Introduction to PCB Plating Simulation
Printed circuit board (PCB) design has come a long way in recent decades. With the advent of powerful computer-aided design (CAD) tools, PCB designers can now create complex, high-density boards with ease. However, one aspect of PCB design that has remained challenging is predicting and optimizing the plating process.
PCB plating is a critical step in the manufacturing process, as it determines the electrical conductivity, durability, and reliability of the finished board. Traditionally, designers have had to rely on trial and error, or on simplified models, to predict the outcome of the plating process. This can lead to costly redesigns and production delays.
Fortunately, there is now a new tool available to PCB designers: plating simulation. Plating simulation software uses advanced mathematical models to predict the behavior of the plating process, allowing designers to optimize their designs for manufacturability and performance.
What is PCB Plating?
Before we dive into the details of plating simulation, let’s take a moment to review what PCB plating is and why it’s important.
PCB plating is the process of depositing a thin layer of metal onto the surface of a PCB. This metal layer serves several important functions:
-
Electrical conductivity: The plated metal layer provides a low-resistance path for electrical current to flow between components on the PCB.
-
Corrosion protection: The plated metal layer helps to protect the underlying copper traces from oxidation and other forms of corrosion.
-
Solderability: The plated metal layer provides a surface that is easy to solder to, allowing components to be attached to the board.
-
Wear resistance: The plated metal layer can help to protect the PCB from mechanical wear and tear.
There are several different metals that can be used for PCB plating, each with its own advantages and disadvantages. The most common plating metals are:
Metal | Advantages | Disadvantages |
---|---|---|
Copper | – Good electrical conductivity – Relatively inexpensive |
– Prone to oxidation – Difficult to solder to |
Nickel | – Good corrosion resistance – Hard and wear-resistant |
– Relatively poor electrical conductivity |
Gold | – Excellent corrosion resistance – Easy to solder to |
– Expensive |
Silver | – Excellent electrical conductivity | – Prone to tarnishing – Relatively soft |
Tin | – Good solderability – Relatively inexpensive |
– Prone to whisker growth |
The choice of plating metal will depend on the specific requirements of the PCB, such as the operating environment, the expected lifespan, and the cost constraints.
The Challenges of PCB Plating
While PCB plating is a critical step in the manufacturing process, it is also one of the most challenging. There are several factors that can affect the quality and consistency of the plating process, including:
-
Board geometry: The shape and layout of the PCB can affect the uniformity of the plating process. For example, tight spaces between traces can lead to uneven plating thickness.
-
Surface preparation: The cleanliness and roughness of the PCB surface can affect the adhesion and uniformity of the plated layer.
-
Bath chemistry: The composition and concentration of the plating bath can affect the properties of the plated layer, such as its thickness, hardness, and electrical conductivity.
-
Current density: The amount of electrical current used in the plating process can affect the speed and uniformity of the plating process.
-
Temperature: The temperature of the plating bath can affect the rate of deposition and the properties of the plated layer.
Traditionally, PCB designers have had to rely on trial and error, or on simplified models, to predict the outcome of the plating process. This can lead to several problems:
-
Overplating: If the plating process is not well-controlled, it can result in excessive plating thickness, which can cause problems with component placement and solderability.
-
Underplating: If the plating process is not sufficiently aggressive, it can result in thin or inconsistent plating, which can lead to poor electrical conductivity and reduced durability.
-
Voids and Nodules: Uneven plating can result in voids (areas with no plating) or nodules (areas with excessive plating), which can cause problems with electrical continuity and reliability.
-
Wasted Materials: If the plating process is not optimized, it can result in wasted materials, such as excess plating solution or overplated boards that need to be reworked.
To avoid these problems, PCB designers need a way to predict and optimize the plating process before the board goes into production. This is where plating simulation comes in.
