1. Choosing the Right Solder Paste
Selecting the appropriate solder paste is essential for achieving a strong and reliable solder joint on Flex PCBs. When working with SMD components, it is recommended to use a no-clean solder paste with a fine particle size, such as Type 3 or Type 4. These pastes have a smaller grain size, which allows for better print definition and improved solder joint formation on the small pads of SMD components.
Additionally, consider the viscosity of the solder paste. A paste with a higher viscosity will be less likely to slump or spread on the flexible substrate, reducing the risk of bridging or short circuits. It is also essential to ensure that the solder paste is compatible with the surface finish of the Flex PCB, such as ENIG (Electroless Nickel Immersion Gold) or OSP (Organic Solderability Preservative).
Solder Paste Type | Particle Size | Viscosity | Compatible Surface Finishes |
---|---|---|---|
No-Clean Type 3 | 25-45 µm | High | ENIG, OSP, HASL |
No-Clean Type 4 | 20-38 µm | High | ENIG, OSP, HASL |
Water-Soluble | 25-45 µm | Medium | ENIG, OSP, HASL |
2. Proper Stencil Design and Printing
Creating a well-designed stencil is crucial for achieving consistent and accurate solder paste deposits on the Flex PCB. When designing the stencil, consider the following factors:
- Aperture Size: Ensure that the aperture size is optimized for the SMD component’s pad size. A general rule of thumb is to have an aperture size that is slightly smaller than the pad size to prevent solder bridging.
- Stencil Thickness: Use a stencil thickness that is appropriate for the solder paste and component size. A thinner stencil (e.g., 4-5 mils) is generally preferred for smaller SMD components, while a thicker stencil (e.g., 6-8 mils) may be necessary for larger components.
- Aperture Shape: Consider using rounded or tapered aperture shapes to improve paste release and reduce the risk of clogging.
When printing the solder paste, ensure that the stencil is properly aligned with the Flex PCB and that the printing parameters, such as squeegee pressure, speed, and angle, are optimized. Regularly inspect the printed pads for consistency and make adjustments as needed.
3. Controlled Reflow Profile
Developing a controlled reflow profile is critical for achieving reliable solder joints on Flex PCBs. The reflow profile should be tailored to the specific solder paste and SMD components being used. A typical reflow profile consists of four stages: preheat, soak, reflow, and cooling.
- Preheat: Gradually raise the temperature to activate the flux and remove any moisture from the PCB and components. A typical preheat rate is 1-3°C/second.
- Soak: Maintain a stable temperature to allow the flux to clean the surfaces and prepare for reflow. The soak temperature should be below the solder paste’s melting point.
- Reflow: Increase the temperature above the solder paste’s melting point to allow the solder to flow and form a strong bond between the component and the PCB. The peak temperature and time above liquidus (TAL) should be carefully controlled to prevent damage to the components or the Flex PCB.
- Cooling: Gradually cool the PCB and components to room temperature. A controlled cooling rate helps to prevent thermal shock and minimize stress on the solder joints.
Reflow Stage | Temperature Range | Duration |
---|---|---|
Preheat | 25-150°C | 60-90 seconds |
Soak | 150-180°C | 60-120 seconds |
Reflow | 220-250°C (peak) | 30-90 seconds |
Cooling | 250-25°C | 60-120 seconds |
It is essential to monitor the reflow profile using a thermocouple or a profiling system to ensure that the desired temperatures and durations are achieved. Regularly review and adjust the reflow profile to optimize the solder joint quality and reliability.
