Introduction to PCB Thickness
Printed Circuit Boards (PCBs) are essential components in modern electronics, providing a platform for mounting and interconnecting electronic components. One of the critical factors in PCB design and manufacturing is the thickness of the board. PCB thickness plays a vital role in determining the mechanical stability, electrical performance, and overall reliability of the circuit board. In this article, we will explore the standard PCB thicknesses, factors influencing thickness selection, and guidelines for choosing the right thickness for your specific application.
Understanding PCB Thickness Measurements
PCB thickness is typically measured in either millimeters (mm) or mils (thousandths of an inch). The most common unit used in the industry is mils. To convert between millimeters and mils, you can use the following conversion factor:
1 mm = 39.37 mils
For example, a PCB with a thickness of 1.6 mm is equivalent to approximately 63 mils (1.6 × 39.37 = 62.992).
Standard PCB Thicknesses
There are several standard PCB thicknesses used in the electronics industry. The following table lists the most common PCB thicknesses in both millimeters and mils:
Thickness (mm) | Thickness (mils) |
---|---|
0.4 | 15.7 |
0.6 | 23.6 |
0.8 | 31.5 |
1.0 | 39.4 |
1.2 | 47.2 |
1.6 | 63.0 |
2.0 | 78.7 |
2.4 | 94.5 |
These standard thicknesses are widely available from PCB manufacturers and are suitable for a wide range of applications. However, it’s important to note that custom thicknesses can also be produced based on specific requirements.
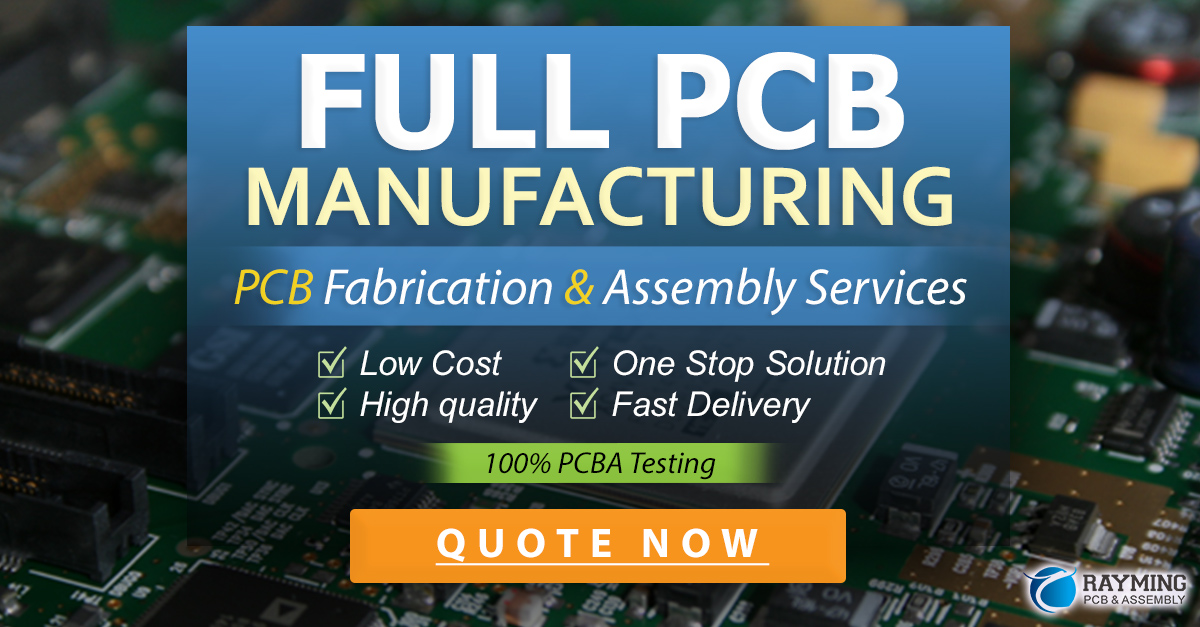
Factors Influencing PCB Thickness Selection
When deciding on the appropriate PCB thickness for your project, several factors need to be considered. These factors include:
1. Mechanical Stability
The thickness of the PCB directly affects its mechanical stability. Thicker boards provide greater rigidity and resistance to bending and vibration. If your application involves high mechanical stress or requires a sturdy structure, opting for a thicker PCB is advisable.
2. Electrical Performance
PCB thickness can impact the electrical performance of the circuit. Thinner boards have lower dielectric losses and can offer better high-frequency performance. However, thinner boards also have higher impedance and may be more susceptible to signal integrity issues. It’s crucial to consider the electrical requirements of your design when selecting the PCB thickness.
3. Heat Dissipation
The ability of a PCB to dissipate heat is influenced by its thickness. Thicker boards have better thermal conductivity and can more effectively transfer heat away from components. If your circuit generates significant heat, using a thicker PCB can help improve thermal management.
4. Manufacturing Constraints
PCB manufacturers have specific capabilities and limitations when it comes to producing different thicknesses. Some manufacturers may have a minimum or maximum thickness they can accommodate. It’s important to consult with your chosen PCB manufacturer to ensure they can produce the desired thickness for your design.
5. Cost Considerations
The thickness of the PCB can impact the overall cost of manufacturing. Thinner boards generally require less material and may be more cost-effective. However, thinner boards may also be more challenging to manufacture and assemble, which can increase costs. It’s essential to find a balance between cost and performance when selecting the PCB thickness.
Guidelines for Choosing the Right PCB Thickness
When determining the appropriate PCB thickness for your project, consider the following guidelines:
-
For general-purpose applications with moderate mechanical and electrical requirements, a thickness of 1.6 mm (63 mils) is a common choice. This thickness offers a good balance between stability, performance, and cost.
