Introduction to Flex PCB Soldering
Flexible printed circuit boards (Flex PCBs) have gained immense popularity in recent years due to their versatility and ability to conform to various shapes and sizes. These PCBs are used in a wide range of applications, including wearable devices, medical equipment, aerospace, and automotive industries. However, soldering components onto flex PCBs requires specialized techniques and considerations compared to traditional rigid PCBs. In this article, we will explore five common Flex PCB Soldering technologies and their advantages and disadvantages.
What is Flex PCB Soldering?
Flex PCB soldering is the process of attaching electronic components to a flexible printed circuit board using solder, a fusible metal alloy. The goal is to create reliable electrical connections between the components and the PCB traces while maintaining the flexibility and integrity of the board. Soldering flex PCBs requires careful consideration of the materials, temperatures, and techniques used to ensure a successful and durable assembly.
Why is Flex PCB Soldering Important?
Proper soldering is crucial for the functionality, reliability, and longevity of flex PCB assemblies. Poor soldering can lead to issues such as:
- Intermittent or open connections
- Short circuits
- Component damage
- Reduced flexibility and durability of the PCB
By using appropriate soldering techniques and materials, manufacturers can ensure that their flex PCB assemblies perform optimally and meet the required quality standards.
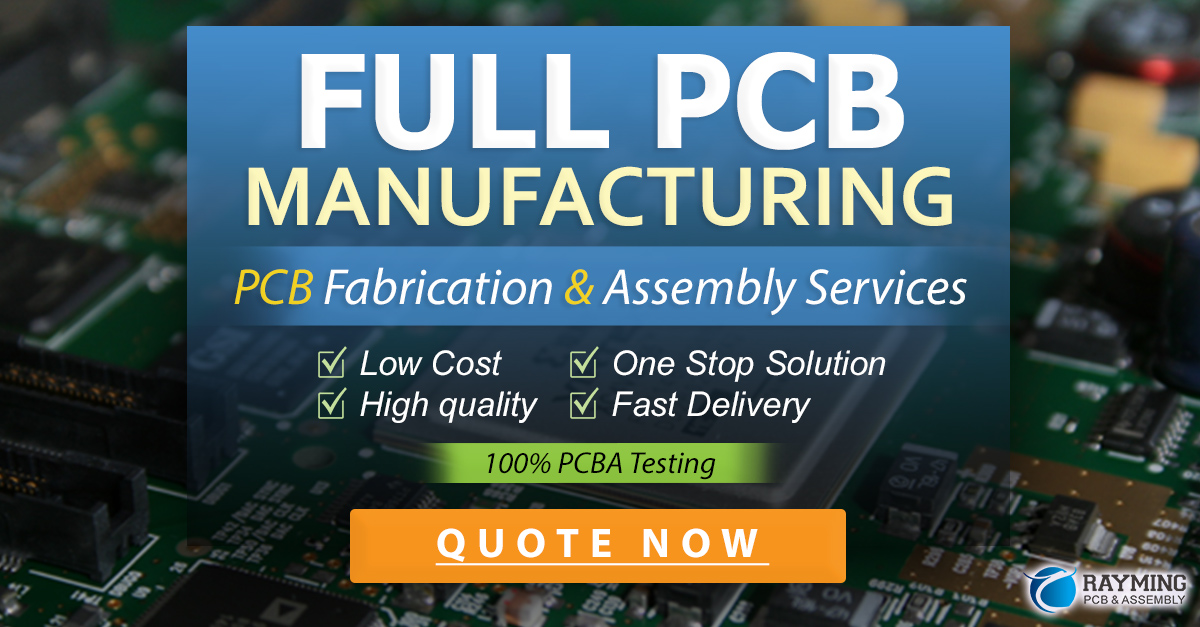
5 Common Flex PCB Soldering Technologies
1. Hand Soldering
Hand soldering is a manual process that involves using a soldering iron to apply heat and solder to the component leads and PCB pads. This method is often used for low-volume production, prototyping, or rework.
Advantages:
- Low setup costs
- Flexibility in component placement and soldering
- Suitable for small-scale production and repairs
Disadvantages:
- Time-consuming and labor-intensive
- Requires skilled operators
- Inconsistent results and potential for human error
2. Reflow Soldering
Reflow soldering is an automated process that uses a reflow oven to melt and fuse solder paste applied to the PCB pads and component leads. The PCB Assembly is heated in a controlled manner, following a predetermined temperature profile.
Advantages:
- High-volume production capability
- Consistent and repeatable results
- Suitable for surface mount components
Disadvantages:
- Higher setup costs and equipment investment
- Limited flexibility in component placement
- Requires precise control of temperature and time
3. Wave Soldering
Wave soldering is an automated process that involves passing the PCB assembly over a molten solder wave. The solder adheres to the exposed component leads and PCB pads, creating electrical connections.
Advantages:
- High-volume production capability
- Suitable for through-hole components
- Faster than hand soldering
Disadvantages:
- Limited compatibility with surface mount components
- Potential for solder bridging and shorts
- Requires careful control of solder wave parameters
4. Selective Soldering
Selective soldering is an automated process that targets specific areas of the PCB assembly for soldering. This method uses a localized solder fountain or mini-wave to apply solder to the desired locations.
