Understanding the Basics of Flexible Circuit Design
Before diving into the specific factors, let’s briefly discuss the fundamentals of flexible circuit design. Flexible circuits consist of a thin, flexible substrate, typically made of polyimide or other flexible materials, with conductive traces and pads printed on one or both sides. These circuits can be single-sided, double-sided, or multi-layered, depending on the complexity and requirements of the application.
Flexible circuits offer several advantages over traditional rigid PCBs, including:
- Reduced weight and space requirements
- Increased flexibility and durability
- Improved signal integrity and reduced electromagnetic interference (EMI)
- Enhanced design freedom and integration possibilities
Factor 1: Material Selection
One of the most critical factors in flexible circuit design is the selection of appropriate materials. The substrate material should be chosen based on the application’s requirements, such as temperature range, chemical resistance, and mechanical properties. Polyimide is the most commonly used substrate material due to its excellent thermal stability, chemical resistance, and mechanical strength.
Other substrate materials include:
- Polyester (PET)
- Polyethylene naphthalate (PEN)
- Liquid crystal polymer (LCP)
- Polytetrafluoroethylene (PTFE)
The conductive traces are typically made of copper, with varying thicknesses depending on the current carrying requirements and mechanical flexibility needed. Adhesives and cover layers should also be carefully selected to ensure proper bonding and protection of the circuit.
Factor 2: Bend Radius and Flexibility Requirements
Flexible circuits are designed to bend and flex, but the extent of flexibility required varies depending on the application. The bend radius is a critical parameter that determines the minimum radius around which the circuit can be bent without causing damage or affecting its performance.
The bend radius is influenced by several factors, including:
- Substrate material and thickness
- Copper thickness and type
- Adhesive material and thickness
- Cover layer material and thickness
As a general rule, the minimum bend radius should be at least six times the total thickness of the flexible circuit. However, for dynamic flexing applications, a larger bend radius may be necessary to ensure long-term reliability.
Flexing Type | Bend Radius Recommendation |
---|---|
Static (one-time) Flexing | 6x total thickness |
Dynamic Flexing (>100,000 cycles) | 12x total thickness |
High-Cycle Dynamic Flexing (>1,000,000 cycles) | 24x total thickness |
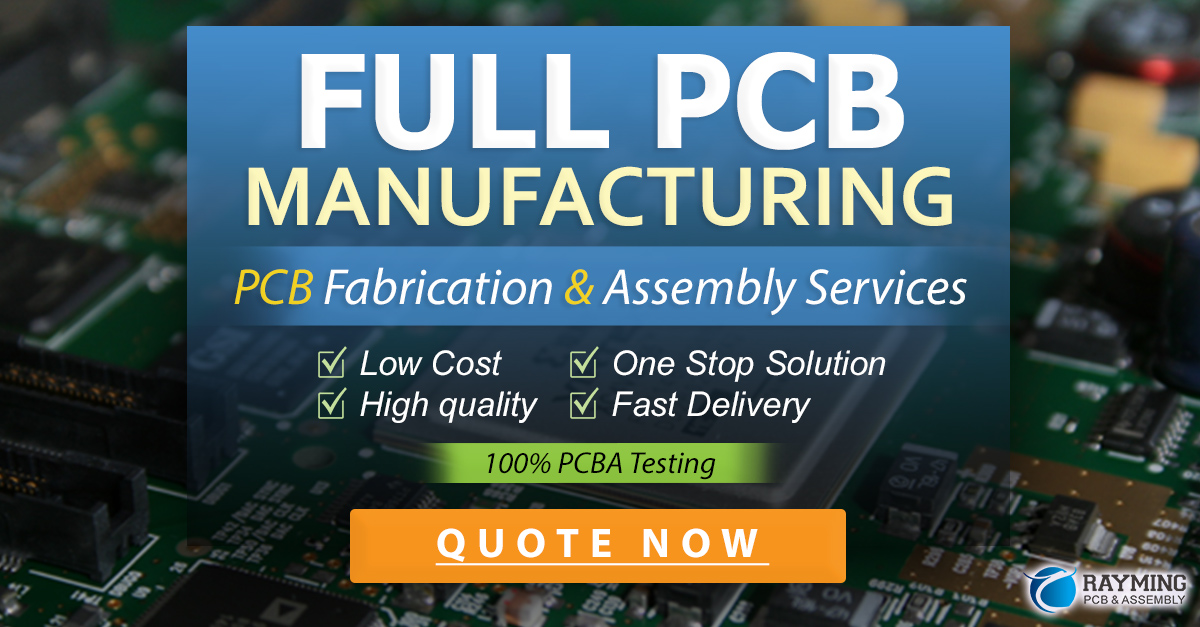
Factor 3: Trace Width and Spacing
The width and spacing of conductive traces on a flexible circuit are critical factors that impact the circuit’s electrical performance, current carrying capacity, and manufacturability. Trace width and spacing are determined by the circuit’s electrical requirements, such as current, voltage, and impedance, as well as the manufacturing capabilities of the fabricator.
