What is Component Tombstoning?
Component tombstoning, also known as “chip tombstoning” or “tombstone effect”, is a defect that can occur during the surface mount assembly process where a component lifts up at one end, resembling a tombstone. This defect prevents proper electrical connection and renders the entire circuit board unusable.
Tombstoning typically affects small, lightweight, 2-terminal surface mount devices (SMDs) such as chip resistors and capacitors. The smaller the component size, the higher the risk of tombstoning.
Common components affected by tombstoning:
Component | Size Range |
---|---|
Chip resistors | 0201 to 1206 |
Chip capacitors | 0201 to 1206 |
Inductors | 0201 to 0603 |
LEDs | 0402 to 0603 |
Diodes | SOD-323 to SOD-123 |
What Causes Components to Tombstone?
Several factors can contribute to component tombstoning during the solder reflow process. Understanding the root causes is key to preventing this defect.
Uneven Heating of Component Terminations
The primary cause of tombstoning is uneven heating and solder Wetting of the component’s terminations or pads. If one end of the component heats up and wets with solder before the other end, the surface tension of the molten solder can pull the component up into a near vertical position.
Factors that can lead to uneven component heating include:
- Dissimilar thermal mass of solder pads
- Unequal amounts of solderable surface on pads
- Uneven application of Solder Paste
- Poor oven profiling with rapid temperature ramp rates
Unbalanced Solder Paste Deposits
If significantly more solder paste is deposited on one pad versus the other, the extra volume of molten solder can exert a stronger pull force and lift the component. Uneven solder deposits are usually caused by issues with the stencil design or solder paste printing process.
Common solder paste deposition issues include:
- Improper aperture size or shape on stencil
- Stencil apertures not centered over pads
- Poor gasketing between stencil and PCB
- Worn or damaged stencils
- Improper squeegee pressure and speed
- Solder paste viscosity and rheology issues
Component Placement Errors
Improper placement of the component during the pick-and-place operation can also increase the risk of tombstoning. If the component is askew or off-center relative to the pads, one termination may touch its pad and wet with solder before the other, resulting in uneven forces.
Component placement issues are often due to:
- Incorrect pick-and-place machine settings (pressure, height, speed, etc.)
- Worn or damaged pickup nozzles
- Component tape feeding problems
- Incorrect CAD centroid data
- PCB support and clamping issues
PCB Layout and Design Factors
Certain PCB design choices can make components more susceptible to tombstoning. For example:
- Unequal pad sizes
- Excessive pad spacing relative to component size
- Unsuitable pad shape (roundness)
- Inadequate solder mask clearance
- Traces too close to pads
- Vias in pad
Component and Packaging Issues
Characteristics of the component itself and its packaging may also promote tombstoning, such as:
- Nonuniform component termination plating (tin, silver, etc.)
- Oxidation or contamination on termination surfaces
- Bent or misaligned component terminations
- Inconsistent component placement in tape pockets
- Improper cover tape sealing
How to Prevent Component Tombstoning
Fortunately, tombstoning can be prevented or minimized by implementing good design and manufacturing practices:
Optimize PCB Footprint Design
- Ensure solder pads are equal in size and shape
- Avoid excessively large or small pad spacings
- Use “teardrop” or rounded pad shapes to promote even solder wetting
- Provide adequate solder mask clearance around pads
- Avoid placing vias and traces too close to pads
Control Solder Paste Deposition
- Optimize stencil aperture dimensions for even paste deposits
- Ensure apertures are centered over pads
- Maintain stencils in good condition
- Use proper squeegee pressure, speed, and material
- Monitor paste properties (viscosity, tackiness, etc.)