Advantages:
- Precise control over soldering areas
- Suitable for mixed assembly (through-hole and surface mount)
- Reduced thermal stress on components
Disadvantages:
- Higher equipment costs
- Slower than wave soldering
- Requires programming and setup for each PCB design
5. Vapor Phase Soldering
Vapor phase soldering is a reflow soldering process that uses a heated vapor to transfer heat to the PCB assembly. The assembly is immersed in a vapor of an inert liquid, which condenses on the PCB and components, providing uniform heating.
Advantages:
- Uniform and controlled heating
- Reduced risk of thermal damage to components
- Suitable for heat-sensitive components
Disadvantages:
- Higher equipment costs
- Limited throughput compared to conventional reflow ovens
- Requires special fluids and maintenance
Comparison of Flex PCB Soldering Technologies
Soldering Technology | Advantages | Disadvantages |
---|---|---|
Hand Soldering | – Low setup costs – Flexibility in component placement and soldering – Suitable for small-scale production and repairs |
– Time-consuming and labor-intensive – Requires skilled operators – Inconsistent results and potential for human error |
Reflow Soldering | – High-volume production capability – Consistent and repeatable results – Suitable for surface mount components |
– Higher setup costs and equipment investment – Limited flexibility in component placement – Requires precise control of temperature and time |
Wave Soldering | – High-volume production capability – Suitable for through-hole components – Faster than hand soldering |
– Limited compatibility with surface mount components – Potential for solder bridging and shorts – Requires careful control of solder wave parameters |
Selective Soldering | – Precise control over soldering areas – Suitable for mixed assembly (through-hole and surface mount) – Reduced thermal stress on components |
– Higher equipment costs – Slower than wave soldering – Requires programming and setup for each PCB design |
Vapor Phase Soldering | – Uniform and controlled heating – Reduced risk of thermal damage to components – Suitable for heat-sensitive components |
– Higher equipment costs – Limited throughput compared to conventional reflow ovens – Requires special fluids and maintenance |
Factors to Consider When Choosing a Flex PCB Soldering Technology
When selecting a soldering technology for your flex PCB assembly, consider the following factors:
- Production volume and scalability
- Component types and sizes
- PCB design complexity
- Thermal sensitivity of components
- Budget and equipment availability
- Operator skill and training requirements
- Quality and reliability standards
By carefully evaluating these factors, you can choose the most suitable soldering technology for your specific flex PCB assembly needs.
Best Practices for Flex PCB Soldering
Regardless of the soldering technology used, following best practices can help ensure successful and reliable flex PCB assemblies:
- Use appropriate solder alloys and fluxes
- Control soldering temperatures and times
- Maintain proper alignment and support of components
- Minimize handling and bending of the flex PCB
- Implement quality control and inspection procedures
- Provide adequate training for operators
- Follow industry standards and guidelines
Future Trends in Flex PCB Soldering
As the demand for smaller, lighter, and more flexible electronic devices continues to grow, flex PCB soldering technologies are expected to evolve. Some future trends include:
- Increased adoption of laser soldering for precise and localized heating
- Development of advanced materials and coatings for improved soldering performance
- Integration of automated inspection and quality control systems
- Emphasis on environmentally friendly and lead-free soldering processes
- Exploration of alternative joining methods, such as conductive adhesives and ultrasonic welding
Conclusion
Flex PCB soldering is a critical process that requires careful consideration of the technologies, materials, and techniques used. By understanding the advantages and disadvantages of common soldering methods, such as hand soldering, reflow soldering, wave soldering, selective soldering, and vapor phase soldering, manufacturers can make informed decisions based on their specific requirements. Implementing best practices and staying updated with future trends can help ensure the production of high-quality and reliable flex PCB assemblies.
Frequently Asked Questions (FAQ)
1. What is the most suitable soldering technology for high-volume production of flex PCBs?
For high-volume production of flex PCBs, reflow soldering and wave soldering are the most suitable technologies. Reflow soldering is ideal for surface mount components, while wave soldering is better suited for through-hole components.
2. Can hand soldering be used for large-scale production of flex PCBs?
While hand soldering can be used for flex PCBs, it is not recommended for large-scale production due to its time-consuming and labor-intensive nature. Hand soldering is better suited for prototyping, small-scale production, or rework.
3. What are the main advantages of selective soldering for flex PCBs?
Selective soldering offers precise control over soldering areas, making it suitable for mixed assemblies with both through-hole and surface mount components. It also reduces thermal stress on components compared to wave soldering.
4. How does vapor phase soldering differ from conventional reflow soldering?
Vapor phase soldering uses a heated vapor to transfer heat to the PCB assembly, providing uniform and controlled heating. In contrast, conventional reflow soldering uses a reflow oven with a predetermined temperature profile to melt and fuse the solder.
5. What factors should be considered when choosing a soldering technology for flex PCBs?
When choosing a soldering technology for flex PCBs, consider factors such as production volume, component types and sizes, PCB design complexity, thermal sensitivity of components, budget and equipment availability, operator skill requirements, and quality and reliability standards.
Leave a Reply