What is a Rigid-Flex PCB?
A rigid-flex PCB is a printed circuit board that combines both rigid and flexible substrates, allowing for a more versatile and adaptable design. The rigid portions of the board provide structural support and house the majority of the components, while the flexible portions allow for bending, folding, and twisting, enabling the PCB to fit into tight spaces or conform to unique shapes.
Advantages of Rigid-Flex PCBs
- Space savings: Rigid-flex PCBs can be folded or bent to fit into smaller spaces, reducing the overall size of the device.
- Weight reduction: By eliminating the need for connectors and cables between rigid boards, rigid-flex PCBs can significantly reduce the weight of the final product.
- Increased reliability: With fewer interconnects and connectors, rigid-flex PCBs are less prone to failures caused by mechanical stress or vibrations.
- Enhanced signal integrity: The shorter signal paths and reduced number of interconnects in rigid-flex PCBs result in improved signal integrity and reduced electromagnetic interference (EMI).
- Cost-effective: Although the initial design and fabrication costs may be higher, rigid-flex PCBs can lead to overall cost savings by reducing assembly time, minimizing the number of components, and improving reliability.
Designing Rigid-flex PCBs
Designing rigid-flex PCBs requires a thorough understanding of the unique challenges and considerations involved. In this section, we will discuss the key aspects of rigid-flex PCB design and provide tips for mastering rapid design techniques.
Planning and Layout
- Define the mechanical requirements: Before starting the design process, clearly define the mechanical requirements of your device, including the desired shape, size, and flexibility of the PCB.
- Create a 3D model: Develop a 3D model of your device to visualize how the rigid-flex PCB will fit and function within the enclosure. This will help you identify potential issues early in the design process.
- Determine the layer stack-up: Carefully plan the layer stack-up of your rigid-flex PCB, taking into account the number of layers, materials, and thicknesses required for both the rigid and flexible portions.
- Optimize component placement: Place components strategically on the rigid portions of the board to minimize the number of flex layers and reduce mechanical stress on the flexible portions.
Flexible Circuit Design
- Choose the right materials: Select materials that can withstand the expected mechanical stresses and environmental conditions, such as polyimide or polyester for the flexible portions.
- Design for flexibility: Ensure that the flexible portions of the PCB are designed to accommodate the required bending and folding without causing damage to the traces or components.
- Consider the bend radius: Determine the minimum bend radius for your flexible circuit based on the materials and layer stack-up used. This will help prevent damage and ensure long-term reliability.
- Use strain relief: Incorporate strain relief features, such as stiffeners or adhesives, to protect the transition zones between the rigid and flexible portions of the PCB.
Signal Integrity and EMI
- Minimize crosstalk: Ensure that the trace routing and spacing are optimized to minimize crosstalk and signal integrity issues, especially in the flexible portions of the PCB.
- Use shielding: Implement shielding techniques, such as ground planes or shielded traces, to reduce EMI and improve signal integrity.
- Consider impedance control: Design your traces with controlled impedance to maintain signal integrity and minimize reflections, particularly in high-speed designs.
Thermal Management
- Evaluate heat dissipation: Assess the heat dissipation requirements of your components and design the PCB accordingly, ensuring that the rigid portions can effectively dissipate heat.
- Use thermal vias: Incorporate thermal vias to transfer heat from the components to the ground planes or heatsinks, improving overall thermal performance.
- Consider thermal expansion: Account for the differing thermal expansion coefficients of the rigid and flexible materials, and design your PCB to minimize stress caused by temperature changes.
Manufacturing Considerations
- Communicate with your manufacturer: Work closely with your PCB manufacturer to ensure that they have the capability and experience to produce your rigid-flex PCB design.
- Provide clear documentation: Create detailed and accurate documentation, including drawings, layer stack-up information, and material specifications, to minimize the risk of manufacturing errors.
- Allow for manufacturing tolerances: Design your PCB with appropriate manufacturing tolerances in mind, particularly for the flexible portions, to ensure that the final product meets your specifications.
Mastering Rapid Design Techniques
To streamline your rigid-flex PCB design process and achieve faster turnaround times, consider implementing the following rapid design techniques:
- Use design templates: Develop a library of proven design templates for common rigid-flex PCB configurations, allowing you to quickly adapt and customize designs for new projects.
- Leverage simulation tools: Utilize simulation tools to analyze signal integrity, thermal performance, and mechanical stress, enabling you to identify and resolve issues early in the design process.
- Collaborate with your team: Foster effective communication and collaboration among your design team members, ensuring that everyone is working towards the same goals and sharing knowledge and expertise.
- Continuously refine your process: Regularly review and refine your design process, incorporating lessons learned and best practices to improve efficiency and reduce design iterations.
