Introduction to PCB Types
Printed Circuit Boards (PCBs) are the foundation of modern electronics. They provide a platform for mounting and interconnecting electronic components to create functional circuits and systems. PCBs come in various types, each with its own characteristics, advantages, and limitations. Two of the most common PCB types are single-sided PCBs and double-sided PCBs. In this article, we will explore these two PCB types in detail, discussing their features, applications, manufacturing processes, and more.
What is a Single-Sided PCB?
A single-sided PCB, also known as a single-layer PCB, is a type of printed circuit board that has conductive copper traces on only one side of the insulating substrate material. The components are mounted on the same side as the copper traces, and the connections between them are made through the traces and solder joints.
Advantages of Single-Sided PCBs
- Cost-effective: Single-sided PCBs are generally the most affordable option due to their simple design and manufacturing process.
- Easy to manufacture: The fabrication of single-sided PCBs is straightforward, requiring fewer steps and materials compared to more complex PCB types.
- Suitable for simple circuits: Single-sided PCBs are ideal for basic electronic projects and low-density designs with fewer components.
Limitations of Single-Sided PCBs
- Limited routing options: With only one layer available for copper traces, single-sided PCBs may face routing challenges for more complex designs.
- Lower component density: The single-layer design restricts the number of components that can be accommodated on the board.
- Potential for interference: Single-sided PCBs are more susceptible to electromagnetic interference (EMI) due to the exposed traces on the surface.
Applications of Single-Sided PCBs
Single-sided PCBs are commonly used in various applications, such as:
- Simple electronic projects and prototypes
- Low-cost consumer electronics
- Educational and hobby projects
- Basic control systems and sensors
What is a Double-Sided PCB?
A double-sided PCB, also known as a two-layer PCB, is a type of printed circuit board that has conductive copper traces on both sides of the insulating substrate material. Components can be mounted on either side of the board, and the two layers are interconnected through Plated-through Holes (PTHs) or vias.
Advantages of Double-Sided PCBs
- Increased routing options: With two layers available for copper traces, double-sided PCBs offer more flexibility in routing and component placement.
- Higher component density: Double-sided PCBs can accommodate more components per unit area compared to single-sided PCBs.
- Improved signal integrity: The additional layer helps to reduce electromagnetic interference and crosstalk between signals.
- Better heat dissipation: Double-sided PCBs can effectively dissipate heat from components mounted on both sides of the board.
Limitations of Double-Sided PCBs
- Higher manufacturing cost: The fabrication process for double-sided PCBs is more complex and requires additional steps, resulting in higher production costs compared to single-sided PCBs.
- Increased design complexity: Designing double-sided PCBs requires careful consideration of layer alignment, via placement, and signal integrity.
- Potential for warpage: Double-sided PCBs are more susceptible to warpage during the manufacturing process due to the different thermal expansion rates of the materials used.
Applications of Double-Sided PCBs
Double-sided PCBs are widely used in various applications, such as:
- Moderate-complexity electronic devices
- Telecommunications equipment
- Industrial control systems
- Automotive electronics
- Medical devices
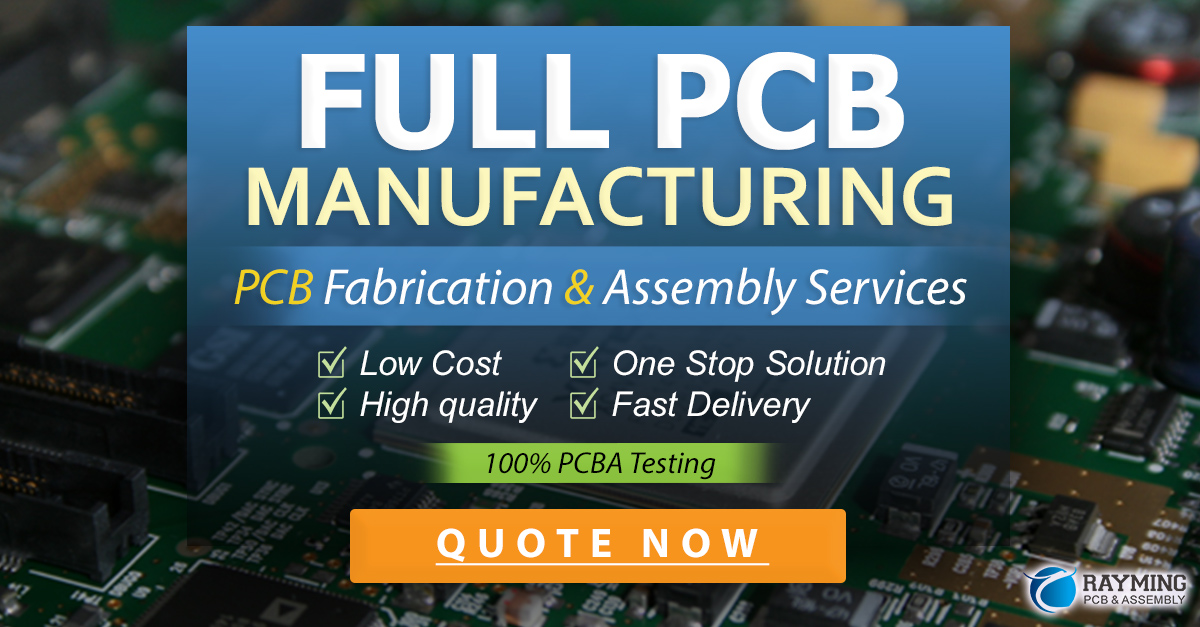
Manufacturing Process of Single-Sided and Double-Sided PCBs
The manufacturing process for single-sided and double-sided PCBs involves several steps, including:
-
Substrate preparation: The insulating substrate material, typically FR-4, is cut to the desired size and shape.