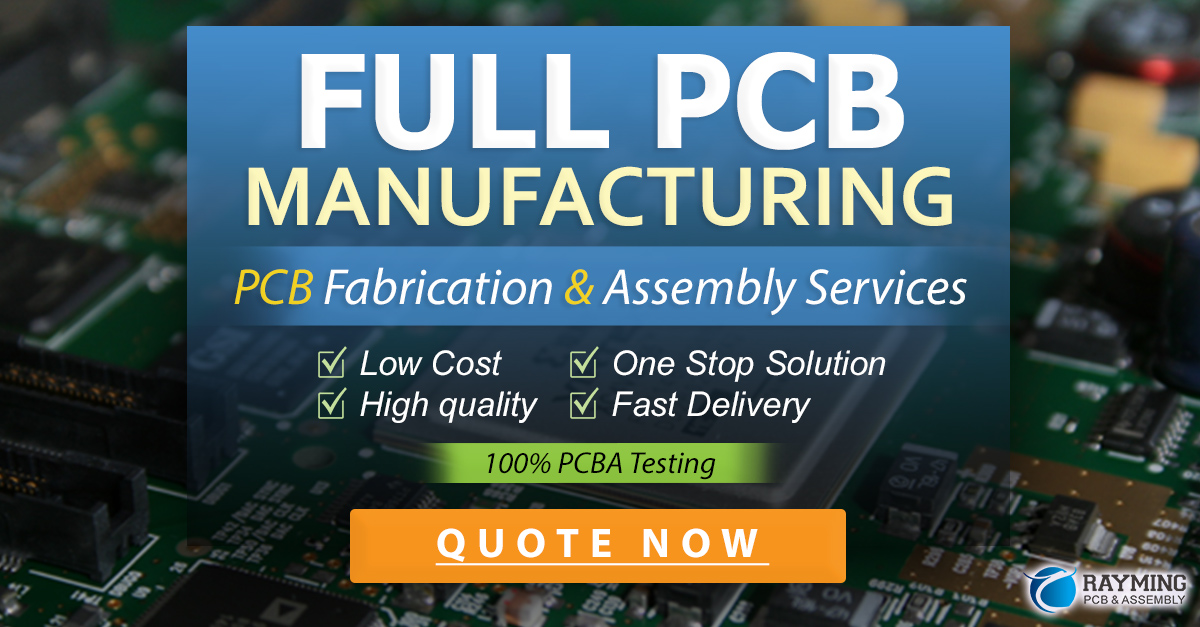
4. Proper Component Placement
Accurate component placement is crucial for achieving a successful Flex PCB assembly. When placing SMD components on a flexible substrate, consider the following guidelines:
- Alignment: Ensure that the components are correctly aligned with the solder pads. Use a high-quality pick-and-place machine or a vision system to achieve precise placement.
- Placement Pressure: Apply the appropriate amount of pressure when placing the components to ensure good contact with the solder paste. Excessive pressure can cause the component to shift or damage the Flex PCB, while insufficient pressure may result in poor solder joint formation.
- Component Orientation: Pay attention to the correct orientation of polarized components, such as diodes, electrolytic capacitors, and ICs. Incorrect orientation can lead to malfunction or damage to the component and the circuit.
- Clearance: Maintain sufficient clearance between components to prevent shorts and facilitate inspection and rework. Follow the manufacturer’s guidelines for minimum spacing requirements.
5. Inspection and Quality Control
Implementing a robust inspection and quality control process is essential for identifying and addressing any issues related to Flex PCB Soldering SMD. Visual inspection is the first line of defense in detecting soldering defects, such as bridging, insufficient solder, or poor wetting. Use a magnifying glass or a microscope to examine the solder joints closely.
In addition to visual inspection, consider the following techniques for quality control:
- X-ray Inspection: X-ray imaging can reveal hidden defects, such as voids, cracks, or insufficient solder, especially in areas obscured by the component body.
- Automated Optical Inspection (AOI): AOI systems use high-resolution cameras and advanced algorithms to detect soldering defects automatically. This method is particularly useful for high-volume production runs.
- Electrical Testing: Perform electrical tests, such as continuity and insulation resistance tests, to verify the functionality and reliability of the soldered connections.
Establish a defect classification system and set acceptable quality levels (AQLs) for each type of defect. Regularly review the inspection results and implement corrective actions to address any recurring issues. By maintaining a stringent quality control process, you can ensure that your Flex PCB assemblies meet the required performance and reliability standards.
Frequently Asked Questions (FAQ)
-
Q: What are the most common defects in Flex PCB soldering SMD?
A: The most common defects in Flex PCB soldering SMD include bridging, insufficient solder, poor wetting, component misalignment, and solder joint cracking due to stress. -
Q: How can I prevent solder bridging when soldering SMD components on Flex PCBs?
A: To prevent solder bridging, use a solder paste with the appropriate viscosity and particle size, design the stencil apertures to be slightly smaller than the pad size, and optimize the reflow profile to ensure proper solder melting and flow. -
Q: What should I do if I encounter component shifting during the reflow process?
A: If you notice component shifting during reflow, check the placement pressure, stencil design, and solder paste volume. Ensure that the components are securely placed and that the solder paste volume is sufficient to hold the components in place during reflow. -
Q: How can I minimize stress on the solder joints in Flex PCB assemblies?
A: To minimize stress on the solder joints, use a controlled reflow profile with gradual temperature changes, select a flexible solder mask to absorb stress, and consider using underfill or conformal coating to provide additional support to the components. -
Q: What are the benefits of using an automated optical inspection (AOI) system for Flex PCB soldering SMD?
A: AOI systems offer several benefits, including faster inspection speeds, consistent and objective defect detection, improved traceability, and reduced human error. AOI can help identify defects early in the production process, reducing rework costs and improving overall quality.
In conclusion, Flex PCB soldering SMD requires careful attention to various aspects, including solder paste selection, stencil design, reflow profile optimization, component placement, and quality control. By understanding and addressing these critical factors, you can ensure a successful and reliable assembly process for your flexible PCBs. Remember to stay up-to-date with industry best practices and continuously monitor and improve your soldering processes to achieve the best possible results.
Leave a Reply