-
If your design requires high mechanical strength or involves larger components, consider using a thicker PCB, such as 2.0 mm (78.7 mils) or 2.4 mm (94.5 mils). These thicknesses provide increased rigidity and can accommodate heavier components.
-
For high-frequency or high-speed designs, thinner PCBs, such as 0.8 mm (31.5 mils) or 1.0 mm (39.4 mils), may be preferable. Thinner boards have lower dielectric losses and can improve signal integrity at higher frequencies.
-
If your application has strict space constraints or requires a lightweight design, thinner PCBs, such as 0.4 mm (15.7 mils) or 0.6 mm (23.6 mils), can be used. However, keep in mind that thinner boards may be more fragile and require careful handling during manufacturing and assembly.
-
Always consult with your PCB manufacturer and consider their capabilities and recommendations. They can provide valuable insights based on their experience and help you select the most suitable thickness for your specific project.
Multilayer PCBs and Thickness Considerations
Multilayer PCBs consist of multiple layers of conductive copper and insulating material laminated together. The thickness of multilayer PCBs is determined by the number of layers and the thickness of each individual layer. The following table provides a general guide for the relationship between the number of layers and the typical overall thickness:
Number of Layers | Typical Thickness (mm) | Typical Thickness (mils) |
---|---|---|
2 | 0.8 – 1.6 | 31.5 – 63.0 |
4 | 1.0 – 2.0 | 39.4 – 78.7 |
6 | 1.2 – 2.4 | 47.2 – 94.5 |
8 | 1.6 – 3.2 | 63.0 – 126.0 |
10 and above | 2.0 – 3.2+ | 78.7 – 126.0+ |
When designing multilayer PCBs, it’s important to consider the thickness of each individual layer and the overall stack-up. The thickness of the copper layers and the dielectric material between layers can impact the electrical performance and signal integrity of the board. It’s recommended to work closely with your PCB manufacturer to optimize the layer stack-up and ensure the desired thickness is achieved.
PCB Thickness and Manufacturing Process
The manufacturing process used to produce PCBs can also influence the selection of PCB thickness. Different manufacturing processes have their own limitations and capabilities when it comes to handling different thicknesses. Here are some common manufacturing processes and their impact on PCB thickness:
-
Standard PCB Manufacturing: Standard PCB manufacturing processes can typically handle thicknesses ranging from 0.4 mm to 3.2 mm (15.7 to 126.0 mils). This covers the majority of standard PCB thicknesses used in the industry.
-
High-Density Interconnect (HDI) PCBs: HDI PCBs often require thinner layers and overall thinner board thicknesses to achieve fine pitch and high-density trace routing. HDI PCBs commonly use thicknesses ranging from 0.4 mm to 1.6 mm (15.7 to 63.0 mils).
-
Flexible PCBs: Flexible PCBs are designed to be bendable and require thinner materials. Typical thicknesses for flexible PCBs range from 0.1 mm to 0.3 mm (3.9 to 11.8 mils). However, the overall thickness of a flexible PCB Assembly can be increased by adding stiffeners or using multiple layers.
-
Rigid-Flex PCBs: Rigid-flex PCBs combine both rigid and flexible sections in a single board. The thickness of the rigid sections can follow the standard PCB thicknesses, while the flexible sections typically use thinner materials similar to flexible PCBs.
It’s crucial to discuss your specific requirements with your PCB manufacturer and ensure that the chosen manufacturing process can accommodate the desired PCB thickness.
Frequently Asked Questions (FAQ)
-
What is the most common PCB thickness?
The most common PCB thickness used in the industry is 1.6 mm (63 mils). This thickness provides a good balance between mechanical stability, electrical performance, and cost-effectiveness for a wide range of applications. -
Can I use a custom PCB thickness for my project?
Yes, custom PCB thicknesses can be manufactured based on specific project requirements. However, it’s important to consult with your PCB manufacturer to ensure they have the capability to produce the desired thickness and to discuss any potential implications on cost and lead time. -
How does PCB thickness affect signal integrity?
PCB thickness can impact signal integrity in several ways. Thinner PCBs generally have lower dielectric losses and can offer better high-frequency performance. However, thinner boards also have higher impedance and may be more susceptible to signal integrity issues such as crosstalk and electromagnetic interference (EMI). -
What factors should I consider when selecting the appropriate PCB thickness for my project?
When selecting the appropriate PCB thickness, consider factors such as mechanical stability, electrical performance, heat dissipation, manufacturing constraints, and cost. Evaluate your specific project requirements and consult with your PCB manufacturer to determine the most suitable thickness. -
Can I mix different PCB thicknesses within the same board?
Yes, it is possible to have different thicknesses within the same PCB, especially in the case of rigid-flex PCBs where the rigid sections can have a different thickness than the flexible sections. However, mixing different thicknesses within a single rigid board is less common and may require special manufacturing considerations.
Conclusion
Selecting the appropriate PCB thickness is a critical aspect of PCB design and manufacturing. Understanding the standard PCB thicknesses and the factors that influence thickness selection is essential for ensuring the optimal performance, reliability, and cost-effectiveness of your electronic devices. By considering mechanical stability, electrical performance, heat dissipation, manufacturing constraints, and cost, you can make informed decisions when choosing the right PCB thickness for your specific application.
Remember to collaborate closely with your PCB manufacturer throughout the design and manufacturing process. Their expertise and guidance can help you navigate the complexities of PCB thickness selection and ensure the successful realization of your electronic projects.
Leave a Reply