What is PCB Thickness?
PCB thickness refers to the distance between the top and bottom surfaces of a printed circuit board. It is typically measured in either millimeters (mm) or mils (thousandths of an inch). The thickness of a PCB is determined by the combined thickness of the copper layers, substrate material, and any additional layers such as solder mask or silkscreen.
Standard PCB Thicknesses
There are several standard thicknesses for PCBs, each suitable for different applications and manufacturing processes. The most common PCB thicknesses are:
Thickness (mm) | Thickness (mils) | Application |
---|---|---|
0.4 | 15.75 | Very thin, flexible PCBs for wearable electronics |
0.6 | 23.62 | Thin, flexible PCBs for compact devices |
0.8 | 31.50 | Commonly used for small, lightweight PCBs |
1.0 | 39.37 | Widely used for general-purpose PCBs |
1.2 | 47.24 | Suitable for more robust PCBs with higher layer count |
1.6 | 62.99 | Standard thickness for many industrial applications |
2.0 | 78.74 | Used for high-power, high-reliability applications |
2.4 | 94.49 | Thick PCBs for extreme environments or heavy components |
0.4mm (15.75 mils) PCBs
These ultra-thin PCBs are primarily used in wearable electronics, such as smartwatches or fitness trackers. They offer excellent flexibility and can be easily integrated into compact devices. However, their thin profile makes them more susceptible to damage and limits the number of layers and component sizes that can be used.
0.6mm (23.62 mils) PCBs
Thin and flexible, 0.6mm PCBs are often found in compact devices like smartphones, tablets, and small IoT devices. They provide a good balance between flexibility and durability, allowing for more layers and component options compared to 0.4mm PCBs.
0.8mm (31.50 mils) PCBs
PCBs with a thickness of 0.8mm are commonly used in small, lightweight devices where space is limited. They offer improved mechanical strength compared to thinner options while still maintaining a compact profile. This thickness is suitable for many consumer electronics and low-power applications.
1.0mm (39.37 mils) PCBs
The 1.0mm thickness is widely used for general-purpose PCBs across various industries. It provides a good balance between mechanical strength, thermal management, and ease of manufacturing. Many consumer electronics, industrial control systems, and telecommunication devices utilize 1.0mm PCBs.
1.2mm (47.24 mils) PCBs
For applications requiring more robust PCBs or higher layer counts, 1.2mm thickness is often chosen. This thickness offers increased mechanical stability and allows for more complex designs with a greater number of layers. It is commonly found in industrial automation, automotive electronics, and medical devices.
1.6mm (62.99 mils) PCBs
Considered a standard thickness for many industrial applications, 1.6mm PCBs provide excellent mechanical strength and thermal management capabilities. They are well-suited for high-power applications, such as power supplies, motor controllers, and renewable energy systems. The increased thickness allows for more layers and accommodates larger components.
2.0mm (78.74 mils) PCBs
PCBs with a thickness of 2.0mm are used in high-power and high-reliability applications where mechanical stability and thermal dissipation are critical. These thick boards are commonly found in aerospace, defense, and heavy industrial equipment. They can support a high number of layers and accommodate large, heavy components.
2.4mm (94.49 mils) PCBs
The thickest standard PCB option, 2.4mm boards, are designed for extreme environments and applications with substantial mechanical stress. They are often used in military equipment, oil and gas exploration, and other harsh environments. The increased thickness provides superior mechanical strength and allows for the use of heavy components and connectors.
Factors Influencing PCB Thickness Selection
When choosing the appropriate PCB thickness for a project, several factors must be considered:
-
Application Requirements: The specific needs of the application, such as mechanical strength, thermal management, and space constraints, play a significant role in determining the suitable PCB thickness.
-
Number of Layers: The number of copper layers in a PCB directly impacts its thickness. More layers require a thicker substrate to accommodate the additional copper and insulation.
-
Component Sizes: The size and weight of the components mounted on the PCB influence the required thickness. Heavier components may necessitate a thicker board for proper support and stability.
-
Manufacturing Capabilities: The chosen PCB thickness should be compatible with the manufacturing processes and equipment available. Some manufacturers may have limitations on the minimum or maximum thickness they can produce.
-
Cost Considerations: Thicker PCBs generally cost more due to the increased material usage and manufacturing complexity. The project budget must be balanced with the required performance and reliability.
