1. Understanding SMT Components
SMT components are designed specifically for surface mounting on PCBs. These components are smaller and have flat, lightweight leads or terminations that allow them to be soldered directly onto the surface of the board. Common SMT components include:
- Resistors
- Capacitors
- Inductors
- Diodes
- Transistors
- Integrated Circuits (ICs)
SMT components come in various package sizes, such as 0201, 0402, 0603, 0805, and 1206, with the numbers representing the component’s dimensions in inches.
2. PCB Design Considerations for SMT
When designing a PCB for SMT assembly, several factors must be considered to ensure optimal performance and manufacturability:
2.1 Component Placement
Proper component placement is crucial for SMT assembly. Components should be placed with sufficient spacing between them to allow for efficient soldering and to avoid potential short circuits. Additionally, components should be oriented in a manner that facilitates automated pick-and-place machines.
2.2 Pad Size and Shape
The pads on the PCB must be designed to match the size and shape of the SMT component’s leads. Proper pad design ensures a strong solder joint and prevents component misalignment during the assembly process.
2.3 Solder Mask and Silkscreen
A solder mask is a protective layer applied to the PCB that prevents solder from bridging between adjacent pads. The silkscreen layer is used to print component identifiers, polarity markers, and other important information on the PCB surface. Both layers play a vital role in the SMT assembly process.
3. Solder Paste Printing
Solder paste printing is the first step in the SMT assembly process. Solder paste, a mixture of tiny solder particles suspended in a flux medium, is applied to the PCB pads using a stencil or screen printing technique. The stencil is a thin metal sheet with apertures that correspond to the PCB pad locations. The solder paste is deposited through these apertures onto the pads.
3.1 Stencil Design
Proper stencil design is essential for accurate solder paste deposition. The stencil thickness, aperture size, and shape must be carefully selected based on the PCB design and SMT component requirements.
3.2 Solder Paste Inspection (SPI)
After printing, the solder paste deposits are inspected using an SPI machine. This automated inspection process verifies the presence, volume, and alignment of the solder paste on each pad. SPI helps identify any printing defects early in the assembly process, allowing for timely corrections.
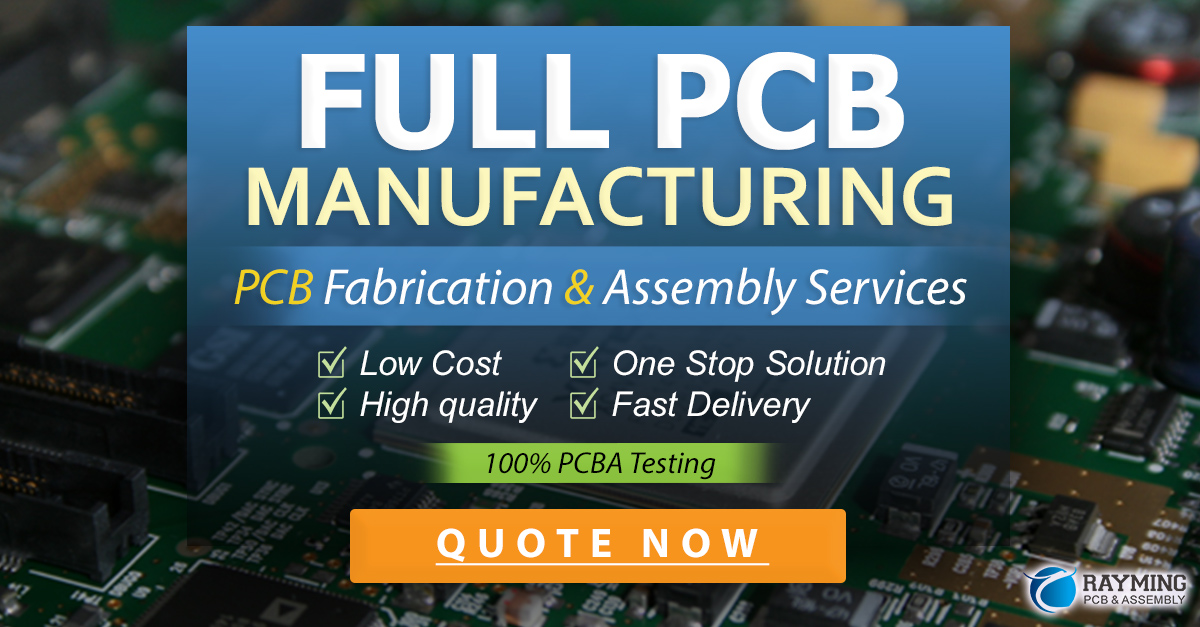
4. Component Placement
Once the solder paste is printed, the SMT components are placed onto the PCB using automated pick-and-place machines. These machines use vacuum nozzles or grippers to pick up components from feeders and place them accurately on the corresponding pads.
4.1 Pick-and-Place Machine Programming
Pick-and-place machines must be programmed with the correct component data, including the component type, size, and placement coordinates. This information is typically generated from the PCB design files and loaded into the machine’s control software.
4.2 Component Feeders
SMT components are supplied to the pick-and-place machine using various types of feeders, such as tape-and-reel, tube, or tray feeders. The choice of feeder depends on the component package size and quantity.
5. Reflow Soldering
After component placement, the PCB undergoes reflow soldering. In this process, the PCB is heated in a reflow oven, causing the solder paste to melt and form a permanent electrical and mechanical connection between the components and the PCB pads.
5.1 Reflow Temperature Profile
The reflow temperature profile is a critical factor in achieving a successful solder joint. The profile consists of several stages, including preheat, soak, reflow, and cooling. Each stage has specific temperature and time requirements that must be carefully controlled to ensure proper solder melting and flux activation.