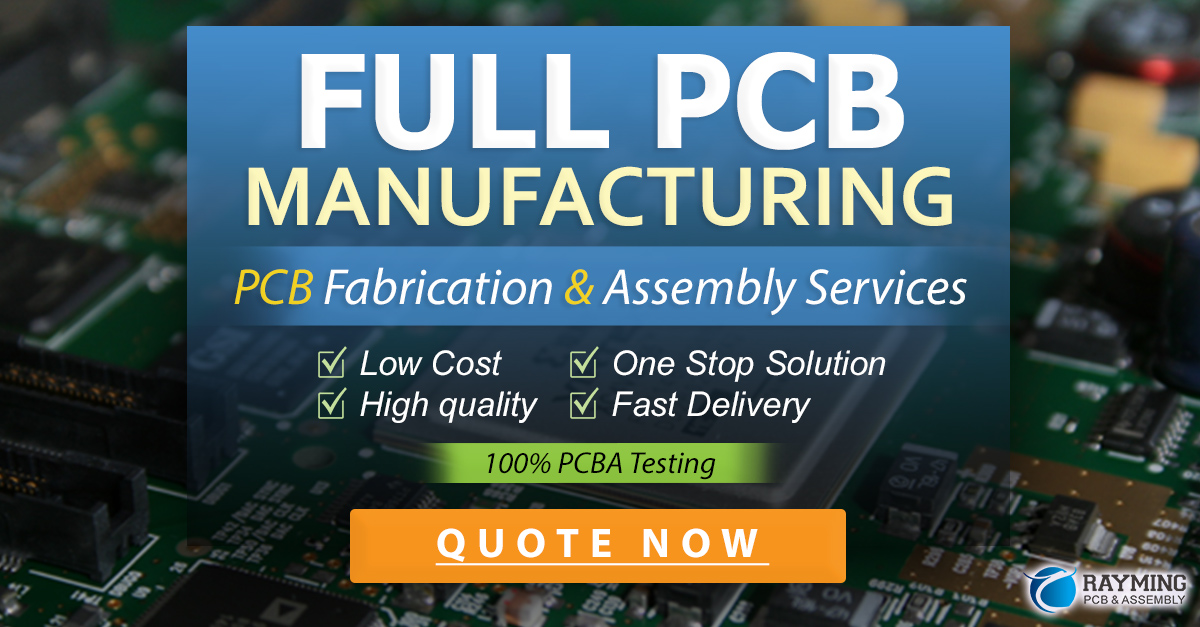
FAQs
-
What is the difference between a rigid-flex PCB and a flex PCB?
A rigid-flex PCB combines both rigid and flexible substrates, allowing for a more versatile and adaptable design. In contrast, a flex PCB is entirely flexible and does not have any rigid portions. -
Can rigid-flex PCBs be used in high-temperature environments?
Yes, rigid-flex PCBs can be designed to withstand high-temperature environments by selecting appropriate materials and incorporating thermal management techniques, such as thermal vias and heat sinks. -
How do I choose the right materials for my rigid-flex PCB?
The choice of materials depends on the specific requirements of your application, such as the expected mechanical stresses, environmental conditions, and electrical performance. Work closely with your PCB manufacturer to select the most suitable materials for your design. -
What are the challenges in designing rigid-flex PCBs?
Designing rigid-flex PCBs can be challenging due to the need to account for mechanical stress, thermal expansion, and signal integrity issues. It is essential to have a thorough understanding of the unique considerations involved and to work closely with your manufacturer to ensure a successful design. -
How can I reduce the cost of rigid-flex PCB design and manufacturing?
To reduce costs, consider optimizing your design to minimize the number of layers and components, using standardized materials and processes, and partnering with a reliable and experienced PCB manufacturer who can provide guidance and support throughout the design and manufacturing process.
Aspect | Considerations |
---|---|
Planning | – Define mechanical requirements – Create 3D model – Determine layer stack-up – Optimize component placement |
Flexible | – Choose the right materials – Design for flexibility – Consider bend radius – Use strain relief |
Signal and EMI | – Minimize crosstalk – Use shielding – Consider impedance control |
Thermal | – Evaluate heat dissipation – Use thermal vias – Consider thermal expansion |
Manufacturing | – Communicate with manufacturer – Provide clear documentation – Allow for tolerances |
Rapid Design | – Use design templates – Leverage simulation tools – Collaborate with team – Continuously refine process |
Mastering rigid-flex PCB design requires a combination of technical expertise, careful planning, and effective collaboration. By understanding the unique challenges and considerations involved, and by implementing rapid design techniques, you can streamline your design process, reduce turnaround times, and create reliable and high-performance rigid-flex PCBs for a wide range of applications.
Leave a Reply