-
Copper lamination: A thin layer of copper foil is laminated onto one side (for single-sided PCBs) or both sides (for double-sided PCBs) of the substrate using heat and pressure.
-
Drilling: Holes are drilled through the board for component mounting and, in the case of double-sided PCBs, for interconnecting the two layers via PTHs.
-
Patterning: The desired circuit pattern is transferred onto the copper layer(s) using photoresist and exposure to UV light.
-
Etching: The unwanted copper is chemically removed, leaving only the desired circuit traces.
-
Plating (for double-sided PCBs): The holes are plated with copper to create electrical connections between the two layers.
-
Solder mask application: A protective solder mask is applied to the board, covering the copper traces while leaving the pads and holes exposed.
-
Silkscreen printing: Text, symbols, and component identifiers are printed onto the solder mask using a silkscreen process.
-
Surface finish: A surface finish, such as HASL (Hot Air Solder Leveling) or ENIG (Electroless Nickel Immersion Gold), is applied to the exposed pads and holes to prevent oxidation and improve solderability.
Choosing Between Single-Sided and Double-Sided PCBs
When deciding between single-sided and double-sided PCBs for your project, consider the following factors:
-
Circuit complexity: If your design has a high component count or requires complex routing, a double-sided PCB may be more suitable.
-
Signal integrity: For applications sensitive to electromagnetic interference or requiring high-speed signals, double-sided PCBs offer better signal integrity.
-
Cost: Single-sided PCBs are generally more cost-effective, especially for low-volume production or simple designs.
-
Size constraints: Double-sided PCBs allow for higher component density and can help reduce the overall size of the board.
-
Reliability: Double-sided PCBs offer better mechanical stability and heat dissipation, which can improve the reliability of the circuit.
Comparison Table: Single-Sided vs. Double-Sided PCBs
Feature | Single-Sided PCB | Double-Sided PCB |
---|---|---|
Copper Layers | One | Two |
Component Mounting | One side | Both sides |
Routing Flexibility | Limited | High |
Component Density | Low | High |
Manufacturing Cost | Low | Moderate |
Signal Integrity | Moderate | High |
Heat Dissipation | Limited | Better |
Suitable for | Simple circuits | Complex circuits |
Frequently Asked Questions (FAQ)
-
Q: Can single-sided PCBs have components on both sides?
A: No, single-sided PCBs have copper traces and components on only one side of the board. -
Q: Are double-sided PCBs more expensive than single-sided PCBs?
A: Yes, double-sided PCBs are generally more expensive due to the additional manufacturing steps and materials required. -
Q: Can single-sided PCBs be used for high-frequency applications?
A: Single-sided PCBs are not ideal for high-frequency applications due to their limited routing options and potential for signal integrity issues. -
Q: How are the two layers of a double-sided PCB connected?
A: The two layers of a double-sided PCB are connected through plated-through holes (PTHs) or vias, which are copper-plated holes that allow electrical connections between the layers. -
Q: Are there any limitations on the component types that can be used on single-sided PCBs?
A: Single-sided PCBs can accommodate most through-hole components and some surface-mount components, but the single-layer design may limit the use of certain high-density or fine-pitch components.
Conclusion
Single-sided and double-sided PCBs are two fundamental types of printed circuit boards, each with its own advantages, limitations, and applications. Single-sided PCBs are cost-effective and suitable for simple electronic projects, while double-sided PCBs offer increased routing flexibility, higher component density, and better signal integrity for more complex designs. Understanding the differences between these PCB types and considering factors such as circuit complexity, cost, and reliability will help you make an informed decision when selecting the appropriate PCB for your project.
Leave a Reply