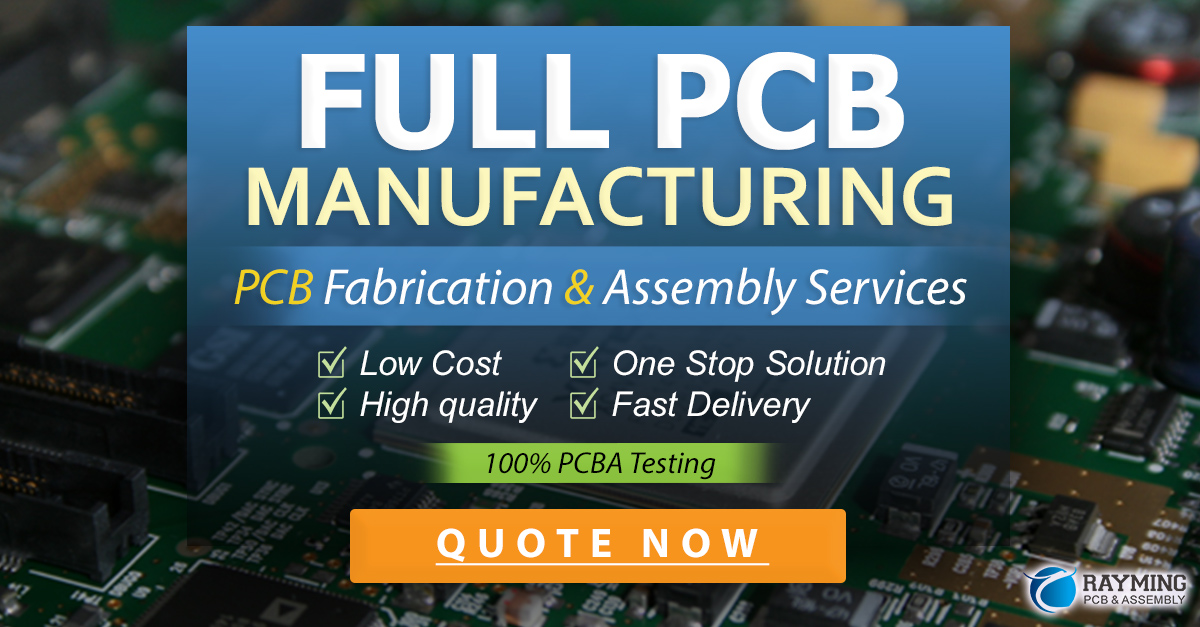
How Plating Simulation Works
Plating simulation software uses advanced mathematical models to predict the behavior of the plating process. These models take into account a wide range of factors, including:
-
Board Geometry: The software can import the CAD files for the PCB and use them to create a 3D model of the board. This allows the software to predict how the shape and layout of the board will affect the plating process.
-
Plating Bath Chemistry: The software can model the composition and concentration of the plating bath, including the type of metal being deposited and any additives or surfactants used.
-
Current Density: The software can predict the distribution of electrical current across the surface of the PCB, taking into account factors such as the shape and spacing of the traces.
-
Fluid Dynamics: The software can model the flow of the plating solution over the surface of the PCB, taking into account factors such as the temperature and agitation of the bath.
By combining these factors, the plating simulation software can predict the thickness, uniformity, and properties of the plated layer across the entire surface of the PCB. This allows designers to optimize their designs for manufacturability and performance, before the board ever goes into production.
Benefits of Plating Simulation
There are several key benefits to using plating simulation in the PCB design process:
-
Reduced Time to Market: By predicting and optimizing the plating process in advance, designers can avoid costly redesigns and production delays. This can help to reduce the overall time to market for the product.
-
Improved Quality: Plating simulation can help to ensure that the finished PCB meets all of the necessary quality and reliability standards, by predicting and preventing problems such as overplating, underplating, and voids.
-
Reduced Costs: By optimizing the plating process, designers can reduce the amount of materials and labor required to produce the PCB. This can lead to significant cost savings, especially for high-volume production runs.
-
Increased Innovation: By providing designers with a powerful new tool for optimizing the plating process, plating simulation can help to enable new and innovative PCB designs that might not have been possible with traditional methods.
Case Studies
To illustrate the benefits of plating simulation, let’s look at a few real-world case studies:
Case Study 1: High-Density PCB for Aerospace Application
A major aerospace company was designing a high-density PCB for use in a satellite. The board had a complex shape and a large number of tightly-spaced traces, which made it challenging to achieve uniform plating.
Using plating simulation software, the designers were able to predict the plating thickness and uniformity across the entire board. They identified several areas where the plating was too thin, and made adjustments to the design to improve the uniformity.