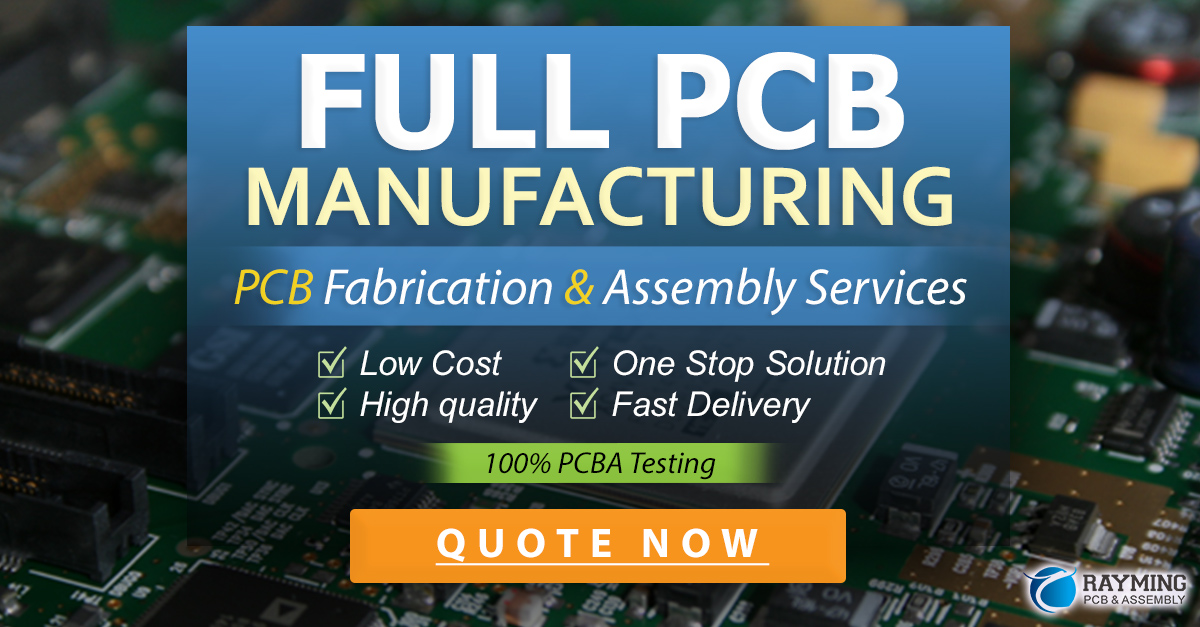
Impact of PCB Thickness on Functionality
PCB thickness has a direct impact on various aspects of a board’s functionality:
Mechanical Strength
Thicker PCBs offer greater mechanical strength and stability, making them more resistant to vibration, shock, and physical stress. This is particularly important in applications where the PCB is subject to harsh environments or frequent handling.
Thermal Management
The thickness of a PCB influences its ability to dissipate heat generated by the mounted components. Thicker boards have better thermal conductivity and can more effectively transfer heat away from hot spots, preventing component failure and ensuring reliable operation.
Signal Integrity
PCB thickness can affect signal integrity, particularly at high frequencies. Thinner boards may be more susceptible to signal distortion and crosstalk due to the closer proximity of traces. Thicker boards provide more space for proper trace routing and shielding, minimizing signal integrity issues.
Flexibility
Thinner PCBs, such as 0.4mm and 0.6mm, offer greater flexibility, making them suitable for applications where the board needs to conform to a specific shape or withstand repeated bending. However, this flexibility comes at the cost of reduced mechanical strength and limited layer count.
Manufacturing Considerations
The chosen PCB thickness should be compatible with the available manufacturing processes and equipment. Thinner boards may require specialized handling and more precise manufacturing techniques, while thicker boards may necessitate different drilling and plating methods.
Frequently Asked Questions (FAQ)
1. What is the most common PCB thickness?
The most common PCB thickness is 1.6mm (62.99 mils). This thickness is widely used in various industries and offers a good balance between mechanical strength, thermal management, and ease of manufacturing.
2. Can I use a thinner PCB to save space in my design?
Yes, thinner PCBs, such as 0.4mm or 0.6mm, can be used to save space in compact designs. However, keep in mind that thinner boards have limitations in terms of mechanical strength, layer count, and component sizes.
3. How does PCB thickness affect the cost of manufacturing?
Generally, thicker PCBs cost more to manufacture due to the increased material usage and processing requirements. However, the cost difference may be justified if the application demands the enhanced mechanical strength or thermal management provided by a thicker board.
4. Can I mix different PCB thicknesses in the same design?
While it is technically possible to mix different PCB thicknesses in a single design, it is generally not recommended. Using a consistent thickness throughout the board simplifies the manufacturing process and ensures better overall performance and reliability.
5. How do I determine the appropriate PCB thickness for my project?
To determine the appropriate PCB thickness, consider factors such as the application requirements, number of layers needed, component sizes, manufacturing capabilities, and budget constraints. Consult with your PCB manufacturer for guidance on selecting the best thickness for your specific project.
Conclusion
Selecting the appropriate PCB thickness is a critical decision in the design process, as it significantly impacts the board’s mechanical strength, thermal management, signal integrity, and overall performance. By understanding the standard PCB thicknesses and the factors influencing thickness selection, designers can make informed choices that balance the project’s requirements with manufacturing capabilities and cost considerations.
When in doubt, consult with experienced PCB manufacturers and assembly partners to ensure the chosen thickness aligns with the specific needs of the application. By carefully considering PCB thickness and its implications, designers can create reliable, high-performance electronic devices that meet the demands of today’s ever-evolving technology landscape.
Leave a Reply