Minimum trace width and spacing are limited by the fabrication process and the substrate material used. Typical minimum trace widths range from 50µm to 100µm, while minimum spacing ranges from 50µm to 150µm, depending on the fabricator and the circuit’s complexity.
When designing trace width and spacing, consider the following guidelines:
- Use wider traces for high-current paths to minimize resistance and heat generation
- Maintain consistent trace width and spacing to ensure consistent impedance and signal integrity
- Follow the fabricator’s design rules and guidelines for minimum trace width and spacing
- Use copper thickening or multiple layers for high-current applications
Factor 4: Copper Thickness and Plating
The thickness of the copper traces on a flexible circuit plays a significant role in its electrical and mechanical properties. Thicker copper traces offer lower resistance and higher current carrying capacity but may reduce the circuit’s flexibility and increase its overall thickness.
Copper thickness is typically specified in ounces per square foot (oz/ft²), with common thicknesses ranging from 0.5 oz/ft² to 2 oz/ft². The choice of copper thickness depends on the application’s electrical and mechanical requirements.
Plating is another critical aspect of copper traces in flexible circuits. Plating options include:
- Electrodeposited (ED) copper: A low-cost option suitable for most applications
- Rolled annealed (RA) copper: Offers higher ductility and flexibility compared to ED copper
- High-ductility electrodeposited (HD ED) copper: Combines the advantages of ED and RA copper
Consider the following factors when selecting copper thickness and plating:
- Current carrying requirements and voltage drop
- Mechanical flexibility and bend radius requirements
- Cost and availability of materials
- Fabricator’s capabilities and recommendations
Factor 5: Adhesives and Bonding
Adhesives play a crucial role in bonding the various layers of a flexible circuit together, ensuring mechanical stability and reliability. The choice of adhesive material depends on the application’s requirements, such as temperature range, chemical resistance, and flexibility.
Common adhesive materials used in flexible circuits include:
- Acrylic: Offers good flexibility and adhesion but limited temperature resistance
- Epoxy: Provides excellent temperature resistance and chemical stability but may be brittle
- Polyimide: Offers high temperature resistance and good chemical stability
- Pressure-sensitive adhesive (PSA): Provides easy assembly and disassembly but limited temperature resistance
When selecting adhesives, consider the following factors:
- Compatibility with substrate and cover layer materials
- Temperature range and chemical resistance requirements
- Flexibility and bend radius requirements
- Ease of processing and assembly
- Cost and availability of materials
Factor 6: Cover Layers and Protection
Cover layers, also known as coverlay or cover film, are used to protect the conductive traces and provide electrical insulation on flexible circuits. The choice of cover layer material depends on the application’s requirements, such as temperature range, chemical resistance, and mechanical properties.
Common cover layer materials include:
- Polyimide: Offers excellent thermal stability, chemical resistance, and mechanical strength
- Polyester: Provides good electrical insulation and flexibility but limited temperature resistance
- Liquid photoimageable (LPI) solder mask: Allows for selective coverage and fine-pitch features
When selecting cover layers, consider the following factors:
- Compatibility with substrate and adhesive materials
- Temperature range and chemical resistance requirements
- Flexibility and bend radius requirements
- Electrical insulation and dielectric properties
- Ease of processing and assembly
- Cost and availability of materials
Factor 7: Shielding and Grounding
Shielding and grounding are essential considerations in flexible circuit design to minimize electromagnetic interference (EMI) and ensure signal integrity. Proper shielding and grounding techniques help to reduce noise, crosstalk, and other unwanted electromagnetic effects.