As a result, the final board had excellent electrical conductivity and reliability, and met all of the necessary quality standards for aerospace applications. The use of plating simulation helped to reduce the overall development time and cost for the project.
Case Study 2: Automotive ECU Board
An automotive supplier was designing a new electronic control unit (ECU) board for use in a high-performance vehicle. The board needed to be highly reliable and able to withstand harsh environmental conditions.
Using plating simulation software, the designers were able to optimize the plating process for maximum durability and corrosion resistance. They identified areas where the plating was too thin or inconsistent, and made adjustments to the design to improve the uniformity.
As a result, the final board had excellent durability and reliability, and was able to withstand the harsh conditions of the automotive environment. The use of plating simulation helped to reduce the overall development time and cost for the project, while ensuring that the board met all of the necessary quality and safety standards.
Implementing Plating Simulation in Your Design Process
If you’re interested in incorporating plating simulation into your PCB design process, there are a few key steps you’ll need to follow:
-
Choose a plating simulation software package: There are several commercially available plating simulation packages on the market, each with its own strengths and weaknesses. Some of the most popular options include:
-
AutoPlate
- PlatingCell
- SimPlate
-
PlatingMaster
-
Integrate the software into your design workflow: Once you’ve chosen a plating simulation package, you’ll need to integrate it into your existing design workflow. This may involve training your designers on how to use the software, and establishing new processes for incorporating plating simulation into the design process.
-
Validate the simulation results: Before relying on the plating simulation results, it’s important to validate them against actual plating data. This may involve running test boards through the plating process and comparing the results to the simulation predictions.
-
Continuously improve the process: As with any new tool or process, it’s important to continuously monitor and improve the plating simulation process over time. This may involve fine-tuning the simulation parameters, incorporating new features or capabilities, and sharing best practices among your design team.
By following these steps, you can successfully implement plating simulation into your PCB design process, and start realizing the benefits of this powerful new tool.
Plating Simulation FAQ
Q: What types of PCBs can plating simulation be used for?
A: Plating simulation can be used for virtually any type of PCB, from simple single-layer boards to complex Multi-layer Boards with high-density interconnects. However, the benefits of plating simulation are typically greater for more complex boards with tight tolerances and challenging geometries.
Q: Can plating simulation be used for Prototype Boards?
A: Yes, plating simulation can be used for prototype boards as well as production boards. In fact, using plating simulation for prototypes can help to identify and correct potential issues early in the design process, before they become more costly and time-consuming to fix.
Q: How accurate are plating simulation predictions?
A: The accuracy of plating simulation predictions depends on a number of factors, including the quality of the input data (e.g. CAD files, plating bath parameters), the sophistication of the simulation models, and the skill of the operator. In general, plating simulation can provide predictions that are within 10-20% of actual plating results, which is sufficient for most design optimization purposes.
Q: Is plating simulation expensive?
A: The cost of plating simulation software varies depending on the specific package and vendor. In general, plating simulation is a relatively small investment compared to the overall cost of PCB design and manufacturing. The cost of the software is typically offset by the savings in time, materials, and rework that result from using plating simulation to optimize the design.
Q: Do I need special training to use plating simulation software?
A: While plating simulation software is designed to be user-friendly, it does require some specialized knowledge and skills to use effectively. Most vendors offer training and support services to help users get up to speed quickly. In addition, many PCB design firms have in-house experts who specialize in plating simulation and can provide guidance and support to other members of the design team.
Conclusion
Plating simulation is a powerful new tool for PCB designers that can help to predict and optimize the plating process, reducing costs, improving quality, and accelerating time to market. By using advanced mathematical models to simulate the behavior of the plating bath, plating simulation software can help designers to identify and correct potential issues before the board goes into production.
While implementing plating simulation into the design process does require some upfront investment and effort, the benefits can be significant. By embracing this new technology, PCB designers can stay ahead of the curve and deliver better, faster, and more cost-effective solutions to their customers.
As PCB technology continues to evolve and become more complex, tools like plating simulation will become increasingly essential for designers who want to stay competitive in the marketplace. So if you’re not already using plating simulation in your design process, now is the time to start exploring this exciting new technology.
Leave a Reply