Introduction
Through-hole technology has been a staple in printed circuit board (PCB) design and manufacturing for decades. Despite the rise of surface mount technology (SMT), through-hole components and assembly methods remain relevant and widely used in various applications. In this article, we will explore the reasons behind the continued relevance of through-hole technology in PCB designs.
What is Through-Hole Technology?
Through-hole technology refers to the method of mounting electronic components on a PCB by inserting their leads through drilled holes in the board and soldering them on the opposite side. The components used in through-hole assembly typically have long leads that are inserted into the holes, allowing for a secure mechanical and electrical connection.
Advantages of Through-Hole Technology
- Mechanical Strength
- Through-hole components provide a stronger mechanical bond to the PCB compared to surface-mounted components.
-
The leads of through-hole components are inserted through the board and soldered on the opposite side, creating a robust connection that can withstand physical stress and vibrations.
-
Ease of Manual Assembly
- Through-hole components are easier to handle and assemble manually compared to their surface-mount counterparts.
-
The larger size and longer leads of through-hole components make them more suitable for hand soldering and prototyping.
-
Reliability in Harsh Environments
- Through-hole components are often preferred in applications that are exposed to harsh environments, such as high temperatures, vibrations, or mechanical shocks.
-
The stronger mechanical bond provided by through-hole mounting enhances the reliability and durability of the PCB Assembly in these conditions.
-
Higher Power Handling Capability
- Through-hole components generally have higher power handling capabilities compared to surface-mount components.
- The larger size and greater lead cross-sectional area of through-hole components allow them to dissipate heat more effectively and handle higher currents.
Disadvantages of Through-Hole Technology
- Larger PCB Size
- Through-hole components require drilling holes in the PCB, which occupies more board space compared to surface-mount components.
-
The larger size of through-hole components and the need for drilled holes result in a larger overall PCB size.
-
Higher Manufacturing Costs
- Through-hole assembly involves additional steps, such as drilling holes and manual insertion of components, which increase manufacturing costs.
-
The manual labor required for through-hole assembly can be more time-consuming and expensive compared to automated SMT assembly processes.
-
Limited Component Density
- Due to the larger size of through-hole components and the required hole spacing, the component density on a Through-hole PCB is lower compared to SMT designs.
- This limitation can be a disadvantage in applications that require high component density and miniaturization.
Applications of Through-Hole Technology
Despite the advantages of surface mount technology, through-hole components and assembly methods remain relevant in various applications. Let’s explore some of the common applications where through-hole technology is still widely used.
1. Power Electronics
In power electronics applications, such as power supplies, Motor Controllers, and high-current circuits, through-hole components are often preferred due to their higher power handling capabilities and better heat dissipation properties. The larger size and lead cross-sectional area of through-hole components allow them to handle higher currents and withstand higher temperatures compared to surface-mount alternatives.
2. Automotive Electronics
The automotive industry relies on through-hole technology for certain applications due to its reliability and durability in harsh environments. Through-hole components provide a stronger mechanical bond to the PCB, making them more resistant to vibrations and mechanical shocks commonly encountered in automotive systems. Additionally, through-hole technology is often used for connectors and high-power components in automotive electronics.
3. Industrial Control Systems
Industrial control systems, such as programmable logic controllers (PLCs), industrial automation equipment, and process control systems, often employ through-hole technology. These systems require robust and reliable PCB assemblies that can withstand harsh industrial environments, including extreme temperatures, vibrations, and exposure to dust and moisture. Through-hole components offer the necessary mechanical strength and durability to ensure the longevity and reliability of industrial control systems.
4. Prototype and Low-Volume Production
Through-hole technology remains a popular choice for prototype development and low-volume production runs. The ease of manual assembly and the ability to hand-solder through-hole components make them well-suited for quick prototyping and small batch manufacturing. Engineers and hobbyists often rely on through-hole components for initial circuit design and testing before transitioning to surface mount technology for mass production.
5. Educational and Hobbyist Projects
In educational settings and hobbyist projects, through-hole components are commonly used due to their ease of handling and assembly. Through-hole components are larger and more visible, making them easier for beginners to work with and understand. Many educational kits, such as Arduino and Raspberry Pi, include through-hole components to facilitate learning and experimentation.