5.2 Nitrogen Atmosphere
Some reflow ovens use a nitrogen atmosphere to reduce oxidation and improve solder joint quality. The nitrogen displaces oxygen in the oven, preventing the formation of oxides on the solder surface during the reflow process.
6. Inspection and Testing
After the SMT assembly process, the PCBs undergo various inspection and testing procedures to ensure quality and functionality.
6.1 Visual Inspection
A visual inspection is performed to check for any visible defects, such as component misalignment, solder bridges, or insufficient solder joints. This inspection can be done manually or using automated optical inspection (AOI) machines.
6.2 X-Ray Inspection
For components with hidden solder joints, such as ball grid arrays (BGAs) or quad flat no-lead (QFN) packages, X-ray inspection is used. This non-destructive method allows for the examination of solder joint quality beneath the component.
6.3 Functional Testing
Functional testing verifies that the assembled PCB performs as intended. This may include in-circuit testing (ICT), boundary scan testing, or functional test fixtures that simulate the PCB’s actual operating conditions.
7. Rework and Repair
Despite best efforts, SMT assembly defects can occur. Rework and repair techniques are employed to correct these issues without scrapping the entire PCB.
7.1 Component Removal
Defective SMT components can be removed using specialized heating tools, such as hot air pencils or soldering irons. Care must be taken to avoid damaging the PCB or surrounding components during the removal process.
7.2 Component Replacement
After removing the defective component, a new one is soldered in its place. This can be done manually or using a rework station that combines heating and placement functions.
8. Traceability and Documentation
Traceability and documentation are essential for quality control and regulatory compliance in SMT assembly.
8.1 Lot Tracking
Each PCB and component lot should be tracked throughout the assembly process. This allows for quick identification and isolation of any issues that may arise.
8.2 Assembly Documentation
Detailed assembly documentation, including bill of materials (BOM), assembly drawings, and work instructions, should be maintained. This documentation serves as a reference for operators and helps ensure consistency in the assembly process.
9. Selecting an SMT Assembly Partner
For companies that do not have in-house SMT assembly capabilities, partnering with a reliable SMT assembly provider is crucial.
9.1 Experience and Expertise
Choose an SMT assembly partner with a proven track record and expertise in assembling PCBs similar to your project. They should have a deep understanding of SMT processes and be able to provide valuable insights and recommendations.
9.2 Quality Management System
Ensure that the SMT assembly partner has a robust quality management system in place. This may include certifications such as ISO 9001, ISO 13485 (for medical devices), or AS9100 (for aerospace applications).
9.3 Communication and Support
Clear communication and responsive support are key to a successful partnership. The SMT assembly provider should be proactive in providing updates, addressing concerns, and offering technical support throughout the project.
Conclusion
SMT assembly is a complex process that requires careful planning, execution, and quality control. By understanding the fundamentals of SMT components, PCB design, solder paste printing, component placement, reflow soldering, inspection, testing, rework, traceability, and documentation, you can ensure the success of your SMT-PCB projects. Whether you have in-house SMT assembly capabilities or partner with an external provider, keeping these nine essential aspects in mind will help you achieve high-quality, reliable PCB assemblies.
FAQs
1. What are the advantages of SMT assembly compared to through-hole mounting?
SMT assembly offers several advantages over through-hole mounting, including:
- Smaller component sizes, allowing for higher circuit density and reduced PCB size
- Faster assembly speeds, as components can be placed and soldered in a single automated process
- Lower production costs, due to reduced manual labor and faster throughput
- Improved mechanical stability, as SMT components have a lower profile and are less susceptible to vibration
2. What is the purpose of solder paste in SMT assembly?
Solder paste serves two main purposes in SMT assembly:
- It provides a temporary adhesive to hold the components in place during the placement process.
- When heated during reflow soldering, the solder particles in the paste melt and form a permanent electrical and mechanical connection between the component leads and PCB pads.
3. How does the reflow temperature profile affect SMT assembly quality?
The reflow temperature profile is crucial for achieving high-quality solder joints in SMT assembly. An improper profile can lead to issues such as:
- Insufficient solder melting, resulting in weak or open solder joints
- Excessive heat exposure, causing component damage or PCB Warpage
- Inadequate flux activation, leading to poor solder wetting and joint formation
A well-designed reflow temperature profile ensures that the solder paste is exposed to the correct temperatures for the appropriate durations, allowing for optimal solder melting, flux activation, and component protection.
4. What are some common defects that can occur during SMT assembly?
Common SMT assembly defects include:
- Solder bridges: Unintended solder connections between adjacent pads or components
- Tombstoning: When a component stands up on one end due to uneven solder melting or surface tension
- Insufficient solder joints: Weak or incomplete solder connections due to inadequate solder volume or poor wetting
- Component misalignment: When components are not placed accurately on their designated pads
- Solder balls: Small spheres of solder that can cause short circuits or reliability issues
Regular inspection and testing help identify and correct these defects before they impact the final product.
5. How can I ensure the reliability and quality of my SMT-PCB assemblies?
To ensure the reliability and quality of your SMT-PCB assemblies:
- Follow best practices for PCB design, considering factors such as component placement, pad size, and solder mask.
- Use high-quality components and materials, including solder paste and PCB substrates.
- Implement a robust quality management system that includes incoming inspection, process control, and outgoing testing.
- Regularly maintain and calibrate your SMT assembly equipment to ensure consistent performance.
- Partner with experienced and reputable SMT assembly providers who have a proven track record of delivering high-quality products.
By adhering to these guidelines and continuously monitoring and improving your SMT assembly processes, you can achieve reliable, high-quality PCB assemblies that meet your project requirements.
Leave a Reply