Shielding options for flexible circuits include:
- Conductive adhesives or paints
- Conductive fabric or mesh
- Copper or aluminum foil
- Plated through holes (PTHs) or vias
Grounding techniques for flexible circuits include:
- Dedicated ground planes
- Grounding traces or rings
- Stitching vias or PTHs
- Conductive adhesives or gaskets
When designing shielding and grounding, consider the following factors:
- EMI and signal integrity requirements
- Shielding effectiveness and coverage
- Grounding path impedance and continuity
- Mechanical flexibility and bend radius requirements
- Manufacturability and assembly considerations
Factor 8: Stiffeners and Reinforcements
Stiffeners and reinforcements are used in flexible circuits to provide mechanical support, improve handling, and ensure proper connector mating. Stiffeners are typically made of rigid materials, such as polyimide, FR-4, or metal, and are bonded to specific areas of the flexible circuit.
Common types of stiffeners and reinforcements include:
- Localized stiffeners: Used to reinforce connector areas or provide support for components
- Full-panel stiffeners: Used to improve overall handling and stability of the flexible circuit
- Bend relief: Used to minimize stress and prevent damage at the transition between flexible and rigid sections
When designing stiffeners and reinforcements, consider the following factors:
- Mechanical requirements and stress distribution
- Compatibility with substrate and adhesive materials
- Thickness and material properties of the stiffener
- Placement and bonding techniques
- Assembly and mating requirements
Factor 9: Assembly and Manufacturability
Designing a flexible circuit with assembly and manufacturability in mind is crucial for ensuring a successful and cost-effective product. Considerations for assembly and manufacturability include:
- Component placement and orientation
- Soldering and bonding techniques
- Connector and termination options
- Strain relief and mechanical support
- Tooling and fixturing requirements
- Testing and inspection methods
When designing for assembly and manufacturability, consider the following guidelines:
- Follow the fabricator’s design rules and guidelines
- Use standard component sizes and packaging where possible
- Provide adequate clearance and access for soldering and inspection
- Consider the impact of flexing on component placement and reliability
- Incorporate strain relief and mechanical support where necessary
- Plan for testing and inspection requirements early in the design process
FAQ
-
Q: What is the minimum bend radius for a flexible circuit?
A: The minimum bend radius depends on the total thickness of the flexible circuit and the flexing requirements. As a general rule, the minimum bend radius should be at least six times the total thickness for static flexing, 12 times for dynamic flexing, and 24 times for high-cycle dynamic flexing. -
Q: Can flexible circuits be multi-layered?
A: Yes, flexible circuits can be single-sided, double-sided, or multi-layered, depending on the complexity and requirements of the application. Multi-layer flexible circuits offer increased circuit density and design flexibility but may have limitations in terms of minimum bend radius and overall thickness. -
Q: What is the typical copper thickness used in flexible circuits?
A: Copper thickness in flexible circuits is typically specified in ounces per square foot (oz/ft²), with common thicknesses ranging from 0.5 oz/ft² to 2 oz/ft². The choice of copper thickness depends on the application’s electrical and mechanical requirements, such as current carrying capacity and flexibility. -
Q: How can I minimize electromagnetic interference (EMI) in my flexible circuit design?
A: To minimize EMI in flexible circuits, consider implementing proper shielding and grounding techniques. Shielding options include conductive adhesives, fabrics, foils, and plated through holes (PTHs), while grounding techniques include dedicated ground planes, grounding traces, stitching vias, and conductive adhesives or gaskets. -
Q: What should I consider when designing flexible circuits for assembly and manufacturability?
A: When designing flexible circuits for assembly and manufacturability, follow the fabricator’s design rules and guidelines, use standard component sizes and packaging where possible, provide adequate clearance and access for soldering and inspection, consider the impact of flexing on component placement and reliability, incorporate strain relief and mechanical support where necessary, and plan for testing and inspection requirements early in the design process.
Conclusion
Designing flexible circuits requires careful consideration of multiple factors to ensure optimal performance, reliability, and manufacturability. By understanding and addressing these nine key factors – material selection, bend radius and flexibility, trace width and spacing, copper thickness and plating, adhesives and bonding, cover layers and protection, shielding and grounding, stiffeners and reinforcements, and assembly and manufacturability – designers can create successful and cost-effective flexible circuit solutions for a wide range of applications.
As the demand for compact, lightweight, and flexible electronic devices continues to grow, the importance of flexible circuit design will only increase. By staying informed about the latest materials, technologies, and best practices in flexible circuit design, engineers and designers can stay ahead of the curve and deliver innovative solutions that meet the evolving needs of the electronics industry.
Leave a Reply