage than traditional PCBs, especially in applications with large temperature variations. To mitigate this issue, aluminum PCBs often use a dielectric layer with a similar CTE to aluminum, such as polyimide or epoxy. Additionally, the design of the aluminum PCB can be optimized to minimize thermal stress, such as by using a symmetric stack-up or incorporating stress-relief features.
5. Can aluminum PCBs be recycled?
Yes, aluminum PCBs can be recycled more easily than traditional PCBs. Aluminum is a highly recyclable material, and the recycling process for aluminum PCBs is simpler and more cost-effective than for traditional PCBs. The aluminum substrate can be separated from the other materials, such as copper and dielectric, and then melted down and reused in other applications. This makes aluminum PCBs a more environmentally friendly option than traditional PCBs, which can be difficult and expensive to recycle due to the presence of hazardous materials, such as lead and brominated flame retardants.
Conclusion
Aluminum PCBs offer a unique set of properties and advantages over traditional PCBs, making them suitable for a wide range of applications that require high thermal conductivity, lightweight design, or high strength and durability. While aluminum PCBs have some disadvantages, such as limited flexibility and difficulty in soldering, these can be mitigated through careful design and material selection.
As the demand for high-performance electronics continues to grow, aluminum PCBs are likely to play an increasingly important role in the industry. Their cost-effectiveness, environmental friendliness, and unique properties make them an attractive option for manufacturers looking to optimize their products and stay competitive in the market.
Property | Aluminum PCB | Traditional FR-4 PCB |
---|---|---|
Thermal Conductivity | High | Low |
Weight | Lightweight | Heavy |
Strength and Durability | High | Moderate |
Flexibility | Limited | Moderate |
Solderability | Difficult | Easy |
Electrical Insulation | Limited | High |
Cost | Cost-effective | Moderate to High |
Recyclability | High | Low |
In summary, aluminum PCBs offer a compelling alternative to traditional PCBs in applications that prioritize thermal management, weight reduction, and durability. As the technology continues to evolve and mature, we can expect to see even more innovative applications and designs that leverage the unique properties of aluminum PCBs.
Leave a Reply