Improve Component Placement Accuracy
- Optimize pick-and-place machine settings
- Regularly maintain machines and pickup nozzles
- Ensure component tapes are loaded correctly
- Verify CAD centroid data matches component footprints
- Provide proper support for PCBs during placement
Adjust Reflow Profile
- Use thermocouples to accurately profile ovens
- Avoid excessively high ramp rates and peak temperatures
- Ensure even heating across PCB surface
- Optimize TAL (time above liquidus) for solder paste
Inspect Incoming Components
- Verify uniform termination plating and dimensions
- Check for bent or skewed terminations
- Look for signs of oxidation or contamination
- Ensure components are seated properly in tape pockets
- Avoid using expired or improperly stored components
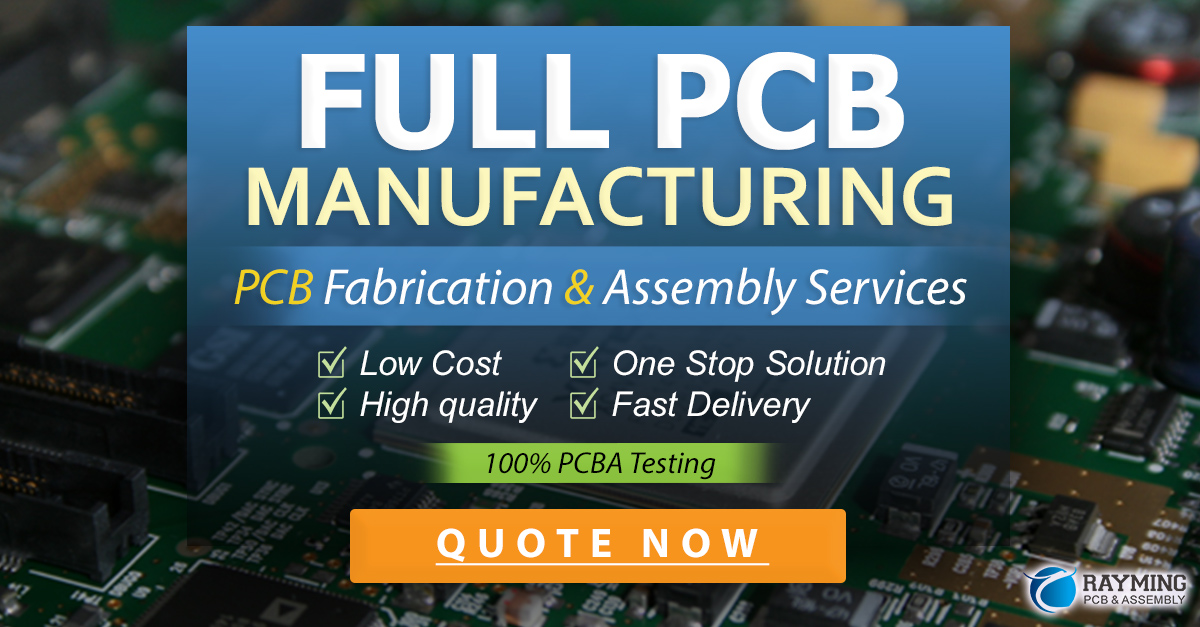
Frequently Asked Questions
What is the most common cause of tombstoning?
Uneven heating and solder wetting of the component terminations is the primary cause of tombstoning. If one termination wets with solder before the other, the surface tension of the molten solder can pull the component into a vertical position.
What component sizes are most affected by tombstoning?
In general, the smaller the component size, the higher the risk of tombstoning. Chip components in the 0201 to 0603 size range are most susceptible. Larger components are less likely to tombstone due to their greater mass.
Can tombstoning be fixed after reflow?
Once a component has tombstoned, it is very difficult to repair. Removal and replacement of the component is usually necessary. In some cases, the defect may be correctable by careful reheating and nudging the component back into place, but this is not always reliable. Prevention is the best strategy.
How can PCB design minimize tombstoning?
Proper footprint design is important for minimizing tombstoning risk. Use equal sized solder pads with rounded shapes to promote even solder wetting. Provide adequate solder mask clearance around pads. Avoid placing vias, traces, or other features too close to the pads.
What role does solder paste play in tombstoning?
Solder paste is a major factor in tombstoning. Uneven paste deposition can lead to unbalanced solder volumes on component pads. The stencil design, aperture dimensions, and solder paste printing process must be optimized to ensure uniform deposits. Solder paste properties like viscosity and tackiness also play a role.
Conclusion
Component tombstoning is a challenging defect in surface mount assembly that can lead to costly rework and scrap. By understanding the causes of tombstoning, designers and manufacturers can take steps to prevent or minimize its occurrence.
Effective tombstone prevention requires a holistic approach considering PCB design, solder paste printing, component placement, and Reflow Soldering parameters. Optimizing footprint layouts, controlling solder deposition, improving placement accuracy, and adjusting reflow profiles are key strategies.
With proper process controls and best practices, the risk of component tombstoning can be significantly reduced, leading to higher yields and more reliable circuit board assemblies.
Leave a Reply