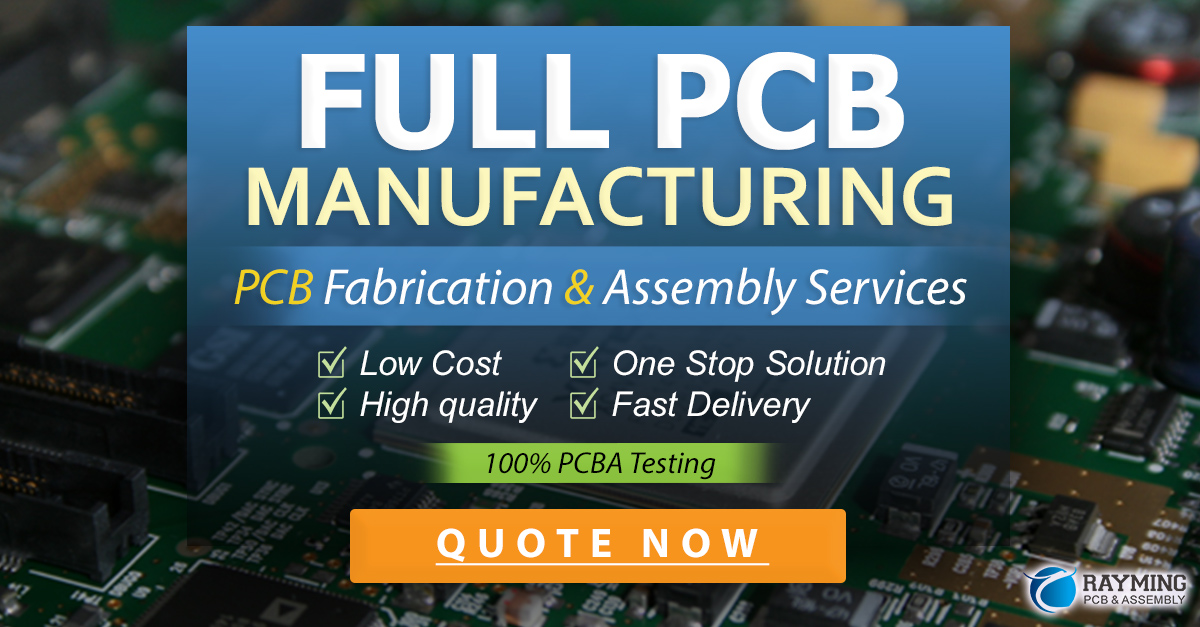
Comparison of Through-Hole and Surface Mount Technology
To understand the continued relevance of through-hole technology, it’s essential to compare it with surface mount technology (SMT). The following table highlights the key differences between through-hole and SMT:
Characteristic | Through-Hole Technology | Surface Mount Technology |
---|---|---|
Component Size | Larger | Smaller |
PCB Space Utilization | Less efficient | More efficient |
Component Density | Lower | Higher |
Assembly Method | Manual or Wave soldering | Automated pick-and-place |
Manufacturing Cost | Higher | Lower |
Mechanical Strength | Stronger | Weaker |
Heat Dissipation | Better | Limited |
Rework and Repair | Easier | More challenging |
While SMT offers advantages such as smaller component size, higher component density, and lower manufacturing costs, through-hole technology still holds its ground in certain applications due to its superior mechanical strength, better heat dissipation, and ease of manual assembly and rework.
Best Practices for Through-Hole PCB Design
When designing a PCB that incorporates through-hole components, consider the following best practices to ensure optimal performance and manufacturability:
- Hole Size and Pad Diameter
- Choose appropriate hole sizes and pad diameters based on the lead diameter of the through-hole components.
-
Ensure sufficient clearance between the hole and the lead to allow for proper soldering and prevent mechanical stress.
-
Component Placement
- Place through-hole components in a way that minimizes the distance between them to reduce the overall PCB size.
-
Consider the orientation and spacing of components to facilitate manual assembly and soldering.
-
Soldering Considerations
- Provide adequate space around through-hole components for soldering and inspection.
-
Ensure proper soldering techniques are used to create reliable and strong solder joints.
-
Thermal Management
- Consider the power dissipation requirements of through-hole components and provide sufficient copper area for heat dissipation.
-
Use thermal relief pads or vias to enhance heat transfer from the component to the PCB.
-
Manufacturing Considerations
- Communicate clearly with the PCB manufacturer about the specific requirements for through-hole components, such as hole sizes, pad dimensions, and soldering preferences.
- Provide comprehensive assembly instructions and guidelines to ensure proper handling and assembly of through-hole components.
Frequently Asked Questions (FAQ)
-
Q: Can through-hole and surface mount components be used together on the same PCB?
A: Yes, it is common to have a mix of through-hole and surface mount components on the same PCB, known as a mixed-technology PCB. This approach allows designers to leverage the advantages of both technologies based on the specific requirements of different components. -
Q: Are through-hole components becoming obsolete?
A: While surface mount technology has become more prevalent, through-hole components are not becoming obsolete. They continue to be used in various applications where their specific advantages, such as mechanical strength and power handling, are required. However, the overall trend is towards increased adoption of surface mount technology. -
Q: Can through-hole PCBs be assembled using automated processes?
A: Yes, through-hole PCBs can be assembled using automated processes, such as wave soldering or selective soldering. However, the level of automation is typically lower compared to surface mount assembly, and manual intervention may still be required for certain components or assembly steps. -
Q: Are through-hole components more expensive than surface mount components?
A: In general, through-hole components tend to be less expensive than their surface mount counterparts due to their simpler packaging and manufacturing processes. However, the overall cost of a through-hole PCB assembly may be higher due to the additional manufacturing steps and manual labor involved. -
Q: What are some common through-hole components?
A: Common through-hole components include: - Resistors
- Capacitors
- Inductors
- Diodes
- Transistors
- Integrated Circuits (DIPs)
- Connectors
- Switches
- LEDs
Conclusion
In conclusion, through-hole technology remains relevant in PCB designs due to its unique advantages, such as mechanical strength, reliability in harsh environments, and ease of manual assembly. While surface mount technology has become the dominant choice for many applications, through-hole components continue to play a crucial role in power electronics, automotive systems, industrial control systems, prototyping, and educational projects.
When designing a PCB that incorporates through-hole components, it is essential to consider factors such as hole size, pad diameter, component placement, soldering considerations, and thermal management. By following best practices and leveraging the strengths of through-hole technology, designers can create robust and reliable PCB assemblies that meet the specific requirements of their applications.
As technology continues to evolve, it is likely that through-hole and surface mount technologies will coexist, each serving specific needs and requirements in the diverse landscape of electronic products and systems. Understanding the relevance and applications of through-hole technology empowers designers to make informed decisions and select the most suitable approach for their PCB designs.
Leave a Reply